Category: Profilometry | Roughness and Finish
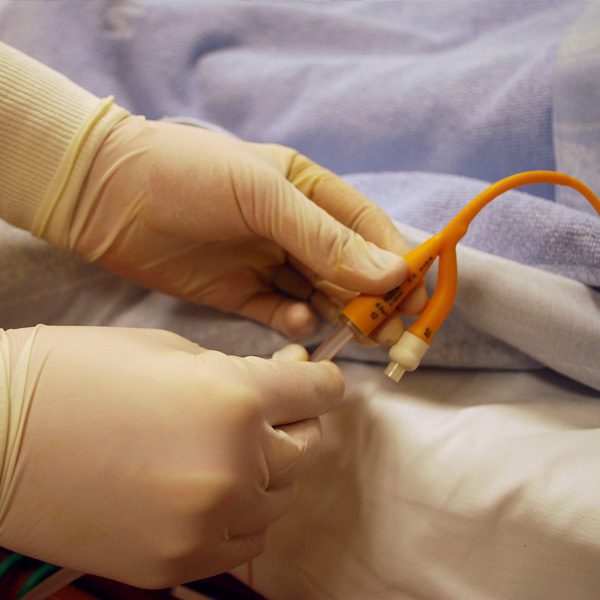
Dimensional and Surface Finish of Polymeric Tubes
Importance of Dimensional and Surface Analysis of Polymeric Tubes
Tubes made from polymeric material are commonly used in many industries ranging from automotive, medical, electrical, and many other categories. In this study, medical catheters made of different polymeric materials were studied using the Nanovea 3D Non-Contact Profilometer to measure surface roughness, morphology, and dimensions. Surface roughness is crucial for catheters as many problems with catheters, including infection, physical trauma, and inflammation can be linked with the catheter surface. Mechanical properties, such as coefficient of friction, can also be studied by observing surface properties. These quantifiable data can be obtained to ensure the catheter can be used for medical applications.
Compared to optical microscopy and electron microscopy, 3D Non-Contact Profilometry using axial chromatism is highly preferable for characterizing catheter surfaces due to its ability to measure angles/curvature, ability to measure material surfaces despite transparency or reflectivity, minimal sample preparation, and non-invasive nature. Unlike conventional optical microscopy, the height of the surface can be obtained and used for computational analysis; e.g. finding dimensions and removing form to find surface roughness. Having little sample preparation, in contrast to electron microscopy, and non-contact nature also allows for quick data collection without fearing contamination and error from sample preparation.
Measurement Objective
In this application, the Nanovea 3D Non-Contact Profilometer is used to scan the surface of two catheters: one made of TPE (Thermoplastic Elastomer) and the other made of PVC (Polyvinyl Chloride). The morphology, radial dimension, and height parameters of the two catheters will be obtained and compared.
Results and Discussion
3D Surface
Despite the curvature on polymeric tubes, the Nanovea 3D Non-contact profilometer can scan the surface of the catheters. From the scan done, a 3D image can be obtained for quick, direct visual inspection of the surface.
The outer radial dimension was obtained by extracting a profile from the original scan and fitting an arc to the profile. This shows the ability of the 3D Non-contact profilometer in conducting quick dimensional analysis for quality control applications. Multiple profiles can easily be obtained along the catheter’s length as well.
The outer radial dimension was obtained by extracting a profile from the original scan and fitting an arc to the profile. This shows the ability of the 3D Non-contact profilometer in conducting quick dimensional analysis for quality control applications. Multiple profiles can easily be obtained along the catheter’s length as well.
Conclusion
In this application, we have shown how the Nanovea 3D Non-contact profilometer can be used to characterize polymeric tubes. Specifically, surface metrology, radial dimensions, and surface roughness were obtained for medical catheters. The outer radius of the TPE catheter was found to be 2.40mm while the PVC catheter was 1.27mm. The surface of the TPE catheter was found to be rougher than the PVC catheter. The Sa of TPE was 0.9740µm compared to 0.1791µm of PVC. While medical catheters were used for this application, 3D Non-Contact Profilometry can be applied to a large variety of surfaces as well. Obtainable data and calculations are not limited to what is shown.
NOW, LET'S TALK ABOUT YOUR APPLICATION
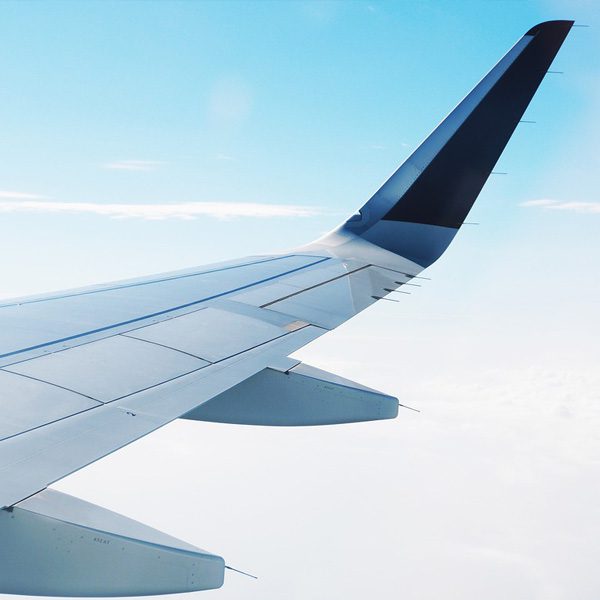
Honeycomb Panel Surface Finish with 3D Profilometry
INTRODUCTION
Roughness, porosity, and texture of the honeycomb panel surface are critical to quantify for the final panel design. These surface qualities can directly correlate to the aesthetics and functional characteristics of the panel surface. A better understanding of the surface texture and porosity can help optimize the panel surface processing and manufacturability. A quantitative, precise, and reliable surface measurement of the honeycomb panel is needed to control surface parameters for application and painting requirements. The Nanovea 3D Non-Contact sensors utilize unique chromatic confocal technology capable of precisely measuring these panel surfaces.
MEASUREMENT OBJECTIVE
In this study, the Nanovea HS2000 platform equipped with a high-speed Line Sensor was used to measure and compare two honeycomb panels with different surface finishes. We showcase the Nanovea non-contact profilometer’s ability to provide fast and precise 3D profiling measurements and comprehensive in-depth analysis of the surface finish.
RESULTS AND DISCUSSION
The surface of two honeycomb panel samples with varied surface finishes, namely Sample 1 and Sample 2, were measured. The false color and 3D view of the Samples 1 and 2 surfaces are shown in Figure 3 and Figure 4, respectively. The roughness and flatness values were calculated by advanced analysis software and are compared in Table 1. Sample 2 exhibits a more porous surface compared to Sample 1. As a result, Sample 2 possesses a higher roughness Sa of 14.7 µm, compared to an Sa value of 4.27 µm for Sample 1.
The 2D profiles of the honeycomb panel surfaces were compared in Figure 5, allowing users to have a visual comparison of the height change at different locations of the sample surface. We can observe that Sample 1 has a height variation of ~25 µm between the highest peak and lowest valley location. On the other hand, Sample 2 shows several deep pores across the 2D profile. The advanced analysis software has the ability to automatically locate and measure the depth of six relatively deep pores as shown in the table of Figure 4.b Sample 2. The deepest pore amongst the six possesses a maximum depth of nearly 90 µm (Step 4).
To further investigate the pore size and distribution of Sample 2, porosity evaluation was performed and discussed in the following section. The sliced view is displayed in Figure 5 and the results are summarized in Table 2. We can observe that the pores, marked in blue color in Figure 5, have a relatively homogeneous distribution on the sample surface. The projected area of the pores constitutes 18.9% of the whole sample surface. The volume per mm² of the total pores is ~0.06 mm³. The pores have an average depth of 42.2 µm, and the maximum depth is 108.1 µm.
CONCLUSION
In this application, we have showcased that the Nanovea HS2000 platform equipped with a high-speed Line Sensor is an ideal tool for analyzing and comparing the surface finish of honeycomb panel samples in a fast and accurate manner. The high-resolution profilometry scans paired with an advanced analysis software allow for a comprehensive and quantitative evaluation of the surface finish of honeycomb panel samples.
The data shown here represents only a small portion of the calculations available in the analysis software. Nanovea Profilometers measure virtually any surface for a wide range of applications in the Semiconductor, Microelectronic, Solar, Fiber Optics, Automotive, Aerospace, Metallurgy, Machining, Coatings, Pharmaceutical, Biomedical, Environmental and many other industries.
NOW, LET'S TALK ABOUT YOUR APPLICATION

High Speed Scanning w/ Non-contact Profilometry
Introduction:
Quick and easy set-up surface measurements save time, effort and are essential for quality control, research and development and production facilities. The Nanovea Non-Contact Profilometer is capable of performing both 3D & 2D surface scans to measure nano to macro scale features on any surface, providing broad range usability.
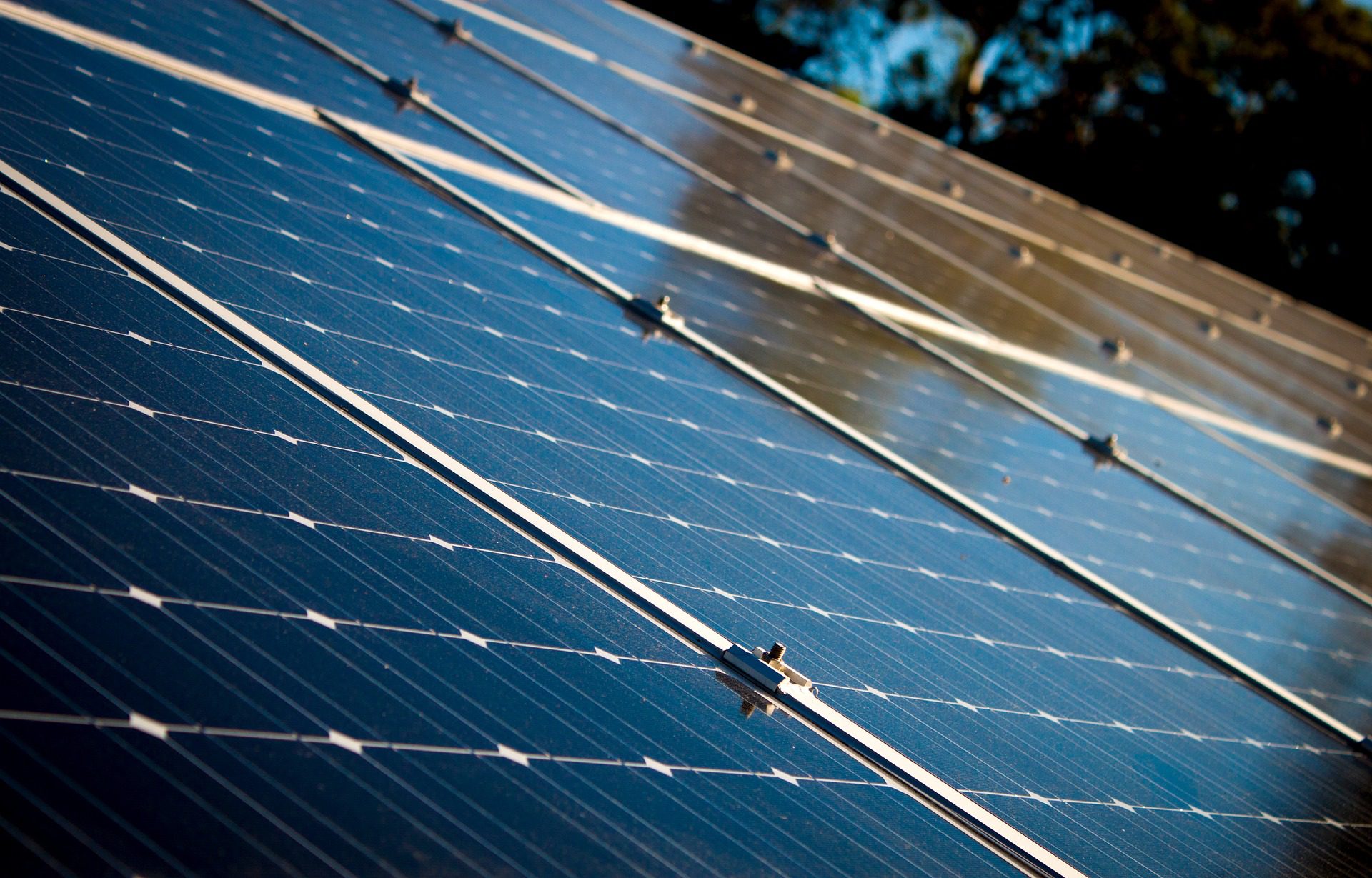
Surface Roughness and Features of a Solar Cell
Importance of Solar Panel Testing
Maximizing a solar cell’s energy absorption is key for the technology’s survival as a renewable resource. The multiple layers of coating and glass protection allow for the absorption, transmittance, and reflection of light that is necessary for the photovoltaic cells to function. Given that most consumer solar cells operate at 15-18% efficiency, optimizing their energy output is an ongoing battle.
Studies have shown that surface roughness plays a pivotal role in the reflectance of light. The initial layer of glass must be as smooth as possible to mitigate the reflectance of light, but the subsequent layers do not follow this guideline. A degree of roughness is necessary at each coatings interface to another to increase the possibility of light scattering within their respective depletion zones and increase the absorption of light within the cell1. Optimizing the surface roughness in these regions allows the solar cell to operate to the best of its ability and with the Nanovea HS2000 High Speed Sensor, measuring surface roughness can be done quickly and accurately.
Measurement Objective
In this study we will display the capabilities of the Nanovea Profilometer HS2000 with High Speed Sensor by measuring the surface roughness and geometric features of a photovoltaic cell. For this demonstration a monocrystalline solar cell with no glass protection will be measured but the methodology can be used for various other applications.
Test Procedure and Procedures
The following test parameters were used to measure the surface of the solar cell.
Results and Discussion
Depicted below is the 2D false-color view of the solar cell and an area extraction of the surface with its respective height parameters. A Gaussian filter was applied to both surfaces and a more aggressive index was used to flatten the extracted area. This excludes form (or waviness) larger than the cut-off index, leaving behind features that represent the solar cell’s roughness.
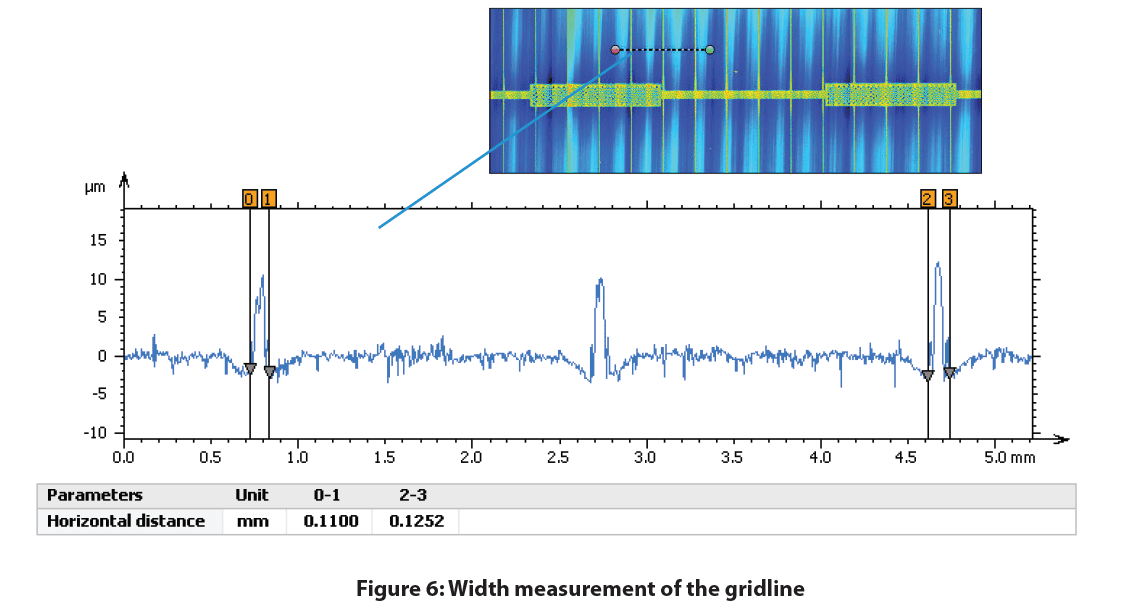

Conclusion
In this study we were able to display the Nanovea HS2000 Line Sensor’s ability to measure a monocrystalline photovoltaic cell’s surface roughness and features. With the ability to automate accurate measurements of multiple samples and set pass fail limits, the Nanovea HS2000 Line Sensor is a perfect choice for quality control inspections.
Reference
1 Scholtz, Lubomir. Ladanyi, Libor. Mullerova, Jarmila. “Influence of Surface Roughness on Optical Characteristics of Multilayer Solar Cells “ Advances in Electrical and Electronic Engineering, vol. 12, no. 6, 2014, pp. 631-638.
NOW, LET'S TALK ABOUT YOUR APPLICATION
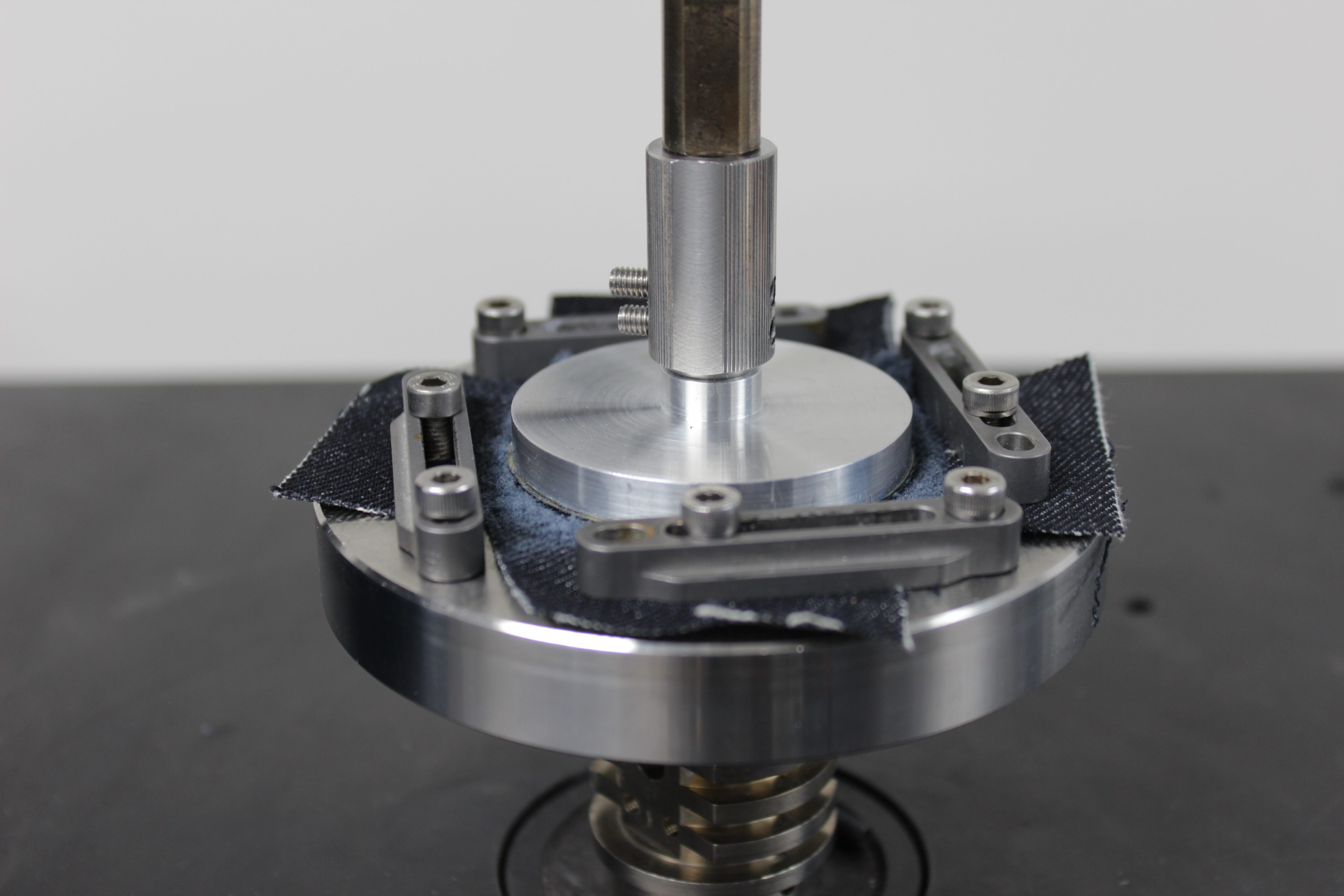
Comparing Abrasion Wear on Denim
Introduction
The form and function of a fabric is determined by its quality and durability. Daily usage of fabrics cause wear and tear on the material, e.g. piling, fuzzing, and discoloration. Subpar fabric quality used for clothing can often lead to consumer dissatisfaction and brand damage.
Attempting to quantify the mechanical properties of fabrics can pose many challenges. The yarn structure and even the factory in which it was produced can result in poor reproducibility of test results. Making it difficult to compare test results from different laboratories. Measuring the wear performance of fabrics is critical to the manufacturers, distributors, and retailers in the textile production chain. A well controlled and reproducible wear resistance measurement is crucial to ensure reliable quality control of the fabric.
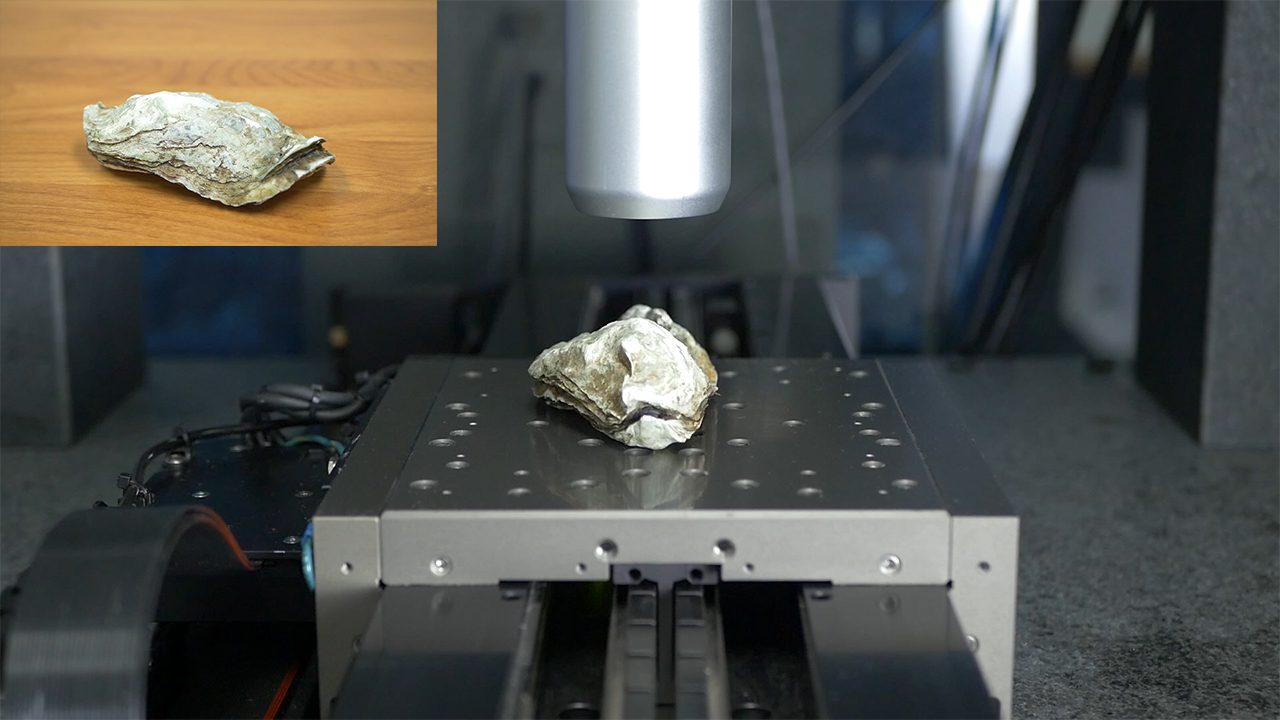
High Speed Characterization of an Oyster Shell
Large samples with complex geometries can prove difficult to work with due to sample preparation, size, sharp angles, and curvature. In this study an oyster shell will be scanned to demonstrate the Nanovea HS2000 Line Sensor’s capability to scan a large, biological sample with complex geometry. While a biological sample was used in this study, the same concepts can be applied to other samples.
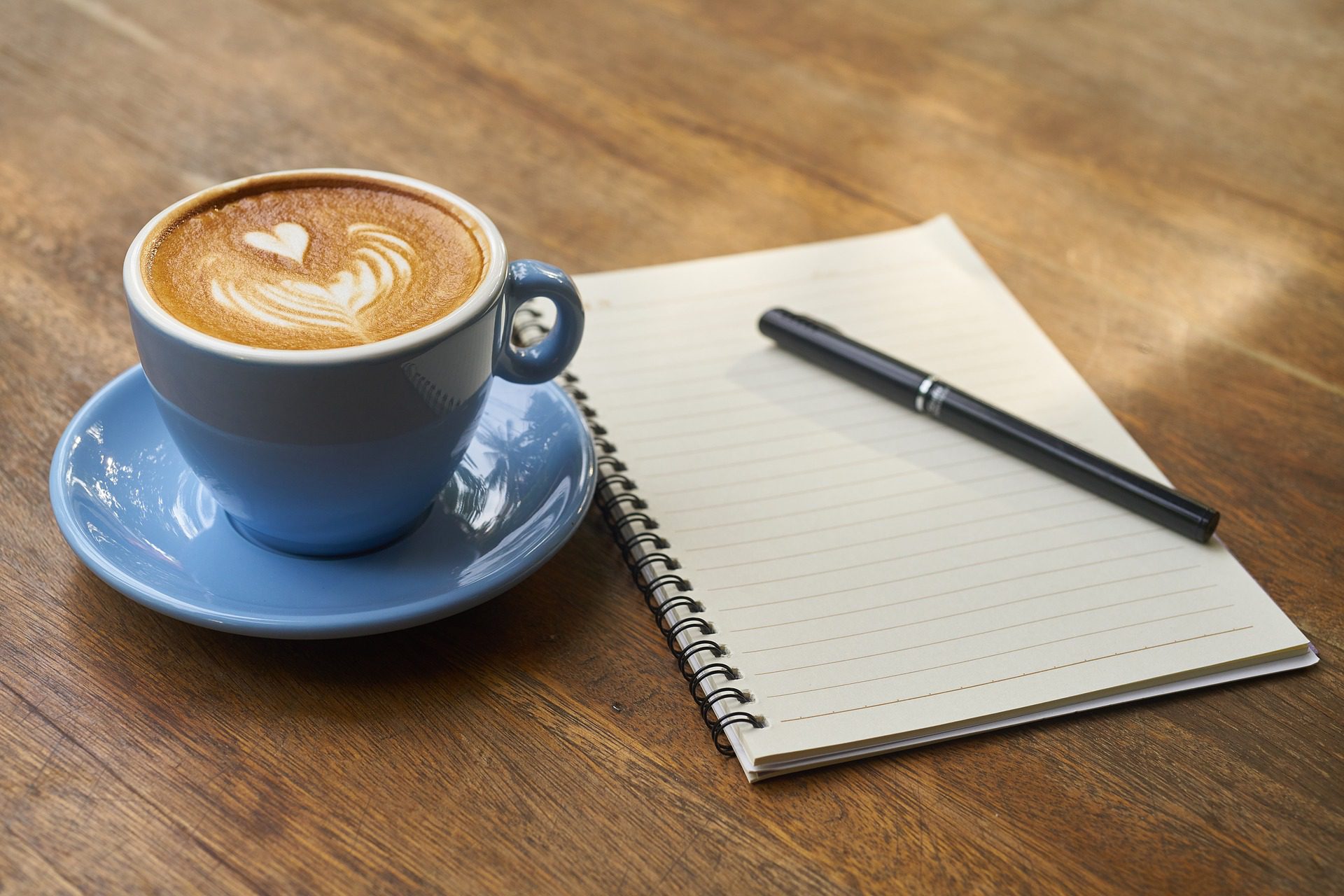
Surface Finish Inspection of Wood Flooring
Importance of Profiling Wood Finishes
In various industries, the purpose of a wood finish is to protect the wooden surface from various types of damage such as chemical, mechanical or biological and/or provide a specific visual aesthetic. For manufacturers and buyers alike, quantifying surface characteristics of their wood finishes can be vital to the quality control or optimization of finishing processes for wood. In this application, we will explore the various surface features that can be quantified using a Nanovea 3D Non-Contact Profilometer.
Quantifying the amount of roughness and texture that exists on a wooden surface can be essential to know in order to ensure it can meet the requirements of its application. Refining the finishing process or checking the quality of wooden surfaces based on a quantifiable, repeatable and reliable surface inspection method would allow manufacturers to create controlled surface treatments and buyers the ability to inspect and select wood materials to meet their needs.
Measurement Objective
In this study, the high-speed Nanovea HS2000 profilometer equipped with a non-contact profiling line sensor was used to measure and compare the surface finish of three flooring samples: Antique Birch Hardwood, Courtship Grey Oak, and Santos Mahogany flooring. We showcase the capability of the Nanovea Non-Con-tact Profilometer in delivering both speed and precision when measuring three types of surface areas and a comprehensive in-depth analysis of the scans.
Test Procedure and Procedures
Results and Discussion
Sample description: Courtship Grey Oak and Santos Mahogany flooring are laminate flooring types. Courtship Grey Oak is a low gloss, textured slate gray sample with an EIR finish. Santos Mahogany is a high gloss, dark burgundy sample that was prefinished. Antique Birch Hardwood has a 7-layer aluminum oxide finish, providing everyday wear and tear protection.
Discussion
There is a clear distinction between all the samples’ Sa value. The smoothest was Antique Birch Hardwood with a Sa of 1.716 µm, followed by Santos Mahogany with a Sa of 2.388 µm, and significantly increasing for Courtship Grey Oak with a Sa of 11.17 µm. P-values and R-values are also common roughness values that can be used to assess the roughness of specific profiles along the surface. The Courtship Grey Oak possess-es a coarse texture full of crack-like features along the wood’s cellular and fiber direction. Additional analysis was done on the Courtship Grey Oak sample because of its textured surface. On the Courtship Grey Oak sample, slices were used to separate and calculate the depth and volume of the cracks from the flatter uniform surface.
Conclusion
In this application, we have shown how the Nanovea HS2000 high-speed profilometer can be used to inspect the surface finish of wood samples effectively and efficiently. Surface finish measurements can prove to be important to both manufactures and consumers of hardwood flooring in understanding how they can improve a manufacturing process or choose the appropriate product that performs best for a specific application.
NOW, LET'S TALK ABOUT YOUR APPLICATION
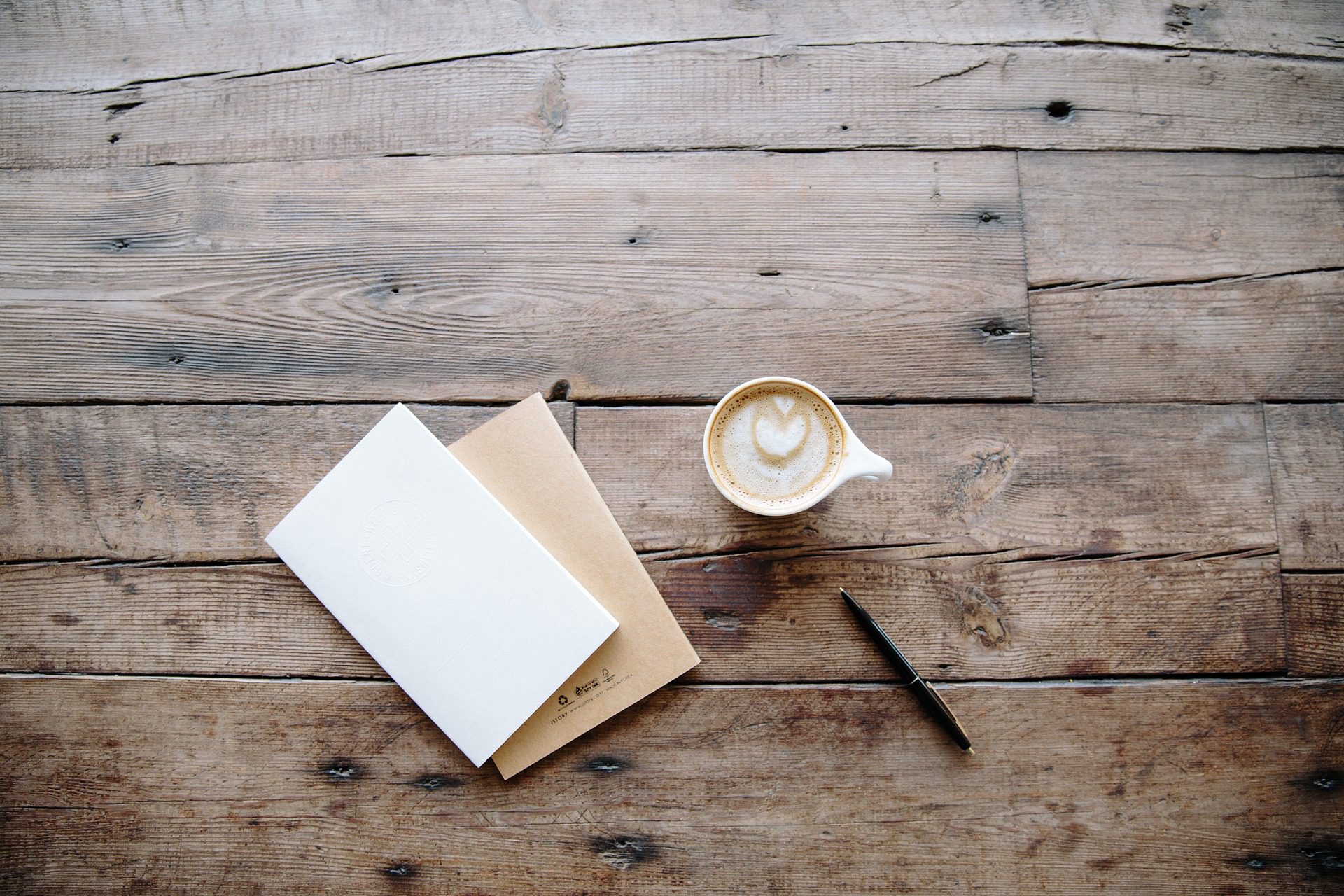
Wood Wear Test with the Nanovea Tribometer
Importance of Comparing Wood Finish Wear & COF
Wood has been used for thousands of years as a building material for homes, furniture, and flooring. It has a combination of natural beauty, and durability, making it an ideal candidate for flooring. Unlike carpet, hardwood floors keep their color for a long time and can be easily cleaned and maintained, however, being a natural material, most wood flooring requires the application of a surface finish to protect the wood from various kinds of damage such as scuffing and chipping over time. In this study, a Nanovea Tribometer was used to measure the wear rate and coefficient of friction (COF) to better understand the comparative performance of three wood finishes.
The service behavior of a wood species used for flooring is often related to its wear resistance. The change in the individual cellular and fiber structure of different species of wood contributes to their different mechanical and tribological behaviors. Actual service tests of wood as flooring materials are expensive, difficult to duplicate, and require long periods of testing time. As a result, it becomes valuable to develop a simple wear test that can produce reliable, reproducible, and straight forward.
Measurement Objective
In this study, we simulated and compared the wear behaviors of three types of wood to showcase the capability of the Nanovea Tribometer in evaluating the tribological properties of wood in a controlled and monitored manner.
Discussion
Sample Description: Antique Birch Hardwood has a 7-layer aluminum oxide finish, providing everyday wear and tear protection. Courtship Grey Oak, & Santos Mahogany are both laminate flooring types that vary in surface finish and gloss. The Courtship Grey Oak is a slate gray color, EIR finish, and low gloss. On the other hand, Santos Mahogany is a dark burgundy color, prefinished, and high gloss which allows surface scratches and defects to be more easily hidden.
The evolution of COF during the wear tests of the three wood flooring samples are plotted in Fig. 1. The Antique Birch Hardwood, Courtship Grey Oak, & Santos Mahogany samples all showed different COF behavior.
It can be observed in the graph above that Antique Birch Hardwood was the only sample that demonstrated a steady COF for the duration of an entire test. The Courtship Grey Oak’s sharp increase in COF and then gradual decrease could be indicative that the sample’s surface roughness largely contributed to its COF behavior. As the sample wore, the surface roughness decreased and became more homogenous which explains the decrease in COF as the sample surface became smoother from mechanical wear. The COF on Santos Mahogany displays a smooth gradual increase in COF at the beginning of the test and then transitioned abruptly into a choppy COF trend. This could indicate that once the laminate coating started to wear through, the steel ball (counter material) made contact with the wood substrate which wore in a quicker and turbulent manner creating the noisier COF behavior towards the end of the test.
Antique Birch Hardwood:
Courtship Grey Oak:
Santos Mahogany
Table 2 summarizes the results of the wear track scans and analysis on all wood flooring samples after the wear tests were performed. Detailed information and images for each sample can be seen in Figures 2-7. Based on the Wear Rate comparison between all three samples, we can deduct that Santos Mahogany proved to be less resilient to mechanical wear than the other two samples. Antique Birch Hardwood and Courtship Grey Oak had very similar wear rates although their wear behavior during their tests differed significantly. Antique Birch Hardwood had a gradual and more uniform wear trend while Court-ship Grey Oak showed a shallow and pitted wear track due to the pre-existing surface texture and finish
Conclusion
In this study, we showcased the capacity of Nanovea’s Tribometer in evaluating the coefficient of friction and wear resistance of three types of wood, Antique Birch Hardwood, Courtship Grey Oak, and Santos Mahogany in a controlled and monitored manner. The superior mechanical properties of the Antique Birch Hardwood leads to its better wear resistance. The texture and homogeneity of the wood surface play an important role in the wear behavior. The Courtship Grey Oak surface texture such as gaps or cracks between the wood cell fibers may become the weak spots where the wear initiates and propagates.
NOW, LET'S TALK ABOUT YOUR APPLICATION

Portability and Flexibility of the Jr25 3D Non-contact Profilometer
Understanding and quantifying a sample’s surface is crucial for many applications including quality control and research. To study surfaces, profilometers are often used to scan and image samples. A large problem with conventional profilometry instruments is the inability to accommodate for non conventional samples. Difficulties in measuring non conventional samples can occur due to sample size, geometry, inability to move the sample, or other inconvenient sample preparations. Nanovea’s portable 3D non-contact profilometers, the JR series, is able to solve most of these problems with its ability to scan sample surfaces from varying angles and its portability.

A Better Look at Paper
Paper has played a large role in information distribution since its invention in the 2nd century [1]. Paper consists of intertwined fibers, typically obtained from trees, that have been dried into thin sheets. As a medium for information storage, paper has allowed the spread of ideas, art, and history over long distances and through passing time.
Today, paper is commonly used for currency, books, toiletries, packaging, and more. Paper is processed in different ways to obtain properties to match their application. For example, the visually appealing, glossy paper from a magazine is different compared to rough, cold-pressed watercolor paper. The method in which paper is produced will affect the surface properties of the paper. This influences how ink (or other medium) will settle onto and appear on the paper. To inspect how different paper processes affect surface properties, Nanovea inspected the roughness and texture of various types of paper by conducting a large area scan with our 3D Non-Contact Profilometer.
Click to learn about the Surface Roughness of Paper!
Categories
- Application Notes
- Block on Ring Tribology
- Corrosion Tribology
- Friction Testing | Coefficient of Friction
- High Temperature Mechanical Testing
- High Temperature Tribology
- Humidity and Gases Tribology
- Humidity Mechanical Testing
- Indentation | Creep and Relaxation
- Indentation | Fracture Toughness
- Indentation | Hardness and Elastic
- Indentation | Loss and Storage
- Indentation | Stress vs Strain
- Indentation | Yield Strength and Fatigue
- Laboratory Testing
- Linear Tribology
- Liquid Mechanical Testing
- Liquid Tribology
- Low Temperature Tribology
- Mechanical Testing
- Press Release
- Profilometry | Flatness and Warpage
- Profilometry | Geometry and Shape
- Profilometry | Roughness and Finish
- Profilometry | Step Height and Thickness
- Profilometry | Texture and Grain
- Profilometry | Volume and Area
- Profilometry Testing
- Ring on Ring Tribology
- Rotational Tribology
- Scratch Testing | Adhesive Failure
- Scratch Testing | Cohesive Failure
- Scratch Testing | Multi-Pass Wear
- Scratch Testing | Scratch Hardness
- Scratch Testing Tribology
- Tradeshow
- Tribology Testing
- Uncategorized
Archives
- September 2023
- August 2023
- June 2023
- May 2023
- July 2022
- May 2022
- April 2022
- January 2022
- December 2021
- November 2021
- October 2021
- September 2021
- August 2021
- July 2021
- June 2021
- May 2021
- March 2021
- February 2021
- December 2020
- November 2020
- October 2020
- September 2020
- July 2020
- May 2020
- April 2020
- March 2020
- February 2020
- January 2020
- November 2019
- October 2019
- September 2019
- August 2019
- July 2019
- June 2019
- May 2019
- April 2019
- March 2019
- January 2019
- December 2018
- November 2018
- October 2018
- September 2018
- July 2018
- June 2018
- May 2018
- April 2018
- March 2018
- February 2018
- November 2017
- October 2017
- September 2017
- August 2017
- June 2017
- May 2017
- April 2017
- March 2017
- February 2017
- January 2017
- November 2016
- October 2016
- August 2016
- July 2016
- June 2016
- May 2016
- April 2016
- March 2016
- February 2016
- January 2016
- December 2015
- November 2015
- October 2015
- September 2015
- August 2015
- July 2015
- June 2015
- May 2015
- April 2015
- March 2015
- February 2015
- January 2015
- November 2014
- October 2014
- September 2014
- August 2014
- July 2014
- June 2014
- May 2014
- April 2014
- March 2014
- February 2014
- January 2014
- December 2013
- November 2013
- October 2013
- September 2013
- August 2013
- July 2013
- June 2013
- May 2013
- April 2013
- March 2013
- February 2013
- January 2013
- December 2012
- November 2012
- October 2012
- September 2012
- August 2012
- July 2012
- June 2012
- May 2012
- April 2012
- March 2012
- February 2012
- January 2012
- December 2011
- November 2011
- October 2011
- September 2011
- August 2011
- July 2011
- June 2011
- May 2011
- November 2010
- January 2010
- April 2009
- March 2009
- January 2009
- December 2008
- October 2008
- August 2007
- July 2006
- March 2006
- January 2005
- April 2004