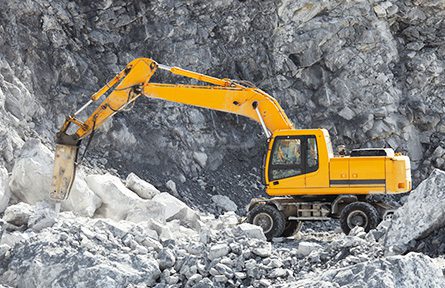
TRIBOMETER
NANOVEA Tribometer is a powerful and adaptable all-in-one friction and wear tester with the widest range of testing and environmental modules on the market. The simple design of a NANOVEA Tribometer allows for fast interchangeability to accommodate for any research need and requirement or standard.
Advanced Pneumatic Technology allows for stable applications of normal force at speeds of 0.001 to 15000 rpm (10+ m/s) for highly accurate wear, scratch, friction, lubrication and mechanical property evaluations, which are then measured in seconds with an integrated NANOVEA 3D Optical Profilometer.
Wear Testing Modules include Rotational, Linear, Block-On-Ring, Ring-On-Ring and Scratch. Tribometer environmental modules include Corrosion, High and Low Temperature, Liquid and Humidity. NANOVEA Tribometers are a culmination of over 25 years of experience empowering materials testing and quality control in companies all over the world.
NANOVEA TRIBOMETER MODELS
WEAR & FRICTION MODULES
ENVIRONMENTAL MODULES
Unmatched Speed Control (0.01 to 15000 rpm)
Advanced Pneumatic Technology
Integrated Optical Profiler
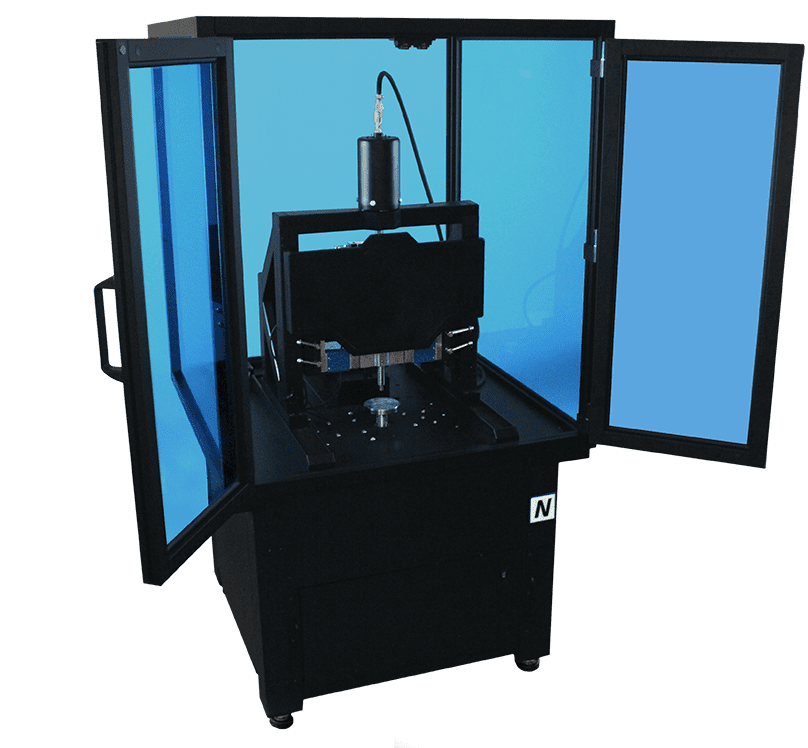
