Category: Indentation | Yield Strength and Fatigue
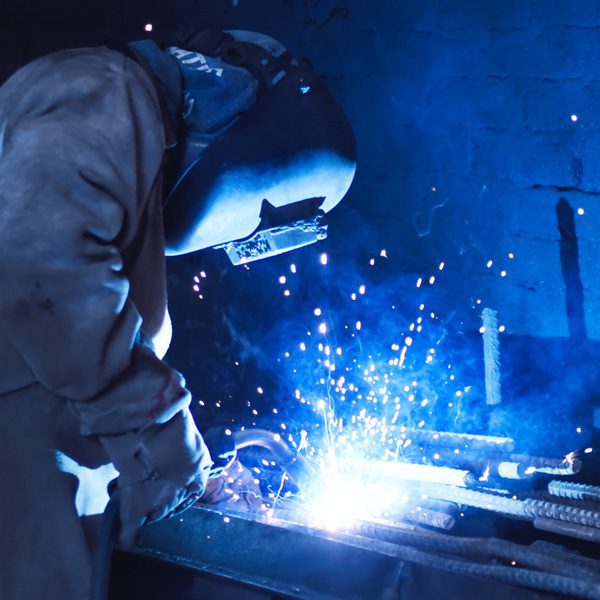
Yield and Tensile Strength of Steel and Aluminum
Importance of Yield Strength and Ultimate Tensile Strength Measurement using Indentation
Traditionally Yield Strength and Ultimate Tensile Strength have been tested using a large tensile testing machine requiring enormous strength to pull apart test specimens. It is costly and time-consuming to properly machine many test coupons for a material where each sample can only be tested once. Small defects in the sample create a noticeable variance in test results. Different configurations and alignments of the tensile testers in the market often result in substantial variations in testing mechanics and outcomes.
Measurement Objective
In this application, the Nanovea Mechanical Tester measures the Yield Strength and Ultimate Tensile Strength of stainless steel SS304 and aluminum Al6061 metal alloy samples. The samples were chosen for their commonly recognized Yield Strength and Ultimate Tensile Strength values showing the reliability of Nanovea’s indentation methods.
Test Procedure and Procedures
The Yield Strength and Ultimate Tensile Strength tests were performed on the Nanovea Mechanical Tester in the Microindentation mode. A cylindrical flat diamond tip of 200 μm diameter was used for this application. SS304 and Al6061 alloys were selected for their extensive industrial application and commonly recognized Yield Strength and Ultimate Tensile Strength values, in order to show the great potential and reliability of the indentation method. Samples were mechanically polished to a mirror-like finish before testing to avoid surface roughness or defect influence on test results. Test conditions are listed in Table 1. More than ten tests were performed on each sample to ensure the repeatability of the test values.
Results and Discussion
Load-displacement curves of the SS304 and Al6061 alloy samples are shown in Figure 3 with the flat indenter imprints on the test samples inset. Analysis of the “S” shaped loading curve using special algorithms developed by Nanovea calculates Yield Strength and Ultimate Tensile Strength . Values are automatically calculated by the software as summarized in Table 1. Yield Strength and Ultimate Tensile Strength values obtained by conventional tensile tests are listed for comparison.
Conclusion
In this study, we showcased the capacity of Nanovea Mechanical Tester in evaluating Yield Strength & Ultimate Tensile Strength of stainless steel and aluminum alloy sheet samples. The simple experimental setup significantly cuts the time and cost for sample preparation required for tensile tests. The small indentation size makes it possible to perform multiple measurements on one single sample. This method allows YS/UTS measurements on small samples and localized areas, providing a solution for YS/UTS mapping and local defect detection of pipelines or auto structure.
The Nano, Micro or Macro modules of the Nanovea Mechanical Tester all include ISO and ASTM compliant indentation, scratch and wear tester modes, providing the widest and most user friendly range of testing available in a single system. Nanovea’s unmatched range is an ideal solution for determining the full range of mechanical properties of thin or thick, soft or hard coatings, films and substrates, including hardness, Young’s modulus, fracture toughness, adhesion, wear resistance and many others. In addition, optional 3D non-contact profiler and AFM Module are available for high resolution 3D imaging of indentation, scratch and wear track in addition to other surface measurements such as roughness.
NOW, LET'S TALK ABOUT YOUR APPLICATION
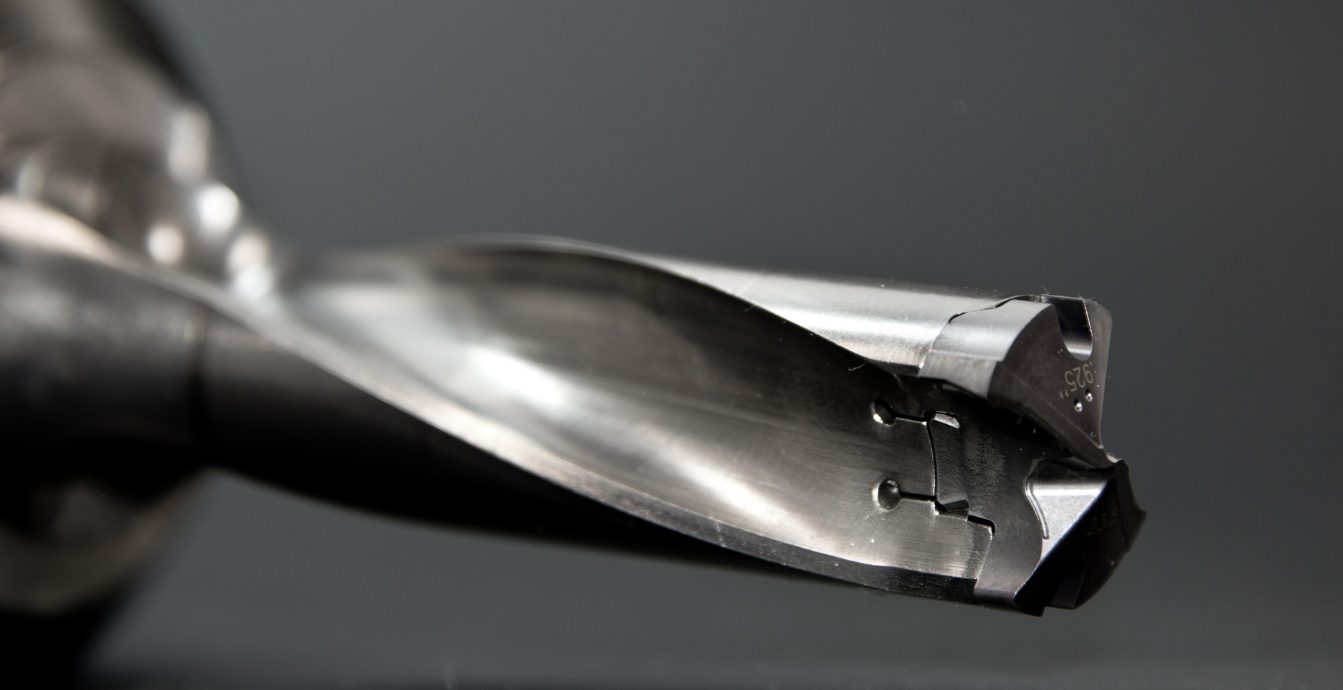
Cyclical Nanoindentation Stress-Strain Measurement
Cyclical Nanoindentation Stress-Strain Measurement
Learn more
Importance of Nanoindentation
Continuous stiffness measurements (CSM) obtained by nanoindentation reveals the stress-strain relationship of materials with minimally invasive methods. Unlike traditional tensile testing methods, nanoindentation provides stress-strain data at the nanoscale without the need of a large instrument. The stress-strain curve provides crucial information on the threshold between elastic and plastic behavior as the sample is subject to increasing loads. CSM gives the capability to determine the yield stress of a material without dangerous equipment.
Nanoindentation provides a reliable and user-friendly method to quickly investigate stress-strain data. Furthermore, measuring stress-strain behavior on the nanoscale makes it possible to study important properties on small coatings and particles in materials as they get more advanced. Nanoindentation provides information on elastic limit and yield strength in addition to hardness, elastic modulus, creep, fracture toughness, etc. making it a versatile metrology instrument.
The stress-strain data provided by nanoindentation in this study identifies the elastic limit of the material while only going 1.2 microns into the surface. We use CSM to determine how mechanical properties of materials develop as an indenter travels deeper into the surface. This is especially useful in thin film applications where properties can be depth dependent. Nanoindentation is a minimally invasive method of confirming material properties in test samples.
The CSM test is useful in measuring material properties versus depth. Cyclical tests can be performed at constant loads to determine more complex material properties. This can be useful to study fatigue or eliminate the effect of porosity to obtain true elastic modulus.
Measurement Objective
In this application, the Nanovea mechanical tester uses CSM to study hardness and elastic modulus versus depth and stress-strain data on a standard steel sample. Steel was chosen for its commonly recognized characteristics to display the control and accuracy of the nanoscale stress-strain data. A spherical tip with a 5-micron radius was used to reach high enough stresses beyond the elastic limit for steel.
Test Conditions & Procedures
The following indentation parameters were used:
Results:
Increase in load during oscillations provide the following depth versus load curve. Over 100 oscillations were conducted during loading to find the stress-strain data as the indenter penetrates the material.
We determined stress and strain from the information obtained at each cycle. The maximum load and depth at each cycle allows us to calculate the maximum stress applied in each cycle to the material. Strain is calculated from the residual depth at each cycle from the partial unloading. This allows us to calculate the radius of the residual imprint by dividing the radius of the tip to give the strain factor. Plotting stress versus strain for the material shows the elastic and plastic zones with the corresponding elastic limit stress. Our tests determined the transition between the elastic and plastic zones of the material to be around 0.076 strain with an elastic limit of 1.45 GPa.
Each cycle acts as a single indent so as we increase load, we run tests at various controlled depths in the steel. So, hardness and elastic modulus versus depth can be plotted directly from the data obtained for each cycle.
As the indenter travels into the material we see hardness increase and elastic modulus decrease.
Conclusion
We have shown the Nanovea mechanical tester provides reliable stress-strain data. Using a spherical tip with CSM indentation allows for material property measurement under increased stress. Load and indenter radius can be changed to test various materials at controlled depths. Nanovea mechanical testers provide these indentation tests from the sub mN range to 400N.
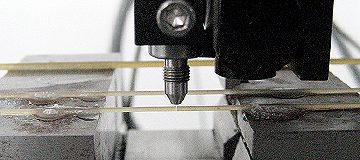
3 Point Bend Test Using Microindentation
In this application, the Nanovea Mechanical Tester, in Microindentation mode, is used to measure the flexural strength (using 3 Point Bend) of various sized rod samples (pasta) to show a range of data. 2 different diameters were chosen to demonstrate both elastic and brittle characteristics. Using a flat tip indenter to apply a point load, we determine stiffness (Young’s Modulus) and identify the critical loads at which the sample will fracture.
Categories
- Application Notes
- Block on Ring Tribology
- Corrosion Tribology
- Friction Testing | Coefficient of Friction
- High Temperature Mechanical Testing
- High Temperature Tribology
- Humidity and Gases Tribology
- Humidity Mechanical Testing
- Indentation | Creep and Relaxation
- Indentation | Fracture Toughness
- Indentation | Hardness and Elastic
- Indentation | Loss and Storage
- Indentation | Stress vs Strain
- Indentation | Yield Strength and Fatigue
- Laboratory Testing
- Linear Tribology
- Liquid Mechanical Testing
- Liquid Tribology
- Low Temperature Tribology
- Mechanical Testing
- Press Release
- Profilometry | Flatness and Warpage
- Profilometry | Geometry and Shape
- Profilometry | Roughness and Finish
- Profilometry | Step Height and Thickness
- Profilometry | Texture and Grain
- Profilometry | Volume and Area
- Profilometry Testing
- Ring on Ring Tribology
- Rotational Tribology
- Scratch Testing | Adhesive Failure
- Scratch Testing | Cohesive Failure
- Scratch Testing | Multi-Pass Wear
- Scratch Testing | Scratch Hardness
- Scratch Testing Tribology
- Tradeshow
- Tribology Testing
- Uncategorized
Archives
- September 2023
- August 2023
- June 2023
- May 2023
- July 2022
- May 2022
- April 2022
- January 2022
- December 2021
- November 2021
- October 2021
- September 2021
- August 2021
- July 2021
- June 2021
- May 2021
- March 2021
- February 2021
- December 2020
- November 2020
- October 2020
- September 2020
- July 2020
- May 2020
- April 2020
- March 2020
- February 2020
- January 2020
- November 2019
- October 2019
- September 2019
- August 2019
- July 2019
- June 2019
- May 2019
- April 2019
- March 2019
- January 2019
- December 2018
- November 2018
- October 2018
- September 2018
- July 2018
- June 2018
- May 2018
- April 2018
- March 2018
- February 2018
- November 2017
- October 2017
- September 2017
- August 2017
- June 2017
- May 2017
- April 2017
- March 2017
- February 2017
- January 2017
- November 2016
- October 2016
- August 2016
- July 2016
- June 2016
- May 2016
- April 2016
- March 2016
- February 2016
- January 2016
- December 2015
- November 2015
- October 2015
- September 2015
- August 2015
- July 2015
- June 2015
- May 2015
- April 2015
- March 2015
- February 2015
- January 2015
- November 2014
- October 2014
- September 2014
- August 2014
- July 2014
- June 2014
- May 2014
- April 2014
- March 2014
- February 2014
- January 2014
- December 2013
- November 2013
- October 2013
- September 2013
- August 2013
- July 2013
- June 2013
- May 2013
- April 2013
- March 2013
- February 2013
- January 2013
- December 2012
- November 2012
- October 2012
- September 2012
- August 2012
- July 2012
- June 2012
- May 2012
- April 2012
- March 2012
- February 2012
- January 2012
- December 2011
- November 2011
- October 2011
- September 2011
- August 2011
- July 2011
- June 2011
- May 2011
- November 2010
- January 2010
- April 2009
- March 2009
- January 2009
- December 2008
- October 2008
- August 2007
- July 2006
- March 2006
- January 2005
- April 2004