Category: Mechanical Testing
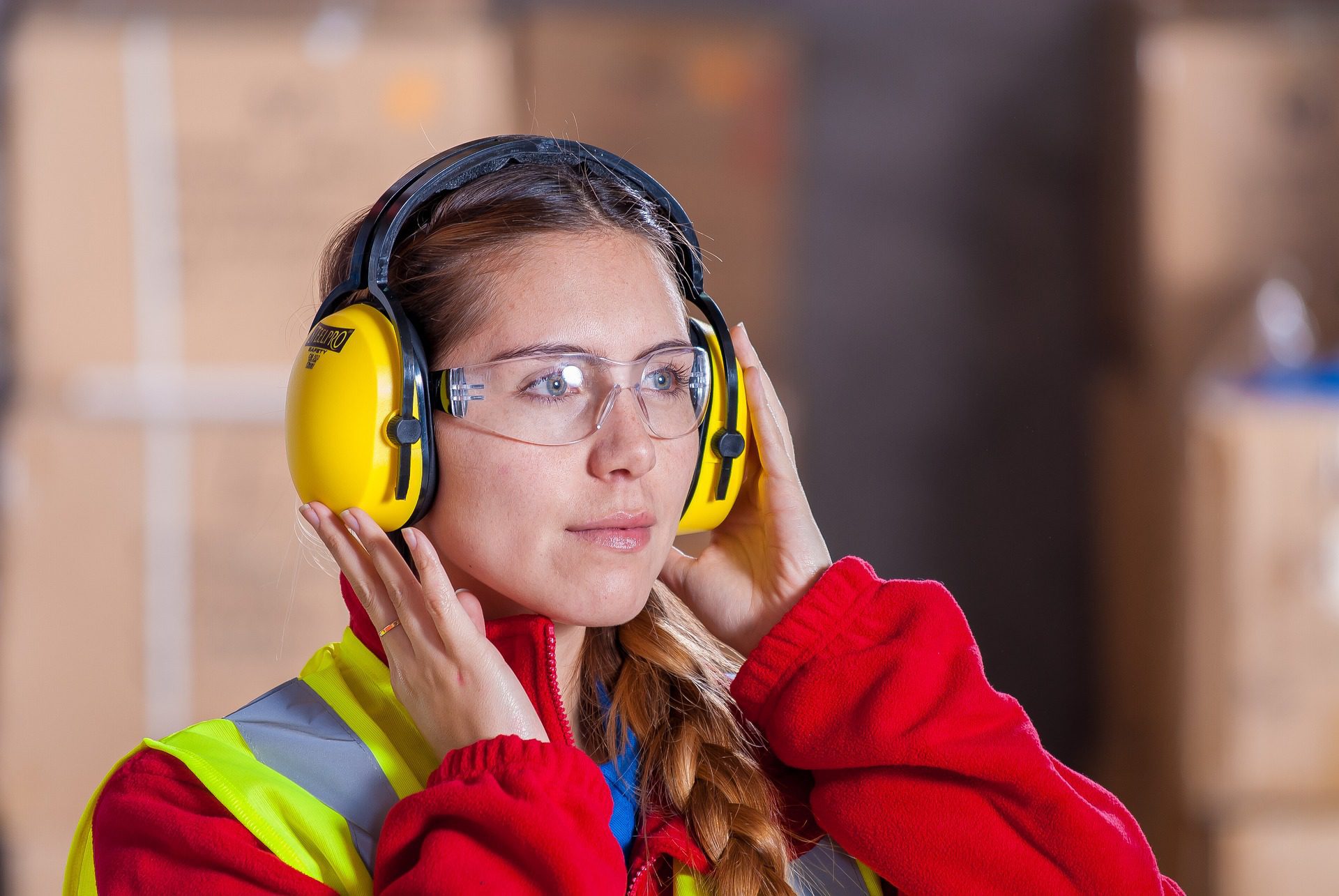
A BETTER Look at Polycarbonate Lens
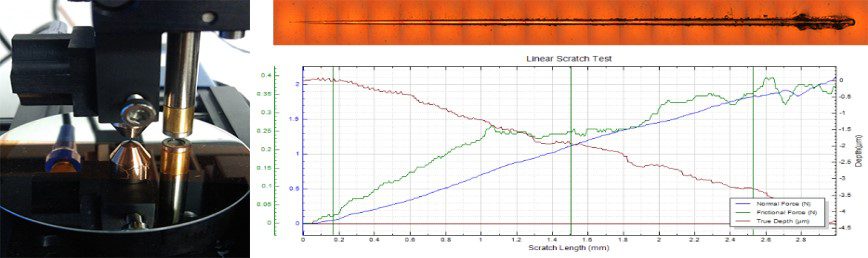
Scratch Testing on Multi-Layered Thin Film
Coatings used extensively throughout multiple industries to preserve the underlying layers, to create electronic devices, or to improve surface properties of materials. Due to their numerous uses coatings are extensively studied, but their mechanical properties can be difficult to understand. Failure of coatings can occur in the micro/nanometer range from surface-atmosphere interaction, cohesive failure, and poor substrate-interface adhesion. A consistent method to test for coating failures is scratch testing. By applying a progressively increasing load, cohesive (e.g. cracking) and adhesive (e.g. delamination) failures of coatings can be quantitatively compared.
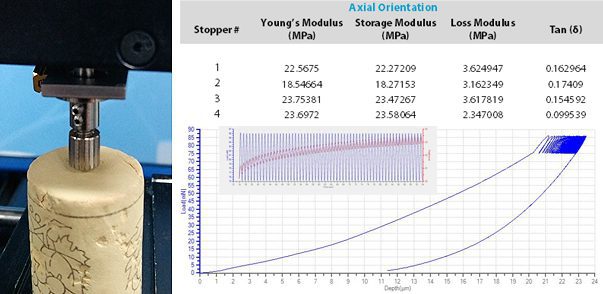
Dynamic Mechanical Analysis With Nanoindentation
The quality of corks depends heavily on its mechanical and physical property. Its ability to seal wine can be identified as these important factors: flexibility, insulation, resilience, and impermeability to gas and liquids. By conducting dynamic mechanical analysis (DMA) testing, its flexibility and resilience properties can be gauged with a quantifiable method. These properties are characterized with Nanovea Mechanical Tester’s Nanoindentaion in the form of Young’s modulus, storage modulus, loss modulus, and tan delta (tan (δ)). Other data that can be gathered from DMA testing are phase shift, hardness, stress, and strain of the material.

Mechanical Properties of Silicon Carbide Wafer Coatings
Understanding the mechanical properties of silicon carbide wafer coatings is critical. The fabrication process for microelectronic devices can have over 300 different processing steps and can take anywhere from six to eight weeks. During this process, the wafer substrate must be able to withstand the extreme conditions of manufacturing, since a failure at any step would result in the loss of time and money. The testing of hardness, adhesion/scratch resistance and COF/wear rate of the wafer must meet certain requirements in order to survive the conditions imposed during the manufacturing and application process to insure a failure will not occur.
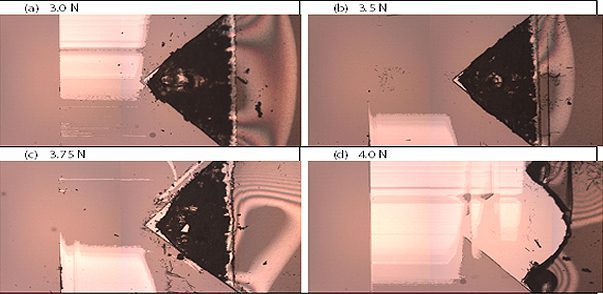
Micro Scrape Test Of Polymeric Coating
Scratch testing has developed to be one of the most widely applied methods to evaluate the cohesive and adhesive strength of the coatings. The critical load, at which a certain type of coating failure occurs as the applied load progressively increases, is widely regarded as a reliable tool to determine and compare the adhesive and cohesive properties of the coatings. The most commonly used indenter for scratch testing is the conical Rockwell diamond indenter. However, when the scratch test is performed on the soft polymeric coating deposited on a brittle substrate such as silicon wafer, the conical indenter tends to plough through the coating forming grooves rather than creating cracks or delamination. Cracking of the brittle silicon wafer takes place when the load further increases. Therefore, it is vital to develop a new technique to evaluate the cohesion or adhesion properties of soft coatings on a brittle substrate.

ASTM D7187 Temperature Effect Using Nanoscratching
ASTM D7187, the resistance of the paint to scratch and mar plays a vital role in its end use. Automotive paint susceptible to scratches makes it difficult and costly to maintain and repair. Different coating architectures of the primer, basecoat, and clearcoat have been developed to achieve the best scratch/mar resistance. Nanoscratch testing has been developed as a standard test method to measure the mechanistic aspects of scratch/mar behavior of paint coatings as described in ASTM D7187. Different elementary deformation mechanisms, namely elastic deformation, plastic deformation and fracture, occur at different loads during the scratch test. It provides a quantitative assessment of the plastic resistance and fracture resistance of the paint coatings.

Self Cleaning Glass Coating Friction Measurement
Self cleaning glass coating possesses a low surface energy that repels both water and oils. Such a coating creates an easy-clean and non-stick glass surface that protects it against grime, dirt and staining. The easy-clean coating substantially cuts the water and energy usage on glass cleaning. It does not require harsh and toxic chemical detergents, making it an eco-friendly choice for a wide variety of residential and commercial applications, such as mirrors, shower glasses, windows and windshields.
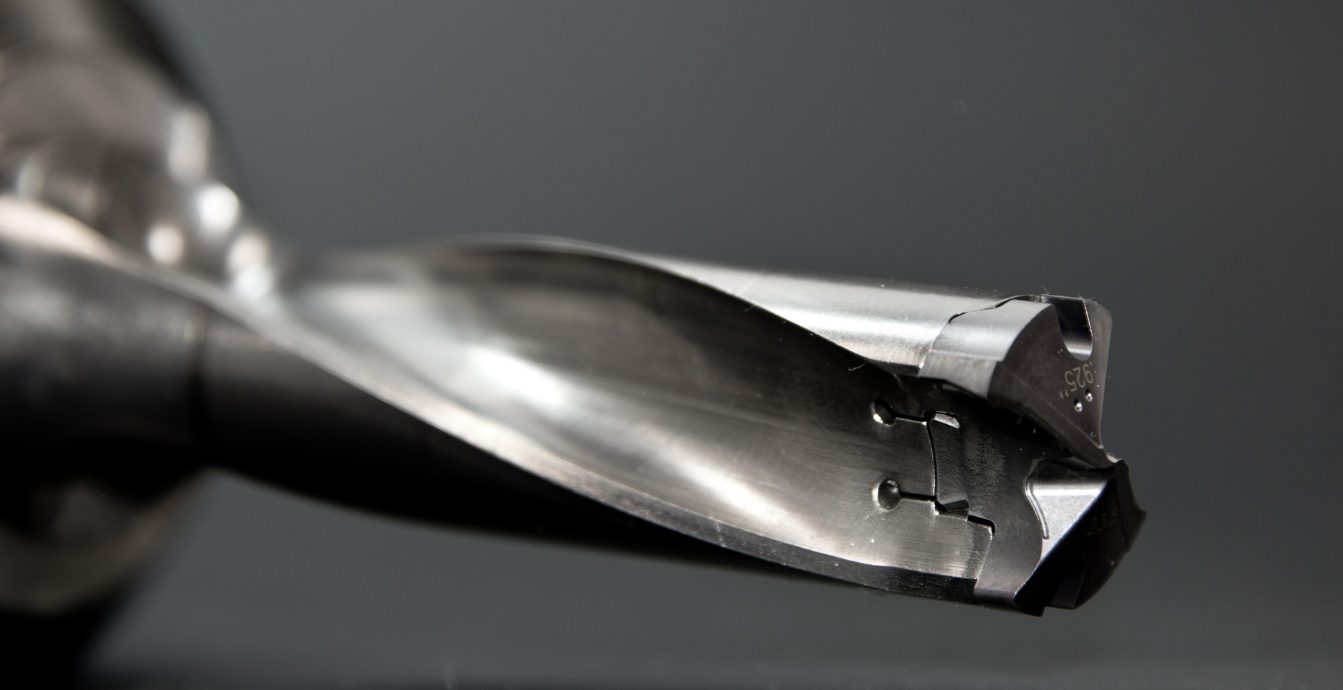
Cyclical Nanoindentation Stress-Strain Measurement

Grooved Stent Coating Failure Using Nano Scratch Testing
Drug–eluting stent is a novel approach in stent technology. It possesses a biodegradable and biocompatible polymer coating that releases medicine slowly and continuously at the local artery to inhibit intimal thickening and prevent the artery from being blocked again. One of the major concerns is the delamination of the polymer coating that carries the drug-eluting layer from the metal stent substrate. In order to improve the adhesion of this coating to the substrate, the stent is designed in different shapes. Specifically in this study, the polymer coating locates at the bottom of the groove on the mesh wire, which brings enormous challenge to the adhesion measurement. A reliable technique is in need to quantitatively measure the interfacial strength between the polymer coating and the metal substrate. The special shape and the small diameter of the stent mesh (comparable to a human hair) require ultrafine X-Y lateral accuracy to locate the test position and proper control and measurement of the load and depth during the test.

Controlled Humidity Nanoindentation of Polymer Films
The mechanical properties of polymer is modified as the environmental humidity elevates. Transient moisture effects, a.k.a. mechano-sorptive effects arises as the polymer absorbs high moisture content and experiences accelerated creep behavior. The higher creep compliance is a result of complex combined effects such as increased molecular mobility, sorption-induced physical aging and sorption-induced stress gradients.
Therefore, a reliable and quantitative test (Humidity Nanoindentation)of the sorption-induced influence on the mechanical behavior of polymeric materials at different moisture level is in need. The Nano module of the Nanovea Mechanical Tester applies the load by a high-precision piezo and directly measures the evolution of force and displacement. Uniform humidity is created surrounding the indentation tip and the sample surface by an isolation enclosure, which ensures measurement accuracy and minimizes the influence of drift caused by humidity gradient.