Category: Application Notes

Micro Scrape Test Of Polymeric Coating
Scratch testing has developed to be one of the most widely applied methods to evaluate the cohesive and adhesive strength of the coatings. The critical load, at which a certain type of coating failure occurs as the applied load progressively increases, is widely regarded as a reliable tool to determine and compare the adhesive and cohesive properties of the coatings. The most commonly used indenter for scratch testing is the conical Rockwell diamond indenter. However, when the scratch test is performed on the soft polymeric coating deposited on a brittle substrate such as silicon wafer, the conical indenter tends to plough through the coating forming grooves rather than creating cracks or delamination. Cracking of the brittle silicon wafer takes place when the load further increases. Therefore, it is vital to develop a new technique to evaluate the cohesion or adhesion properties of soft coatings on a brittle substrate.
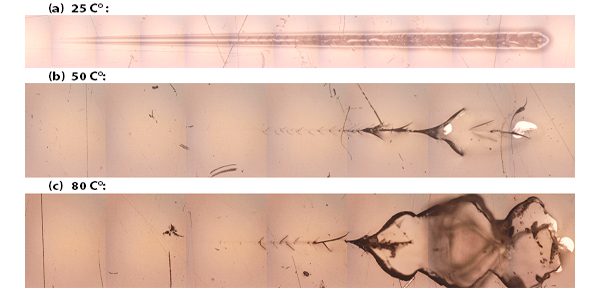
ASTM D7187 Temperature Effect Using Nanoscratching
ASTM D7187, the resistance of the paint to scratch and mar plays a vital role in its end use. Automotive paint susceptible to scratches makes it difficult and costly to maintain and repair. Different coating architectures of the primer, basecoat, and clearcoat have been developed to achieve the best scratch/mar resistance. Nanoscratch testing has been developed as a standard test method to measure the mechanistic aspects of scratch/mar behavior of paint coatings as described in ASTM D7187. Different elementary deformation mechanisms, namely elastic deformation, plastic deformation and fracture, occur at different loads during the scratch test. It provides a quantitative assessment of the plastic resistance and fracture resistance of the paint coatings.
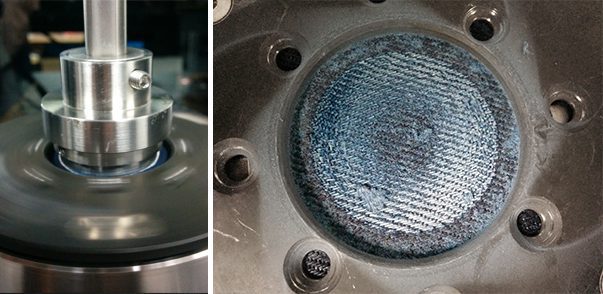
Textile Abrasion Wear By Tribometer
The measurement of textile abrasion resistance of fabrics is very challenging. Many factors play a role during the test, including the mechanical properties of the fibers, the structure of the yarns and the weave of the fabrics. This may result in poor reproducibility of test results and create difficulty in comparing values reported from different laboratories. Wear performance of the fabrics is critical to the manufacturers, distributors, and retailers in the textile production chain. A well-controlled quantifiable and reproducible Tribometer wear resistance measurement is crucial to ensure reliable quality control of the fabric production.
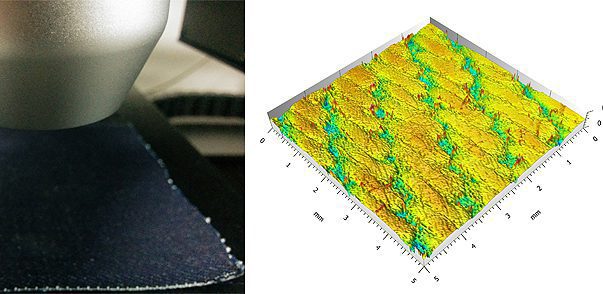
Textile Texture Measurement Using 3D Profilometry
Understanding textile texture, consistency and patterns of the fabrics allows the best selection of processing and control measures. Traditional stylus-based profilometers determine the surface morphology of the coatings by sliding in contact across the measured surface, which may deform the soft fabric and induce inaccurate measurement. The Nanovea 3D Non-Contact Profilometer utilize chromatic confocal technology with unmatched capability to provide a comprehensive analysis of the surface feature of fabrics, making it an ideal tool for reliable product inspection and quality control.
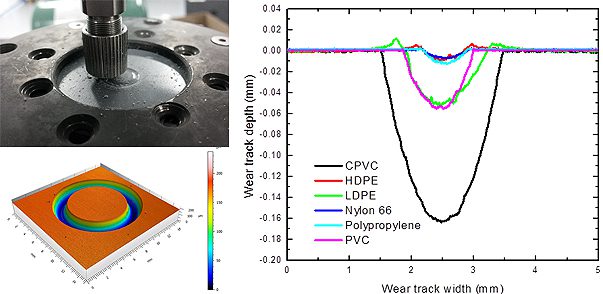
Tribology of Polymers by Tribometer
Tribology of Polymers are commonly seen for tribological applications, such as tires, bearings and conveyor belts. Different wear mechanisms occur depending on the mechanical properties of the polymer, the contact conditions, and the properties of the debris or transfer film formed during the wear process. In order to ensure that the polymers possess sufficient wear resistance under the service conditions, reliable and quantifiable tribological evaluation is in need. It allows us to quantitatively compare the wear behaviors of different polymers in a controlled and monitored manner and to select the best candidate for the target application. The Nanovea Tribometer offers repeatable wear and friction testing using ISO and ASTM compliant rotative and linear modes, with optional high temperature wear and lubrication modules available in one pre-integrated system. This unmatched range allows users to simulate different work environment of the polymers including concentrated stress, wear and high temperature, etc.
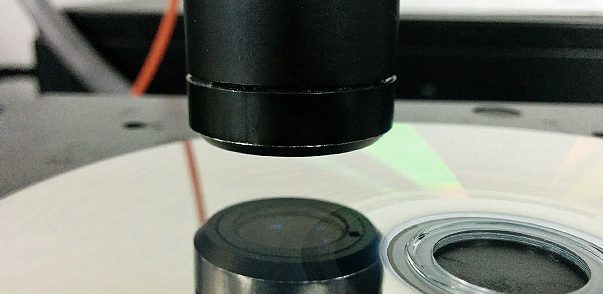
Transparent Film Thickness by 3D Non Contact Profilometry
Transparent film thickness and uniformity is critical for product quality and performance. For example, in CD, DVD and Blu-Ray Disc (BO) production, precise control of the thickness and uniformity of the transparent cover and space layers plays an important role in avoiding focus errors of the laser. Improper injection molding process during CD and BO production may lead to stress-induced birefringence and unreliable data reading. An accurate thickness measurement of the transparent film ensures reliable product inspection and quality control.
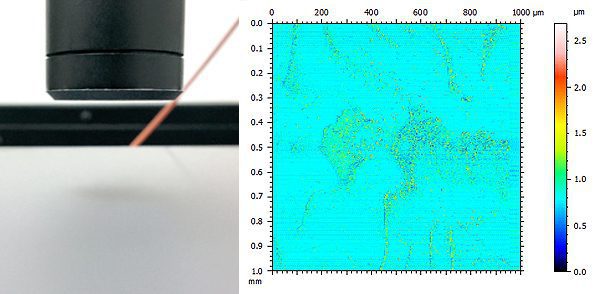
Optoelectronic Film Inspection Using 3D Profilometry
Optoelectronic film devices and systems convert visible or infrared radiation to electrical signals. Thin-film optoelectronic devices have a wide variety of applications, including photocells, solar cells and LEDs, etc. The continual development of the optoelectronic thin films and the associated technologies such as impurity incorporation, etching and surface chemistry aims for improving the photoconversion at micro or nano scale levels.
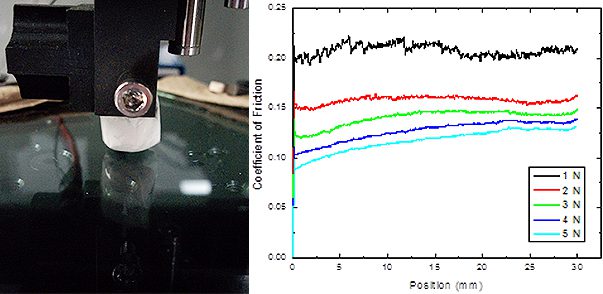
Self Cleaning Glass Coating Friction Measurement
Self cleaning glass coating possesses a low surface energy that repels both water and oils. Such a coating creates an easy-clean and non-stick glass surface that protects it against grime, dirt and staining. The easy-clean coating substantially cuts the water and energy usage on glass cleaning. It does not require harsh and toxic chemical detergents, making it an eco-friendly choice for a wide variety of residential and commercial applications, such as mirrors, shower glasses, windows and windshields.
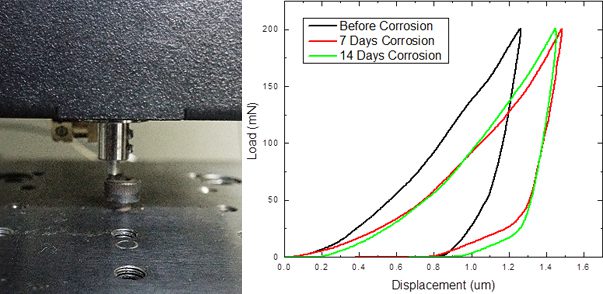
Corrosion Effect On Hardness Using Nanoindentation
The mechanical properties of materials deteriorate during the corrosion process. For example, lepidocrocite (γ-FeOOH) and goethite (α-FeOOH) form in the atmospheric corrosion of carbon steel. Their loose and porous nature results in absorption of moisture and in turn further acceleration of the corrosion process. Akaganeite (β-FeOOH), another form of iron
oxyhydroxide, is generated on the steel surface in chloride containing environments. Nanoindentation can control the indentation depth in the range of nanometers and microns, making it possible to quantitatively measure the hardness and Young’s modulus of the corrosion products formed on the metal surface. It provides physicochemical insight in corrosion mechanisms involved so as to select the best candidate material for the target applications.