Category: Profilometry | Volume and Area

Portability and Flexibility of the Jr25 3D Non-contact Profilometer
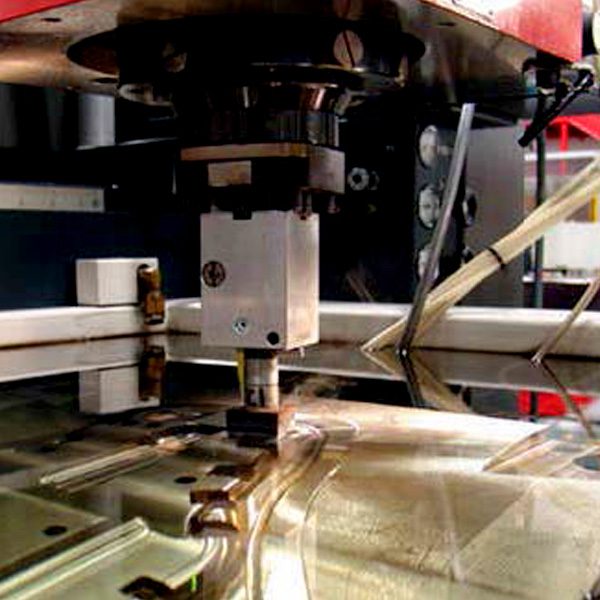
Quality Analysis on Electrical Discharge Machined Metals
Electrical discharge machining, or EDM, is a manufacturing process that removes material via electrical
discharges [1]. This machining process is generally used with conductive metals that would be difficult
to machine with conventional methods.
As with all machining processes, precision and accuracy must be high in order to meet acceptable
tolerance levels. In this application note, the quality of the machined metals will be assessed with a
Nanovea 3D non-contact profilometer.
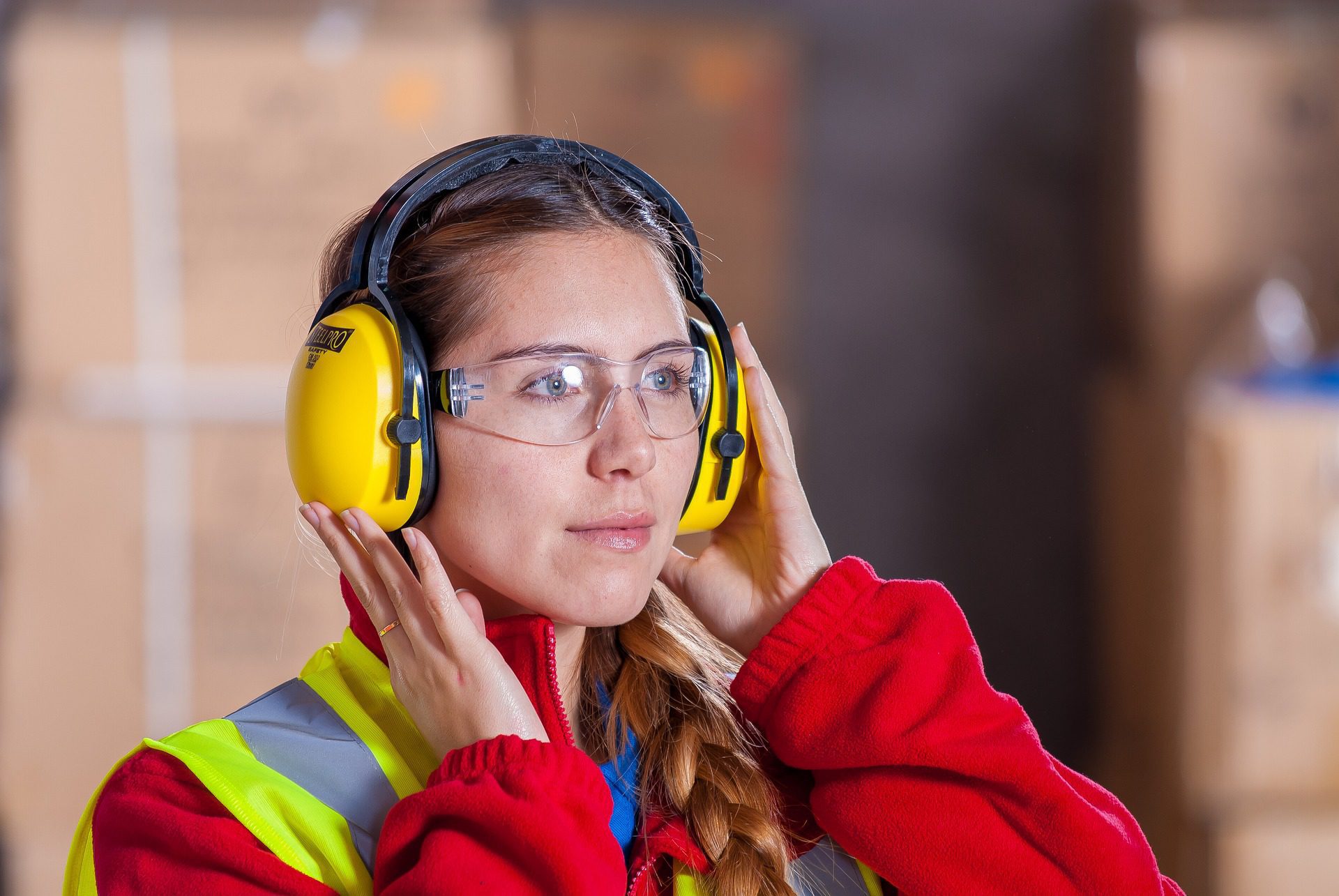
A BETTER Look at Polycarbonate Lens
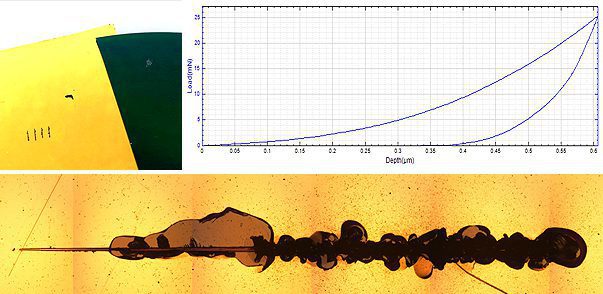
Mechanical Properties of Silicon Carbide Wafer Coatings
Understanding the mechanical properties of silicon carbide wafer coatings is critical. The fabrication process for microelectronic devices can have over 300 different processing steps and can take anywhere from six to eight weeks. During this process, the wafer substrate must be able to withstand the extreme conditions of manufacturing, since a failure at any step would result in the loss of time and money. The testing of hardness, adhesion/scratch resistance and COF/wear rate of the wafer must meet certain requirements in order to survive the conditions imposed during the manufacturing and application process to insure a failure will not occur.
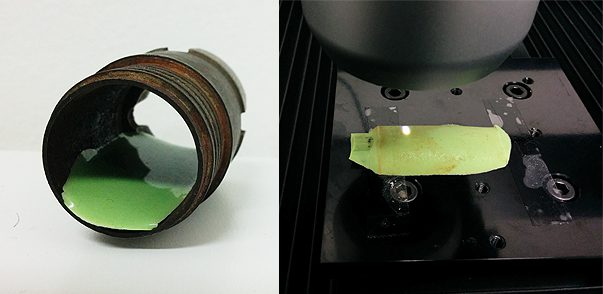
Replica Molding of Inner Pipe Corrosion
Surface finish of the metal pipe is critical for its product quality and performance. Rust progressively builds up and pits initiate and grow on the metal surface as corrosion process takes place, resulting in roughening of the pipe surface. The differential galvanic properties between metals, the ionic influences of solutions as well as the solution pH may all play roles in the pipe corrosion process, leading to corroded metal with different surface features. An accurate surface roughness and texture measurement of the corroded surface provides insight in the mechanisms involved in a specific corrosion process. Conventional profilometers have difficulty in reaching in and measuring the corroded inner pipe wall. Replica molding provides a solution by replicating the inner surface features in a non-destructive way. It can easily be applied on the inner wall of the corroded pipe and sets in 15 min. We scan the replicated surface of the replica molding to obtain the surface morphology of the inner pipe wall.

Surface Analysis of Carbon & Zeolite Catalysts Using 3D Profilometry
In this application the Nanovea ST400 Profilometer is used to measure the surface of carbon and zeolite catalysts. The area measured was selected at random, and assumed large enough in that it could be extrapolated to make assumptions about a much larger surface. Surface roughness and developed area will be used to characterize the available surface area.
Surface Analysis of Carbon & Zeolite Catalysts Using 3D Profilometry

Pitting Corrosion density, area, volume, size and shape
In this application the Nanovea ST400 Profilometer is used to measure the surface of a corrosion pitted stainless steel coupon. The area measured was selected at random, and assumed large enough in that it could be extrapolated to make assumptions
about a much larger surface. Density, area, volume, size and shape will be used here to quantify the level of corrosion.
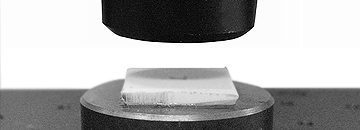
Micro Scratch Depth Measurement Using 3D Profilometry
In this application the Nanovea ST400 Profilometer is used for depth measurement of a row of micro scratches created using Nanovea’s Mechanical Tester in scratch mode. In seconds the Profilometer, with a single line pass in 2D mode, provides area and depth measurement.