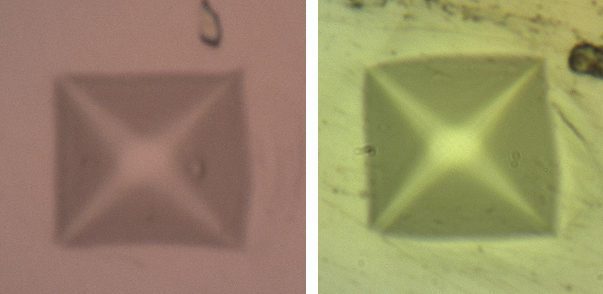
Low Load Vickers Hardness Measurement
During Vickers Hardness inevitable user errors are introduced during the measurement of the imprint under the microscope. Especially at low loads, small measurement errors of the indent size will produce large hardness deviations. In comparison, nanoindentation testing evaluates the mechanical properties of a material by driving the indenter tip into the test material and precisely recording the evolution of load and displacement of the tip. It avoids user errors in imprint size measurement.
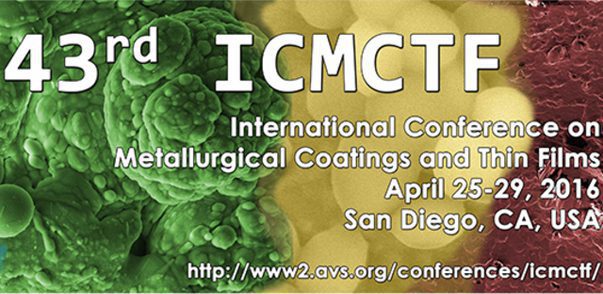
ICMCTF 2016 San Diego | Vist With Nanovea
Visit Nanovea this week at ICMCTF. For more information or to request guest passes please Contact Nanovea.
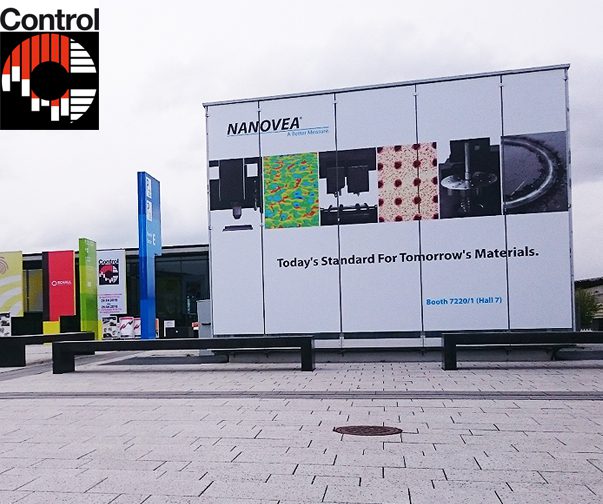
Control 2016 Stuttgart | Visit Booth 7220/1 Hall 7
Learn more about Nanovea at Control 2016 this week at booth 7220/1 Hall 7 in Stuttgart Germany April 26th – 29th.
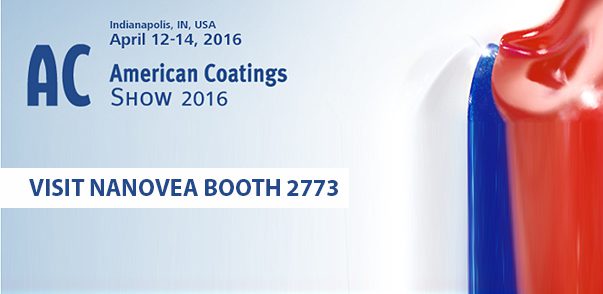
American Coatings Show 2016 | Visit Nanovea @ Booth 2773
Visit Nanovea at American Coatings Show 2016 booth 2773. The Jr25 Profilometer will be displayed on-site for live demos. For more information or to request guest passes please Contact Nanovea.
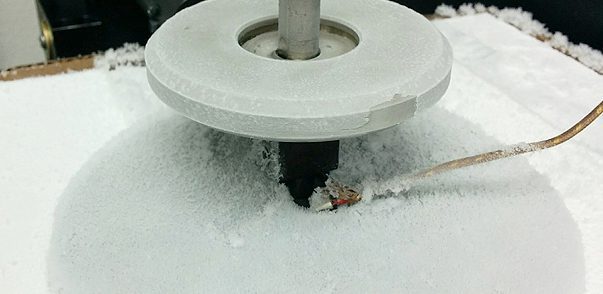
Low Temperature Tribology
A reliable measurement of low temperature tribology, static and dynamic coefficient of friction, COF, as well as wear behavior is needed in order to better understand the tribological performance of materials for sub-zero applications. It provides a useful tool to correlate the frictional property with the influence of various factors, such as reactions at the interface, interlocking surface features, cohesion of surface films, and even microscopic solid static junctions between surfaces at low temperatures.
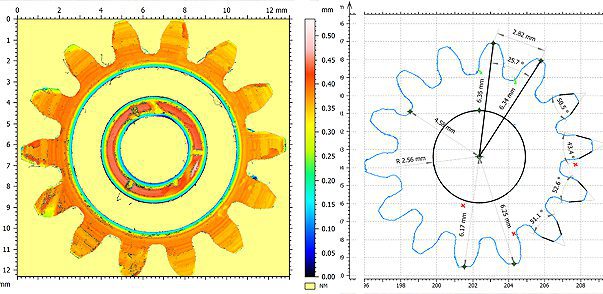
Gear Contour Analysis
Manufacturing of high precision gears requires stringent quality control, in order to obtain the best operational conditions and energy efficiency. Surface defects on the gears may lead to negative impact on the gear mesh quality. Moreover, during the service time, wear and tear takes places, creating surface defects such as dents and cracks in the gears that may result in decreased power transmission efficiency and potential mechanical failure. An accurate and quantifiable tool for surface inspection is in need. Unlike a touch probe technique, the Nanovea Profilometer performs 3D contour analysis of the sample without touching, making it possible to precisely scan samples with a complex shape, such as gears of different geometry.
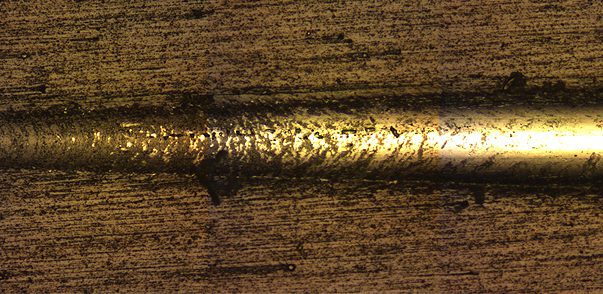
Macro Adhesion Failure of DLC
bits and bearings. Under such extreme conditions, sufficient cohesive and adhesive strength of the coating/substrate system becomes vital. In order to select the best metal substrate for the target application and to establish a consistent coating process for DLC, it is critical to develop a reliable technique to quantitatively assess cohesion and adhesion failure of different DLC coating systems.
Cohesive & Adhesive Strength of DLC Using Macro Scratch Testing
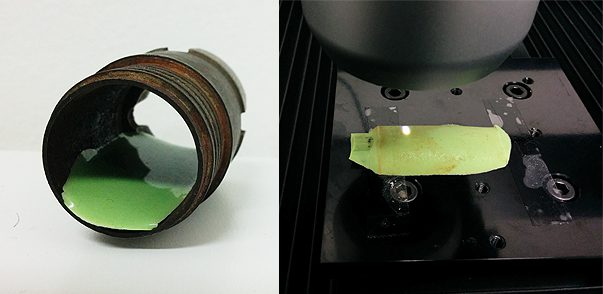
Replica Molding of Inner Pipe Corrosion
Surface finish of the metal pipe is critical for its product quality and performance. Rust progressively builds up and pits initiate and grow on the metal surface as corrosion process takes place, resulting in roughening of the pipe surface. The differential galvanic properties between metals, the ionic influences of solutions as well as the solution pH may all play roles in the pipe corrosion process, leading to corroded metal with different surface features. An accurate surface roughness and texture measurement of the corroded surface provides insight in the mechanisms involved in a specific corrosion process. Conventional profilometers have difficulty in reaching in and measuring the corroded inner pipe wall. Replica molding provides a solution by replicating the inner surface features in a non-destructive way. It can easily be applied on the inner wall of the corroded pipe and sets in 15 min. We scan the replicated surface of the replica molding to obtain the surface morphology of the inner pipe wall.
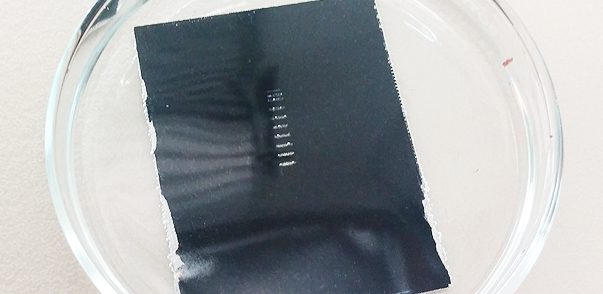
Corrosion Resistance of Coating After Scratch Testing
The corrosion resistant coatings should possess sufficient mechanical strength as they are often exposed to abrasive and erosive application environments. For example, the abrasive oil sands constantly wear away the inside of pipe, which progressively compromise the pipe’s integrity and potentially result in failure. In auto industry, corrosion takes place at the location of scratches on the auto
paint, especially during freezing winter when salts are applied on road. Therefore, a quantitative and reliable tool for measuring the
influence of scratch testing on protective coatings and its corrosion resistance is in need, in order to select the most proper coating for the intended application.
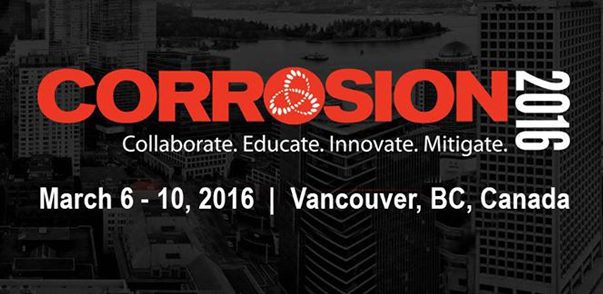
Corrosion 2016 | Visit Nanovea @ Booth 447
Visit Nanovea at Corrosion 2016 booth 447. The Tribometer, equipped with the Tribocorrosion module, will be displayed on-site for live demos. For more information or to request guest passes please Contact Nanovea.