Monthly Archives: November 2015
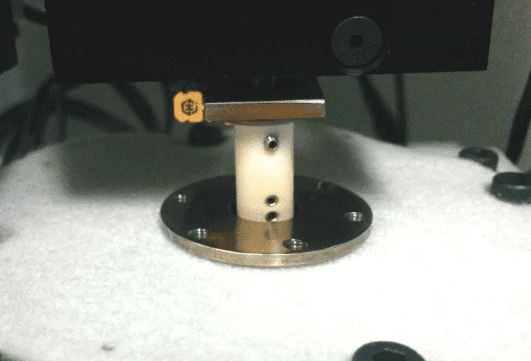
Thermomechanical Analysis of Solder Using Nanoindentation
Solder joints are subjected to thermal and/or external stress when the temperature exceeds 0.6 Tm where Tm is the melting point of the material in Kelvin. The creep behavior of solders at elevated temperatures can directly influence the reliability of solder interconnections. As a result, a reliable and quantitative thermomechanical analysis of the solder at different temperatures is in need. The Nano module of the Nanovea Mechanical Tester applies the load by a high-precision piezo and directly measures the evolution of force and displacement. The advanced heating oven provides a uniform temperature at the tip and sample surface, which ensures measuring accuracy and minimizes the influence of thermal drift.
Thermomechanical Analysis of Solder Using Nanoindentation
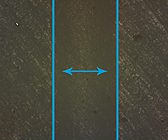
High Temperature Scratch Hardness Using Tribometer
Materials are selected based on the service requirements. For applications involving significant temperature changes and thermal gradients, it is critical to investigate the mechanical properties of materials at high temperatures to be fully aware of the mechanical limits. Materials, especially polymers, usually soften at high temperatures. A lot of mechanical failures are caused by creep deformation and thermal fatigue taking place only at elevated temperatures. Therefore, a reliable technique for measuring high temperature scratch hardness is in need to ensure proper selection of the materials for high temperature applications.
High Temperature Scratch Hardness Using Tribometer
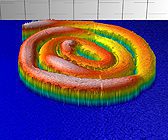
In Situ Morphology at High Temperature Using 3D Profilometry
High temperature environment can change the surface texture, roughness and shapes of materials, resulting in device malfunction and mechanical failures. To ensure the quality of materials or devices used at elevated temperatures, accurate and reliable in situ morphology monitoring of the shape evolution at high temperatures is in need to provide insight into the mechanism of material deformation. Moreover, real-time monitoring of surface morphology at high temperatures is very useful in materials processing, such as laser machining. The Nanovea 3D Non-Contact Profilometers measure the surface morphology of materials without touching the sample, avoiding introducing additional scratches or shape alteration which may be caused by contact technologies such as sliding stylus. Its capacity of non-contact measurement also makes it possible to measure the shape of melted samples.