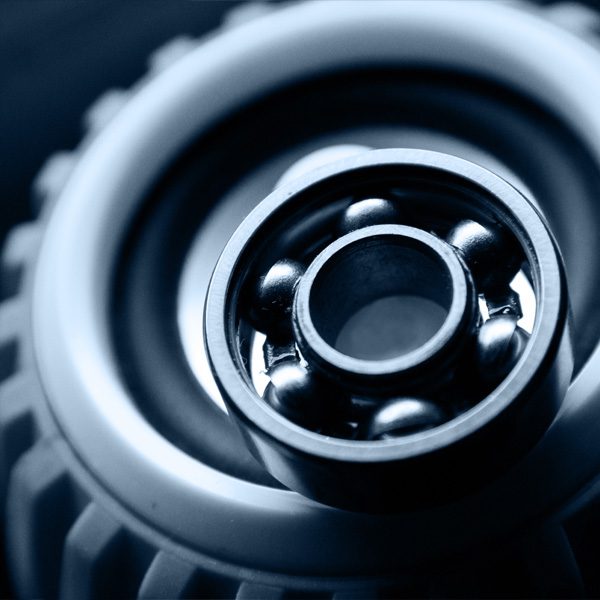
Block-On-Ring Wear Test
IMPORTANCE OF BLOCK-ON-RING WEAR EVALUATION
Block-on-Ring (ASTM G77) test is a widely used technique that evaluates the sliding wear behaviors of materials in different simulated conditions, allows reliable ranking of material couples for specific tribological applications.
MEASUREMENT OBJECTIVE
In this application, the Nanovea Mechanical Tester measures the YS and UTS of stainless steel SS304 and aluminum Al6061 metal alloy samples. The samples were chosen for their commonly recognized YS and UTS values showing the reliability of Nanovea’s indentation methods.
The sliding wear behavior of an H-30 block on an S-10 ring was evaluated by Nanovea’s tribometer using the Block-on-Ring module. The H-30 block is made of 01 tool steel of 30HRC hardness, while the S-10 ring is steel type 4620 of surface hardness 58 to 63 HRC and ring diameter of ~34.98 mm. Block-on-Ring tests were performed in dry and lubricated environments to investigate the effect on wear behavior. Lubrication tests were performed in USP heavy mineral oil. The wear track was examined using Nanovea’s 3D non-contact profilometer. Test parameters are summarized in Table 1. The wear rate (K), was evaluated using the formula K=V/(F×s), where V is the worn volume, F is the normal load, s is the sliding distance.
RESULTS AND DISCUSSION
Figure 2 compares the coefficient of friction (COF) of the Block-on-Ring tests in dry and lubricated environments. The block has significantly more friction in a dry environment than a lubricated environment. COF
fluctuates during the run-in period in the first 50-revolution and reaches a constant COF of ~0.8 for the rest of the 200-revolution wear test. In comparison, the Block-on-Ring test performed in the USP heavy mineral oil lubrication exhibits constant low COF of 0.09 throughout the 500,000-revolution wear test. The lubricant significantly reduces the COF between the surfaces by ~90 times.
Figures 3 and 4 show the optical images and cross-section 2D profiles of the wear scars on the blocks after dry and lubricated wear tests. The wear track volumes and wear rates are listed in Table 2. The steel block after the dry wear test at a lower rotational speed of 72 rpm for 200 revolutions exhibits a large wear scar volume of 9.45 mm˙. In comparison, the wear test carried out at a higher speed of 197 rpm for 500,000 revolutions in the mineral oil lubricant creates a substantially smaller wear track volume of 0.03 mm˙.
The images in ÿgure 3 show severe wear takes place during tests in the dry conditions compared to the mild wear from the lubricated wear test. High heat and intense vibrations generated during the dry wear test promotes oxidation of metallic debris resulting in severe three-body abrasion. In the lubricated test the mineral oil reduces friction and cools the contact face as well as transporting abrasive debris created during wear away. This leads to signiÿcant reduction of wear rate by a factor of ~8×10ˆ. Such a substantial di˛erence in wear resistance in di˛erent environments shows the importance of proper sliding wear simulation in realistic service conditions.
Wear behavior can change drastically when small changes in test conditions are introduced. The versatility of Nanovea’s tribometer allows wear measurement in high temperature, lubrication, and tribocorrosion conditions. The accurate speed and position control by the advanced motor enables wear tests to be performed at speeds ranging from 0.001 to 5000 rpm, making it an ideal tool for research/testing labs to investigate the wear in di˛erent tribological conditions.
The surface condition of the samples was examined by Nanovea’s non-contact optical proÿlometer. Figure 5 shows the surface morphology of the rings after the wear tests. The cylinder form is removed to better present the surface morphology and roughness created by the sliding wear process. Signiÿcant surface roughening took place due to the three-body abrasion process during the dry wear test of 200 revolutions. The block and ring after the dry wear test exhibit a roughness Ra of 14.1 and 18.1 µm, respectively, compared to 5.7 and 9.1 µm for the long-term 500,000 – revolution lubricated wear test at a higher speed. This test demonstrates the importance of proper lubrication of piston ring-cylinder contact. Severe wear quickly damages the contact surface without lubrication and leads to irreversible deterioration of the service quality and even breakage of the engine.
CONCLUSION
In this study we showcase how Nanovea’s Tribometer is used to evaluate the sliding wear behavior of a steel metal couple using the Block-on-Ring module following the ASTM G77 Standard. The lubricant plays a critical role in the wear properties of the material couple. The mineral oil reduces the wear rate of the H-30 block by a factor of ~8×10ˆ and the COF by ~90 times. The versatility of Nanovea’s Tribometer makes it an ideal tool for measuring wear behavior under various lubrication, high temperature, and tribocorrosion conditions.
Nanovea’s Tribometer o˛ers precise and repeatable wear and friction testing using ISO and ASTM compliant rotative and linear modes, with optional high-temperature wear, lubrication, and tribo-corrosion modules available in one pre-integrated system. Nanovea’s unmatched range is an ideal solution for determining the full range of tribological properties of thin or thick, soft, or hard coatings, ÿlms, and substrates.
NOW, LET'S TALK ABOUT YOUR APPLICATION
Categories
- Application Notes
- Block on Ring Tribology
- Corrosion Tribology
- Friction Testing | Coefficient of Friction
- High Temperature Mechanical Testing
- High Temperature Tribology
- Humidity and Gases Tribology
- Humidity Mechanical Testing
- Indentation | Creep and Relaxation
- Indentation | Fracture Toughness
- Indentation | Hardness and Elastic
- Indentation | Loss and Storage
- Indentation | Stress vs Strain
- Indentation | Yield Strength and Fatigue
- Laboratory Testing
- Linear Tribology
- Liquid Mechanical Testing
- Liquid Tribology
- Low Temperature Tribology
- Mechanical Testing
- Press Release
- Profilometry | Flatness and Warpage
- Profilometry | Geometry and Shape
- Profilometry | Roughness and Finish
- Profilometry | Step Height and Thickness
- Profilometry | Texture and Grain
- Profilometry | Volume and Area
- Profilometry Testing
- Ring on Ring Tribology
- Rotational Tribology
- Scratch Testing | Adhesive Failure
- Scratch Testing | Cohesive Failure
- Scratch Testing | Multi-Pass Wear
- Scratch Testing | Scratch Hardness
- Scratch Testing Tribology
- Tradeshow
- Tribology Testing
- Uncategorized
Archives
- September 2023
- August 2023
- June 2023
- May 2023
- July 2022
- May 2022
- April 2022
- January 2022
- December 2021
- November 2021
- October 2021
- September 2021
- August 2021
- July 2021
- June 2021
- May 2021
- March 2021
- February 2021
- December 2020
- November 2020
- October 2020
- September 2020
- July 2020
- May 2020
- April 2020
- March 2020
- February 2020
- January 2020
- November 2019
- October 2019
- September 2019
- August 2019
- July 2019
- June 2019
- May 2019
- April 2019
- March 2019
- January 2019
- December 2018
- November 2018
- October 2018
- September 2018
- July 2018
- June 2018
- May 2018
- April 2018
- March 2018
- February 2018
- November 2017
- October 2017
- September 2017
- August 2017
- June 2017
- May 2017
- April 2017
- March 2017
- February 2017
- January 2017
- November 2016
- October 2016
- August 2016
- July 2016
- June 2016
- May 2016
- April 2016
- March 2016
- February 2016
- January 2016
- December 2015
- November 2015
- October 2015
- September 2015
- August 2015
- July 2015
- June 2015
- May 2015
- April 2015
- March 2015
- February 2015
- January 2015
- November 2014
- October 2014
- September 2014
- August 2014
- July 2014
- June 2014
- May 2014
- April 2014
- March 2014
- February 2014
- January 2014
- December 2013
- November 2013
- October 2013
- September 2013
- August 2013
- July 2013
- June 2013
- May 2013
- April 2013
- March 2013
- February 2013
- January 2013
- December 2012
- November 2012
- October 2012
- September 2012
- August 2012
- July 2012
- June 2012
- May 2012
- April 2012
- March 2012
- February 2012
- January 2012
- December 2011
- November 2011
- October 2011
- September 2011
- August 2011
- July 2011
- June 2011
- May 2011
- November 2010
- January 2010
- April 2009
- March 2009
- January 2009
- December 2008
- October 2008
- August 2007
- July 2006
- March 2006
- January 2005
- April 2004