Monthly Archives: May 2016
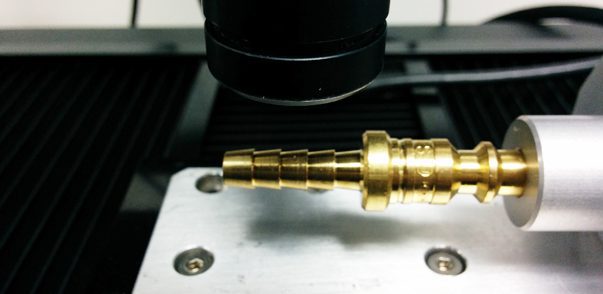
Rotational Measurement Using 3D Profilometry
Surface roughness and texture of the mechanical parts is vital to its end use. Conventional surface profilometry usually scan the sample surface from just one direction. A precise 360° rotational measurement of parts with a cylindrical shape is in need to measure detailed surface feature from different angles. Such 360° 3D inspection ensures the narrowest tolerances in quality control of manufacturing processes. Moreover, during the service time, wear creates dents, cracks, and surface roughening all over the cylindrical part surface. Surface inspection on one face of the sample may miss important information hidden on the backside.
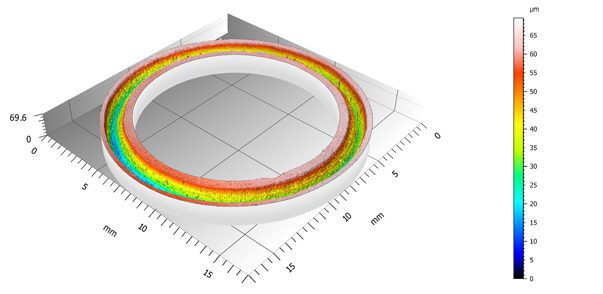
3D Wear Track Scan In Situ on Tribometer
Conventional pin-on-disc or reciprocating tribometer records the COF during the wear test. The wear rate is measured after the wear test by moving the sample to a profilometer and scanning the cross section profiles of the wear track. Such a method may introduce errors when the sample possesses an inhomogeneous wear track. Moreover, samples like multilayer coatings possess different wear resistance at different layers of the coating. A more reliable and repeatable technique for wear evaluation is in need – Nanovea developed a tribometer equipped with a 3D non-contact profilometer that performs a 3D scan of the complete wear track on the sample stage of the tribometer. It monitors the evolution of the 3D wear track morphology, allowing users to accurately calculate the wear rate and determine the failure mode at different stages using one test sample.