Category: Tribology Testing
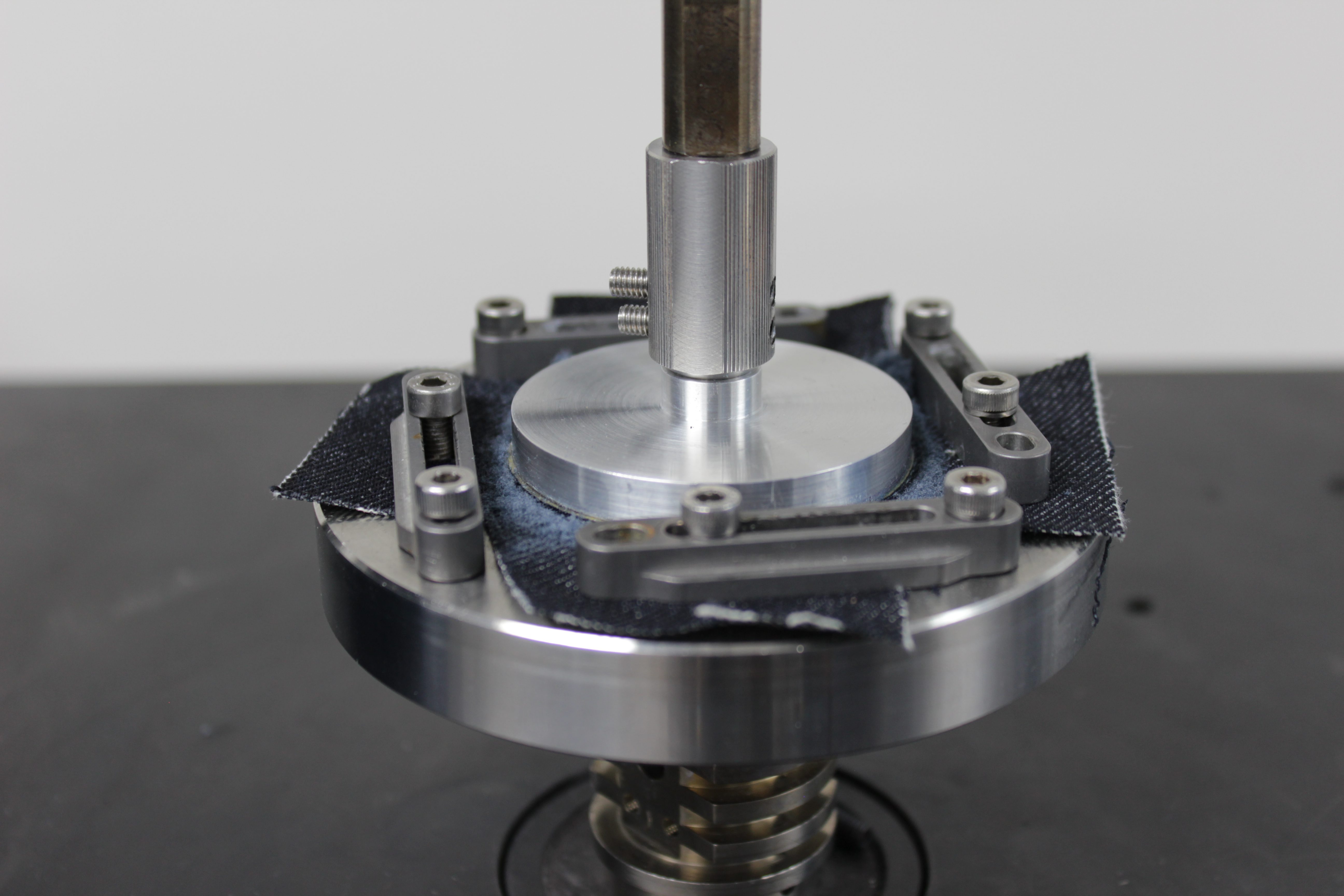
Comparing Abrasion Wear on Denim
Introduction
The form and function of a fabric is determined by its quality and durability. Daily usage of fabrics cause wear and tear on the material, e.g. piling, fuzzing, and discoloration. Subpar fabric quality used for clothing can often lead to consumer dissatisfaction and brand damage.
Attempting to quantify the mechanical properties of fabrics can pose many challenges. The yarn structure and even the factory in which it was produced can result in poor reproducibility of test results. Making it difficult to compare test results from different laboratories. Measuring the wear performance of fabrics is critical to the manufacturers, distributors, and retailers in the textile production chain. A well controlled and reproducible wear resistance measurement is crucial to ensure reliable quality control of the fabric.
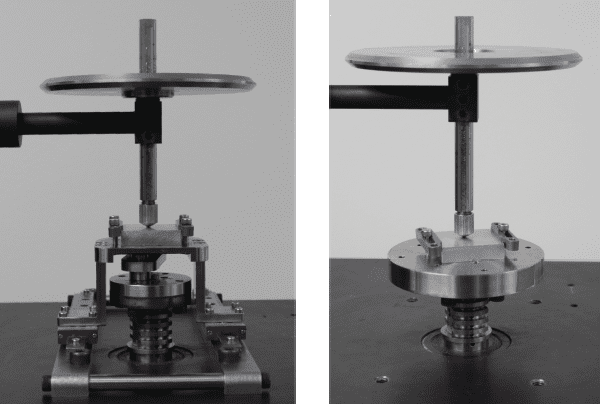
Rotative or Linear Wear & COF? (A Comprehensive Study Using the Nanovea Tribometer)
Wear is the process of removal and deformation of material on a surface as a result of the mechanical action of the opposite surface. It is influenced by a variety of factors, including unidirectional sliding, rolling, speed, temperature, and many others. The study of wear, tribology, spans many disciplines, from physics and chemistry to mechanical engineering and material science. The complex nature of wear requires isolated studies toward specific wear mechanisms or processes, such as adhesive wear, abrasive wear, surface fatigue, fretting wear, and erosive wear. However, “Industrial Wear” commonly involves multiple wear mechanisms occurring in synergy.
Linear reciprocating and Rotative (Pin on Disk) wear tests are two widely used ASTM-compliant setups for measuring sliding wear behaviors of materials. Since the wear rate value of any wear test method is often used to predict the relative ranking of material combinations, it is extremely important to confirm the repeatability of the wear rate measured using different test setups. This enables users to carefully consider the wear rate value reported in the literature, which is critical in understanding the tribological characteristics of materials.
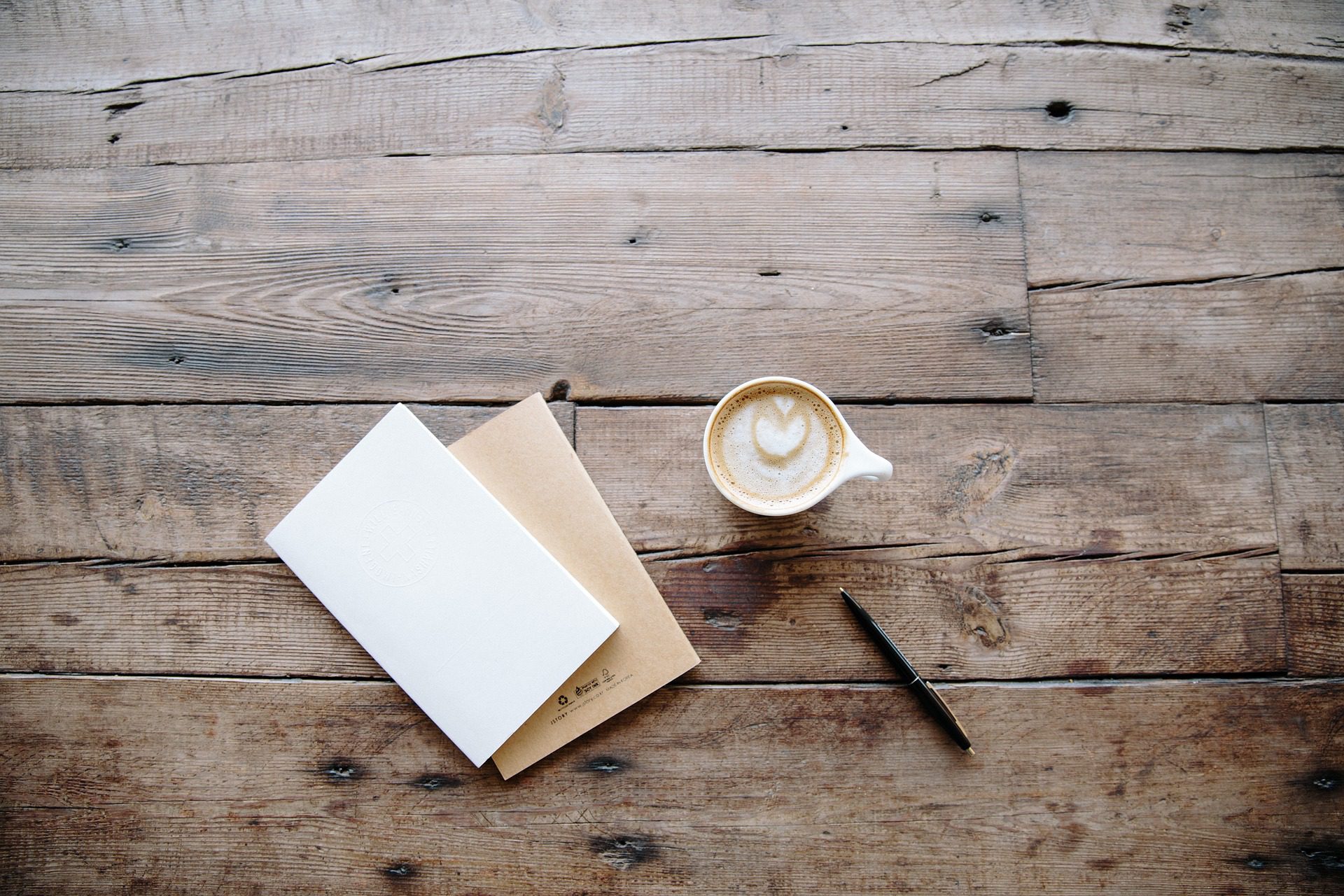
Wood Wear Test with the Nanovea Tribometer
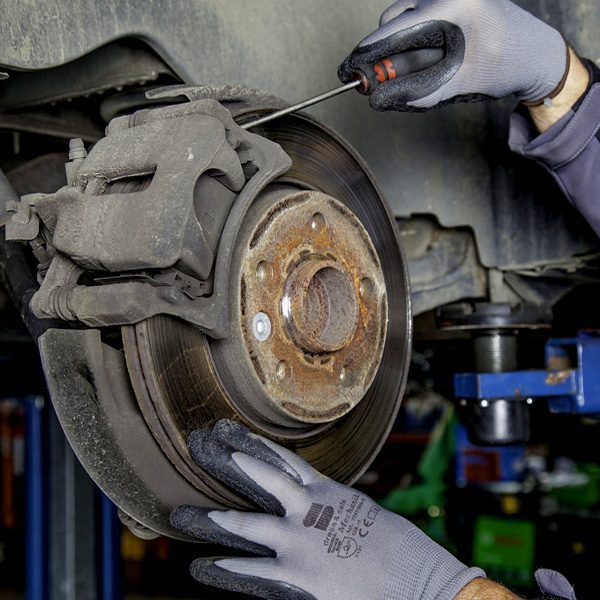
Evaluating Brake Pads with Tribology
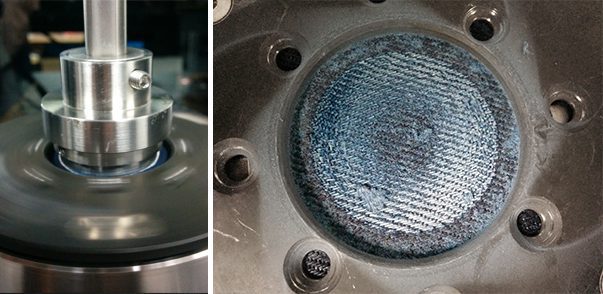
Textile Abrasion Wear By Tribometer
The measurement of textile abrasion resistance of fabrics is very challenging. Many factors play a role during the test, including the mechanical properties of the fibers, the structure of the yarns and the weave of the fabrics. This may result in poor reproducibility of test results and create difficulty in comparing values reported from different laboratories. Wear performance of the fabrics is critical to the manufacturers, distributors, and retailers in the textile production chain. A well-controlled quantifiable and reproducible Tribometer wear resistance measurement is crucial to ensure reliable quality control of the fabric production.
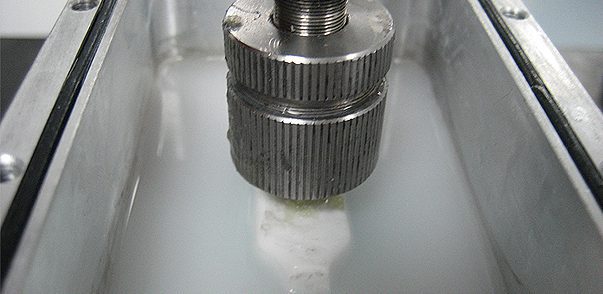
Brush Bristle Stiffness Performance Using Tribometer
Brushes are among the most basic and widely used tools in the world. They can be used to remove material (toothbrush, archaeological brush, bench grinder brush), apply material (paintbrush, makeup brush, gilding brush), comb filaments, or add a pattern. As a result of the mechanical and abrasive forces on them, brushes constantly have to be replaced after moderate use. For example toothbrush heads should be replaced every three to four months because of fraying as a result of repeated usage. Making the toothbrush fiber filaments too stiff risks wearing away the actual tooth instead of soft plaque. Making the toothbrush fibers too soft makes the brush lose its form faster. Understanding the changing bend of the brush, as well as the wear and overall change in shape in the filaments under different loading conditions is necessary to design brushes that better fulfill their application.
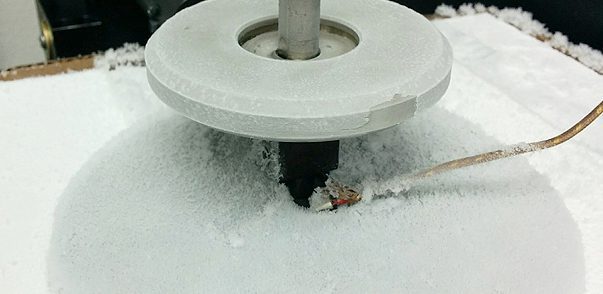
Low Temperature Tribology
A reliable measurement of low temperature tribology, static and dynamic coefficient of friction, COF, as well as wear behavior is needed in order to better understand the tribological performance of materials for sub-zero applications. It provides a useful tool to correlate the frictional property with the influence of various factors, such as reactions at the interface, interlocking surface features, cohesion of surface films, and even microscopic solid static junctions between surfaces at low temperatures.
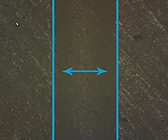
High Temperature Scratch Hardness Using Tribometer
Materials are selected based on the service requirements. For applications involving significant temperature changes and thermal gradients, it is critical to investigate the mechanical properties of materials at high temperatures to be fully aware of the mechanical limits. Materials, especially polymers, usually soften at high temperatures. A lot of mechanical failures are caused by creep deformation and thermal fatigue taking place only at elevated temperatures. Therefore, a reliable technique for measuring high temperature scratch hardness is in need to ensure proper selection of the materials for high temperature applications.
High Temperature Scratch Hardness Using Tribometer
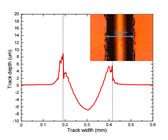
Scratch Hardness Measurement Using Tribometer
In this study, the Nanovea Tribometer is used to measure the scratch hardness of different metals. The
capacity of performing scratch hardness measurement with high precision and reproducibility makes
Nanovea Tribometer a more complete system for tribological and mechanical evaluations.

Mechanical & Tribological Properties of Carbon Fiber
Combined with the wear test by Tribometer and surface analysis by Optical 3D Profilometer, we
showcase the versatility and accuracy of the Nanovea instruments in testing composite materials
with directional mechanical properties.