
SCRATCH TESTER
Scratch Tester Overview
Scratch testing is a vital technique in material science that enables researchers to evaluate the mechanical properties of various materials. A scratch tester, an essential instrument in this process, creates controlled scratches or cuts on the surface of a material, allowing scientists to measure its adhesive, cohesive and wear resistance. As new materials with increasingly complex structures and properties continue to be developed, the importance of scratch testing grows. In this article, we will delve into the definition of scratch tester and explore the significance of scratch testing in material science, as well as discuss the different types of scratch tests, their applications, and how to interpret the results.
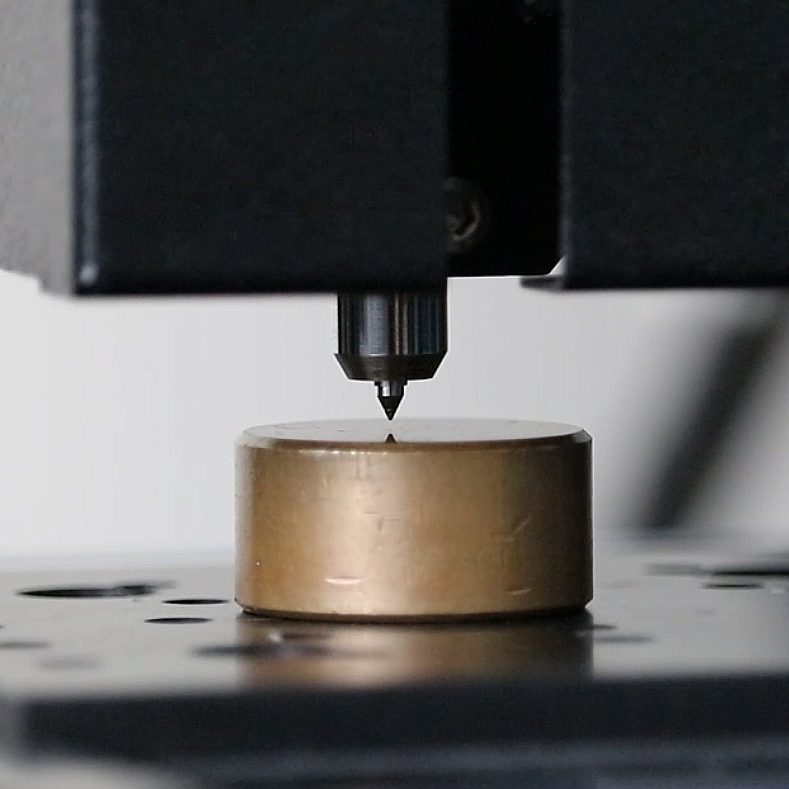
Table of Contents
DISCOVER SCRATCH TESTING
WITH NANOVEA MECHANICAL TESTERS
Key Features of a Nanovea Scratch Tester
A Nanovea nano scratch or micro scratch tester enables precise examination of surface scratches at critical load points using an advanced integrated video microscope system. The data collected during the scratch test, including visible critical locations, friction, depth, and load, can be utilized to determine various scratch properties for diverse film/substrate combinations. By quantifying all aspects of a scratch, researchers can enhance and optimize coating materials for specific applications. Throughout the scratch test, real-time measurements such as friction, normal force, and true depth are recorded. True Depth measurements, based on European Patent No. 0663068, ensure accurate elastic and plastic deformation analysis resulting from a scratch.
Scratch Testing Standards
Nanovea conducts scratch testing in compliance with established standards, ensuring accurate and reliable results for evaluating the mechanical properties of materials, while also offering tailored testing solutions designed for unique applications.
- ASTM D7187 – Standard Test Method for Measuring Mechanistic Aspects of Scratch/Mar Behavior of Paint Coatings by Nanoscratching
- ASTM C1624 – Standard Test Method for Adhesion Strength and Mechanical Failure Modes of Ceramic Coatings by Quantitative Single Point Scratch Testing
- ASTM D7027 – Standard Test Method for Evaluation of Scratch Resistance of Polymeric Coatings and Plastics Using an Instrumented Scratch Machine
- ASTM G171 – Standard Test Method for Scratch Hardness of Materials Using a Diamond Stylus
- ISO 20502 – Fine ceramics (advanced ceramics, advanced technical ceramics) — Determination of adhesion of ceramic coatings by scratch testing
- ISO 1518 – Paints And Varnishes — Determination Of Scratch Resistance
- DIN EN 1071 – Advanced technical ceramics – Methods of test for ceramic coatings
- DVM-0058-PA – Exterior Clearcoat – Scratch Resistance On Rigid Substrates
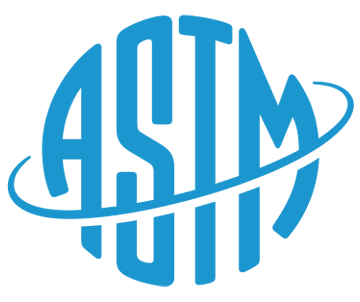
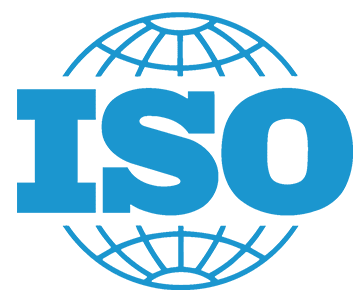
Nanovea Scratch Tester Software Features
- Recipes
- Raw Data and Individual/Full Length Scratch
- Image Exporting
- Real Time Data Display – Depth, Normal Force, Friction, Coefficient of Friction
- Automatic Reporting
- Critical Failure Comparison Tool
- Mapped Scratch Automation
- Full Length Scratch Imaging for post-test inspection using tracking zoomed view (Add Image)
- Tracking Zoomed View for easy post inspection with data depth, friction and AE analysis (add Image)
- Multi-Language Support
Advanced Micro Scratch Automation
- Broadview Map Selection Tool: Advanced Mapping on stitched image
- Automated multi-sample testing (handles height variance of up to 50mm)
- Navigation Plus: User Friendly surface navigation imaging
- Quick Approach, Auto Surface Detection and Auto Analysis
- Direct & Easy Calibration Tools for Load & Depth Measurements
- Single Indent Area Function (European Patent No. 3076153)
- Quantifiable quality check for indenters (European Patent No. 3076153)
- Wizard: Automatic Test Parameter generator (patent pending)
- Savable recipes of all macros programmed
TRACKING ZOOMED VIEW
SAMPLE HOLDERS AND ENVIRONMENTAL CONDITIONS
- High Temperature Testing – up to 450°C
- Cold Temperature testing – down to -40°C
- Humidity Chamber
- Room Temperature & High Temperature Liquid Testing – up to 60°C
- Custom Sample & Indenter Holding Mounts
HIGH TEMP
LOW TEMP
LIQUID
HUMIDITY
VACUUM
Scratch Testing Procedure
Scratch tester works by using a stylus with a defined geometry that moves across the surface while gradually increasing the load. This process measures the depth of the scratch or the force required to initiate the scratch as a function of the applied load. However, factors like stylus shape and size, sliding speed, temperature, and humidity can influence the scratch testing results. To get reliable data on mechanical characteristics, researchers must choose the most appropriate type of scratch resistance test for each material. Different types of scratch tests include single-pass progressive or constant load scratch tests, multi-pass or reciprocating constant load scratch tests, each with unique advantages and limitations. By using scratch testers, scientists can gain insights into the mechanical behavior of materials and develop new materials with improved properties.
Single-pass scratch tests
Single-pass scratch tests are a type of scratch testing where the stylus moves across the material’s surface at a constant or progressive load in one continuous motion. Scratch test for coatings and thin films is essential in determining the adhesion, and scratch resistance of various protective layers applied to materials, ensuring their durability and performance in real-world applications. The advantage of single-pass scratch test lies in its repeatability and simplicity as only one pass is needed to obtain results.
Progressive load scratch tests
Progressive load scratch tests, also known as load ramp tests, involve gradually increasing the load applied to the stylus as it moves across the material’s surface. This method allows researchers to evaluate the critical loads at which different types of damage occur, such as delamination, cracking, or plastic deformation. Paint scratch test for example, involves assessing the durability of a coating by performing a progressive scratch, while sometimes also comparing the coefficient of friction between different coatings to determine their performance and resistance to wear in various applications. The main advantage of progressive load scratch tests is that they provide a comprehensive view of a material’s mechanical properties and failure mechanisms under varying loads. The limitation, however, is that they can be more complex and time-consuming compared to single-pass scratch tests.
Reciprocating or multi-pass scratch tests
Reciprocating scratch tests involve moving the stylus back and forth over the same area on the material’s surface multiple times while multi-pass scratch testing involves moving the stylus always in the same direction. Both methods help to assess the wear resistance and durability of materials under cyclic loading conditions, simulating real-world scenarios where materials are subjected to repeated stresses. The advantage of reciprocating and multi-pass scratch tests is that they can provide more information about the material’s wear behavior.
Each type of scratch test offers unique advantages and limitations, making them suitable for different applications and materials. Researchers must carefully consider the specific requirements of their study and the material being tested to select the most appropriate scratch testing method. By choosing the right type of scratch test, researchers can gain valuable insights into a material’s mechanical behavior, ultimately leading to the development of new materials with tailored properties and improved performance in various applications.
Applications of Scratch Testing
Scratch testers are widely used for evaluating the mechanical properties of various materials, including metals, ceramics, polymers, and coatings. Industries that use scratch testing include automotive, aerospace, electronics, and biomedical, where material durability and performance are critical for success. Scratch testing has several advantages over other methods because it provides quick very reproducible direct measurement of the surface properties of a material. Furthermore, scratch testing enables precise control over scratch parameters, allowing researchers to obtain repeatable and consistent data on a wide range of materials. By using scratch tester, scientists can gain insights into the mechanical behavior of materials and develop new materials with improved properties, making them an essential tool in materials science research.
Interpretation of Scratch Test Results
Interpreting scratch test results is crucial for understanding the mechanical properties of materials, and a scratch tester plays a key role in this process. From the scratch test results, researchers can gain insights into cohesive and adhesive failure, scratch hardness, multi-pass wear, and wear resistance, which are essential factors in evaluating a material’s performance and durability. Cohesive failure refers to the breakdown of the material itself, while adhesive failure occurs when the bond between two materials fails. Scratch hardness is determined by the depth of the scratch created on the material’s surface, and multi-pass wear indicates the material’s resistance to repeated stresses. Techniques for analyzing scratch test data include depth data, acoustic emission, friction measurement, optical microscopy, white light chromatic confocal profilometry, scanning electron microscopy, and atomic force microscopy, which provide valuable information on the deformation behavior of materials and the underlying physics of the scratch testing process. By using scratch testers and analyzing their results, researchers can develop new materials with tailored mechanical properties and improve existing materials for various applications.
Challenges of Scratch Testing
Although scratch testing is a powerful method for measuring the mechanical properties of materials, it does have challenges related to interpreting scratch test results that can be complex, especially when multiple parameters are involved. The complexity of the deformation process and the variability of different testing conditions can also affect the interpretation of results. Despite these challenges, scratch tester remains a valuable tool for evaluating the mechanical properties of various materials. With proper testing techniques and data analysis, researchers can overcome these challenges and gain valuable insights into the mechanical behavior of materials.
Conclusion
Scratch testing is a critical technique in material science research that provides researchers with the ability to directly measure the mechanical properties of materials with excellent repeatability. The insights gained from scratch testing help to develop new materials with improved properties and enhance the performance of current materials used in various industries. The potential for future applications of scratch testing technology is vast, as researchers now have an increased understanding of the deformation behavior of materials. With ongoing advances in microscopes and other technologies, researchers are continuously improving their understanding of the mechanisms responsible for various material behavior. The future of scratch testing looks promising, and it is expected to play a significant role in the development of new materials with customized mechanical properties. If you seek help finding a suitable solution for your application, don’t hesitate to get in touch with us so that we can assist you further.
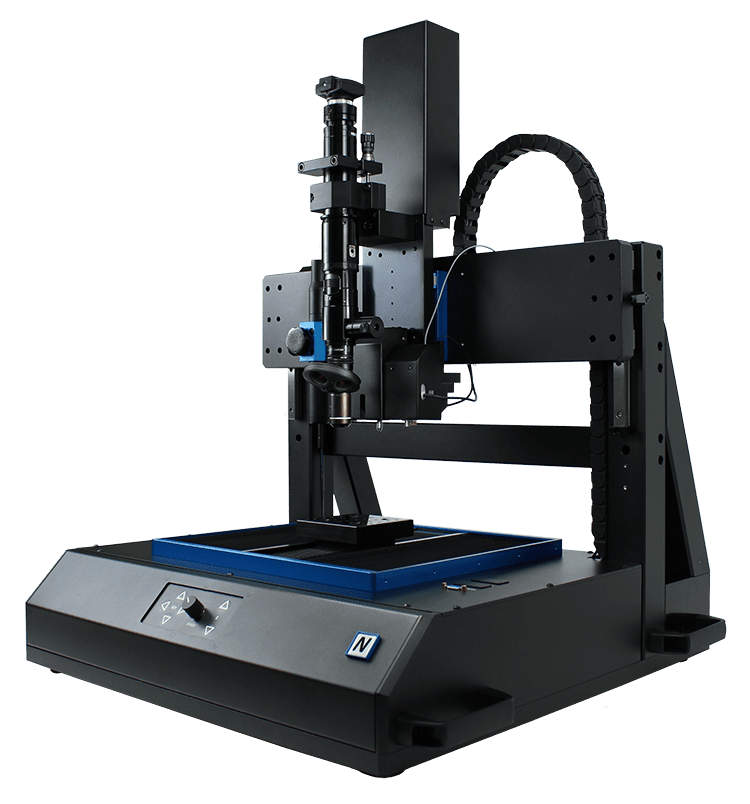