Cohesive & adhesive coating failure

Coating failure can be detrimental to the lifespan and functionality of surfaces in industrial settings, which is why effective methods for evaluating coating durability and performance are fundamental. One such method that is widely used in materials evaluation is scratch testing, which determines the cohesive and adhesive properties of coatings and bulk materials by applying critical loads on surfaces. This technique allows for the identification of potential failure points and provides insights into the behavior of coatings under varying conditions, making it an invaluable tool for optimizing and improving their properties.
In this article, we delve into the measurement principle of scratch testing, exploring its methodology and the types of failures it can detect, as well as the factors influencing critical loads. With this essential knowledge, materials scientists and engineers can better evaluate and improve the reliability of coatings.
Scratch Testing Methodology
The scratch testing method is a crucial technique for investigating cohesive and adhesive coating failure. This widely-used practice involves making controlled scratches using a sphero-conical stylus with a tip radius range of 1 to 200 μm. The scratches are made under either a constant load or progressive load at fixed loading rates, while the stylus moves at a constant speed across the sample. These tests enable the determination of critical loads, which highlight the limits of a coating’s durability. Critical loads for progressive load testing are the minimum loads at which recognizable failure occurs, while for constant load testing, they correspond to the loads at which regular failure is observed. The results of scratch tests contribute significantly to the development of more resilient coatings for various applications, making this analysis a vital part of materials science and engineering.
Cohesive and adhesive costing Failures
Bulk materials can exhibit cohesive failures like cracking or plastic deformation at critical loads, while coated samples may show lower loads with conformal or tensile cracking of the coating. However, as the load regime intensifies, coating detachment from the substrate becomes a possibility, presenting spalling, buckling, or chipping. Figure 1 illustrates the principle of scratch testing. These failures may occur due to a wide range of factors such as inadequate adhesion between the coating and the substrate, mismatch in the coefficients of thermal expansion, uneven stresses, and so on. Understanding the different types of coating failure and their underlying mechanisms is crucial for designing more robust coatings that can withstand harsh environments. This knowledge not only benefits the scientific community but also serves multiple industries that rely on advanced coatings to improve the performance of their products.
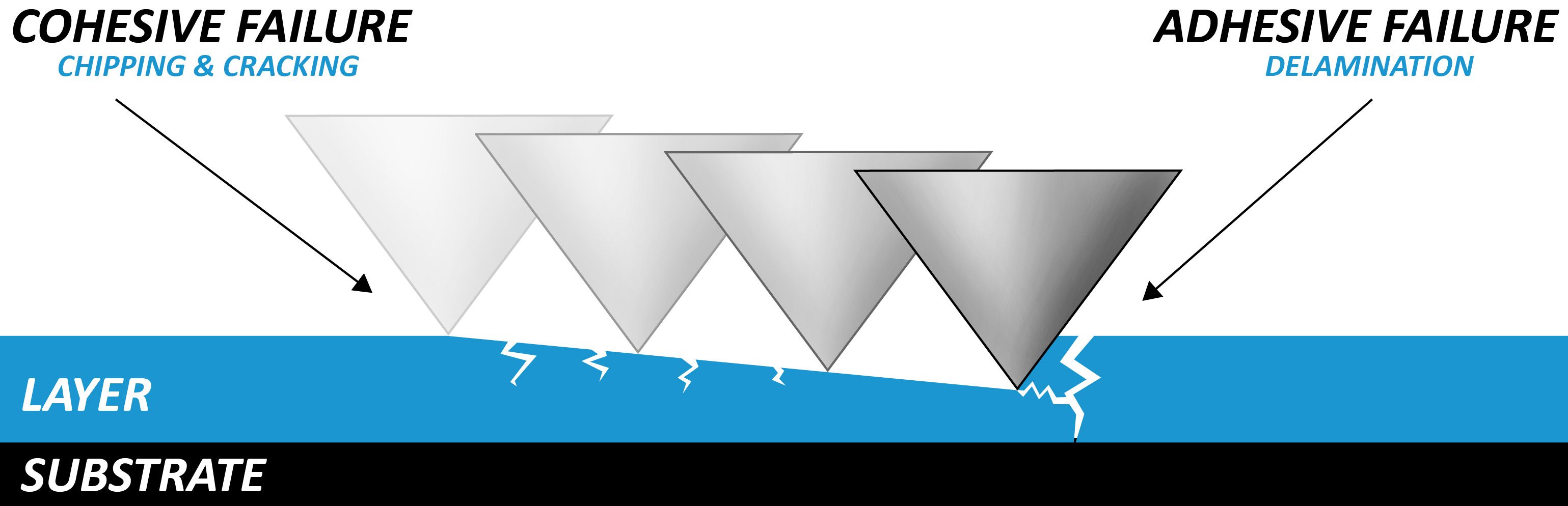

FIGURE 1: Principle of scrath testing
Factors Influencing Critical Loads
The scratch test is a valuable tool for studying the behavior of various coatings and their interaction with their underlying substrates. It generates highly reproducible, quantitative data that can provide insight into the strength and adhesion of the coatings. The critical loads obtained from the scratch test depend not only on the cohesive and adhesive strength of the coating-substrate composite, but also on various other factors. These parameters, which are summarized in Table 1, include factors that are related to the test itself, as well as those that are related to the coating-substrate system. By understanding the complex interplay between these variables, researchers can gain a deeper understanding of how coatings perform under different conditions and work to improve their overall performance. Ultimately, this knowledge can lead to the development of stronger, more effective coatings that are better able to resist failure and extend the lifespan of critical components.
SCRATCH TESTING PARAMETERS
Friction coefficient between surface and indenter | Loading rate |
Internal stresses in the material for bulk materials | Scratching speed |
Material hardness & roughness for coating-substrate systems | Indenter tip radius |
Substrate hardness and roughness | Indenter material |
Coating hardness and roughness | Test specific parameters |
Coating thickness | Sample specific parameters |
Table 1: List of parameters that influence the critical loads.
The strength of scratch testing lies in its ability to provide reproducible and quantitative data, making it a go-to method for detecting quantitatively small changes in both cohesive and adhesive properties. Its ability to compare coatings and evaluate the effects of manufacturing processes or batch variations has enabled researchers to gain a deeper understanding of coating behavior. Perhaps most importantly, scratch testing has contributed to the identification and analysis of coating failure mechanisms. This knowledge has proven to be invaluable in the development of more robust and efficient coating materials and processes.
Means for critical load determination
Microscopic observation
One of the most informative techniques is the use of microscopic observation. This method is able to differentiate between cohesive failure within the coating and adhesive failure at the interface of the coating-substrate system.
Tangential (frictional) force recording
By analyzing the force fluctuations along the scratch, researchers can identify and correlate failures observed under a microscope. In general, a failure in the sample will lead to a noticeable change in the coefficient of friction, such as a step or a change in slope. Frictional responses to failures are very specific to the coating-substrate system in study.
Acoustic emission (AE) detection
This technique involves the detection of elastic waves generated by microcracks forming and propagating within a material, which allows for early detection before they become visible through microscope observation. The sensitivity of this method makes it valuable in predicting the onset of coating failure in a variety of materials. By quantifying the level of energy produced by AE, it is possible to accurately determine the critical load and prevent catastrophic failures.
Depth Sensing
Depth sensing is one effective means of determining the critical load. By analyzing the sudden change in depth data during testing, it is possible to identify delamination. Additionally, residual scratch depth information, along with surface reference correction, can provide insight into the plastic versus elastic deformation of the coating during testing. The use of chromatic 3D non-contact imaging and AFMs also allows for full scratch profile imaging after testing, adding further detail to the analysis. Ultimately, critical load determination through depth sensing is an important tool for preventing coating failure and enhancing product performance.
Conclusion
Cohesive and adhesive coating failure is a crucial aspect that needs to be evaluated in industries that use coatings. This evaluation is made possible through scratch testing, which functions as an essential measurement principle. A deep understanding of this methodology’s types of failures and the critical loads’ influencing factors provides professionals with valuable insights into coating behavior and performance. Thanks to the reproducible and sensitive nature of scratch testing, it has become a crucial tool in materials evaluation. By incorporating scratch testing in quality control measures, industries can improve their coatings and manufacturing processes. The continued advancements and research in scratch testing will contribute to the development of durable and reliable coatings in various industries. Therefore, scratch testing’s significance in mitigating the adverse effects of coating failure cannot be overstated.