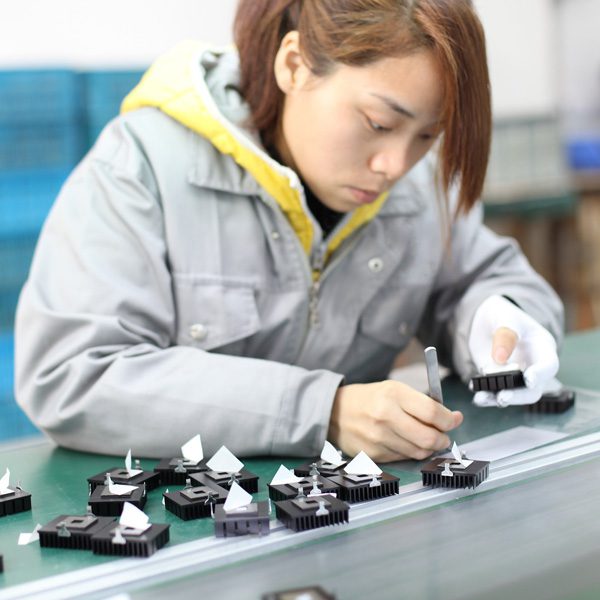
In-line Roughness Inspection
Learn more
IMPORTANCE OF NON-CONTACT PROFILER FOR IN-LINE ROUGHNESS INSPECTION
Surface defects derive from materials processing and product manufacturing. In-line surface quality inspection ensures the tightest quality control of the end products. The Nanovea 3D Non-Contact Profilometers utilize chromatic confocal technology with a unique capability to determine the roughness of a sample with-out contact. Multiple profiler sensors can be installed to monitor the roughness and texture of different areas of the product at the same time. The roughness threshold calculated in real-time by the analysis software serves as a fast and reliable pass/fail tool.
MEASUREMENT OBJECTIVE
In this study, the Nanovea roughness inspection conveyor system equipped with a point sensor is used to inspect the surface roughness of the acrylic and sandpaper samples. We showcase the capacity of Nanovea non-contact profilometer in providing fast and reliable in-line roughness inspection in a production line in real-time.
RESULTS AND DISCUSSION
The conveyor profilometer system can operate in two modes, namely Trigger Mode and Continuous Mode. As illustrated in Figure 2, the surface roughness of the samples are measured when they are passing under the optical profiler heads under the Trigger Mode. In comparison, Continuous Mode provides non-stop measurement of the surface roughness on the continuous sample, such as metal sheet and fabric. Multiple optical profiler sensors can be installed to monitor and record the roughness of different sample areas.
During the real-time roughness inspection measurement, the pass and fail alerts are displayed on the software windows as shown in Figure 4 and Figure 5. When the roughness value is within the given thresholds, the measured roughness is highlighted in green color. However, the highlight turns red when the measured surface roughness is out of the range of the set threshold values. This provides a tool for the user to determine the quality of a product’s surface finish.
In the following sections, two types of samples, e.g. Acrylic and Sandpaper are used to demonstrate the Trigger and Continuous Modes of the Inspection system.
Trigger Mode: Surface inspection of the Acrylic Sample
A series of Acrylic samples are aligned on the conveyor belt and move under the optical profiler head as shown in Figure 1. The false color view in Figure 6 shows the change of the surface height. Some of the mirror-like finished Acrylic samples had been sanded to create a rough surface texture as shown in Figure 6b.
As the Acrylic samples move at a constant speed under the optical profiler head, the surface profile is measured as shown in Figure 7 and Figure 8. The roughness value of the measured profile is calculated at the same time and compared to the threshold values. The red fail alert is launched when the roughness value is over the set threshold, allowing users to immediately detect and locate the defective product on the production line.
Continuous Mode: Surface Inspection of the sandpaper sample
Surface Height Map, Roughness Distribution Map, and Pass / Fail Roughness Threshold Map of the sandpaper sample surface as shown in Figure 9. The sandpaper sample has a couple of higher peaks in the used part as shown in the surface height map. The different colors in the pallet of Figure 9C represent the roughness value of the local surface. The Roughness Map exhibits a homogeneous roughness in the intact area of the sandpaper sample, while the used area is highlighted in dark blue color, indicating the reduced roughness value in this region. A Pass/Fail roughness threshold can be set up to locate such regions as shown in Figure 9D.
As the sandpaper continuously passes under the in-line profiler sensor, the real-time local roughness value is calculated and recorded as plotted in Figure 10. The pass/fail alerts are displayed on the software screen based on the set roughness threshold values, serving as a fast and reliable tool for quality control. The product surface quality in the production line is inspected in situ to discover defective areas in time.
In this application, we have shown the Nanovea Conveyor Profilometer equipped with an optical non-contact profiler sensor works as a reliable in-line quality control tool effectively and efficiently.
The inspection system can be installed in the production line to monitor the surface quality of the products in situ. The roughness threshold works as a dependable criteria to determine the surface quality of the products, allowing users to notice the defective products in time. Two inspection modes, namely Trigger Mode and Continuous Mode, are provided to meet the requirement for inspection on different types of products.
The data shown here represent only a portion of the calculations available in the analysis software. Nanovea Profilometers measure virtually any surface in fields including Semiconductor, Microelectronics, Solar, Fiber, Optics, Automotive, Aerospace, Metallurgy, Machining, Coatings, Pharmaceutical, Biomedical, Environmental and many others.
NOW, LET'S TALK ABOUT YOUR APPLICATION
Categorías
- Application Notes
- Block on Ring Tribology
- Corrosion Tribology
- Friction Testing | Coefficient of Friction
- High Temperature Mechanical Testing
- High Temperature Tribology
- Humidity and Gases Tribology
- Humidity Mechanical Testing
- Indentation | Creep and Relaxation
- Indentation | Fracture Toughness
- Indentation | Hardness and Elastic
- Indentation | Loss and Storage
- Indentation | Stress vs Strain
- Indentation | Yield Strength and Fatigue
- Laboratory Testing
- Linear Tribology
- Liquid Mechanical Testing
- Liquid Tribology
- Low Temperature Tribology
- Mechanical Testing
- Press Release
- Profilometry | Flatness and Warpage
- Profilometry | Geometry and Shape
- Profilometry | Roughness and Finish
- Profilometry | Step Height and Thickness
- Profilometry | Texture and Grain
- Profilometry | Volume and Area
- Profilometry Testing
- Ring on Ring Tribology
- Rotational Tribology
- Scratch Testing | Adhesive Failure
- Scratch Testing | Cohesive Failure
- Scratch Testing | Multi-Pass Wear
- Scratch Testing | Scratch Hardness
- Scratch Testing Tribology
- Tradeshow
- Tribology Testing
- Uncategorized
Archivos
- septiembre 2023
- agosto 2023
- junio 2023
- mayo 2023
- julio 2022
- mayo 2022
- abril 2022
- enero 2022
- diciembre 2021
- noviembre 2021
- octubre 2021
- septiembre 2021
- agosto 2021
- julio 2021
- junio 2021
- mayo 2021
- marzo 2021
- febrero 2021
- diciembre 2020
- noviembre 2020
- octubre 2020
- septiembre 2020
- julio 2020
- mayo 2020
- abril 2020
- marzo 2020
- febrero 2020
- enero 2020
- noviembre 2019
- octubre 2019
- septiembre 2019
- agosto 2019
- julio 2019
- junio 2019
- mayo 2019
- abril 2019
- marzo 2019
- enero 2019
- diciembre 2018
- noviembre 2018
- octubre 2018
- septiembre 2018
- julio 2018
- junio 2018
- mayo 2018
- abril 2018
- marzo 2018
- febrero 2018
- noviembre 2017
- octubre 2017
- septiembre 2017
- agosto 2017
- junio 2017
- mayo 2017
- abril 2017
- marzo 2017
- febrero 2017
- enero 2017
- noviembre 2016
- octubre 2016
- agosto 2016
- julio 2016
- junio 2016
- mayo 2016
- abril 2016
- marzo 2016
- febrero 2016
- enero 2016
- diciembre 2015
- noviembre 2015
- octubre 2015
- septiembre 2015
- agosto 2015
- julio 2015
- junio 2015
- mayo 2015
- abril 2015
- marzo 2015
- febrero 2015
- enero 2015
- noviembre 2014
- octubre 2014
- septiembre 2014
- agosto 2014
- julio 2014
- junio 2014
- mayo 2014
- abril 2014
- marzo 2014
- febrero 2014
- enero 2014
- diciembre 2013
- noviembre 2013
- octubre 2013
- septiembre 2013
- agosto 2013
- julio 2013
- junio 2013
- mayo 2013
- abril 2013
- marzo 2013
- febrero 2013
- enero 2013
- diciembre 2012
- noviembre 2012
- octubre 2012
- septiembre 2012
- agosto 2012
- julio 2012
- junio 2012
- mayo 2012
- abril 2012
- marzo 2012
- febrero 2012
- enero 2012
- diciembre 2011
- noviembre 2011
- octubre 2011
- septiembre 2011
- agosto 2011
- julio 2011
- junio 2011
- mayo 2011
- noviembre 2010
- enero 2010
- abril 2009
- marzo 2009
- enero 2009
- diciembre 2008
- octubre 2008
- agosto 2007
- julio 2006
- marzo 2006
- enero 2005
- abril 2004