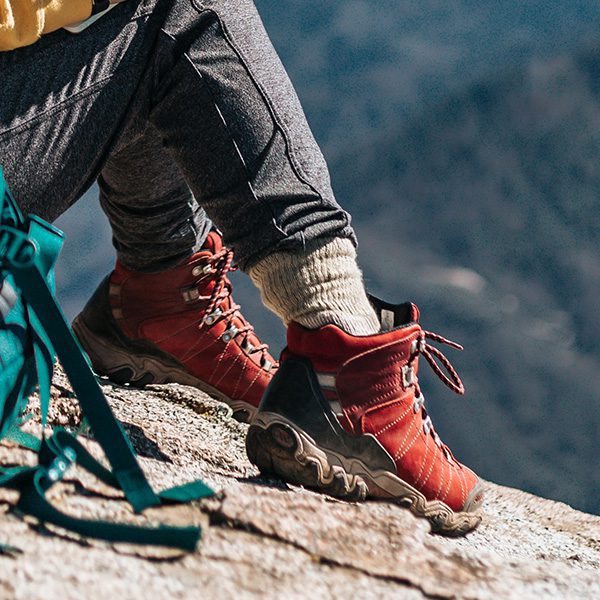
Friction Evaluation at Extreme Low Speeds
Importance of Friction Evaluation at Low Speeds
Friction is the force that resists the relative motion of solid surfaces sliding against each other. When the relative motion of these two contact surfaces takes place, the friction at the interface converts the kinetic energy into heat. Such a process can also lead to wear of the material and thus performance degradation of the parts in use.
With a large stretch ratio, high resilience, as well as great waterproof properties and wear resistance, rubber is extensively applied in a variety of applications and products in which friction plays an important role, such as automobile tires, windshield wiper blades. shoe soles and many others. Depending on the nature and requirement of these applications, either high or low friction against different material is desired. As a consequence, a controlled and reliable measurement of friction of rubber against various surfaces becomes critical.
Objetivo de medición
The coefficient of friction (COF) of rubber against different materials is measured in a controlled and monitored manner using the Nanovea Tribómetro. In this study, we would like to showcase the capacity of Nanovea Tribometer for measuring the COF of different materials at extremely low speeds.
Resultados y debate
The coefficient of friction (COF) of rubber balls (6 mm dia., RubberMill) on three materials (Stainless steel SS 316, Cu 110 and optional Acrylic) was evaluated by Nanovea Tribometer. The tested metal samples were mechanically polished to a mirror-like surface finish before the measurement. The slight deformation of the rubber ball under the applied normal load created an area contact, which also helps to reduce the impact of asperities or inhomogeneity of sample surface finish to the COF measurements. The test parameters are summarized in Table 1.
The COF of a rubber ball against different materials at four different speeds is shown in Figure. 2, and the average COFs calculated automatically by the software are summarized and compared in Figure 3. It is interesting that the metal samples (SS 316 and Cu 110) exhibit significantly increased COFs as the rotational speed increases from a very low value of 0.01 rpm to 5 rpm -the COF value of the rubber/SS 316 couple increases from 0.29 to 0.8, and from 0.65 to 1.1 for the rubber/Cu 110 couple. This finding is in agreement with the results reported from several laboratories. As proposed by Grosch4 the friction of rubber is mainly determined by two mechanisms: (1) the adhesion between rubber and the other material, and (2) the energy losses due to the deformation of the rubber caused by surface asperities. Schallamach5 observed waves of detachment of rubber from the counter material across the interface between soft rubber spheres and a hard surface. The force for rubber to peel from the substrate surface and rate of waves of detachment can explain the different friction at different speeds during the test.
In comparison, the rubber/acrylic material couple exhibits high COF at different rotational speeds. The COF value slightly increases from ~ 1.02 to ~ 1.09 as the rotational speed increases from 0.01 rpm to 5 rpm. Such high COF is possibly attributed to stronger local chemical bonding at the contact face formed during the tests.
Conclusión
In this study, we show that at extremely low speeds, the rubber exhibits a peculiar frictional behavior – its friction against a hard surface increases with the increased speed of the relative movement. Rubber shows different friction when it slides on different materials. Nanovea Tribometer can evaluate the frictional properties of materials in a controlled and monitored manner at different speeds, allowing users to improve fundamental understanding of the friction mechanism of the materials and select the best material couple for targeted tribological engineering applications.
Nanovea Tribometer offers precise and repeatable wear and friction testing using ISO and ASTM compliant rotative and linear modes, with optional high-temperature wear, lubrication and tribo-corrosion modules available in one pre-integrated system. It is capable of controlling the rotational stage at extremely low speeds down to 0.01 rpm and monitor the evolution of friction in situ. Nanovea’s unmatched range is an ideal solution for determining the full range of tribological properties of thin or thick, soft or hard coatings, films, and substrates.
AHORA, HABLEMOS DE SU SOLICITUD
Categorías
- Notas de aplicación
- Bloque sobre tribología anular
- Tribología de la corrosión
- Pruebas de fricción | Coeficiente de fricción
- Pruebas mecánicas a alta temperatura
- Tribología de alta temperatura
- Humedad y gases Tribología
- Humedad Pruebas mecánicas
- Indentación | Fluencia y relajación
- Indentación | Resistencia a la fractura
- Indentación | Dureza y elasticidad
- Indentación | Pérdida y almacenamiento
- Indentación | Esfuerzo frente a deformación
- Indentación | Límite elástico y fatiga
- Pruebas de laboratorio
- Tribología lineal
- Pruebas mecánicas de líquidos
- Tribología de líquidos
- Tribología a baja temperatura
- Pruebas mecánicas
- Comunicado de prensa
- Perfilometría | Planitud y alabeo
- Perfilometría | Geometría y forma
- Perfilometría | Rugosidad y acabado
- Profilometría | Altura y grosor del escalón
- Profilometría | Textura y grano
- Perfilometría | Volumen y área
- Pruebas de perfilometría
- Tribología anillo sobre anillo
- Tribología rotacional
- Prueba de arañazos | Fallo adhesivo
- Prueba del rasguño | Fallo de cohesión
- Pruebas de arañazos | Desgaste en varias pasadas
- Pruebas de rayado | Dureza al rayado
- Pruebas de rayado Tribología
- Feria de muestras
- Pruebas de tribología
- Sin categoría
Archivos
- septiembre 2023
- agosto 2023
- junio 2023
- mayo 2023
- julio 2022
- mayo 2022
- abril 2022
- enero 2022
- diciembre 2021
- noviembre 2021
- octubre 2021
- septiembre 2021
- agosto 2021
- julio 2021
- junio 2021
- mayo 2021
- marzo 2021
- febrero 2021
- diciembre 2020
- noviembre 2020
- octubre 2020
- septiembre 2020
- julio 2020
- mayo 2020
- abril 2020
- marzo 2020
- febrero 2020
- enero 2020
- noviembre 2019
- octubre 2019
- septiembre 2019
- agosto 2019
- julio 2019
- junio 2019
- mayo 2019
- abril 2019
- marzo 2019
- enero 2019
- diciembre 2018
- noviembre 2018
- octubre 2018
- septiembre 2018
- julio 2018
- junio 2018
- mayo 2018
- abril 2018
- marzo 2018
- febrero 2018
- noviembre 2017
- octubre 2017
- septiembre 2017
- agosto 2017
- junio 2017
- mayo 2017
- abril 2017
- marzo 2017
- febrero 2017
- enero 2017
- noviembre 2016
- octubre 2016
- agosto 2016
- julio 2016
- junio 2016
- mayo 2016
- abril 2016
- marzo 2016
- febrero 2016
- enero 2016
- diciembre 2015
- noviembre 2015
- octubre 2015
- septiembre 2015
- agosto 2015
- julio 2015
- junio 2015
- mayo 2015
- abril 2015
- marzo 2015
- febrero 2015
- enero 2015
- noviembre 2014
- octubre 2014
- septiembre 2014
- agosto 2014
- julio 2014
- junio 2014
- mayo 2014
- abril 2014
- marzo 2014
- febrero 2014
- enero 2014
- diciembre 2013
- noviembre 2013
- octubre 2013
- septiembre 2013
- agosto 2013
- julio 2013
- junio 2013
- mayo 2013
- abril 2013
- marzo 2013
- febrero 2013
- enero 2013
- diciembre 2012
- noviembre 2012
- octubre 2012
- septiembre 2012
- agosto 2012
- julio 2012
- junio 2012
- mayo 2012
- abril 2012
- marzo 2012
- febrero 2012
- enero 2012
- diciembre 2011
- noviembre 2011
- octubre 2011
- septiembre 2011
- agosto 2011
- julio 2011
- junio 2011
- mayo 2011
- noviembre 2010
- enero 2010
- abril 2009
- marzo 2009
- enero 2009
- diciembre 2008
- octubre 2008
- agosto 2007
- julio 2006
- marzo 2006
- enero 2005
- abril 2004