Kategorie: Lineare Tribologie
Verschleißtest der PTFE-Beschichtung
Polymerriemenverschleiß und Reibung mit einem Tribometer
Kolbenverschleißprüfung
Bewertung des Reibungsverschleißes
Kugellager: Studie zur Verschleißfestigkeit bei hoher Krafteinwirkung
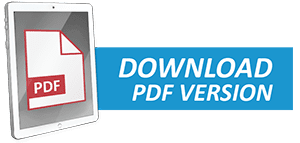
EINFÜHRUNG
Ein Kugellager verwendet Kugeln, um die Rotationsreibung zu reduzieren und radiale und axiale Belastungen zu unterstützen. Die rollenden Kugeln zwischen den Lagerringen erzeugen einen viel niedrigeren Reibungskoeffizienten (COF) im Vergleich zu zwei gegeneinander gleitenden flachen Oberflächen. Kugellager sind häufig hohen Kontaktspannungen, Verschleiß und extremen Umweltbedingungen wie hohen Temperaturen ausgesetzt. Daher ist die Verschleißfestigkeit der Kugeln unter hohen Belastungen und extremen Umgebungsbedingungen von entscheidender Bedeutung für die Verlängerung der Lebensdauer des Kugellagers, um Kosten und Zeit für Reparaturen und Austausch zu reduzieren.
Kugellager sind in fast allen Anwendungen zu finden, in denen bewegliche Teile beteiligt sind. Sie werden häufig in der Transportindustrie wie der Luft- und Raumfahrt und im Automobilbereich sowie in der Spielzeugindustrie eingesetzt, die Artikel wie Fidget Spinner und Skateboards herstellt.
BEWERTUNG DES KUGELLAGERVERSCHLEISSES BEI HOHEN BELASTUNGEN
Kugellager können aus einer umfangreichen Liste von Materialien hergestellt werden. Zu den häufig verwendeten Materialien gehören Metalle wie Edelstahl und Chromstahl oder Keramiken wie Wolframkarbid (WC) und Siliziumnitrid (Si3n4). Um sicherzustellen, dass die hergestellten Kugellager die erforderliche Verschleißfestigkeit aufweisen, die für die jeweiligen Einsatzbedingungen ideal ist, sind zuverlässige tribologische Untersuchungen unter hohen Belastungen erforderlich. Tribologische Tests helfen dabei, das Verschleißverhalten verschiedener Kugellager auf kontrollierte und überwachte Weise zu quantifizieren und gegenüberzustellen, um den besten Kandidaten für die Zielanwendung auszuwählen.
MESSZIEL
In dieser Studie stellen wir einen Nanovea vor Tribometer als ideales Hilfsmittel zum Vergleich der Verschleißfestigkeit verschiedener Kugellager unter hoher Belastung.

Abbildung 1: Aufbau des Lagertests.
PRÜFVERFAHREN
Der Reibungskoeffizient COF und die Verschleißfestigkeit der Kugellager aus verschiedenen Materialien wurden mit einem Nanovea-Tribometer bewertet. Als Gegenmaterial wurde Schleifpapier der Körnung P100 verwendet. Die Verschleißspuren der Kugellager wurden mittels a untersucht Nanovea 3D Non-Contact Profiler nach Abschluss der Verschleißtests. Die Testparameter sind in Tabelle 1 zusammengefasst. Die Verschleißrate, Kwurde anhand der folgenden Formel bewertet K=V/(F×s), wobei V ist das abgenutzte Volumen, F ist die Normalbelastung und s ist die Gleitstrecke. Ballabnutzungsnarben wurden bewertet von a Nanovea 3D-Berührungsloser Profiler zur Gewährleistung einer präzisen Messung des Verschleißvolumens.
Die automatisierte motorisierte radiale Positionierungsfunktion ermöglicht es dem Tribometer, den Radius der Verschleißspur während der Dauer eines Tests zu verringern. Dieser Testmodus wird Spiraltest genannt und stellt sicher, dass das Kugellager immer auf einer neuen Oberfläche des Schleifpapiers gleitet (Abbildung 2). Es verbessert die Wiederholbarkeit der Verschleißfestigkeitsprüfung der Kugel erheblich. Der fortschrittliche 20-Bit-Encoder für die interne Geschwindigkeitssteuerung und der 16-Bit-Encoder für die externe Positionssteuerung liefern präzise Echtzeit-Geschwindigkeits- und Positionsinformationen und ermöglichen eine kontinuierliche Anpassung der Drehzahl, um eine konstante lineare Gleitgeschwindigkeit am Kontakt zu erreichen.
Bitte beachten Sie, dass in dieser Studie Schleifpapier der Körnung P100 verwendet wurde, um das Verschleißverhalten zwischen verschiedenen Kugelmaterialien zu vereinfachen, und dass es durch jede andere Materialoberfläche ersetzt werden kann. Jedes feste Material kann ersetzt werden, um die Leistung einer Vielzahl von Materialkupplungen unter tatsächlichen Anwendungsbedingungen, beispielsweise in Flüssigkeiten oder Schmiermitteln, zu simulieren.
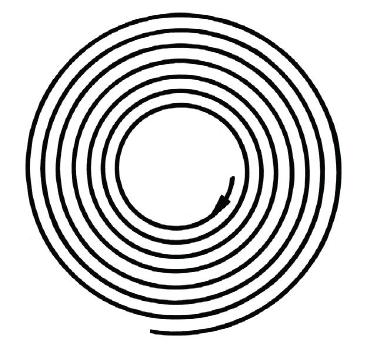
Abbildung 2: Darstellung der Spiraldurchgänge für das Kugellager auf dem Schleifpapier.
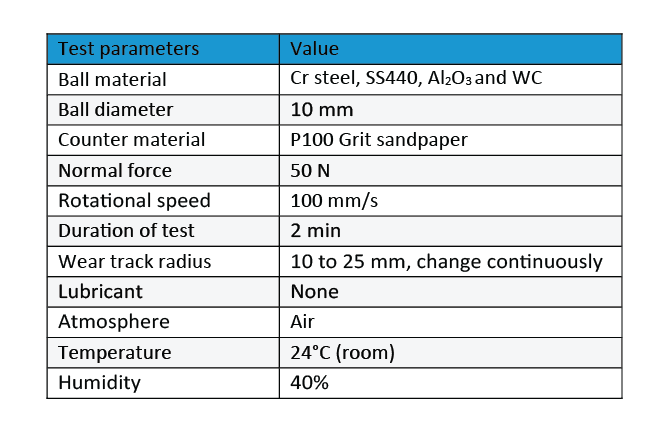
Tabelle 1: Prüfparameter der Verschleißmessungen.
ERGEBNISSE & DISKUSSION
Die Verschleißrate ist ein entscheidender Faktor für die Lebensdauer des Kugellagers, während ein niedriger COF wünschenswert ist, um die Leistung und Effizienz des Lagers zu verbessern. Abbildung 3 vergleicht die Entwicklung des COF für verschiedene Kugellager im Vergleich zum Sandpapier während der Tests. Die Cr-Stahlkugel weist während des Verschleißtests einen erhöhten COF von ~0,4 auf, verglichen mit ~0,32 und ~0,28 für SS440- und Al2O3-Kugellager. Andererseits weist die WC-Kugel während des gesamten Verschleißtests einen konstanten COF von ~0,2 auf. Während jedes Tests sind beobachtbare COF-Schwankungen zu beobachten, die auf Vibrationen zurückzuführen sind, die durch die Gleitbewegung der Kugellager auf der rauen Sandpapieroberfläche verursacht werden.

Abbildung 3: Entwicklung des COF während der Verschleißtests.
Abbildung 4 und Abbildung 5 vergleichen die Verschleißspuren der Kugellager, nachdem sie mit einem optischen Mikroskop bzw. einem berührungslosen optischen Profilmessgerät von Nanovea gemessen wurden, und Tabelle 2 fasst die Ergebnisse der Verschleißspuranalyse zusammen. Der Nanovea 3D-Profiler ermittelt präzise das Verschleißvolumen der Kugellager und ermöglicht so die Berechnung und den Vergleich der Verschleißraten verschiedener Kugellager. Es ist zu beobachten, dass die Cr-Stahl- und SS440-Kugeln nach den Verschleißtests im Vergleich zu den Keramikkugeln, also Al2O3 und WC, viel größere abgeflachte Verschleißnarben aufweisen. Die Kugeln aus Cr-Stahl und SS440 weisen vergleichbare Verschleißraten von 3,7×10-3 bzw. 3,2×10-3 m3/N·m auf. Im Vergleich dazu zeigt die Al2O3-Kugel eine erhöhte Verschleißfestigkeit mit einer Verschleißrate von 7,2×10-4 m3/N·m. Die WC-Kugel weist im flachen Verschleißbahnbereich kaum kleinere Kratzer auf, was zu einer deutlich reduzierten Verschleißrate von 3,3×10-6 mm3/N·m führt.

Abbildung 4: Verschleißnarben der Kugellager nach den Tests.
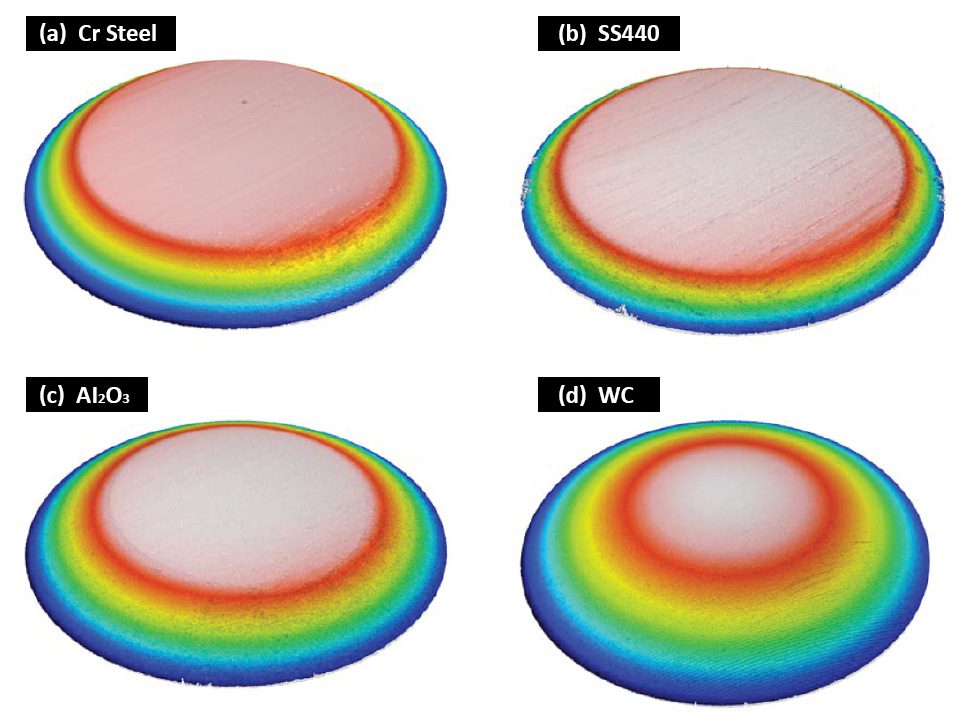
Abbildung 5: 3D-Morphologie der Verschleißnarben an den Kugellagern.
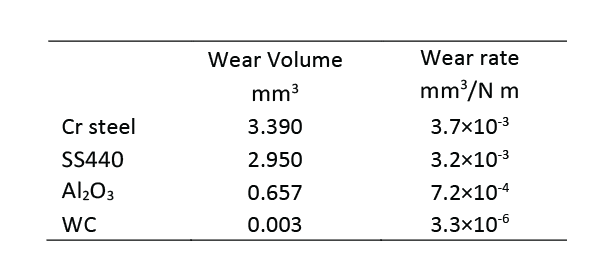
Tabelle 2: Verschleißnarbenanalyse der Kugellager.
Abbildung 6 zeigt Mikroskopbilder der Verschleißspuren, die durch die vier Kugellager auf dem Schleifpapier entstehen. Es ist offensichtlich, dass die WC-Kugel die stärkste Verschleißspur erzeugte (fast alle Sandpartikel auf ihrem Weg entfernte) und die beste Verschleißfestigkeit besitzt. Im Vergleich dazu hinterließen die Kugeln aus Cr-Stahl und SS440 eine große Menge Metallabrieb auf der Verschleißspur des Schleifpapiers.
Diese Beobachtungen verdeutlichen erneut die Bedeutung des Nutzens eines Spiraltests. Es stellt sicher, dass das Kugellager immer auf einer neuen Oberfläche des Schleifpapiers gleitet, was die Wiederholbarkeit einer Verschleißfestigkeitsprüfung deutlich verbessert.

Abbildung 6: Verschleißspuren auf dem Schleifpapier an verschiedenen Kugellagern.

SCHLUSSFOLGERUNG
Die Verschleißfestigkeit der Kugellager unter hohem Druck spielt eine entscheidende Rolle für ihre Betriebsleistung. Die Keramikkugellager verfügen über eine deutlich verbesserte Verschleißfestigkeit unter hohen Belastungsbedingungen und reduzieren den Zeit- und Kostenaufwand für die Reparatur oder den Austausch von Lagern. In dieser Studie weist das WC-Kugellager im Vergleich zu Stahllagern eine wesentlich höhere Verschleißfestigkeit auf, was es zu einem idealen Kandidaten für Lageranwendungen macht, bei denen starker Verschleiß auftritt.
Ein Nanovea-Tribometer ist mit einem hohen Drehmoment für Lasten bis zu 2000 N und einem präzisen und kontrollierten Motor für Drehzahlen von 0,01 bis 15.000 U/min ausgestattet. Es bietet wiederholbare Verschleiß- und Reibungstests mit ISO- und ASTM-konformen Rotations- und Linearmodi, wobei optionale Hochtemperatur-Verschleiß- und Schmiermodule in einem vorintegrierten System verfügbar sind. Dieser unübertroffene Bereich ermöglicht es Benutzern, verschiedene schwere Arbeitsumgebungen der Kugellager zu simulieren, einschließlich hoher Beanspruchung, Verschleiß und hoher Temperatur usw. Es fungiert auch als ideales Werkzeug zur quantitativen Bewertung des tribologischen Verhaltens hochwertiger verschleißfester Materialien unter hohen Belastungen.
Ein berührungsloser 3D-Profiler von Nanovea liefert präzise Verschleißvolumenmessungen und fungiert als Werkzeug zur Analyse der detaillierten Morphologie der Verschleißspuren, was zusätzliche Einblicke in das grundlegende Verständnis der Verschleißmechanismen liefert.
Vorbereitet von
Duanjie Li, PhD, Jonathan Thomas und Pierre Leroux
Bewertung der Abnutzung und des Kratzens von oberflächenbehandeltem Kupferdraht
Einfluss von Luftfeuchtigkeit auf die Tribologie von DLC-Beschichtungen
Vergleich der Abriebfestigkeit von Denim
Einführung
Die Form und Funktion eines Stoffes wird durch seine Qualität und Haltbarkeit bestimmt. Durch den täglichen Gebrauch von Stoffen kommt es zu Abnutzungserscheinungen, wie z. B. Knötchenbildung, Ausfransen und Verfärbung des Materials. Eine minderwertige Stoffqualität bei Kleidung führt oft zu Unzufriedenheit beim Verbraucher und schadet der Marke.
Der Versuch, die mechanischen Eigenschaften von Geweben zu quantifizieren, kann viele Herausforderungen mit sich bringen. Die Garnstruktur und sogar die Fabrik, in der es hergestellt wurde, können zu einer schlechten Reproduzierbarkeit der Testergebnisse führen. Dies erschwert den Vergleich von Testergebnissen aus verschiedenen Labors. Die Messung des Verschleißverhaltens von Stoffen ist für die Hersteller, Verteiler und Einzelhändler in der Textilproduktionskette von entscheidender Bedeutung. Eine gut kontrollierte und reproduzierbare Messung der Verschleißfestigkeit ist entscheidend für eine zuverlässige Qualitätskontrolle des Gewebes.
Klicken Sie hier, um den vollständigen Anwendungshinweis zu lesen!
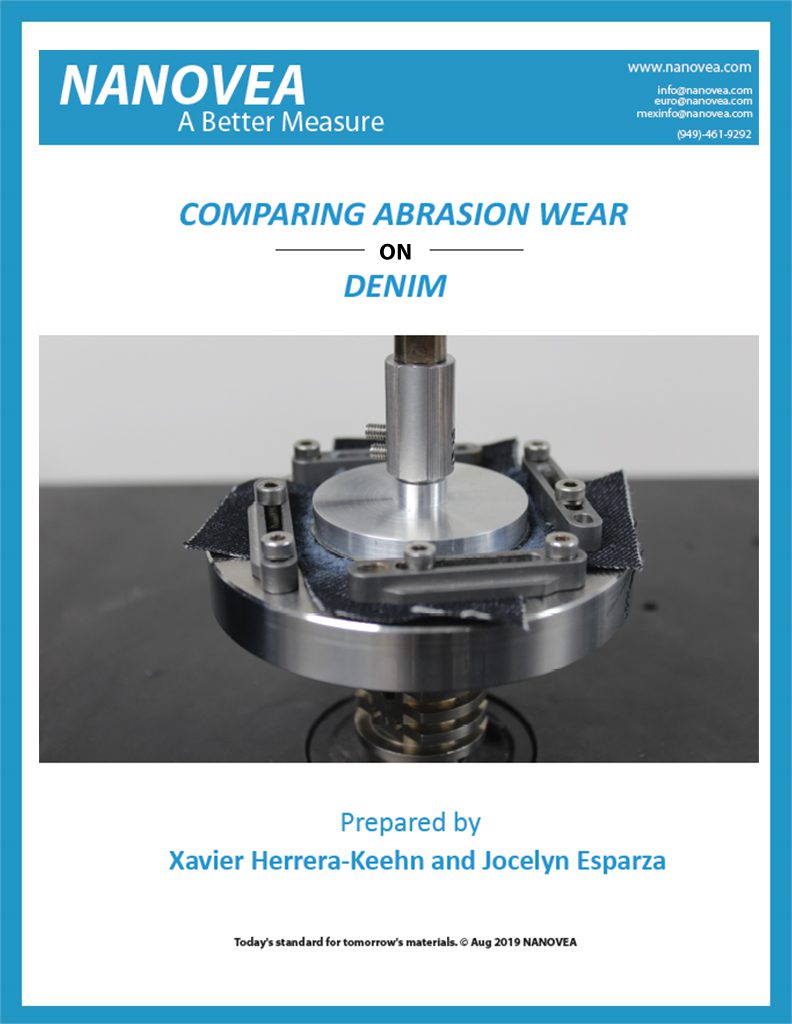
Rotativer oder linearer Verschleiß & COF? (Eine umfassende Studie unter Verwendung des Nanovea Tribometers)
Unter Verschleiß versteht man den Prozess der Abtragung und Verformung von Material auf einer Oberfläche infolge der mechanischen Einwirkung der gegenüberliegenden Oberfläche. Es wird durch eine Vielzahl von Faktoren beeinflusst, darunter unidirektionales Gleiten, Rollen, Geschwindigkeit, Temperatur und viele andere. Das Studium des Verschleißes, der Tribologie, umfasst viele Disziplinen, von Physik und Chemie bis hin zu Maschinenbau und Materialwissenschaften. Die komplexe Natur des Verschleißes erfordert isolierte Studien zu spezifischen Verschleißmechanismen oder -prozessen, wie z. B. adhäsiver Verschleiß, abrasiver Verschleiß, Oberflächenermüdung, Reibverschleiß und erosiver Verschleiß. Bei „industrieller Abnutzung“ handelt es sich jedoch häufig um mehrere Verschleißmechanismen, die synergetisch wirken.
Lineare hin- und hergehende und rotative Verschleißtests (Stift auf Scheibe) sind zwei weit verbreitete ASTM-konforme Aufbauten zur Messung des Gleitverschleißverhaltens von Materialien. Da der Verschleißratenwert einer Verschleißtestmethode häufig zur Vorhersage der relativen Rangfolge von Materialkombinationen verwendet wird, ist es äußerst wichtig, die Wiederholbarkeit der mit verschiedenen Testaufbauten gemessenen Verschleißrate zu bestätigen. Dadurch können Benutzer den in der Literatur angegebenen Verschleißratenwert sorgfältig berücksichtigen, was für das Verständnis der tribologischen Eigenschaften von Materialien von entscheidender Bedeutung ist.
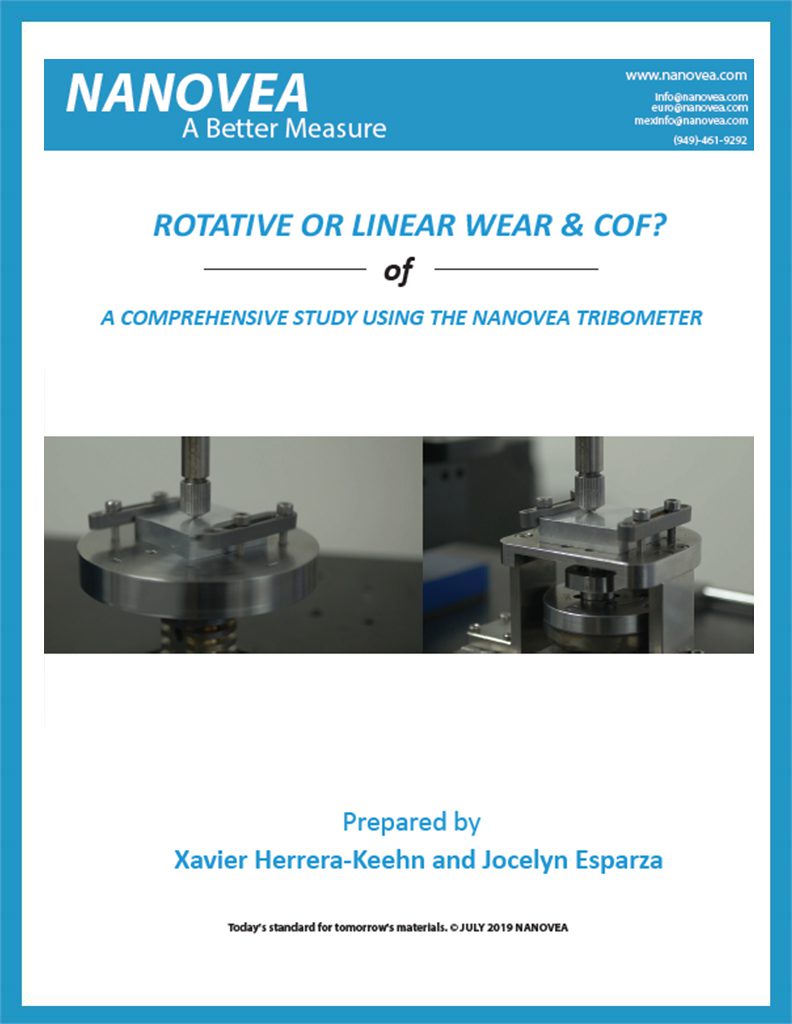
Mehr lesen!
Bewertung von Bremsbelägen mit Tribologie