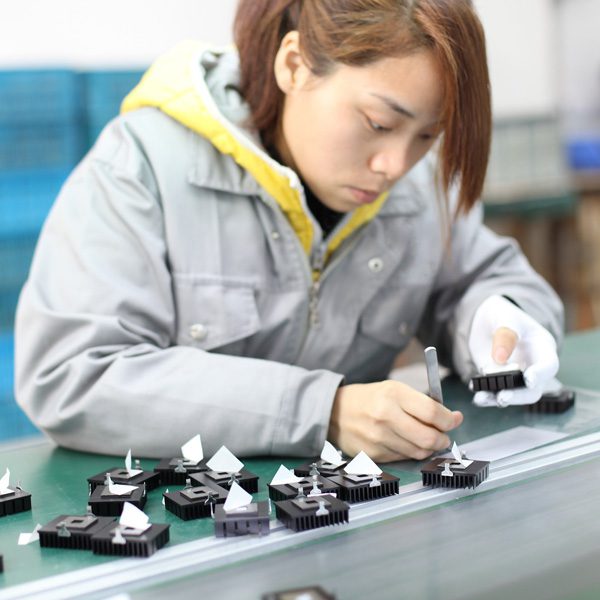
Contrôle de la rugosité en ligne
En savoir plus
IMPORTANCE DU PROFILEUR SANS CONTACT POUR LE CONTRÔLE DE LA RUGOSITÉ EN LIGNE
Les défauts de surface proviennent du traitement des matériaux et de la fabrication des produits. L'inspection de la qualité des surfaces en ligne garantit le contrôle qualité le plus strict des produits finaux. La Nanovéa Profilomètres 3D sans contact utilise la technologie confocale chromatique avec une capacité unique pour déterminer la rugosité d'un échantillon sans contact. Plusieurs capteurs profileurs peuvent être installés pour surveiller simultanément la rugosité et la texture de différentes zones du produit. Le seuil de rugosité calculé en temps réel par le logiciel d’analyse constitue un outil réussite/échec rapide et fiable.
OBJECTIF DE MESURE
Dans cette étude, le système de convoyeur d'inspection de la rugosité Nanovea équipé d'un capteur ponctuel est utilisé pour inspecter la rugosité de surface des échantillons d'acrylique et de papier de verre. Nous démontrons la capacité du profilomètre sans contact Nanovea à fournir une inspection rapide et fiable de la rugosité en ligne sur une ligne de production en temps réel.
RÉSULTATS ET DISCUSSION
Le système de profilomètre à convoyeur peut fonctionner en deux modes, à savoir le mode déclenchement et le mode continu. Comme l'illustre la figure 2, la rugosité de surface des échantillons est mesurée lorsqu'ils passent sous les têtes de profilage optiques en mode Trigger. En comparaison, le mode continu permet de mesurer en continu la rugosité de la surface d'un échantillon continu, tel qu'une feuille de métal ou un tissu. Plusieurs capteurs de profileurs optiques peuvent être installés pour surveiller et enregistrer la rugosité de différentes zones de l'échantillon.
Pendant la mesure d'inspection de la rugosité en temps réel, les alertes de réussite et d'échec s'affichent sur les fenêtres du logiciel, comme le montrent la Figure 4 et la Figure 5. Lorsque la valeur de la rugosité se situe dans les limites des seuils fixés, la rugosité mesurée est mise en évidence en vert. Cependant, la surbrillance devient rouge lorsque la rugosité de surface mesurée est en dehors de la plage des valeurs seuils définies. L'utilisateur dispose ainsi d'un outil lui permettant de déterminer la qualité de la finition de surface d'un produit.
Dans les sections suivantes, deux types d'échantillons, par exemple de l'acrylique et du papier de verre, sont utilisés pour démontrer les modes de déclenchement et continu du système d'inspection.
Mode de déclenchement : Inspection de la surface de l'échantillon d'acrylique
Une série d'échantillons d'acrylique sont alignés sur la bande transporteuse et se déplacent sous la tête du profileur optique, comme le montre la figure 1. La vue en fausses couleurs de la figure 6 montre le changement de la hauteur de la surface. Certains des échantillons d'acrylique finis en miroir ont été poncés pour créer une texture de surface rugueuse, comme le montre la figure 6b.
Lorsque les échantillons d'acrylique se déplacent à une vitesse constante sous la tête du profileur optique, le profil de la surface est mesuré, comme le montrent les Figure 7 et Figure 8. La valeur de rugosité du profil mesuré est calculée en même temps et comparée aux valeurs seuils. L'alerte rouge est déclenchée lorsque la valeur de rugosité est supérieure au seuil fixé, ce qui permet aux utilisateurs de détecter et de localiser immédiatement le produit défectueux sur la ligne de production.
Mode continu : Inspection de la surface de l'échantillon de papier de verre
Carte de hauteur de surface, carte de distribution de la rugosité et carte de seuil de rugosité Pass / Fail de la surface de l'échantillon de papier de verre, comme le montre la figure 9. L'échantillon de papier de verre présente quelques pics plus élevés dans la partie utilisée, comme le montre la carte de hauteur de surface. Les différentes couleurs de la palette de la figure 9C représentent la valeur de rugosité de la surface locale. La carte de rugosité montre une rugosité homogène dans la zone intacte de l'échantillon de papier de verre, tandis que la zone utilisée est surlignée en bleu foncé, indiquant la valeur de rugosité réduite dans cette région. Un seuil de rugosité Pass/Fail peut être défini pour localiser ces régions, comme le montre la figure 9D.
Lorsque le papier de verre passe en continu sous le capteur du profileur en ligne, la valeur de la rugosité locale en temps réel est calculée et enregistrée, comme le montre la figure 10. Les alertes de réussite/échec sont affichées sur l'écran du logiciel en fonction des valeurs seuils de rugosité définies, ce qui constitue un outil rapide et fiable pour le contrôle de la qualité. La qualité de la surface du produit dans la ligne de production est inspectée in situ pour découvrir à temps les zones défectueuses.
Dans cette application, nous avons montré que le profilomètre de convoyeur Nanovea équipé d'un capteur de profilage optique sans contact fonctionne comme un outil fiable de contrôle de la qualité en ligne de manière efficace et efficiente.
Le système d'inspection peut être installé sur la ligne de production pour contrôler la qualité de surface des produits sur place. Le seuil de rugosité est un critère fiable pour déterminer la qualité de la surface des produits, ce qui permet aux utilisateurs de détecter à temps les produits défectueux. Deux modes d'inspection, à savoir le mode de déclenchement et le mode continu, sont prévus pour répondre aux besoins d'inspection de différents types de produits.
Les données présentées ici ne représentent qu'une partie des calculs disponibles dans le logiciel d'analyse. Les profilomètres Nanovea mesurent pratiquement n'importe quelle surface dans des domaines tels que les semi-conducteurs, la microélectronique, le solaire, les fibres, l'optique, l'automobile, l'aérospatiale, la métallurgie, l'usinage, les revêtements, la pharmacie, le biomédical, l'environnement et bien d'autres.
MAINTENANT, PARLONS DE VOTRE CANDIDATURE
Catégories
- Notes d'application
- Bloc sur la tribologie des anneaux
- Corrosion Tribologie
- Essai de friction - Coefficient de friction
- Essais mécaniques à haute température
- Tribologie à haute température
- Humidité et gaz Tribologie
- Humidité Essais mécaniques
- Indentation | Fluage et relaxation
- Indentation | Ténacité à la rupture
- Indentation | Dureté et élasticité
- Indentation | Perte et stockage
- Indentation | Contrainte et déformation
- Indentation | Limite d'élasticité et fatigue
- Tests de laboratoire
- Tribologie linéaire
- Essais mécaniques des liquides
- Tribologie des liquides
- Tribologie à basse température
- Essais mécaniques
- Communiqué de presse
- Profilométrie - Planéité et gauchissement
- Profilométrie | Géométrie et forme
- Profilométrie | Rugosité et finition
- Profilométrie | Hauteur et épaisseur des marches
- Profilométrie | Texture et grain
- Profilométrie | Volume et surface
- Essais de profilométrie
- Tribologie "anneau sur anneau
- Tribologie rotationnelle
- Test de rayures | Défaillance de l'adhésif
- Essai de grattage | Défaillance de la cohésion
- Test de rayures | Usure multi-passages
- Test de rayures | Dureté à la rayure
- Test de rayure Tribologie
- Tradeshow
- Essais de tribologie
- Non classé
Archives
- septembre 2023
- août 2023
- juin 2023
- mai 2023
- juillet 2022
- mai 2022
- avril 2022
- janvier 2022
- décembre 2021
- novembre 2021
- octobre 2021
- septembre 2021
- août 2021
- juillet 2021
- juin 2021
- mai 2021
- mars 2021
- février 2021
- décembre 2020
- novembre 2020
- octobre 2020
- septembre 2020
- juillet 2020
- mai 2020
- avril 2020
- mars 2020
- février 2020
- janvier 2020
- novembre 2019
- octobre 2019
- septembre 2019
- août 2019
- juillet 2019
- juin 2019
- mai 2019
- avril 2019
- mars 2019
- janvier 2019
- décembre 2018
- novembre 2018
- octobre 2018
- septembre 2018
- juillet 2018
- juin 2018
- mai 2018
- avril 2018
- mars 2018
- février 2018
- novembre 2017
- octobre 2017
- septembre 2017
- août 2017
- juin 2017
- mai 2017
- avril 2017
- mars 2017
- février 2017
- janvier 2017
- novembre 2016
- octobre 2016
- août 2016
- juillet 2016
- juin 2016
- mai 2016
- avril 2016
- mars 2016
- février 2016
- janvier 2016
- décembre 2015
- novembre 2015
- octobre 2015
- septembre 2015
- août 2015
- juillet 2015
- juin 2015
- mai 2015
- avril 2015
- mars 2015
- février 2015
- janvier 2015
- novembre 2014
- octobre 2014
- septembre 2014
- août 2014
- juillet 2014
- juin 2014
- mai 2014
- avril 2014
- mars 2014
- février 2014
- janvier 2014
- décembre 2013
- novembre 2013
- octobre 2013
- septembre 2013
- août 2013
- juillet 2013
- juin 2013
- mai 2013
- avril 2013
- mars 2013
- février 2013
- janvier 2013
- décembre 2012
- novembre 2012
- octobre 2012
- septembre 2012
- août 2012
- juillet 2012
- juin 2012
- mai 2012
- avril 2012
- mars 2012
- février 2012
- janvier 2012
- décembre 2011
- novembre 2011
- octobre 2011
- septembre 2011
- août 2011
- juillet 2011
- juin 2011
- mai 2011
- novembre 2010
- janvier 2010
- avril 2009
- mars 2009
- janvier 2009
- décembre 2008
- octobre 2008
- août 2007
- juillet 2006
- mars 2006
- janvier 2005
- avril 2004