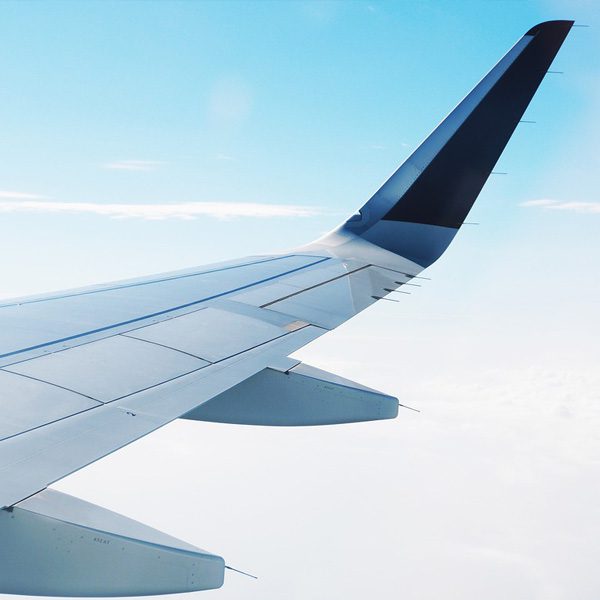
Finition de surface des panneaux en nid d'abeille avec la profilométrie 3D
INTRODUCTION
La rugosité, la porosité et la texture de la surface du panneau en nid d'abeille sont essentielles à quantifier pour la conception finale du panneau. Ces qualités de surface sont en corrélation directe avec les caractéristiques esthétiques et fonctionnelles de la surface du panneau. Une meilleure compréhension de la texture et de la porosité de la surface peut aider à optimiser le traitement et la fabrication de la surface du panneau. Une mesure quantitative, précise et fiable de la surface du panneau en nid d'abeille est nécessaire pour contrôler les paramètres de surface en fonction des exigences d'application et de peinture. Les capteurs Nanovea 3D sans contact utilisent une technologie confocale chromatique unique capable de mesurer précisément la surface de ces panneaux.
OBJECTIF DE MESURE
Dans cette étude, la plateforme Nanovea HS2000 équipée d'un capteur de ligne à grande vitesse a été utilisée pour mesurer et comparer deux panneaux en nid d'abeille avec des finitions de surface différentes. Nous présentons le Nanovea profilomètre sans contactLa capacité de fournit des mesures de profilage 3D rapides et précises et une analyse complète et approfondie de l'état de surface.
RÉSULTATS ET DISCUSSION
La surface de deux échantillons de panneaux en nid d'abeille avec des finitions de surface variées, à savoir l'échantillon 1 et l'échantillon 2, a été mesurée. La fausse couleur et la vue 3D des surfaces des échantillons 1 et 2 sont présentées respectivement sur la Figure 3 et la Figure 4. Les valeurs de rugosité et de planéité ont été calculées par un logiciel d'analyse avancé et sont comparées dans le tableau 1. L'échantillon 2 présente une surface plus poreuse que l'échantillon 1. Par conséquent, l'échantillon 2 possède une rugosité Sa plus élevée de 14,7 µm, par rapport à une valeur Sa de 4,27 µm pour l'échantillon 1.
Les profils 2D des surfaces des panneaux en nid d'abeille ont été comparés dans la Figure 5, permettant aux utilisateurs d'avoir une comparaison visuelle de la variation de hauteur à différents endroits de la surface de l'échantillon. Nous pouvons observer que l'échantillon 1 présente une variation de hauteur de ~25 µm entre le pic le plus élevé et la vallée la plus basse. D'autre part, l'échantillon 2 présente plusieurs pores profonds sur le profil 2D. Le logiciel d'analyse avancée a la capacité de localiser et de mesurer automatiquement la profondeur de six pores relativement profonds, comme le montre le tableau de la figure 4.b de l'échantillon 2. Le pore le plus profond parmi les six possède une profondeur maximale de près de 90 µm (étape 4).
Pour approfondir la taille et la distribution des pores de l'échantillon 2, une évaluation de la porosité a été réalisée et discutée dans la section suivante. La vue en coupe est présentée sur la Figure 5 et les résultats sont résumés dans le Tableau 2. Nous pouvons observer que les pores, marqués en bleu sur la Figure 5, ont une distribution relativement homogène sur la surface de l'échantillon. La surface projetée des pores constitue 18.9% de la surface totale de l'échantillon. Le volume par mm² de l'ensemble des pores est de ~0.06 mm³. Les pores ont une profondeur moyenne de 42,2 µm, et la profondeur maximale est de 108,1 µm.
CONCLUSION
Dans cette application, nous avons montré que la plateforme Nanovea HS2000 équipée d'un capteur linéaire à haute vitesse est un outil idéal pour analyser et comparer la finition de surface des échantillons de panneaux en nid d'abeille de manière rapide et précise. Les scans de profilométrie haute résolution associés à un logiciel d'analyse avancé permettent une évaluation complète et quantitative de la finition de surface des échantillons de panneaux en nid d'abeille.
Les données présentées ici ne représentent qu'une petite partie des calculs disponibles dans le logiciel d'analyse. Les profilomètres Nanovea mesurent pratiquement n'importe quelle surface pour une large gamme d'applications dans les industries des semi-conducteurs, de la microélectronique, du solaire, des fibres optiques, de l'automobile, de l'aérospatiale, de la métallurgie, de l'usinage, des revêtements, de la pharmacie, du biomédical, de l'environnement et bien d'autres.
MAINTENANT, PARLONS DE VOTRE CANDIDATURE
Catégories
- Notes d'application
- Bloc sur la tribologie des anneaux
- Corrosion Tribologie
- Essai de friction - Coefficient de friction
- Essais mécaniques à haute température
- Tribologie à haute température
- Humidité et gaz Tribologie
- Humidité Essais mécaniques
- Indentation | Fluage et relaxation
- Indentation | Ténacité à la rupture
- Indentation | Dureté et élasticité
- Indentation | Perte et stockage
- Indentation | Contrainte et déformation
- Indentation | Limite d'élasticité et fatigue
- Tests de laboratoire
- Tribologie linéaire
- Essais mécaniques des liquides
- Tribologie des liquides
- Tribologie à basse température
- Essais mécaniques
- Communiqué de presse
- Profilométrie - Planéité et gauchissement
- Profilométrie | Géométrie et forme
- Profilométrie | Rugosité et finition
- Profilométrie | Hauteur et épaisseur des marches
- Profilométrie | Texture et grain
- Profilométrie | Volume et surface
- Essais de profilométrie
- Tribologie "anneau sur anneau
- Tribologie rotationnelle
- Test de rayures | Défaillance de l'adhésif
- Essai de grattage | Défaillance de la cohésion
- Test de rayures | Usure multi-passages
- Test de rayures | Dureté à la rayure
- Test de rayure Tribologie
- Tradeshow
- Essais de tribologie
- Non classé
Archives
- septembre 2023
- août 2023
- juin 2023
- mai 2023
- juillet 2022
- mai 2022
- avril 2022
- janvier 2022
- décembre 2021
- novembre 2021
- octobre 2021
- septembre 2021
- août 2021
- juillet 2021
- juin 2021
- mai 2021
- mars 2021
- février 2021
- décembre 2020
- novembre 2020
- octobre 2020
- septembre 2020
- juillet 2020
- mai 2020
- avril 2020
- mars 2020
- février 2020
- janvier 2020
- novembre 2019
- octobre 2019
- septembre 2019
- août 2019
- juillet 2019
- juin 2019
- mai 2019
- avril 2019
- mars 2019
- janvier 2019
- décembre 2018
- novembre 2018
- octobre 2018
- septembre 2018
- juillet 2018
- juin 2018
- mai 2018
- avril 2018
- mars 2018
- février 2018
- novembre 2017
- octobre 2017
- septembre 2017
- août 2017
- juin 2017
- mai 2017
- avril 2017
- mars 2017
- février 2017
- janvier 2017
- novembre 2016
- octobre 2016
- août 2016
- juillet 2016
- juin 2016
- mai 2016
- avril 2016
- mars 2016
- février 2016
- janvier 2016
- décembre 2015
- novembre 2015
- octobre 2015
- septembre 2015
- août 2015
- juillet 2015
- juin 2015
- mai 2015
- avril 2015
- mars 2015
- février 2015
- janvier 2015
- novembre 2014
- octobre 2014
- septembre 2014
- août 2014
- juillet 2014
- juin 2014
- mai 2014
- avril 2014
- mars 2014
- février 2014
- janvier 2014
- décembre 2013
- novembre 2013
- octobre 2013
- septembre 2013
- août 2013
- juillet 2013
- juin 2013
- mai 2013
- avril 2013
- mars 2013
- février 2013
- janvier 2013
- décembre 2012
- novembre 2012
- octobre 2012
- septembre 2012
- août 2012
- juillet 2012
- juin 2012
- mai 2012
- avril 2012
- mars 2012
- février 2012
- janvier 2012
- décembre 2011
- novembre 2011
- octobre 2011
- septembre 2011
- août 2011
- juillet 2011
- juin 2011
- mai 2011
- novembre 2010
- janvier 2010
- avril 2009
- mars 2009
- janvier 2009
- décembre 2008
- octobre 2008
- août 2007
- juillet 2006
- mars 2006
- janvier 2005
- avril 2004