カテゴリー機械試験
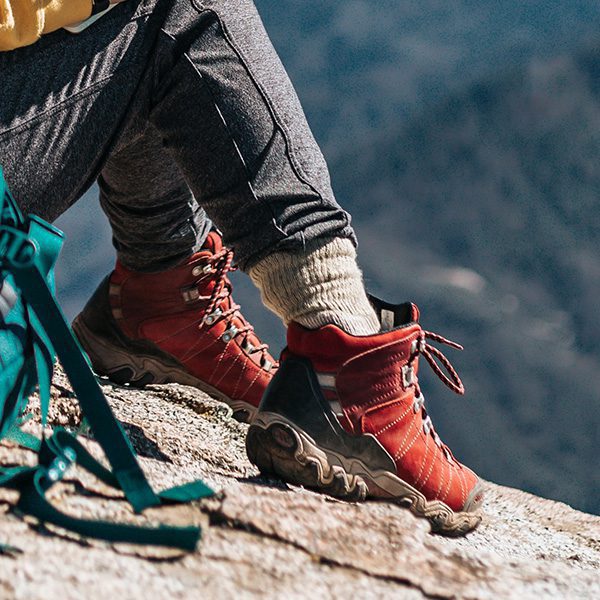
極低速域での摩擦評価
低速域での摩擦評価の重要性
摩擦とは、固体表面同士を滑らせて相対運動に抵抗させる力のことである。この2つの接触面の相対運動が起こると、界面での摩擦により運動エネルギーが熱に変換される。また、このようなプロセスは、材料の摩耗、ひいては使用中の部品の性能劣化につながる可能性がある。
ゴムは伸び率が大きく、弾力性に富み、防水性や耐摩耗性にも優れているため、自動車のタイヤやワイパーブレード、靴底など、摩擦が重要な役割を果たすさまざまな用途や製品に幅広く使用されている。これらの用途の性質や要求に応じて、異なる材料に対して高い摩擦と低い摩擦のどちらかが望まれる。そのため、さまざまな表面に対するゴムの摩擦を制御し、信頼性の高い方法で測定することが重要になります。
測定目的
さまざまな材料に対するゴムの摩擦係数 (COF) は、Nanovea を使用して制御および監視された方法で測定されます。 トライボメータ。この研究では、極低速でさまざまな材料の COF を測定する Nanovea トライボメーターの能力を紹介したいと思います。
結果および考察
3種類の材料(Stainless steel SS 316, Cu 110, optional Acrylic)に対するゴム球(φ6mm, RubberMill)の摩擦係数(COF)をNanovea Tribometerで評価した.試験した金属サンプルは、測定前に機械的に研磨し、鏡面仕上げとした。法線荷重を加えた際のゴム球のわずかな変形によって面積接触が生じ、COF測定に対する試料表面のアスペリティや不均一性の影響を軽減することもできます。試験パラメータを表 1 に示す。
4種類の速度で異なる素材に対してゴム球を衝突させたときのCOFを図2に示す。2 に、ソフトウェアによって自動的に計算された平均 COF をまとめ、図 3 で比較した。興味深いことに、金属試料(SS 316 と Cu 110)は、回転速度が 0.01 rpm という非常に低い値から 5 rpm まで上昇すると、COF が著しく増加することがわかります。この結果は、いくつかの研究室から報告されている結果と一致している。Groschが提案したように4 ゴムの摩擦は、主に(1)ゴムと他の材料の接着、(2)表面の凹凸によるゴムの変形によるエネルギー損失の2つのメカニズムで決定される。シャラマッハ5 軟質ゴム球と硬質表面との界面において,ゴムが相手材から剥離する波が観察された。ゴムが基材表面から剥離する力と剥離の波の速度から、試験中の異なる速度での摩擦の違いを説明することができる。
これに対し、ゴムとアクリルのカップルは、異なる回転数で高いCOFを示しました。回転速度が0.01 rpmから5 rpmまで上昇すると、COF値は1.02から1.09までわずかに上昇した。このような高いCOFは、おそらく試験中に形成された接触面の局所的な化学結合が強くなったことに起因しています。
結論
本研究では、ゴムが極低速で、硬い表面に対する摩擦が相対運動の速度が上がるにつれて大きくなるという特異な摩擦挙動を示すことを示した。ゴムは、異なる材料の上を滑るとき、異なる摩擦を示します。ナノベーストライボメータは、異なる速度で制御・監視された方法で材料の摩擦特性を評価することができ、ユーザーは材料の摩擦メカニズムの基本的な理解を深め、目標とするトライボロジー工学アプリケーションに最適な材料カップルを選択することが可能です。
ナノベーストライボメータは、ISOおよびASTMに準拠した回転モードとリニアモードによる精密で再現性の高い摩耗・摩擦試験と、オプションで高温摩耗、潤滑、トライボコロージョンを1つの統合されたシステムで利用することが可能です。0.01 rpmまでの極めて低い速度で回転ステージを制御し、摩擦の変化をその場でモニターすることが可能です。ナノベアの比類なき製品群は、薄いまたは厚い、柔らかいまたは硬いコーティング、フィルム、および基材のトライボロジー特性をフルレンジで測定するための理想的なソリューションとなります。
さて、次はアプリケーションについてです。
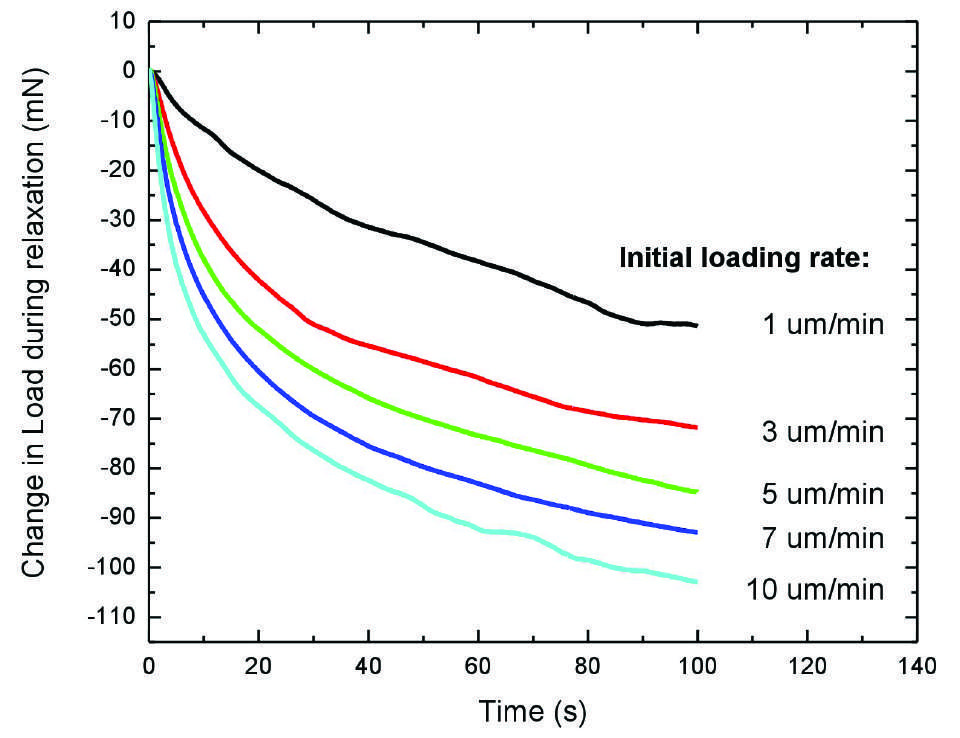
ナノインデンテーションによる応力緩和測定
はじめに
粘弾性材料は、粘性と弾性の両方の材料特性を持つことが特徴である。これらの材料は、一定のひずみで時間依存的に応力が減少(応力「緩和」)し、初期の接触力が大きく損なわれることになる。応力緩和は、材料の種類、組織、温度、初期応力、時間などに依存する。応力緩和を理解することは、特定の用途に必要な強度と柔軟性(緩和)を持つ最適な材料を選択する上で非常に重要である。
ストレス・リラクゼーション測定の重要性
ASTM E328i「材料および構造物の応力緩和の標準試験方法」に従い、材料や構造物に対して、最初に圧子を用いて所定の最大力に達するまで外力を加えておく。最大力に達した後、圧子の位置はその深さで一定に保たれます。そして、圧子の位置を維持するために必要な外力の変化を、時間の関数として測定する。応力緩和試験で難しいのは、深さを一定に保つことです。ナノベアメカニカルテスターの ナノインデンテーション モジュールは、圧電アクチュエーターによる深さの閉ループ(フィードバック)制御を適用することで、応力緩和を正確に測定します。アクチュエーターは深さを一定に保つためにリアルタイムで反応し、荷重の変化は高感度の荷重センサーによって測定・記録されます。この試験は、ほぼすべての種類の材料で実施することができ、厳しい試料寸法の要件は必要ありません。さらに、1つの平らな試料で複数の試験を行うことができ、試験の再現性を確保することができます。
測定目的
このアプリケーションでは、Nanovea Mechanical Tester のナノインデンテーション モジュールが、アクリルと銅のサンプルの応力緩和挙動を測定します。 Nanovea を紹介します。 メカニカルテスター は、ポリマーおよび金属材料の時間依存性の粘弾性挙動を評価するための理想的なツールです。
試験条件
Nanovea Mechanical Testerのナノインデンテーション・モジュールにより、アクリルと銅のサンプルの応力緩和を測定しました。1~10 μm/minの範囲でさまざまな圧痕の負荷速度が適用されました。目標の最大荷重に達すると、一定の深さで緩和が測定されました。一定の深さで100秒間の保持時間を設け、保持時間の経過に伴う荷重の変化を記録しました。試験はすべて周囲条件(室温23℃)で実施し、圧痕試験のパラメータは表1にまとめた。
結果および考察
図2 は、例としてアクリルサンプルと圧痕負荷速度3 µm/minの応力緩和測定中の変位と荷重の時間的変化を示しています。この試験の全体は、3つのステージに分けることができます。ローディング、リラクゼーション、アンローディングです。荷重ステージでは、荷重が徐々に増加するにつれて深さが直線的に増加しました。最大荷重に達すると、弛緩段階が開始されました。このステージでは、装置の閉ループ深度制御機能を使用して100秒間一定の深度を維持し、時間とともに荷重が減少することが観察されました。試験全体は、圧子をアクリル試料から取り外すための除荷ステージで終了しました。
さらに、同じ圧子負荷速度を用いて、緩和(クリープ)期間を除いた圧子試験を実施した。これらの試験から荷重-変位プロットを取得し、アクリルおよび銅の各試料について図3のグラフにまとめました。圧子負荷速度が10μm/minから1μm/minに減少するにつれて、荷重-変位曲線はアクリルと銅の両方でより高い浸透深度に向かって徐々にシフトしていきました。このような時間依存的なひずみの増加は、材料の粘弾性クリープ効果によるものである。低い負荷速度では、粘弾性材料が外部応力に反応し、それに応じて変形するまでの時間が長くなる。
図 4 に、試験した両材料について、異なる押込み荷重速度を用いた一定ひずみでの荷重の推移をプロットし た。荷重は、試験の緩和段階(100秒保持)の初期に高い割合で減少し、保持時間が〜50秒に達すると減速した。ポリマーや金属などの粘弾性材料は、より高い押込み荷重率を受けると、より大きな荷重損失率を示す。緩和時の荷重損失率は、圧子負荷速度が1~10μm/minに増加すると、アクリルでは51.5~103.2mN、銅では15.0~27.4mNに増加したことが、以下に要約されるようになります。 図5.
ASTM規格E328iiに記載されているように、応力緩和試験で遭遇する主な問題は、ひずみ/深さを一定に保つことができない装置であることです。ナノベアメカニカルテスターは、高速で作動する圧電アクチュエーターと独立したコンデンサーの深さセンサーの間で深さの閉ループ制御を行うことができるため、優れた精度の応力緩和測定が可能になっています。緩和の段階では、圧電アクチュエーターが圧子を調節して一定の深さの制約をリアルタイムで維持し、同時に独立した高精度荷重センサーによって荷重の変化が測定・記録されます。
まとめ
ナノベアメカニカルテスターのナノインデンテーション・モジュールを用いて、アクリルと銅のサンプルの応力緩和を、異なる荷重率で測定しました。低い荷重率で圧痕を形成すると、荷重時の材料のクリープ効果により、より大きな最大深さに到達します。アクリルおよび銅の両サンプルは、目標とする最大荷重における圧子位置を一定に保つと、応力緩和挙動を示します。緩和段階での荷重損失の大きな変化は、より高い圧子負荷率の試験で観察された。
ナノベアメカニカルテスターによる応力緩和試験は、ポリマーや金属材料の時間依存の粘弾性挙動を定量的かつ確実に測定できる装置であることを示します。このテスターは、単一プラットフォーム上にナノ・マイクロモジュールを搭載した、他に類を見ない多機能な装置です。湿度・温度制御モジュールを組み合わせることで、幅広い産業に適用可能な環境試験機能を実現します。ナノ・マイクロモジュールには、スクラッチ試験、硬さ試験、摩耗試験などのモードがあり、単一のシステムで最も幅広く、最も使いやすい機械的試験機能を提供します。
さて、次はアプリケーションについてです。
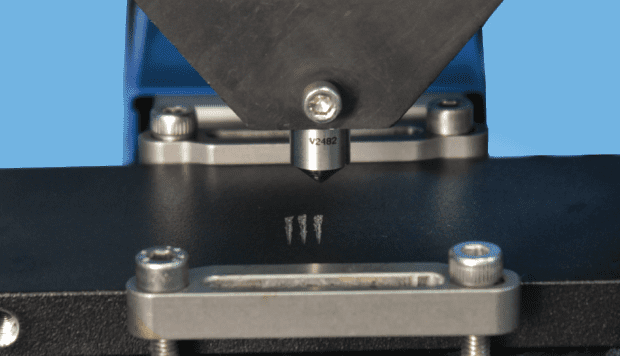
スクラッチテストによる塗膜故障の把握
はじめに
材料の表面処理は、装飾的な外観から、摩耗、腐食、その他の攻撃から基材を保護することまで、さまざまな機能的用途において重要な役割を担っています。コーティングの品質と寿命を決定する重要な要素は、その凝集力と接着力である。
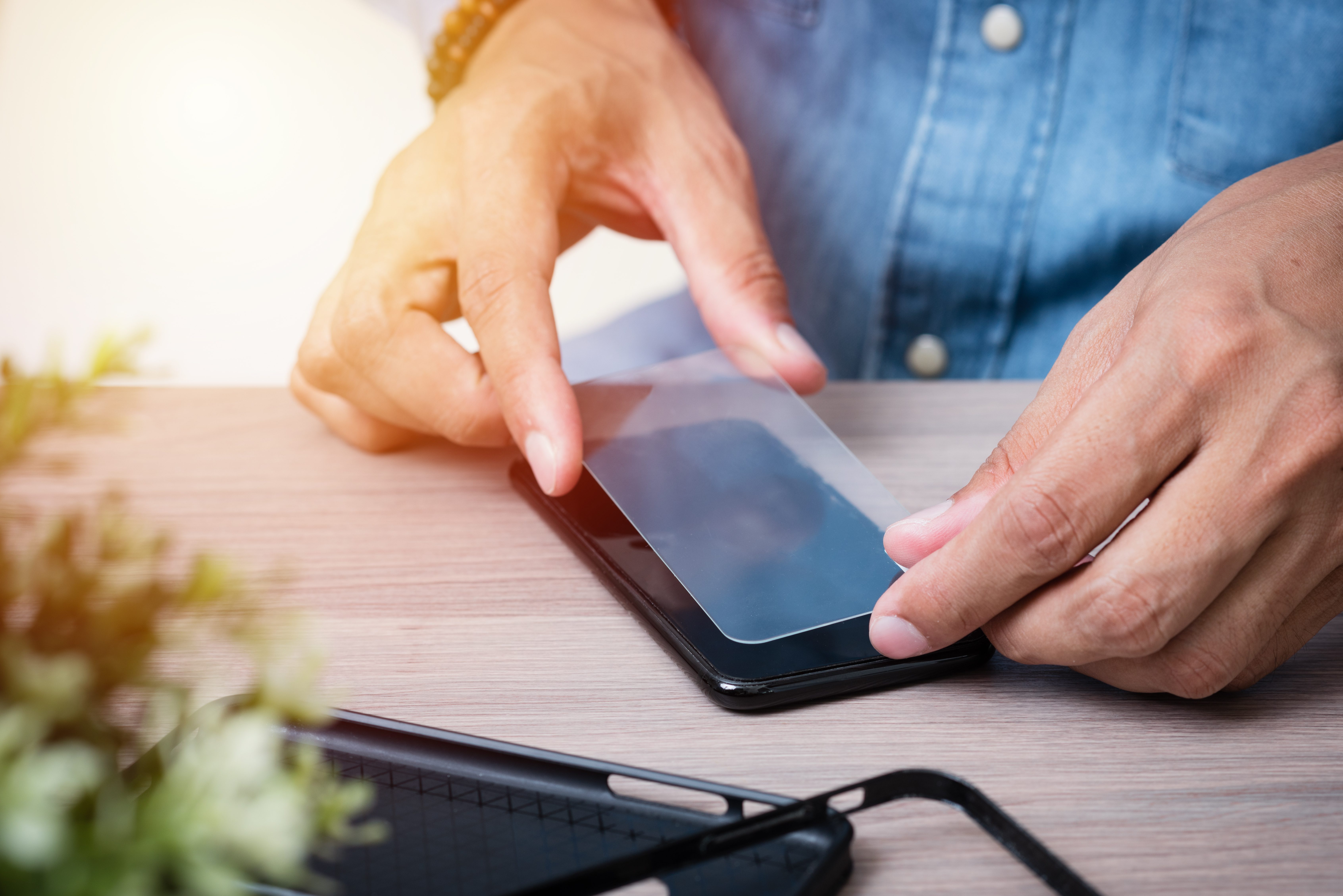
携帯電話用スクリーンプロテクトの耐傷性
スクリーンプロテクターのテストの重要性
携帯電話の画面は、飛散や傷に強い設計になっていますが、それでも損傷を受けやすいものです。日常的に携帯電話を使用することで、傷やひび割れが蓄積されるなど、消耗が激しくなります。このような画面の修理には費用がかかるため、画面の耐久性を高めるために、スクリーンプロテクターは一般的に購入され使用されている手頃な破損防止アイテムです。
ナノベアーのPB1000メカニカルテスターのマクロモジュールとアコースティックエミッション(AE)センサーを併用することで、スクリーンプロテクターがスクラッチ1試験で破損を示す臨界荷重を明確に特定し、2種類のスクリーンプロテクターの比較試験を実施することができます。
スクリーンプロテクターの素材には、TPU(熱可塑性ポリウレタン)と強化ガラスの2種類が一般的です。この2つのうち、強化ガラスは衝撃や傷を防ぐ効果が高いため、最も優れているとされています。しかし、最も高価でもあります。一方、TPUスクリーンプロテクターは安価で、プラスチック製のスクリーンプロテクターを好む消費者に人気のある選択肢です。スクリーンプロテクターは傷や衝撃を吸収するように設計されており、通常、脆い特性を持つ材料で作られているため、in-situ AE検出と組み合わせた制御スクラッチ試験は、凝集破壊(クラック、チッピング、破壊など)や接着破壊(剥離、剥落など)が発生する負荷を判断するのに最適の試験設定と言えます。
測定目的
この研究では、Nanovea社のPB1000メカニカルテスターのマクロモジュールを使用して、2種類の市販スクリーンプロテクターに対して3回のスクラッチテストを実施しました。アコースティックエミッションセンサーと光学顕微鏡を使用し、各スクリーンプロテクターに不具合が発生した際の臨界荷重を特定しました。
試験方法と手順
Nanovea PB1000 メカニカルテスターを使用して、携帯電話のスクリーンに貼られた2つのスクリーンプロテクターを摩擦センサーテーブルにクランプダウンしてテストしました。すべての傷の試験パラメータは、以下の表1にまとめられています。
結果および考察
スクリーンプロテクターは素材が異なるため、故障の種類もそれぞれ異なる。TPUスクリーンプロテクターでは致命的な故障が1つだけ発生したのに対し、強化ガラススクリーンプロテクターでは2つ発生しました。各サンプルの結果を以下の表2に示します。臨界荷重#1は、スクリーンプロテクターが顕微鏡下で凝集破壊の兆候を示し始めた荷重と定義されます。臨界荷重#2は、アコースティックエミッションのグラフデータで最初に見られるピークの変化で定義されます。
TPUスクリーンプロテクターでは、臨界荷重#2は、携帯電話のスクリーンからプロテクターが目に見えて剥がれ始めた傷の位置と相関しています。臨界荷重#2を超えると、残りのスクラッチテストで携帯電話の画面表面にスクラッチが発生しました。強化ガラス製スクリーンプロテクターでは、臨界荷重#1が放射状の割れが発生し始めた位置と相関しています。臨界荷重#2は、より高荷重でスクラッチの終盤に発生します。音響放射はTPUスクリーンプロテクターよりも大きな大きさですが、携帯電話のスクリーンにダメージはありませんでした。どちらの場合も、臨界荷重#2は深さの大きな変化に対応し、圧子がスクリーンプロテクターを貫通したことを示しています。
結論
この研究では、Nanovea PB1000 メカニカルテスターが制御された再現性のあるスクラッチ試験を実施し、同時にアコースティックエミッション検出を使用して TPU および強化ガラス製のスクリーンプロテクターで接着および凝集破壊が発生する荷重を正確に特定できることを紹介しています。本書で紹介する実験データは、強化ガラスが携帯電話のスクリーンの傷防止に最も適しているという当初の想定を裏付けるものです。
Nanovea メカニカル テスターは、ISO および ASTM 準拠の Nano および Micro モジュールを使用して、正確で再現性のある押し込み、傷、摩耗の測定機能を提供します。の メカニカルテスター は完全なシステムであり、薄いか厚いか、柔らかいか硬いコーティング、フィルム、および基材のあらゆる機械的特性を決定するための理想的なソリューションです。
さて、次はアプリケーションについてです。
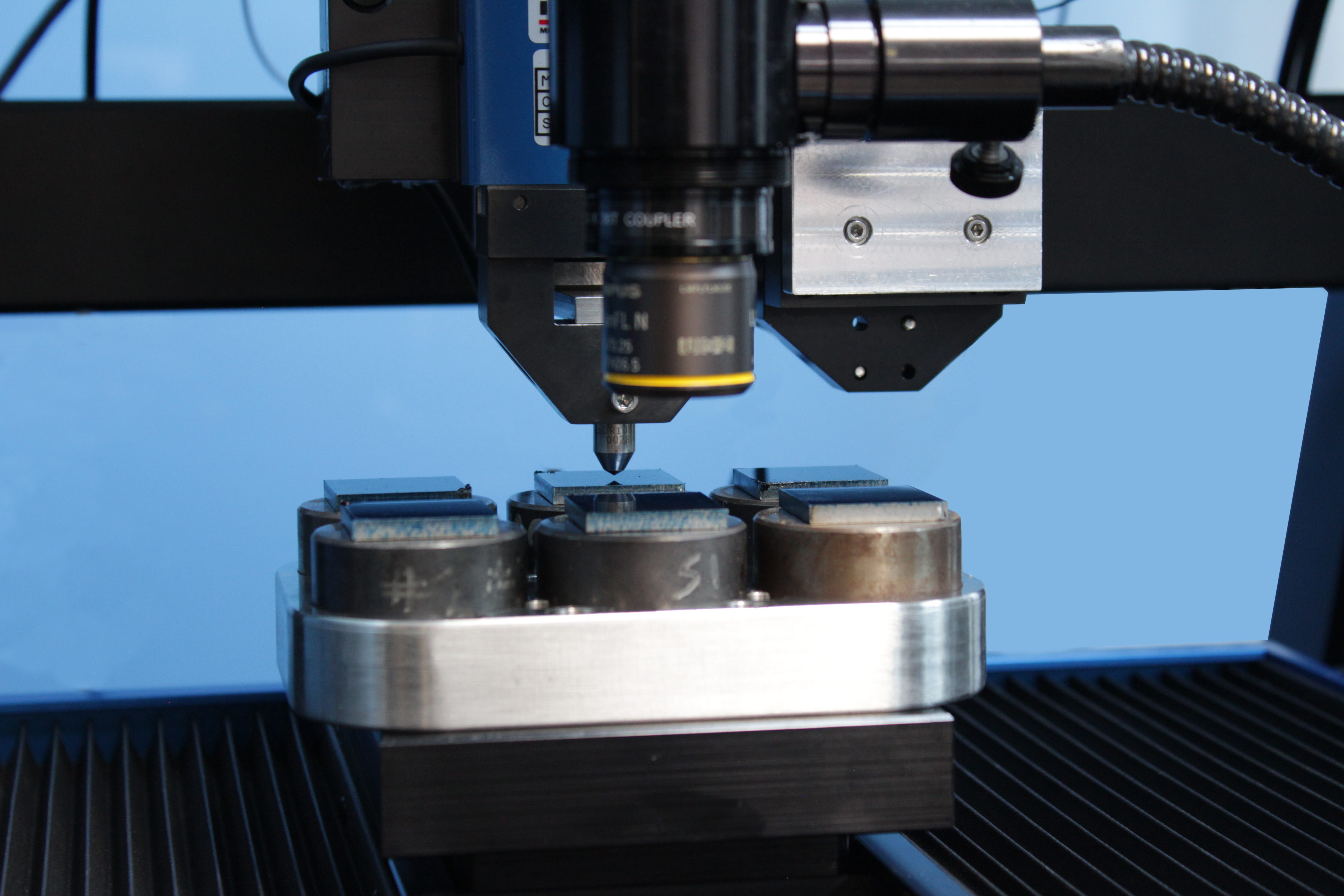
メカニカルテスターPB1000による類似サンプルのマルチスクラッチ自動化
はじめに :
コーティングは、その機能的な特性から、さまざまな産業で広く使用されています。硬度、耐侵食性、低摩擦性、高耐摩耗性など、コーティングが重要視される特性は数多くあります。これらの特性を数値化する方法として一般的に用いられているのがスクラッチ試験で、これによりコーティングの粘着性や凝集性を繰り返し測定することができます。破壊が起こる臨界荷重を比較することで、コーティングの本質的な特性を評価することができます。
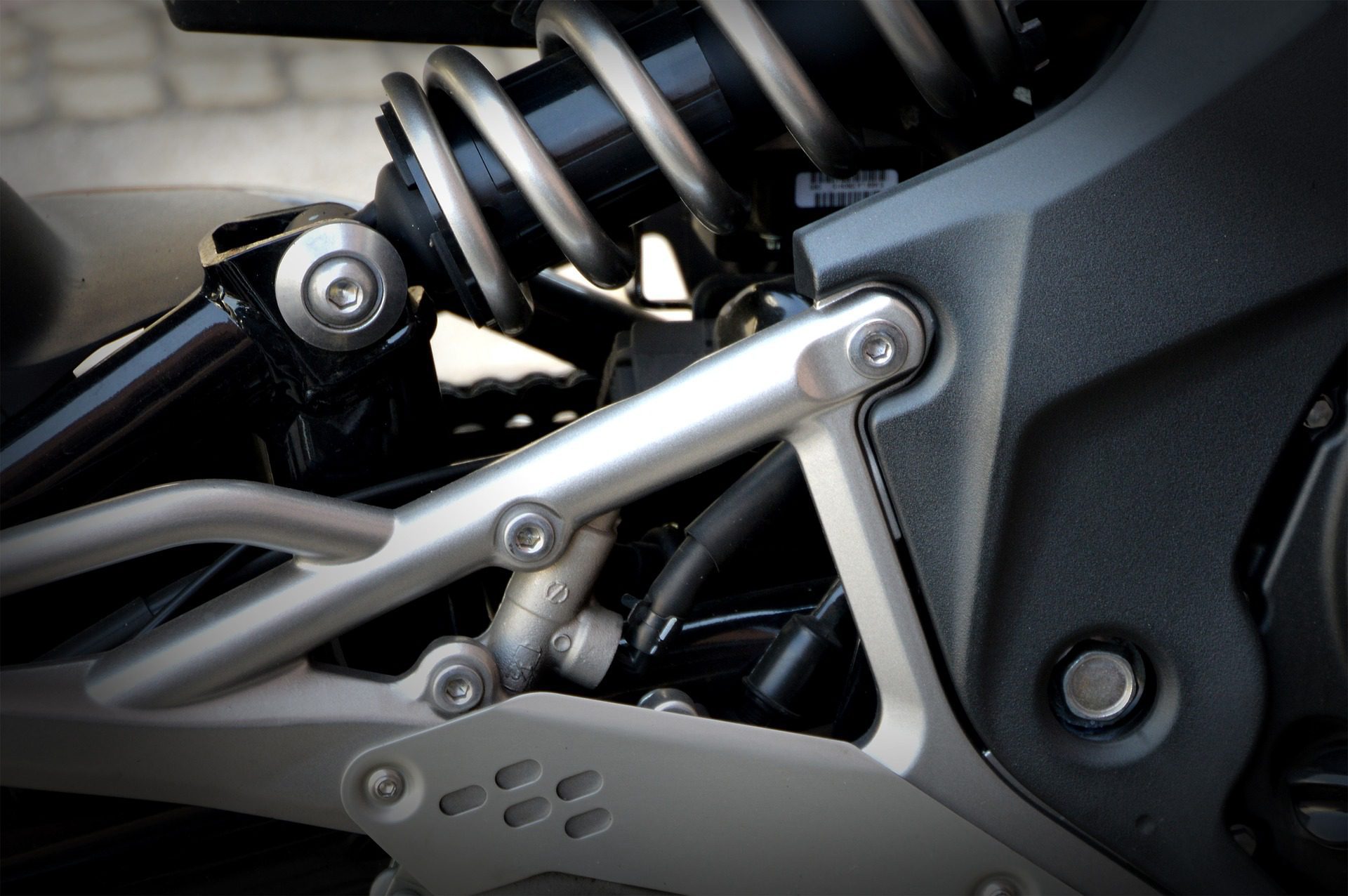
バネ定数のナノメカニクス的特性評価
機械的なエネルギーを蓄えることができるバネの歴史は古く、狩猟のための弓からドアの鍵まで、バネの技術は何世紀にもわたって使われてきた。狩猟のための弓からドアの鍵まで、バネの技術は何世紀にもわたって存在してきました。現在では、マットレスやペン、自動車のサスペンションなど、私たちの生活に欠かせない存在として、バネに依存しています。このように用途や設計が多岐に渡るため、その機械的特性を定量的に把握する能力が必要とされます。
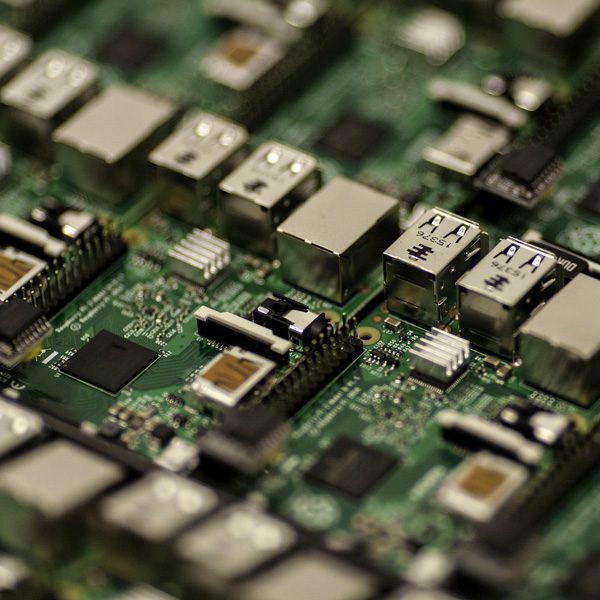
メカニカルブロードビュー地図選択ツール
時は金なり」という言葉を聞いたことがあると思います。多くの企業が、さまざまなプロセスを迅速化し、改善する方法を常に求めているのは、そのためです。ナノベアメカニカルテスターを使用すれば、圧痕試験に関して、スピード、効率、精度を品質管理または研究開発プロセスに組み込むことができます。このアプリケーションノートでは、ナノベアメカニカルテスターとブロードビューマップおよび選択ツールソフトウェアの機能を用いて、時間を節約する簡単な方法を紹介します。
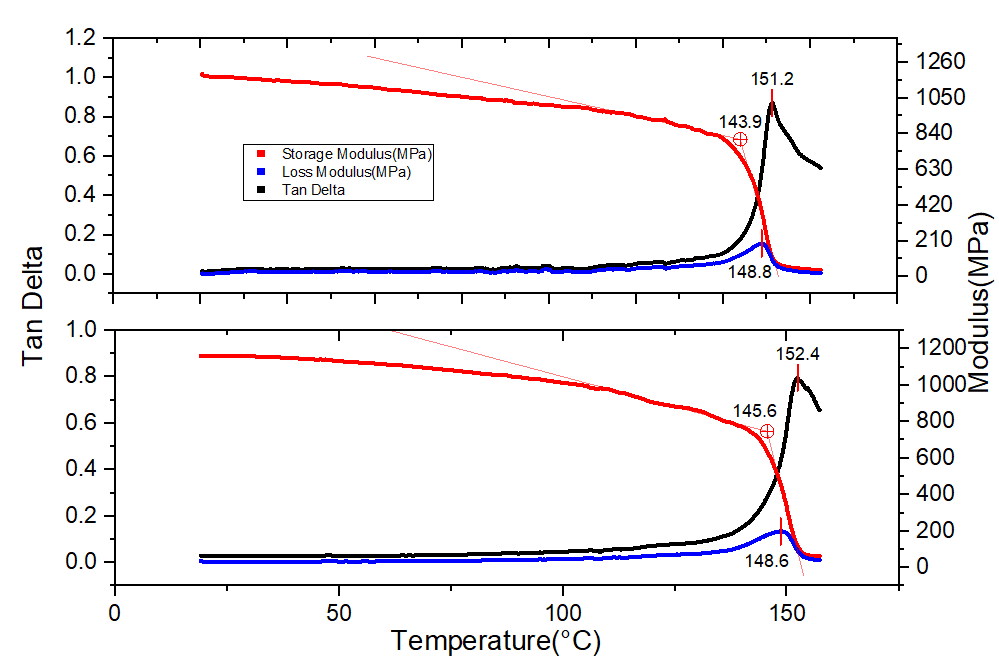
ナノインデンテーションDMAによるローカルスポットガラス転移測定
詳細はこちら
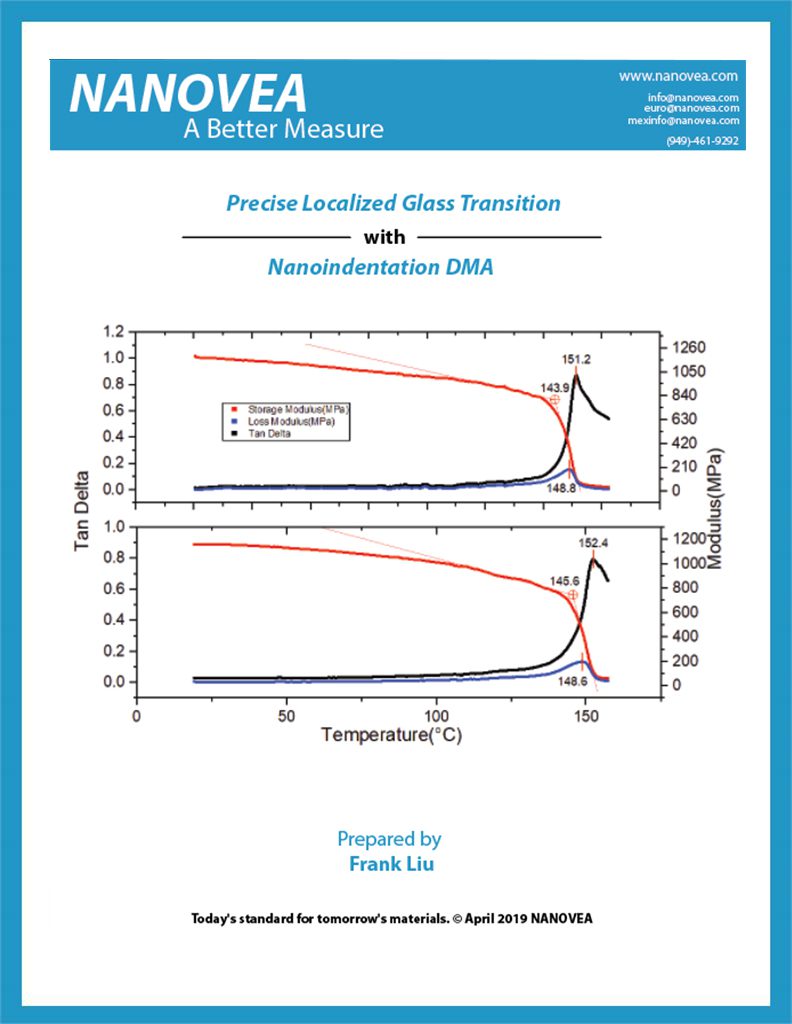
ナノインデンテーションによる応力緩和測定
詳細はこちら
さて、次はアプリケーションについてです。
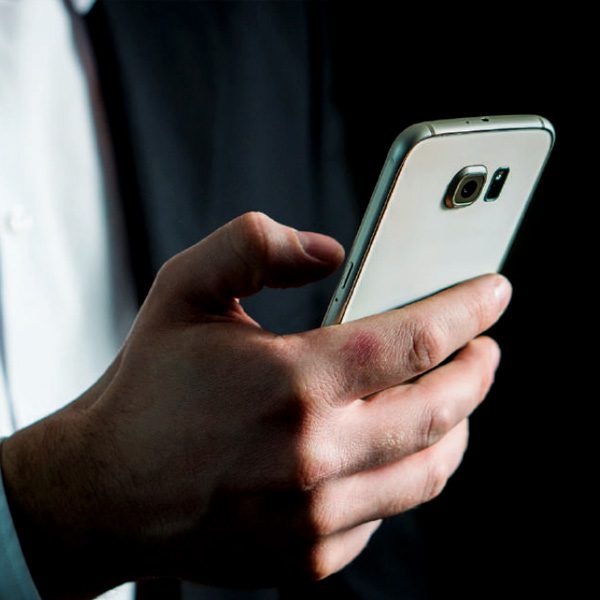
ソフトで柔軟な素材への圧縮
柔らかい素材、柔軟な素材のテストの重要性
非常に柔らかく柔軟性のあるサンプルの例として、マイクロエレクトロメカニカルシステムがある。MEMSは、プリンター、携帯電話、自動車など、日常的に使用される製品に使用されている[1]。また、バイオセンサ[2]やエネルギーハーベスティング[3]などの特殊な機能にも利用されている。MEMSの応用には、元の形状と圧縮された形状の間を可逆的に繰り返し移行できることが必要である[4]。機械的な力に対して構造体がどのように反応するかを理解するために、圧縮試験を実施することができます。圧縮試験は、さまざまなMEMS構成の試験と調整、およびこれらのサンプルの力の上限と下限の試験に利用することができます。
測定目的
このケーススタディでは、ナノベアがユニークな2つの柔軟なバネのようなサンプルに対して圧縮試験を実施しました。非常に低い荷重で圧縮を行い、大きな変位を記録しながら、低荷重で正確にデータを取得する当社の能力と、これがMEMS産業にどのように応用できるかを紹介します。プライバシーポリシーにより、サンプルとその由来は明らかにしていません。
測定パラメータ
注)負荷速度1V/minは、圧子が空中にある場合、約100μmの変位に比例します。
結果および考察
機械的な力に対するサンプルの応答は、荷重対深さの曲線で見ることができます。サンプルAは、上記の試験パラメータで線形弾性変形のみを示します。図2は、75μNでの荷重-深度曲線で達成できる安定性の好例です。荷重センサと深度センサが安定しているため、試料から有意な機械的応答を容易に感知することができます。
深さ750μmを過ぎたあたりから、グラフに破断のような挙動が見られるようになりました。これは深さ850μmと975μmで荷重が急激に減少していることからわかります。8mNの範囲で1mm以上の高荷重で移動しているにもかかわらず、当社の高感度荷重センサーと深度センサーにより、以下のようななめらかな荷重-深度曲線が得られています。
剛性は,荷重-深さ曲線の無負荷部分から算出した。剛性は、試料を変形させるために必要な力の大きさを反映しています。この剛性計算では、材料の実際の比率が分からないため、擬似的なポアソン比である0.3を使用しました。この場合、試料Bは試料Aよりも硬いことがわかりました。
結論
Nanovea Mechanical TesterのNano Moduleを使用して、2種類の柔軟なサンプルの圧縮試験を実施しました。試験は非常に低い荷重(1mm)で実施されました。Nanoモジュールを用いたナノスケールの圧縮試験により、非常に柔らかく柔軟なサンプルを試験するモジュールの能力が示されました。この研究の追加試験として、Nanovea Mechanical Testerのマルチローディングオプションにより、繰り返されるサイクル荷重がバネのようなサンプルの弾性回復にどのような影響を与えるかについて取り上げることができます。
このテスト方法の詳細については、[email protected] までお気軽にお問い合わせください。また、その他のアプリケーションノートについては、当社の広範なアプリケーションノートデジタルライブラリを参照してください。
参考文献
[1] "MEMSの紹介と応用分野".EEHerald, 1 Mar. 2017, www.eeherald.com/section/design-guide/mems_application_introduction.html.
[2] Louizos, Louizos-Alexandros; Athanasopoulos, Panagiotis G.; Varty, Kevin (2012).「Microelectromechanical Systems and Nanotechnology.次のステント技術時代のためのプラットフォーム".Vasc Endovascular Surg.46 (8):605–609. doi:10.1177/1538574412462637.PMID 23047818.
[3] Hajati, Arman; Sang-Gook Kim (2011).「超広帯域圧電エネルギーハーベスティング".AppliedPhysics Letters.99 (8):083105. doi:10.1063/1.3629551.
[4] Fu, Haoran, et al. "Morphable 3D mesostructures and microelectronic devices by multistable bucklingmechanics.".ネイチャー・マテリアル 17.3 (2018): 268.
さて、次はアプリケーションについてです。
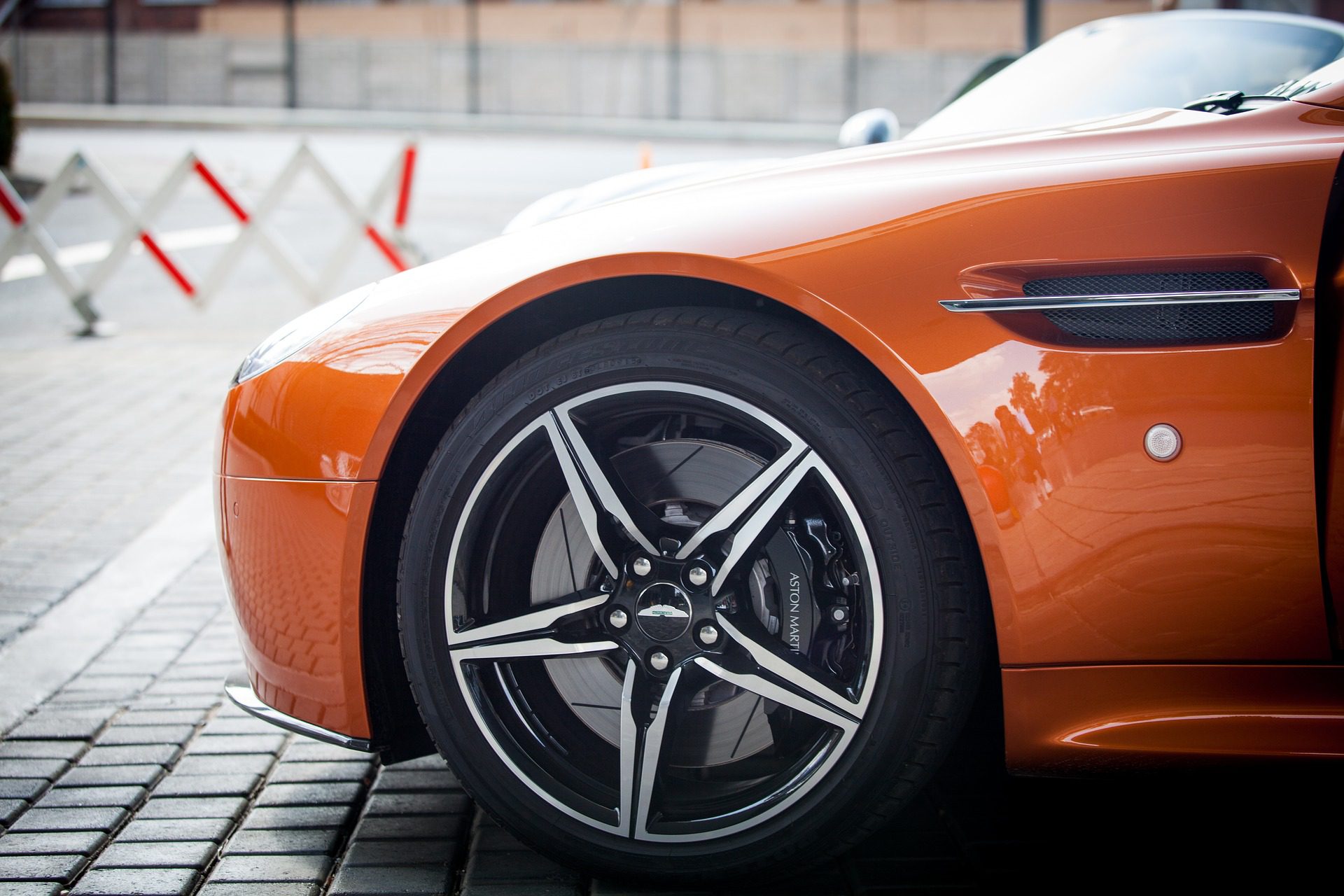
ゴムの粘弾性解析
ゴムの粘弾性解析
詳細はこちら
タイヤは,車両が道路を走行する際に周期的に大きな変形を受ける。過酷な路面条件にさらされたタイヤは、ネジ山の摩耗、摩擦による発熱、ゴムの老化など、さまざまな要因で寿命が短くなる。
その結果、タイヤは通常、カーボン充填ゴム、ナイロンコード、及びスチールワイヤ等からなる複合層構造を有する。特に、タイヤシステムの異なる領域におけるゴムの組成は、耐摩耗糸、クッションゴム層、および硬質ゴムベース層を含むがこれらに限定されない異なる機能特性を提供するように最適化されている。
ゴムの粘弾性挙動の信頼性が高く再現性のあるテストは、新しいタイヤの品質管理と研究開発、さらには古いタイヤの寿命の評価において重要です。動的機械解析(DMA) ナノインデンテーション 粘弾性を特徴付ける手法です。制御された振動応力が適用されると、結果として生じるひずみが測定され、ユーザーはテストされた材料の複素弾性率を決定できます。
カテゴリー
- アプリケーションノート
- ブロック・オン・リングトライボロジー
- 腐食トライボロジー
- 摩擦試験|摩擦係数
- 高温機械試験
- 高温トライボロジー
- 湿度・ガス トライボロジー
- 湿度機械試験
- 圧痕|クリープとリラクゼーション
- 圧痕|破壊靭性
- 圧痕|硬度・弾性率
- 圧痕|紛失と保管
- 圧痕|応力と歪み
- 圧痕|降伏強度と疲労の関係
- ラボラトリーテスト
- リニアトライボロジー
- 液体機械試験
- 液状トライボロジー
- 低温トライボロジー
- メカニカルテスト
- プレスリリース
- プロフィロメトリー|平坦度・反り率
- プロフィロメトリー|幾何学と形状
- プロフィロメトリー|粗さと仕上がり
- プロフィロメトリー|段差の高さと厚み
- プロフィロメトリー|テクスチャーとグレーン
- プロフィロメトリー|体積・面積
- プロフィロメトリーテスト
- リング・オン・リング トライボロジー
- 回転トライボロジー
- スクラッチテスト|接着剤の不具合について
- スクラッチテスト|コヒーシブフェール
- スクラッチテスト|マルチパス摩耗
- スクラッチテスト|スクラッチハードネス
- スクラッチテスト トライボロジー
- トレードショー
- トライボロジー試験
- 未分類
月別アーカイブ
- 2022年7月
- 2022年7月
- 2022年7月
- 2022年7月
- 2022年7月
- 2022年7月
- 2022年7月
- 2022年7月
- 2022年7月
- 2022年7月
- 2022年7月
- 2022年7月
- 2022年7月
- 2022年7月
- 2022年7月
- 2022年7月
- 2022年7月
- 2022年7月
- 2022年7月
- 2022年7月
- 2022年7月
- 2022年7月
- 2022年7月
- 2022年7月
- 2022年7月
- 2022年7月
- 2022年7月
- 2022年7月
- 2022年7月
- 2022年7月
- 2022年7月
- 2022年7月
- 2022年7月
- 2022年7月
- 2022年7月
- 2022年7月
- 2022年7月
- 2022年7月
- 2022年7月
- 2022年7月
- 2022年7月
- 2022年7月
- 2022年7月
- 2022年7月
- 2022年7月
- 2022年7月
- 2022年7月
- 2022年7月
- 2022年7月
- 2022年7月
- 2022年7月
- 2022年7月
- 2022年7月
- 2022年7月
- 2022年7月
- 2022年7月
- 2022年7月
- 2022年7月
- 2022年7月
- 2022年7月
- 2022年7月
- 2022年7月
- 2022年7月
- 2022年7月
- 2022年7月
- 2022年7月
- 2022年7月
- 2022年7月
- 2022年7月
- 2022年7月
- 2022年7月
- 2022年7月
- 2022年7月
- 2022年7月
- 2022年7月
- 2022年7月
- 2022年7月
- 2022年7月
- 2022年7月
- 2022年7月
- 2022年7月
- 2022年7月
- 2022年7月
- 2022年7月
- 2022年7月
- 2022年7月
- 2022年7月
- 2022年7月
- 2022年7月
- 2022年7月
- 2022年7月
- 2022年7月
- 2022年7月
- 2022年7月
- 2022年7月
- 2022年7月
- 2022年7月
- 2022年7月
- 2022年7月
- 2022年7月
- 2022年7月
- 2022年7月
- 2022年7月
- 2022年7月
- 2022年7月
- 2022年7月
- 2022年7月
- 2022年7月
- 2022年7月
- 2022年7月
- 2022年7月
- 2022年7月
- 2022年7月
- 2022年7月
- 2022年7月
- 2022年7月
- 2022年7月
- 2022年7月
- 2022年7月
- 2022年7月
- 2022年7月
- 2022年7月
- 2022年7月
- 2022年7月
- 2022年7月
- 2022年7月
- 2022年7月
- 2022年7月
- 2022年7月
- 2022年7月
- 2022年7月
- 2022年7月
- 2022年7月
- 2022年7月
- 2022年7月