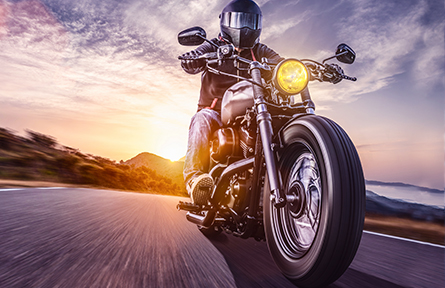
Scratch Testing Module
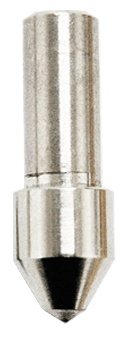
Micro Scratch Adhesion Testing identifies critical loads optically using a built-in video microscope. These critical loads are used to quantify the adhesive and cohesive properties of different film/substrate combinations.
How does it work?
During Scratch Testing, a conical spherical tip, diamond or WC, is drawn across the coated surface with an increasing load, resulting in various types of failure at specific critical loads.
These critical loads are used to quantify the adhesive and cohesive properties of different film/substrate combinations. In addition, failure points can be determined using frictional force and depth measurements.
Depth measurements provide the plastic and elastic portion of the deformation.
Constant road scratch testing can be used, in mapping, to check the surface uniformity.
Extreme Versatility
STANDARDS
- ASTM D7187
- ASTM C1624
- ASTM D7027
- ASTM G171
- ISO 20502
- ISO 1518
- DIN EN 1071
- DVM-0058-PA
* Instrument parameter limits may differ
from those specified within the standard.
Properties Analyzed
- Cohesive & Adhesive failure
- Adhesion Strength
- Marring (Resistance) and Crack/Fracture initiation
- Plastic & Elastic Deformation depth and others
- Full Scratch Image for post inspection using tracking zoomed view
- Tracking Zoomed View for easy post inspection with data depth, friction and AE analysis
SENSORS
- Depth
- Acoustic Emission
Rotating Lower Sample
- Samples with flat surface for the test, Cylindrical Samples.
- Any types of materials.
Fixed Upper Sample
- Various sizes Sphero-conical or Rockwell Diamond or WC tips
- Custom materials and geometries
Environmental Conditions
- Liquid Cup and Liquid Heating up to 150 °C
- Lubrication Drop by Drop
- Humidity Control
- Cooling Chamber -40 °C
- Corrosion Testing Cup
- Various Gases
- Vacuum (Custom)