표면 결함은 재료 가공 및 제품 제조에서 발생합니다. 인라인 표면 품질 검사는 최종 제품의 가장 엄격한 품질 관리를 보장합니다. 나노베아 3D 비접촉 프로파일로미터 접촉 없이 샘플의 거칠기를 결정하는 고유한 기능을 갖춘 색채 공초점 기술을 활용합니다. 여러 프로파일러 센서를 설치하여 제품의 다양한 영역의 거칠기와 질감을 동시에 모니터링할 수 있습니다. 분석 소프트웨어에 의해 실시간으로 계산된 거칠기 임계값은 빠르고 안정적인 합격/불합격 도구 역할을 합니다.
측정 목표
이 연구에서는 포인트 센서가 장착된 나노베아 거칠기 검사 컨베이어 시스템을 사용하여 아크릴 및 사포 샘플의 표면 거칠기를 검사합니다. 생산 라인에서 실시간으로 빠르고 안정적인 인라인 거칠기 검사를 제공하는 나노비아 비접촉식 프로파일로미터의 성능을 보여줍니다.
결과 및 토론
컨베이어 프로파일로미터 시스템은 트리거 모드와 연속 모드의 두 가지 모드로 작동할 수 있습니다. 그림 2에서 볼 수 있듯이 트리거 모드에서는 샘플이 광학 프로파일러 헤드 아래를 통과할 때 표면 거칠기가 측정됩니다. 이에 비해 연속 모드는 금속판이나 직물과 같은 연속 시료의 표면 거칠기를 중단 없이 측정합니다. 여러 광학 프로파일러 센서를 설치하여 다양한 샘플 영역의 거칠기를 모니터링하고 기록할 수 있습니다.
실시간 거칠기 검사 측정 중에는 그림 4 및 그림 5와 같이 소프트웨어 창에 합격 및 불합격 경고가 표시됩니다. 거칠기 값이 지정된 임계값 내에 있으면 측정된 거칠기가 녹색으로 강조 표시됩니다. 그러나 측정된 표면 거칠기가 설정된 임계값 범위를 벗어나면 강조 표시가 빨간색으로 바뀝니다. 이 기능은 사용자가 제품의 표면 마감 품질을 확인할 수 있는 도구를 제공합니다.
다음 섹션에서는 아크릴과 사포 등 두 가지 유형의 샘플을 사용하여 검사 시스템의 트리거 및 연속 모드를 시연합니다.
트리거 모드: 아크릴 샘플의 표면 검사
일련의 아크릴 샘플이 컨베이어 벨트 위에 정렬되어 그림 1과 같이 광학 프로파일러 헤드 아래로 이동합니다. 그림 6의 가색 보기는 표면 높이의 변화를 보여줍니다. 거울처럼 완성된 아크릴 샘플 중 일부는 그림 6b와 같이 거친 표면 질감을 만들기 위해 샌딩 처리되었습니다.
아크릴 샘플이 광학 프로파일러 헤드 아래에서 일정한 속도로 움직이면 그림 7과 그림 8과 같이 표면 프로파일이 측정됩니다. 측정된 프로파일의 거칠기 값은 동시에 계산되어 임계값과 비교됩니다. 거칠기 값이 설정된 임계값을 초과하면 빨간색 불합격 경고가 시작되어 사용자가 생산 라인에서 불량 제품을 즉시 감지하고 위치를 파악할 수 있습니다.

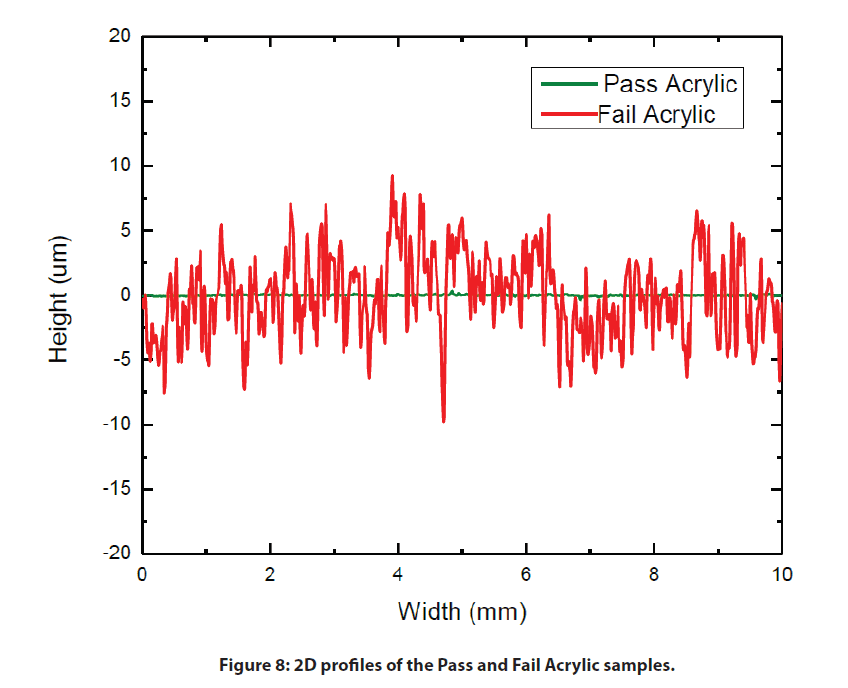
연속 모드: 사포 샘플의 표면 검사
그림 9와 같이 사포 샘플 표면의 표면 높이 맵, 거칠기 분포 맵, 합격/불합격 거칠기 임계값 맵을 확인할 수 있습니다. 사포 샘플은 표면 높이 맵에서 볼 수 있듯이 사용된 부분에 몇 개의 높은 피크가 있습니다. 그림 9C의 팔레트에서 다른 색상은 로컬 표면의 거칠기 값을 나타냅니다. 거칠기 맵에서 사포 샘플의 온전한 영역은 균일한 거칠기를 나타내는 반면, 사용된 영역은 진한 파란색으로 강조 표시되어 이 영역의 거칠기 값이 감소되었음을 나타냅니다. 그림 9D와 같이 이러한 영역을 찾기 위해 합격/불합격 거칠기 임계값을 설정할 수 있습니다.
사포가 인라인 프로파일러 센서 아래를 계속 통과하면 그림 10과 같이 실시간 로컬 거칠기 값이 계산되고 기록됩니다. 설정된 거칠기 임계값에 따라 소프트웨어 화면에 합격/불합격 경고가 표시되어 빠르고 신뢰할 수 있는 품질 관리 도구로 사용됩니다. 생산 라인의 제품 표면 품질을 현장에서 검사하여 결함이 있는 부분을 적시에 발견할 수 있습니다.
이 애플리케이션에서는 광학 비접촉식 프로파일러 센서가 장착된 나노베아 컨베이어 프로파일로미터가 신뢰할 수 있는 인라인 품질 관리 도구로 효과적이고 효율적으로 작동하는 것을 보여주었습니다.
검사 시스템을 생산 라인에 설치하여 현장에서 제품의 표면 품질을 모니터링할 수 있습니다. 거칠기 임계값은 제품의 표면 품질을 판단하는 신뢰할 수 있는 기준으로 작동하여 사용자가 결함이 있는 제품을 제때 발견할 수 있도록 합니다. 다양한 유형의 제품에 대한 검사 요구 사항을 충족하기 위해 트리거 모드와 연속 모드의 두 가지 검사 모드가 제공됩니다.
여기에 표시된 데이터는 분석 소프트웨어에서 사용할 수 있는 계산의 일부만을 나타냅니다. 나노베아 프로파일로미터는 반도체, 마이크로일렉트로닉스, 태양광, 섬유, 광학, 자동차, 항공우주, 야금, 기계 가공, 코팅, 제약, 생의학, 환경 등 다양한 분야의 거의 모든 표면을 측정합니다.