类别。实验室检测
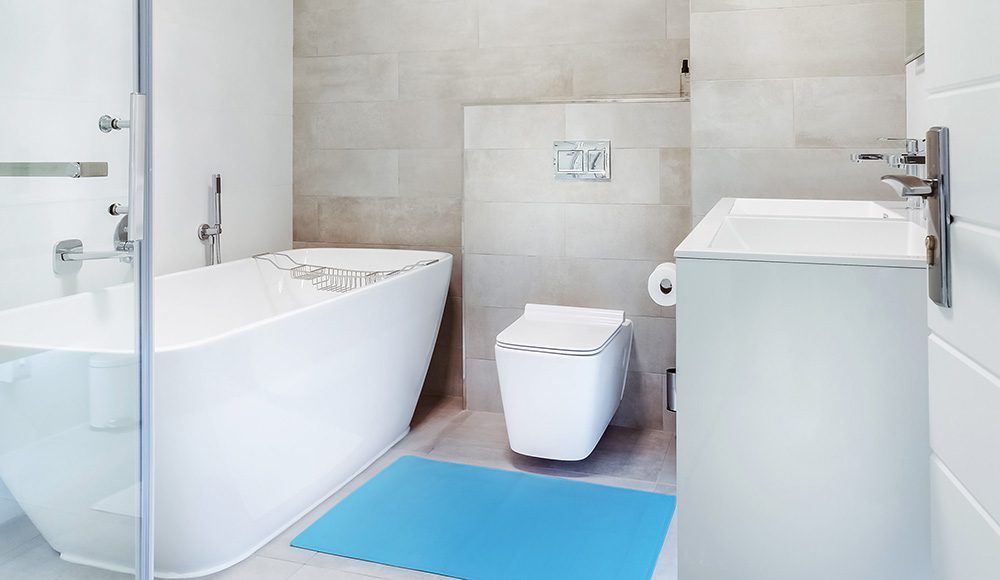
陶瓷:用于晶粒检测的快速点阵纳米压痕测试
简介
纳米压痕 已成为一种广泛应用的小尺度材料机械行为测量技术i ii。纳米压痕测量的高分辨率载荷-位移曲线可以提供各种物理机械特性,包括硬度、杨氏模量、蠕变、断裂韧性等。
快速映射缩进的重要性
纳米压痕技术进一步普及的一个重要瓶颈是时间消耗。通过传统纳米压痕程序绘制机械性能图很容易花费数小时,这阻碍了该技术在大规模生产行业的应用,例如半导体、航空航天、MEMS、瓷砖等消费产品等。
事实证明,快速映射在瓷砖制造行业中至关重要,单个瓷砖上的硬度和杨氏模量映射可以提供表明表面均匀程度的数据分布。可以在此映射中勾勒出瓷砖上较软的区域,并显示更容易因某人住宅中每天发生的物理影响而发生故障的位置。可以在不同类型的瓷砖上进行映射以进行比较研究,并在一批相似的瓷砖上进行映射以测量质量控制过程中瓷砖的一致性。通过快速映射方法,测量设置的组合可以是广泛的、准确且高效的。
测量目标
在这项研究中,Nanovea 机械测试仪,在 FastMap 模式下用于高速绘制地砖的机械属性。我们展示了 Nanovea 机械测试仪以高精度和可重复性执行两次快速纳米压痕测绘的能力。
测试条件
Nanovea 机械测试仪用于使用 Berkovich 压头以 FastMap 模式在地砖上执行一系列纳米压痕。下面总结了所创建的两个缩进矩阵的测试参数。
表 1:测试参数汇总。
结果与讨论
图 1:625 压痕硬度映射的 2D 和 3D 视图。
图 2:625 凹痕基体的显微照片,显示晶粒。
625 凹痕矩阵在 0.20mm 上进行2 存在大的可见颗粒的区域。该颗粒(图 2)的平均硬度低于瓷砖的整体表面。 Nanovea Mechanical 软件允许用户查看 2D 和 3D 模式下的硬度分布图,如图 1 所示。利用样品台的高精度位置控制,该软件允许用户深入定位此类区域机械特性映射。
图 3:1600 压痕硬度映射的 2D 和 3D 视图。
图 4:1600 凹痕矩阵的显微照片。
还在同一块瓷砖上创建了 1600 凹痕矩阵来测量表面的均匀性。在这里,用户再次能够看到 3D 或 2D 模式下的硬度分布(图 3)以及凹痕表面的显微镜图像。根据给出的硬度分布,可以得出结论,由于高硬度和低硬度数据点的均匀分散,该材料是多孔的。
与传统的纳米压痕程序相比,本研究中的 FastMap 模式显着减少了耗时且更具成本效益。它能够快速定量绘制硬度和杨氏模量等机械特性,并提供晶粒检测和材料一致性的解决方案,这对于批量生产中各种材料的质量控制至关重要。
结论
在这项研究中,我们展示了 Nanovea Mechanical Tester 使用 FastMap 模式执行快速、精确的纳米压痕绘图的能力。瓷砖上的机械特性图利用平台的位置控制(精度为 0.2μm)和力模块灵敏度来高速检测表面颗粒并测量表面的均匀性。
本研究中使用的测试参数是根据基体和样品材料的尺寸确定的。可以选择多种测试参数,将总压痕周期时间优化为每个压痕 3 秒(或每 10 个压痕 30 秒)。
Nanovea 机械测试仪的纳米和微米模块均包括符合 ISO 和 ASTM 的压痕、划痕和磨损测试仪模式,可在单个系统中提供最广泛、最用户友好的测试范围。 Nanovea 无与伦比的系列是测定薄或厚、软或硬涂层、薄膜和基材的全方位机械性能的理想解决方案,包括硬度、杨氏模量、断裂韧性、附着力、耐磨性等。
此外,除了粗糙度等其他表面测量之外,可选的 3D 非接触式轮廓仪和 AFM 模块还可用于压痕、划痕和磨损轨迹的高分辨率 3D 成像。
作者:Duanjie Li,博士 由 Pierre Leroux 和 Jocelyn Esparza 修订
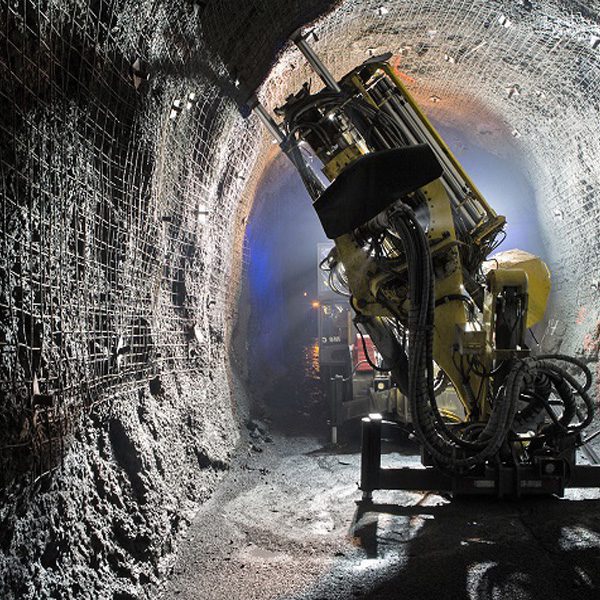
利用微观建议改进采矿程序
微压痕研究和质量控制
岩石力学是研究岩体的机械行为,应用于采矿、钻探、水库生产和民用建筑行业。先进的仪器对机械性能的精确测量使这些行业的零件和程序得以改进。通过了解微观尺度的岩石力学,可以确保成功的质量控制程序。
测量目标
在此应用中,Nanovea 机械测试器 测量矿物岩石样品的维氏硬度 (Hv)、杨氏模量和断裂韧性。该岩石由黑云母、长石和石英组成,形成标准的花岗岩复合材料。每个都单独测试。
结果和讨论
本节包括一个汇总表,对不同样品的主要数值结果进行比较,然后是完整的结果列表,包括所进行的每一个压痕,如果有的话,还附有压痕的显微照片。这些完整的结果显示了硬度和杨氏模量的测量值,以及穿透深度(Δd)的平均值和标准偏差。应该考虑到,在表面粗糙度与压痕大小相同的情况下,结果会出现较大的变化。
硬度和断裂韧性的主要数值结果汇总表
结论
Nanovea机械测试仪在矿物岩石的坚硬表面展示了可重复性和精确的压痕结果。形成花岗岩的每种材料的硬度和杨氏模量是直接从深度与载荷的曲线上测量的。粗糙的表面意味着在更高的载荷下进行测试,可能会引起微裂纹。微裂纹可以解释测量中看到的一些变化。由于样品表面粗糙,通过标准的显微镜观察,裂缝是无法察觉的。因此,不可能计算出需要测量裂纹长度的传统断裂韧度数字。相反,我们使用该系统在增加载荷的同时,通过深度与载荷曲线的位错来检测裂纹的起始。
断裂阈值载荷被报告在发生故障的载荷处。与简单测量裂纹长度的传统断裂韧性测试不同,获得的是阈值断裂开始时的载荷。此外,受控和密切监测的环境允许测量硬度,以作为比较各种样品的定量值。
现在,让我们来谈谈你的申请
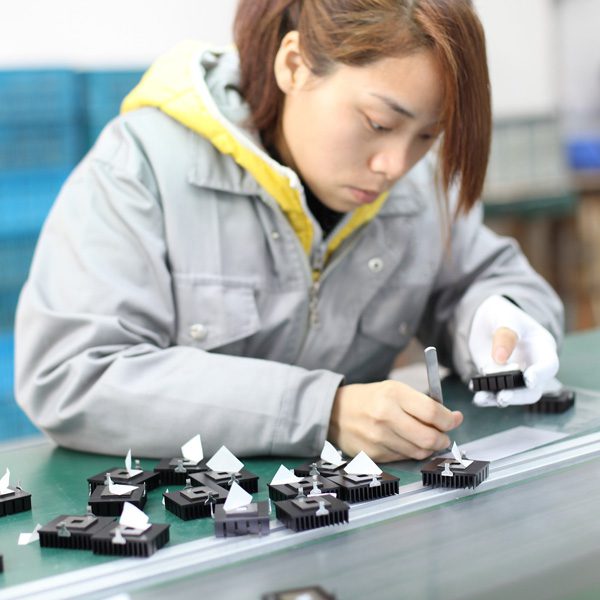
在线粗糙度检查
了解更多
非接触式轮廓仪对在线粗糙度检测的重要性
表面缺陷来源于材料加工和产品制造。在线表面质量检测可确保对最终产品进行最严格的质量控制。纳诺维亚酒店 3D 非接触式轮廓仪 利用具有独特功能的彩色共焦技术,无需接触即可确定样品的粗糙度。可安装多个轮廓仪传感器,同时监测产品不同区域的粗糙度和纹理。由分析软件实时计算的粗糙度阈值可作为快速可靠的通过/失败工具。
测量目标
在这项研究中,Nanovea粗糙度检测传送系统配备了一个点式传感器,用于检测丙烯酸和砂纸样品的表面粗糙度。我们展示了Nanovea非接触式轮廓仪在生产线上实时提供快速、可靠的在线粗糙度检测的能力。
结果和讨论
输送式轮廓仪系统可以在两种模式下工作,即触发模式和连续模式。如图2所示,在触发模式下,当样品在光学轮廓仪头下通过时,样品的表面粗糙度被测量。相比之下,连续模式可以不间断地测量连续样品的表面粗糙度,如金属板和织物。可以安装多个光学轮廓仪传感器来监测和记录不同样品区域的粗糙度。
在实时粗糙度检测测量过程中,软件窗口显示通过和失败告警,如图4和图5所示。当粗糙度值在给定的阈值内时,测量的粗糙度以绿色突出显示。然而,当测量的表面粗糙度超出设定的阈值范围时,高亮部分变成红色。这为用户提供了一个工具来确定产品表面光洁度的质量。
在下面的章节中,将使用两种类型的样品,如丙烯酸和砂纸来演示检测系统的触发和连续模式。
触发模式。亚克力样品的表面检查
如图1所示,一系列亚克力样品在传送带上排列并在光学轮廓仪头下移动。图6中的假彩色视图显示了表面高度的变化。如图6b所示,一些镜子般的成品亚克力样品已经被打磨,形成了粗糙的表面纹理。
当亚克力样品在光学轮廓仪头下以恒定的速度移动时,表面轮廓被测量,如图7和图8所示。同时计算出所测轮廓的粗糙度值,并与阈值进行比较。当粗糙度值超过设定的阈值时,就会启动红色故障警报,使用户能够立即发现并找到生产线上的缺陷产品。
连续模式。砂纸样品的表面检查
如图9所示,砂纸样品表面的表面高度图、粗糙度分布图和合格/不合格粗糙度阈值图。如表面高度图所示,砂纸样品在使用的部分有几个较高的峰值。图9C的调色板上的不同颜色代表了局部表面的粗糙度值。粗糙度图在砂纸样品的完整区域表现出均匀的粗糙度,而使用过的区域则以深蓝色突出显示,表明该区域的粗糙度值降低。可以设置一个合格/不合格的粗糙度阈值来定位这样的区域,如图9D所示。
当砂纸连续通过在线轮廓仪传感器下方时,实时的局部粗糙度值被计算和记录,如图10所示。根据设定的粗糙度阈值,在软件屏幕上显示合格/不合格警报,作为质量控制的一个快速和可靠的工具。对生产线上的产品表面质量进行现场检查,及时发现有缺陷的地方。
在这个应用中,我们已经证明了Nanovea传送带轮廓仪配备的光学非接触式轮廓仪传感器可以作为一个可靠的在线质量控制工具有效和高效地工作。
该检测系统可以安装在生产线上,就地监测产品的表面质量。粗糙度阈值作为判断产品表面质量的可靠标准,使用户能够及时发现有缺陷的产品。提供两种检测模式,即触发模式和连续模式,以满足对不同类型产品的检测要求。
这里显示的数据只代表了分析软件中的一部分计算结果。Nanovea轮廓仪几乎可以测量任何领域的表面,包括半导体、微电子、太阳能、纤维、光学、汽车、航空航天、冶金、加工、涂层、制药、生物医学、环境和其他许多领域。
现在,让我们来谈谈你的申请

环-块磨损测试
块对环磨损评估的重要性
环块 (ASTM G77) 测试是一种广泛使用的技术,可评估材料在不同模拟条件下的滑动磨损行为,为特定摩擦学应用提供可靠的材料对排名。
测量目标
在这个应用中,Nanovea机械测试仪测量不锈钢SS304和铝Al6061金属合金样品的YS和UTS。样品的YS和UTS值是公认的,这表明Nanovea的压痕方法是可靠的。
Nanovea 的摩擦磨损试验机使用 Block-on-Ring 模块评估了 S-10 环上 H-30 块的滑动磨损行为。 H-30 块由硬度为 30HRC 的 01 工具钢制成,而 S-10 环由表面硬度为 58 至 63 HRC 的 4620 型钢制成,环直径约为 34.98 毫米。在干燥和润滑的环境中进行块环测试,以研究对磨损行为的影响。润滑测试是在 USP 重矿物油中进行的。使用 Nanovea 的磨损轨迹进行检查 3D非接触式轮廓仪。测试参数总结于表1中。磨损率(K)采用公式K=V/(F×s)评估,其中V为磨损体积,F为法向载荷,s为滑动距离。
结果和讨论
图 2 比较了干燥和润滑环境下环块测试的摩擦系数 (COF)。该块在干燥环境中的摩擦力明显大于润滑环境中的摩擦力。 COF
在前 50 转的磨合期间,COF 会波动,并在其余 200 转磨损测试中达到约 0.8 的恒定 COF。相比之下,在 USP 重矿物油润滑中进行的环块测试在整个 500,000 转磨损测试中始终表现出 0.09 的低 COF。该润滑剂可将表面之间的摩擦系数显着降低约 90 倍。
图3和图4显示了干磨损和润滑磨损试验后块上磨损疤痕的光学图像和截面2D轮廓。磨损轨迹量和磨损率如表2所示。在较低转速72 rpm、200转的干磨损试验下,钢块表现出9.45 mm˙的大磨损疤痕体积。相比之下,在矿物油润滑剂中以197转/分钟、50转的更高转速进行的磨损试验,产生的磨损轨迹体积很小,为0.03 mm˙。
ÿgure 3中的图像显示在干燥条件下的试验中发生了严重磨损,而润滑磨损试验中则发生了轻微磨损。干磨损试验过程中产生的高温和强烈振动促进了金属碎片的氧化,导致严重的三体磨损。在润滑测试中,矿物油减少摩擦,冷却接触表面,并将磨损过程中产生的磨料碎片运输掉。这导致磨损率降低了signiÿcant ~8×10。在不同的环境中耐磨性的这种巨大差异表明了在实际使用条件下进行适当滑动磨损模拟的重要性。
当试验条件发生微小变化时,磨损行为可能发生剧烈变化。Nanovea的摩擦计的多功能性允许在高温、润滑和摩擦腐蚀条件下进行磨损测量。精确的速度和位置控制的先进电机使磨损测试执行的速度从0.001到5000 rpm,使其成为研究/测试实验室的理想工具,以调查磨损在不同的摩擦学条件。
用Nanovea的非接触光学proÿlometer检测样品的表面状况。图5显示了磨损试验后环的表面形貌。为了更好地呈现滑动磨损过程中产生的表面形貌和粗糙度,去掉了圆柱形。Signiÿcant在200转的干磨损试验中,由于三体磨损过程发生了表面粗糙化。干磨损试验后的块体和环体的粗糙度Ra分别为14.1和18.1 μ m,而在较高速度下进行50万转长期润滑磨损试验后的粗糙度Ra分别为5.7和9.1 μ m。该试验证明了活塞环-气缸接触处适当润滑的重要性。严重的磨损会迅速损坏没有润滑的接触面,导致使用质量不可逆的恶化,甚至导致发动机损坏。
结论
在本研究中,我们展示了如何使用 Nanovea 的摩擦计来评估钢金属对的滑动磨损行为,并使用遵循 ASTM G77 标准的环上块模块。润滑剂在材料对的磨损性能中起着至关重要的作用。矿物油可将 H-30 块的磨损率降低约 8×10ˆ 倍,将 COF 降低约 90 倍。 Nanovea 摩擦计的多功能性使其成为测量各种润滑、高温和摩擦腐蚀条件下磨损行为的理想工具。
Nanovea 的摩擦试验机使用符合 ISO 和 ASTM 的旋转和线性模式提供精确且可重复的磨损和摩擦测试,并在一个预集成系统中提供可选的高温磨损、润滑和摩擦腐蚀模块。 Nanovea 无与伦比的系列是确定薄或厚、软或硬涂层、薄膜和基材的全方位摩擦学特性的理想解决方案。
现在,让我们来谈谈你的申请
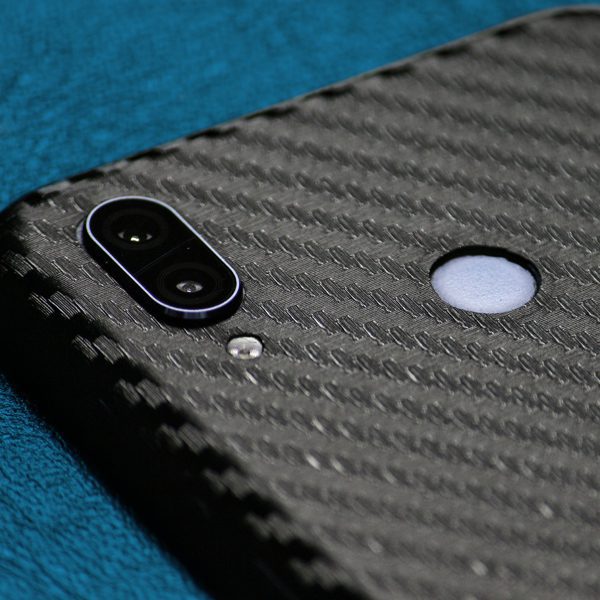
使用三维轮廓测量法的复合材料分析
非接触式轮廓测量法对复合材料的重要性
尽量减少缺陷是至关重要的,这样复合材料在加固应用中才会尽可能的强大。作为一种各向异性的材料,关键是编织方向的一致性,以保持高性能的可预测性。复合材料是强度与重量比最高的材料之一,在某些情况下,它比钢更强。重要的是要限制复合材料的表面暴露面积,以减少化学脆弱性和热膨胀效应。轮廓测量法的表面检测对于复合材料的质量控制生产至关重要,以确保在长期使用中的强大性能。
纳诺维亚的 3D 非接触式轮廓仪 与其他表面测量技术(例如接触式探针或干涉测量法)不同。我们的轮廓仪使用轴向色差来测量几乎任何表面,开放式样品台允许测量任何尺寸的样品,无需准备。在表面轮廓测量过程中获得纳米到宏观测量,样品反射率或吸收的影响为零。我们的轮廓仪可以轻松测量任何材料:透明、不透明、镜面、漫射、抛光和粗糙,具有无需软件操作即可测量高表面角度的先进能力。非接触式轮廓仪技术提供了理想且用户友好的功能,可最大限度地进行复合材料表面研究;以及 2D 和 3D 组合功能的优势。
测量目标
本应用中使用的Nanovea HS2000L轮廓仪测量了两个编织的碳纤维复合材料的表面。表面粗糙度、编织长度、各向同性、分形分析和其他表面参数被用来描述复合材料的特征。测量的区域是随机选择的,并假定足够大,可以使用Nanovea强大的表面分析软件比较属性值。
结果和讨论
表面分析
各向同性显示了编织的方向性,以确定预期的属性值。我们的研究表明,双向复合材料是~60%的各向同性,正如预期。同时,单向复合材料是~13%的各向同性,由于强大的单纤维路径方向纤维。
编织尺寸决定了复合材料中使用的纤维的包装和宽度的一致性。我们的研究表明,我们可以很容易地测量织造尺寸,精确到微米,以确保零件的质量。
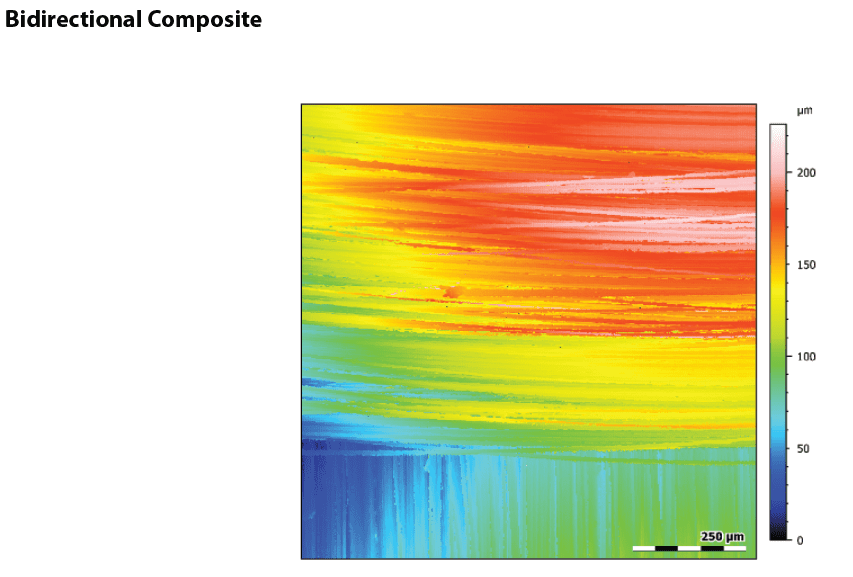
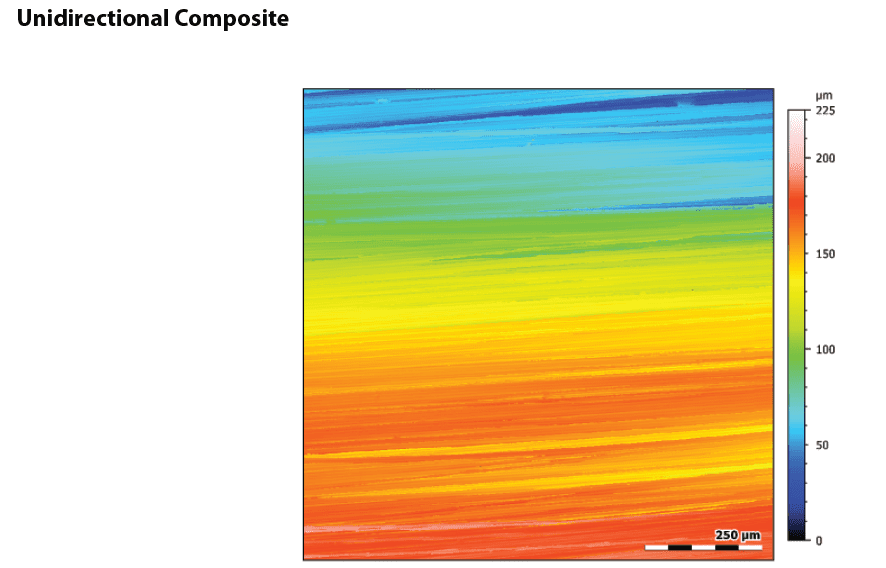
主导波长的纹理分析表明两种复合材料的股线尺寸都是4.27微米厚。纤维表面的分形维度分析决定了光滑度,以寻找纤维在基体中的固定程度。单向纤维的分形尺寸高于双向纤维,这可能影响复合材料的加工。
总结
在这个应用中,我们已经表明Nanovea HS2000L非接触式轮廓仪可以精确地描述复合材料的纤维表面。我们用高度参数、各向同性、纹理分析和距离测量等方法区分了碳纤维的编织类型的差异。
我们的轮廓仪表面测量精确和快速地减轻了复合材料的损坏,这减少了零件的缺陷,最大限度地提高了复合材料的能力。Nanovea的3D轮廓仪速度范围从<1mm/s到500mm/s,适合于研究应用到高速检查的需要。Nanovea的轮廓仪是解决方案
以满足任何复合测量的需要。
现在,让我们来谈谈你的申请

用纳米压痕法评估生物组织硬度
生物组织纳米压痕的重要性
传统的力学测试(硬度、粘附、压缩、穿刺、屈服强度等)在今天的质量控制环境中要求更高的精度和可靠性,包括从组织到脆性材料的各种先进材料。传统的机械仪表无法提供先进材料所需的灵敏负载控制和分辨率。与生物材料相关的挑战要求开发能够对极软材料进行精确负载控制的力学测试。这些材料需要非常低的次mN测试负载和大的深度范围,以确保适当的性能测量。此外,许多不同的机械测试类型可以在一个单一的系统上执行,允许更大的功能。这为生物材料提供了一系列重要的测量,包括硬度、弹性模量、损耗和存储模量、蠕变以及抗划伤性和屈服强度失效点。
测量目标
在本应用中,Nanovea的机械试验机在纳米压痕模式下,研究了一种生物材料替代品在火腿的脂肪、浅肉和暗肉区域上的硬度和弹性模量。
纳米压痕是基于压痕标准ASTM E2546和ISO 14577。它使用既定的方法,将已知几何形状的压头打入测试材料的特定部位,并控制增加法向载荷。当达到预先设定的最大深度时,法向载荷会减少,直到发生完全松弛。负载由压电致动器施加,并在一个受控的循环中用高灵敏度的称重传感器测量。在实验过程中,压头相对于样品表面的位置由一个高精度的电容式传感器监测。由此产生的负载和位移曲线提供了与被测材料的机械性质相关的数据。已建立的模型通过测量数据计算出定量的硬度和模量值。纳米压痕适用于纳米尺度的低负荷和穿透深度测量。
结果和讨论
下表给出了硬度和杨氏模量的实测值,并附有平均值和标准差。由于压痕尺寸小,高表面粗糙度可能导致结果的大变化。
脂肪区的硬度约为肉区的一半。肉类处理使深色的肉区比浅色的肉区更硬。弹性模量和硬度与脂肪和肉区的口感咀嚼度有直接关系。60秒后,脂肪和浅色肉区的蠕动继续率高于深色肉区。
详细结果-脂肪
详细结果-浅色肉
详细结果-深色肉
总结
在此应用中,Nanovea 的 机械测试器 在纳米压痕模式下,可以可靠地确定脂肪和肉类区域的机械特性,同时克服样品表面粗糙度较高的问题。这证明了 Nanovea 机械测试仪的广泛且无与伦比的功能。该系统同时对极硬的材料和软的生物组织提供精确的机械性能测量。
与压电台闭环控制的负载传感器确保了对1至5kPa的硬或软凝胶材料的精确测量。使用同一系统,可以在更高的负荷下测试生物材料,最高可达400N。多周期加载可用于疲劳测试,使用平坦的圆柱形金刚石尖端可获得每个区域的屈服强度信息。此外,通过动态机械分析(DMA),利用闭环载荷控制,可以高精度地评估粘弹性能损失和储存模量。在同一系统上还可以进行各种温度和液体下的测试。
Nanovea的机械测试仪继续是生物和软聚合物/凝胶应用的最佳测试仪器。
现在,让我们来谈谈你的申请
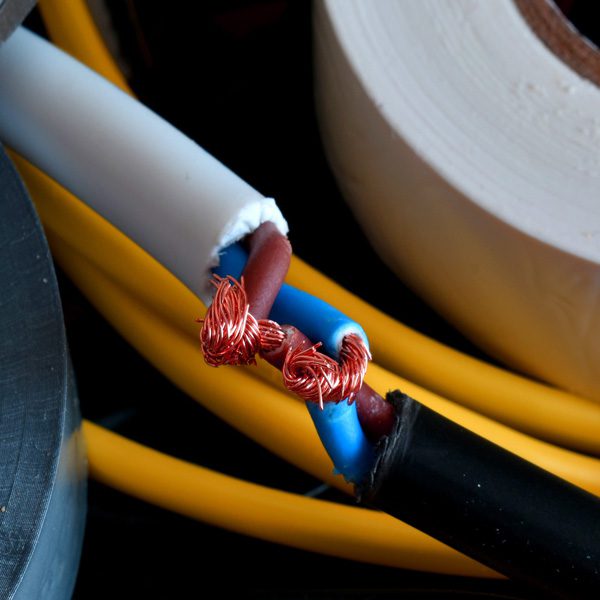
表面处理过的铜线的磨损和划痕评估
铜线的磨损和划痕评估的重要性
自电磁铁和电报发明以来,铜在电线方面的应用有着悠久的历史。由于铜的耐腐蚀性、可焊性以及在高达150℃的高温下的性能,铜线被广泛用于电子设备,如面板、仪表、计算机、商业机器和电器。所有开采出来的铜大约有一半是用来制造电线和电缆导体的。
铜线的表面质量对应用服务性能和使用寿命至关重要。铜线中的微观缺陷可能导致过度磨损、裂纹的产生和扩展、导电性下降和焊接性不足。适当的铜线表面处理可以消除拉丝过程中产生的表面缺陷,提高耐腐蚀、耐刮擦和耐磨性。许多使用铜线的航空应用需要控制行为以防止意外的设备故障。为了正确评估铜线表面的耐磨性和耐刮擦性,需要进行可量化和可靠的测量。
测量目标
在这个应用中,我们模拟了不同铜线表面处理的受控磨损过程。 划痕测试 测量导致处理过的表面层失效所需的负载。这项研究展示了 Nanovea 摩擦仪 和 机械测试仪 作为电线评估和质量控制的理想工具。
测试过程和程序
通过 Nanovea 摩擦磨损试验机使用线性往复磨损模块评估两种不同表面处理的铜线(线 A 和线 B)的摩擦系数 (COF) 和耐磨性。 Al2O3 球(直径 6 毫米)是本应用中使用的计数器材料。使用 Nanovea 的磨损轨迹进行检查 3D非接触式轮廓仪。测试参数总结于表 1 中。
本次研究以Al₂O₃球为例进行了说明。任何具有不同形状和表面光洁度的固体材料都可以使用定制夹具来模拟实际的应用情况。
结果和讨论
铜线的磨损。
图2显示了铜线在磨损测试中的COF变化。A线在整个磨损试验过程中显示出稳定的COF约为0.4,而B线在头100转时显示出约0.35的COF,并逐渐增加到约0.4。
图3比较了测试后铜线的磨损轨迹。Nanovea公司的3D非接触式轮廓仪对磨损痕迹的详细形貌进行了出色的分析。通过提供对磨损机理的基本理解,可以直接和准确地确定磨损轨迹体积。经过600转的磨损试验,B线表面有明显的磨损痕迹损伤。剖面仪3D视图显示,B线的表面处理层被完全去除,大大加快了磨损过程。这在铜基板暴露的B线上留下了平坦的磨损痕迹。这可能导致使用B线的电气设备的寿命显著缩短。相比之下,A线的磨损相对较轻,其表面的磨损痕迹较浅。在相同条件下,A线表面处理层不像B线表面处理层那样被去除。
铜线表面的耐刮擦性。
图4显示了测试后导线上的划痕。线材A的保护层表现出非常好的抗划痕能力。相比之下,B线的保护层在约1.0N的载荷下失效。这些线的耐刮擦性有如此大的差异,这有助于它们的磨损性能,其中A线拥有大大增强的耐磨性。图5所示的划痕测试中法向力、COF和深度的演变提供了关于测试中涂层失效的更多信息。
总结
在这项对照研究中,我们展示了Nanovea的摩擦仪对表面处理过的铜线的耐磨性进行定量评估,以及Nanovea的机械测试仪对铜线的耐刮擦性进行可靠评估。铜线的表面处理在其使用寿命中对三者的机械性能起着关键作用。电线A的适当表面处理大大增强了耐磨性和耐刮擦性,这对粗糙环境中的电线的性能和寿命至关重要。
Nanovea的摩擦仪使用符合ISO和ASTM标准的旋转和线性模式,提供精确和可重复的磨损和摩擦测试,在一个预集成的系统中可以选择高温磨损、润滑和三相腐蚀模块。Nanovea无与伦比的范围是确定薄或厚、软或硬的涂层、薄膜和基材的全部摩擦学特性的理想解决方案。
现在,让我们来谈谈你的申请
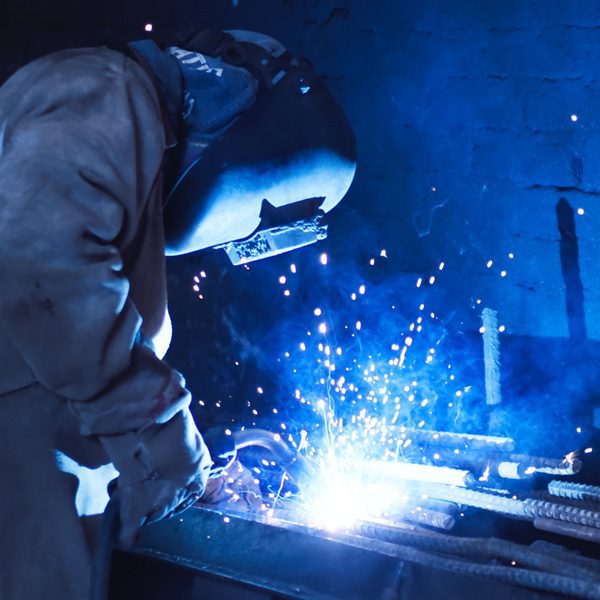
钢和铝的屈服强度和拉伸强度
使用压痕测量屈服强度和极限拉伸强度的重要性
传统上,屈服强度和极限拉伸强度的测试是使用大型拉伸试验机,需要巨大的力量来拉开测试样品。为一种材料适当地加工许多测试券,而每个样品只能测试一次,这既费钱又费时。样品中的小缺陷会在测试结果中产生明显的差异。市场上不同配置和排列的拉伸试验机往往导致测试力学和结果的巨大差异。
测量目标
在这个应用中,Nanovea 机械测试仪 测量不锈钢 SS304 和铝 Al6061 金属合金样品的屈服强度和极限拉伸强度。选择样品是因为其普遍认可的屈服强度和极限拉伸强度值,显示了 Nanovea 压痕方法的可靠性。
测试过程和程序
屈服强度和极限拉伸强度测试是在Nanovea机械测试仪上进行的。 显微压痕 模式。一个直径为200μm的圆柱形扁平金刚石尖端被用于这一应用。SS304和Al6061合金因其广泛的工业应用和公认的屈服强度和极限拉伸强度值而被选中,以显示压痕方法的巨大潜力和可靠性。在测试前,样品被机械地打磨成镜面状,以避免表面粗糙或缺陷对测试结果的影响。测试条件列于表1。每个样品都进行了十次以上的测试,以确保测试值的可重复性。
结果和讨论
SS304和Al6061合金样品的载荷-位移曲线显示在图3中,测试样品上的平面压头印记被插入。使用Nanovea开发的特殊算法分析 "S "形加载曲线,计算屈服强度和极限拉伸强度。数值是由软件自动计算的,如表1所示。通过传统的拉伸试验获得的屈服强度和极限拉伸强度值被列出来进行比较。
总结
在这项研究中,我们展示了 Nanovea Mechanical Tester 评估不锈钢和铝合金板材样品的屈服强度和极限拉伸强度的能力。简单的实验设置显着减少了拉伸测试所需的样品制备时间和成本。小压痕尺寸使得可以对一个样品进行多次测量。该方法允许对小样本和局部区域进行YS/UTS测量,为YS/UTS测绘和管道或汽车结构的局部缺陷检测提供解决方案。
Nanovea 机械测试仪的纳米、微观或宏观模块均包括符合 ISO 和 ASTM 的压痕、划痕和磨损测试仪模式,可在单个系统中提供最广泛、最用户友好的测试范围。 Nanovea 无与伦比的系列是测定薄或厚、软或硬涂层、薄膜和基材的全方位机械性能的理想解决方案,包括硬度、杨氏模量、断裂韧性、附着力、耐磨性等。此外,除了粗糙度等其他表面测量之外,可选的 3D 非接触式轮廓仪和 AFM 模块还可用于压痕、划痕和磨损轨迹的高分辨率 3D 成像。
现在,让我们来谈谈你的申请
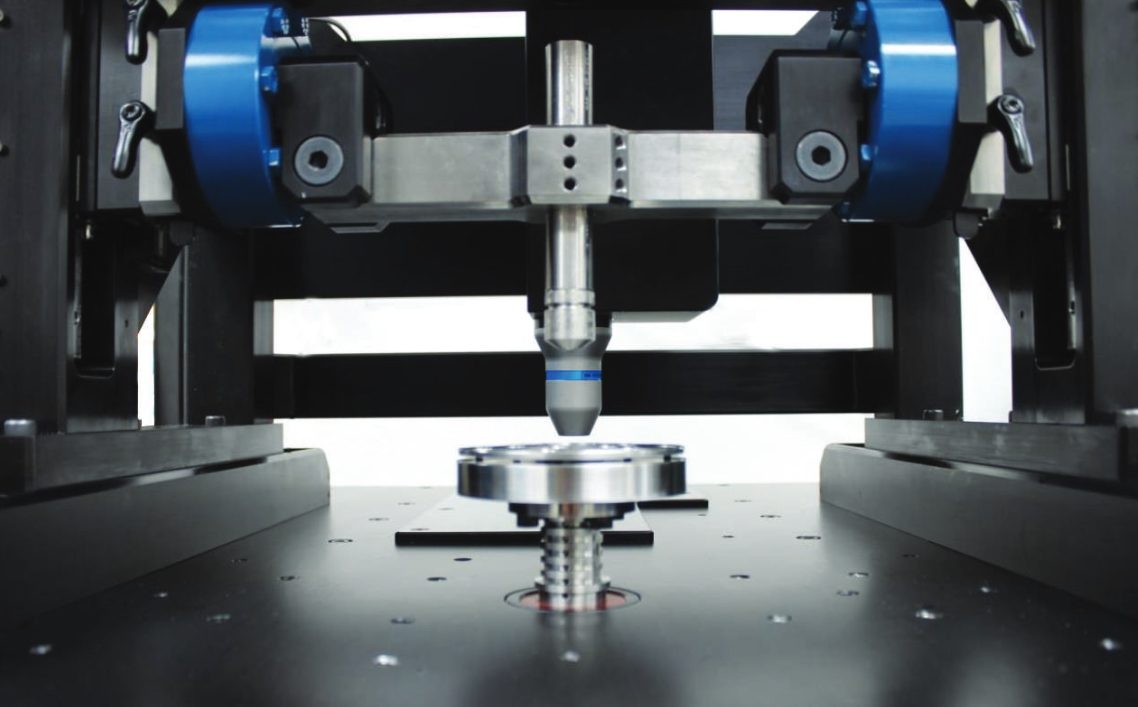
动态负载摩擦学
动态负载摩擦学
简介
磨损几乎发生在每一个工业部门,并造成了约0.75%的GDP成本1。摩擦学研究对于提高生产效率、应用性能以及保护材料、能源和环境至关重要。在广泛的摩擦学应用中,振动和振荡不可避免地发生。过度的外部振动加速了磨损过程,降低了服务性能,导致机械部件出现灾难性的故障。
传统的死荷载摩擦仪通过质量砝码施加正常载荷。这样的加载技术不仅将加载选项限制在一个恒定的负载上,而且在高负载和高速度下产生强烈的不可控振动,导致磨损行为评估的局限性和不一致性。可靠地评估受控振荡对材料磨损行为的影响,对于不同工业应用中的研发和质量控制是可取的。
Nanovea 突破性的高负载 摩擦仪 具有动态负载控制系统,最大负载能力为 2000 N。先进的气动压缩空气加载系统使用户能够评估材料在高正常载荷下的摩擦学行为,并具有抑制磨损过程中产生的不良振动的优点。因此,可以直接测量负载,无需旧设计中使用的缓冲弹簧。并联电磁体振荡加载模块可施加良好控制的振荡,所需振幅高达 20 N,频率高达 150 Hz。
摩擦力是直接根据施加到上支架的侧向力进行高精度测量的。现场监测位移,从而深入了解测试样品磨损行为的演变。受控振荡载荷下的磨损测试还可以在腐蚀、高温、潮湿和润滑环境中进行,以模拟摩擦学应用的真实工作条件。集成高速 非接触式轮廓仪 在几秒钟内自动测量磨损轨迹形态和磨损量。
测量目标
在这项研究中,我们展示了Nanovea T2000动态负载摩擦仪在研究不同涂层和金属样品在受控振荡负载条件下的摩擦学行为的能力。
测试程序
通过Nanovea T2000摩擦仪和传统的死负荷摩擦仪,按照ASTM G992的规定,使用销轴在盘上的设置,评估和比较了300微米厚的耐磨涂层的摩擦学行为,例如摩擦系数,COF和耐磨性。
通过 Nanovea T2000 摩擦试验机的动态负载摩擦学模式,对受控振荡下的 6 mm Al203 球的单独 Cu 和 TiN 涂层样品进行了评估。
测试参数汇总于表1。
集成的三维轮廓仪配备了线传感器,在测试后自动扫描磨损轨迹,在几秒钟内提供最准确的磨损量测量。
结果和讨论
气动负载系统与死负载系统
使用Nanovea T2000摩擦仪对耐磨涂层的摩擦学行为与传统的死负荷(DL)摩擦仪进行了比较。图2显示了涂层COF的变化。我们观察到涂层在磨损测试中表现出了相当的COF值~0.6。然而,图3中不同位置的20个横截面图表明,在死负荷系统下,涂层经历了更严重的磨损。
在高负荷和高速度下,死负载系统的磨损过程产生了强烈的振动。接触面的巨大集中压力与高滑动速度相结合,产生大量的重量和结构振动,导致加速磨损。传统的死负荷摩擦仪使用质量砝码来施加负荷。这种方法在较低的接触载荷和温和的磨损条件下是可靠的;然而,在较高的载荷和速度的侵蚀性磨损条件下,显著的振动导致砝码反复弹跳,造成不均匀的磨损轨迹,导致不可靠的摩擦学评估。计算出的磨损率为8.0±2.4 x 10-4 mm3/N m,显示出高磨损率和大的标准偏差。
Nanovea T2000摩擦仪设计有一个动态控制负载系统,以抑制振荡。它用压缩空气施加正常载荷,最大限度地减少了磨损过程中产生的不必要的振动。此外,主动闭环加载控制确保在整个磨损测试过程中施加恒定的载荷,测针跟随磨损轨迹的深度变化。如图3a所示,测得的磨损轨迹轮廓明显更加一致,从而使磨损率低至3.4±0.5 x 10-4 mm3/N m。
图4所示的磨损轨迹分析证实了Nanovea T2000摩擦仪的气动压缩空气加载系统进行的磨损测试,与传统的死负荷摩擦仪相比,产生了更平滑、更一致的磨损轨迹。此外,Nanovea T2000摩擦仪在磨损过程中测量测针位移,进一步了解现场磨损行为的进展。
铜样品磨损的可控振荡
Nanovea T2000摩擦仪的平行振荡加载电磁铁模块使用户能够研究控制振幅和频率振荡对材料磨损行为的影响。如图6所示,Cu样品的COF被就地记录。在第一次330转的测量中,铜样品表现出恒定的COF~0.3,标志着在界面上形成了稳定的接触和相对平滑的磨损轨迹。随着磨损试验的继续,COF的变化表明磨损机制的变化。相比之下,在50N的振幅控制下的磨损试验表现出不同的磨损行为:COF在磨损过程开始时迅速增加,并在整个磨损试验中表现出明显的变化。COF的这种行为表明,在正常载荷中施加的振荡在接触处的不稳定滑动状态中起了作用。
图7比较了由集成非接触式光学轮廓仪测量的磨损轨迹形态。可以看出,在控制振荡幅度为5N的情况下,Cu样品表现出更大的磨损轨迹,体积为1.35 x 109 µm3,而在没有施加振荡的情况下,体积为5.03 x 108 µm3。受控振荡使磨损率明显加快了约2.7倍,显示了振荡对磨损行为的关键影响。
受控振荡对TiN涂层磨损的影响
图8中显示了TiN涂层样品的COF和磨损轨迹。从测试期间COF的演变来看,TiN涂层在振荡下表现出明显不同的磨损行为。在磨损试验开始时的磨合期后,TiN涂层显示出约0.3的恒定COF,这是由于TiN涂层和亚铝₃球之间界面的稳定滑动接触。然而,当TiN涂层开始失效时,氧化铝球穿透涂层并与下面的新钢基体滑动。同时在磨损轨道上产生大量坚硬的TiN涂层碎片,将稳定的双体滑动磨损变为三体磨损。材料耦合特性的这种变化导致了COF演化过程中的变化增加。强加的5N和10N振荡加速了TiN涂层的失效,从~400转到100转以下。在控制振荡下的磨损试验后,TiN涂层样品上较大的磨损痕迹与COF的这种变化是一致的。
Nanovea T2000摩擦磨损仪的先进气动加载系统与传统的死负载系统相比,拥有作为自然快速减震器的内在优势。与使用伺服电机和弹簧组合来施加负载的负载控制系统相比,气动系统的这种技术优势是真实的。正如本研究中所展示的那样,该技术确保了在高负荷下可靠和更好的控制磨损评估。此外,主动闭环加载系统可以在磨损测试期间将正常载荷改变为所需值,以模拟在制动系统中看到的实际应用。
我们已经表明,Nanovea T2000动态负载摩擦仪使用户能够定量评估材料在不同控制振荡条件下的摩擦学行为,而不是在测试过程中受到不受控制的振动条件的影响。振动在金属和陶瓷涂层样品的磨损行为中起着重要作用。
平行电磁铁振荡加载模块以设定的振幅和频率提供精确控制的振荡,使用户能够模拟现实生活条件下的磨损过程,而环境振动往往是一个重要因素。在磨损过程中存在强加的振荡,铜和TiN涂层样品的磨损率都大大增加。原地测量的摩擦系数和测针位移的变化是摩擦学应用中材料性能的重要指标。集成的三维非接触式轮廓仪提供了一种工具,可以在几秒钟内精确测量磨损量并分析磨损痕迹的详细形态,为从根本上了解磨损机制提供更多的见解。
T2000配备了一个自调谐、高质量和高扭矩的电机,有一个20位的内部速度和一个16位的外部位置编码器。它使摩擦仪能够提供一个无与伦比的转速范围,从0.01到5000rpm,可以以阶梯式跳跃或连续的速度变化。与使用底部扭矩传感器的系统相反,Nanovea摩擦仪使用顶部的高精度称重传感器来准确和单独测量摩擦力。
Nanovea摩擦仪提供精确和可重复的磨损和摩擦测试,使用符合ISO和ASTM标准的旋转和线性模式(包括4球、止推垫圈和环上块状测试),在一个预集成的系统中可选择高温磨损、润滑和三相腐蚀模块。Nanovea T2000无与伦比的范围是确定薄或厚、软或硬的涂层、薄膜和基材的全部摩擦学特性的理想解决方案。
现在,让我们来谈谈你的申请
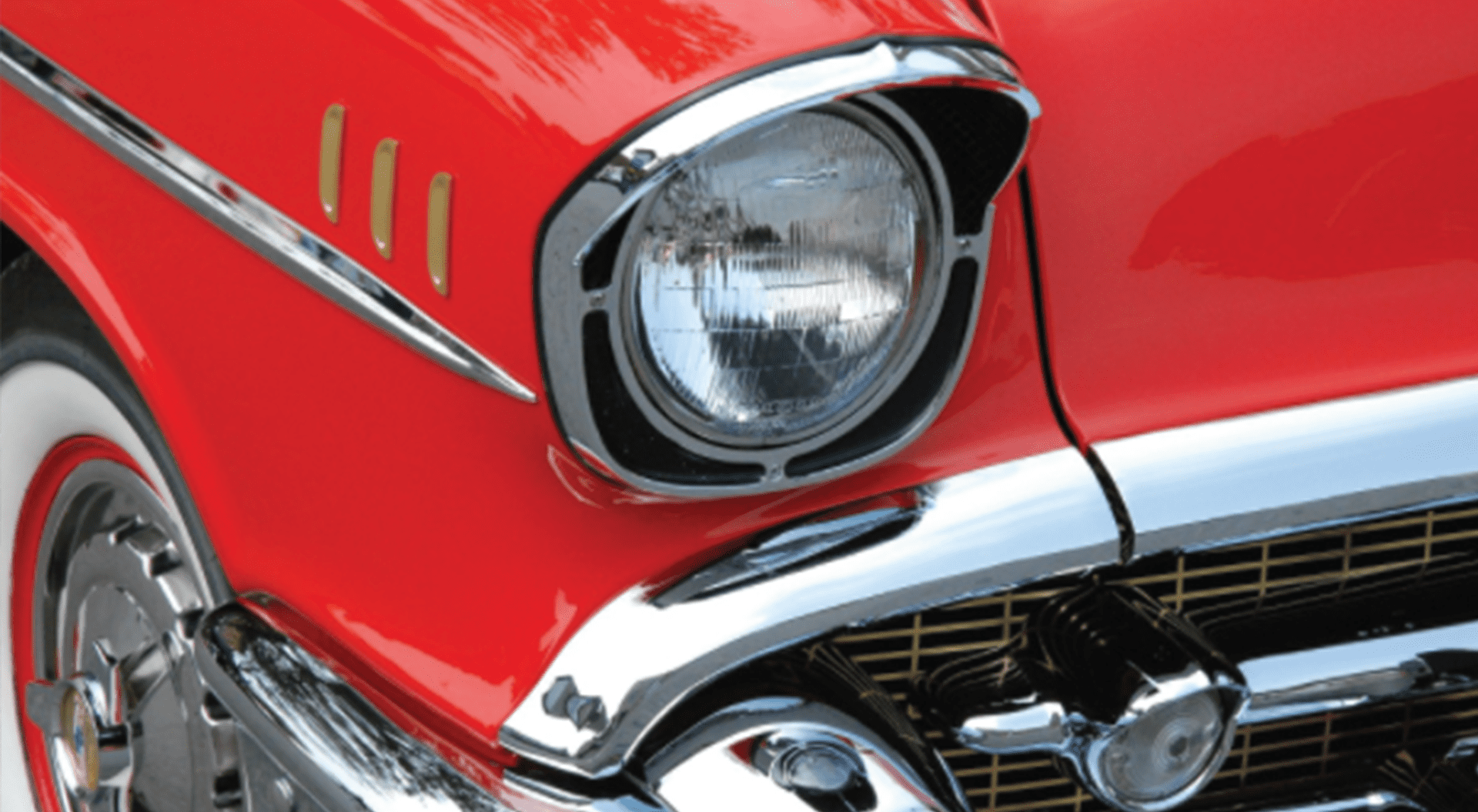
使用三维轮廓测量法的油漆橙皮纹理分析
使用三维轮廓测量法的油漆橙皮纹理分析
简介
基材上表面结构的大小和频率会影响到光泽涂料的质量。涂料桔皮纹理,以其外观命名,可以从基材影响和涂料应用技术中发展。纹理问题通常以波浪形、波长和对光泽涂层的视觉效果来量化。最小的纹理会导致光泽度下降,而较大的纹理则会在涂层表面产生可见的波纹。了解这些纹理的发展及其与基材和技术的关系是质量控制的关键。
轮廓测量法对于纹理测量的重要性
与用于测量光泽纹理的传统二维仪器不同,三维非接触式测量可快速提供用于了解表面特征的三维图像,并可快速调查感兴趣的区域。如果没有速度和三维审查,质量控制环境将完全依赖于二维信息,对整个表面的可预测性很低。了解三维纹理可以选择最佳的加工和控制措施。确保此类参数的质量控制在很大程度上依赖于可量化、可重现和可靠的检测。Nanovea三维非接触式 轮廓仪 Nanovea轮廓仪采用色度共焦技术,具有测量快速测量过程中发现的陡峭角度的独特能力。由于探头接触、表面变化、角度或反射率等原因,其他技术无法提供可靠数据,而Nanovea轮廓仪却能成功解决这些问题。
测量目标
在这个应用中,Nanovea HS2000L测量了亮光油漆的橙皮纹理。有无穷无尽的表面参数从三维表面扫描中自动计算出来。在这里,我们通过量化油漆橙皮纹理的特征来分析扫描的3D表面。
Nanovea HS2000L量化了橙皮漆的各向同性和高度参数。桔子皮纹理以94.4%的各向异性量化了随机图案方向。高度参数以24.84µm的高度差来量化纹理。
图4中的承载率曲线是深度分布的图形化表示。这是软件内的一个互动功能,允许用户查看不同深度的分布和百分比。图5中提取的剖面图给出了橙皮纹理的有用粗糙度值。144微米阈值以上的提取峰值显示了橘子皮的纹理。这些参数很容易调整为其他区域或感兴趣的参数。
总结
在这个应用中,Nanovea HS2000L 3D非接触轮廓仪精确地表征了光泽涂层上的橘皮纹理的地形和纳米细节。通过许多有用的测量(尺寸、粗糙度、表面纹理、形状形状、平面度、翘曲平面度、体积面积、阶跃高度等),可以快速识别和分析3D表面测量中感兴趣的区域。快速选择的二维截面提供了一套完整的表面测量资源的光泽纹理。特殊领域的兴趣可以进一步分析与集成AFM模块。Nanovea 3D轮廓仪的速度范围从<1毫米/秒到500毫米/秒,适用于研究应用,以满足高速检测的需要。Nanovea 3D轮廓仪有广泛的配置,以适合您的应用程序。
现在,让我们来谈谈你的申请
分类
- 应用说明
- 环形摩擦学座谈会
- 腐蚀摩擦学
- 摩擦测试|摩擦系数
- 高温机械测试
- 高温摩擦学
- 湿度和气体 摩擦学
- 湿度的机械测试
- 压痕|蠕变和松弛
- 压痕|断裂韧性
- 压痕 | 硬度和弹性
- 压痕|损失和储存
- 压痕 | 应力与应变
- 压痕|屈服强度和疲劳
- 实验室测试
- 线性摩擦学
- 液体机械测试
- 液体摩擦学
- 低温摩擦学
- 机械测试
- 新闻发布
- 轮廓测量 - 平面度和翘曲度
- 轮廓测量法 | 几何和形状
- 轮廓测量 - 粗糙度和光洁度
- 轮廓测量法|台阶高度和厚度
- 轮廓测量法 | 纹理和颗粒
- 轮廓测量法|体积和面积
- 轮廓仪测试
- 环对环摩擦学
- 旋转摩擦学
- 刮擦测试|胶粘剂失效
- 刮擦测试 | 粘着性失效
- 刮擦测试 | 多次磨损
- 划痕测试|划痕硬度
- 划痕测试 摩擦学
- 贸易展销会
- 摩擦学测试
- 未分类
归档
- 2023年9月
- 2023年8月
- 2023年6月
- 2023年5月
- 2022年7月
- 2022年5月
- 2022年4月
- 2022年1月
- 2021年12月
- 2021年11月
- 2021年10月
- 2021年9月
- 2021年8月
- 2021年7月
- 2021年6月
- 2021年5月
- 2021年3月
- 2021年2月
- 2020年12月
- 2020年11月
- 2020年10月
- 2020年9月
- 2020年7月
- 2020年5月
- 2020年4月
- 2020年3月
- 2020年2月
- 2020年1月
- 2019年11月
- 2019年10月
- 2019年9月
- 2019年8月
- 2019年7月
- 2019年6月
- 2019年5月
- 2019年4月
- 2019年3月
- 2019年1月
- 2018年12月
- 2018年11月
- 2018年10月
- 2018年9月
- 2018年7月
- 2018年6月
- 2018年5月
- 2018年4月
- 2018年3月
- 2018年2月
- 2017年11月
- 2017年10月
- 2017年9月
- 2017年8月
- 2017年6月
- 2017年5月
- 2017年4月
- 2017年3月
- 2017年2月
- 2017年1月
- 2016年11月
- 2016年10月
- 2016年8月
- 2016年7月
- 2016年6月
- 2016年5月
- 2016年4月
- 2016年3月
- 2016年2月
- 2016年1月
- 2015年12月
- 2015年11月
- 2015年10月
- 2015年9月
- 2015年8月
- 2015年7月
- 2015年6月
- 2015年5月
- 2015年4月
- 2015年3月
- 2015年2月
- 2015年1月
- 2014年11月
- 2014年10月
- 2014年9月
- 2014年8月
- 2014年7月
- 2014年6月
- 2014年5月
- 2014年4月
- 2014年3月
- 2014年2月
- 2014年1月
- 2013年12月
- 2013年11月
- 2013年10月
- 2013年9月
- 2013年8月
- 2013年7月
- 2013年6月
- 2013年5月
- 2013年4月
- 2013年3月
- 2013年2月
- 2013年1月
- 2012年12月
- 2012年11月
- 2012年10月
- 2012年9月
- 2012年8月
- 2012年7月
- 2012年6月
- 2012年5月
- 2012年4月
- 2012年3月
- 2012年2月
- 2012年1月
- 2011年12月
- 2011年11月
- 2011年10月
- 2011年9月
- 2011年8月
- 2011年7月
- 2011年6月
- 2011年5月
- 2010年11月
- 2010年1月
- 2009年4月
- 2009年3月
- 2009年1月
- 2008年12月
- 2008年10月
- 2007年8月
- 2006年7月
- 2006年3月
- 2005年1月
- 2004年4月