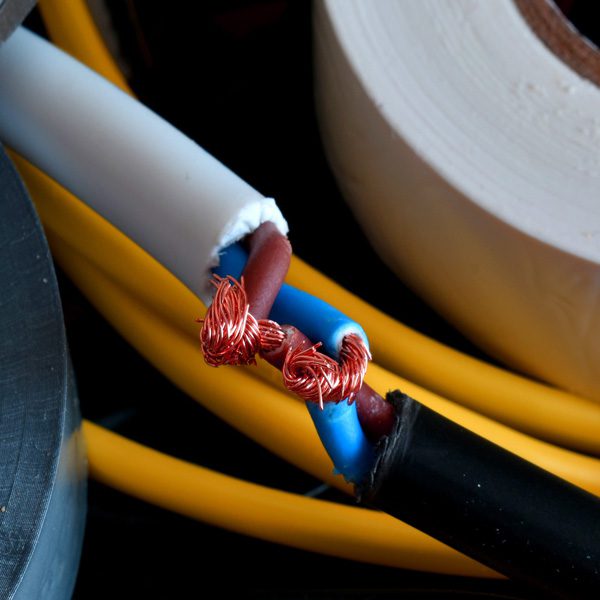
表面処理銅線の耐摩耗性とスクラッチ性の評価
銅線の摩耗・傷評価の重要性
銅は、電磁石や電信機の発明以来、電気配線に使用されてきた長い歴史があります。銅線は、耐食性、はんだ付け性、150℃までの高温での特性から、パネル、メーター、コンピューター、事務機、家電製品など、幅広い電子機器に使用されています。採掘される銅の約半分は、電線・ケーブルの導体製造に使用されています。
銅線の表面品質は、アプリケーションの性能と寿命にとって非常に重要です。ワイヤの微細な欠陥は、過度の摩耗、亀裂の発生と伝播、導電性の低下、不十分なはんだ付け性などにつながる可能性があります。銅線の適切な表面処理は伸線時に発生する表面欠陥を取り除き、耐腐食性、耐傷性、耐摩耗性を向上させます。銅線を使った多くの航空宇宙用途では、予期せぬ機器の故障を防ぐため、その挙動を制御する必要がありま す。銅線表面の耐摩耗性や耐傷性を正しく評価するためには、定量的で信頼性の高い測定が必要です。
測定目的
このアプリケーションでは、異なる銅線の表面処理を制御した摩耗プロセスをシミュレートしています。 スクラッチテスト 処理された表面層に破損を引き起こすのに必要な荷重を測定します。この研究では Nanovea を紹介します トライボメータ と メカニカルテスター 電線の評価・品質管理に最適なツールです。
試験方法と手順
銅線 (ワイヤ A およびワイヤ B) の 2 つの異なる表面処理の摩擦係数 (COF) と耐摩耗性は、線形往復摩耗モジュールを使用する Nanovea トライボメータによって評価されました。 Al₂O₃ ボール (直径 6 mm) が、この用途で使用される相手材です。 Nanovea の摩耗痕跡を調査しました。 3D非接触表面形状計。テストパラメータを表 1 にまとめます。
本研究では、カウンター材料として滑らかなAl₂O₃球を例として使用した。形状や表面仕上げが異なる任意の固体材料は、実際の適用状況をシミュレートするために、カスタムフィクスチャを使用して適用することができます。
結果および考察
銅線の磨耗。
図 2 は,摩耗試験中の銅線の COF の変化を示している。A線は摩耗試験中、COFが〜0.4と安定しているのに対し、B線は最初の100回転でCOFが〜0.35となり、徐々に〜0.4まで増加した。
図3は、試験後の銅線の摩耗痕を比較したものです。ナノベアの3D非接触プロフィロメータは、摩耗痕の詳細な形態について優れた分析を提供しました。摩耗のメカニズムを根本的に理解することで、摩耗痕の体積を直接かつ正確に把握することができます。ワイヤーBの表面は、600回転の摩耗試験後に摩耗痕が顕著に損傷しています。プロフィロメーターの3D表示では、ワイヤーBの表面処理層が完全に除去され、摩耗プロセスが大幅に加速されたことが分かります。このため、ワイヤーBの銅基板が露出している部分には、平坦な摩耗痕が残っています。この結果、ワイヤBを使用する電気機器の寿命が著しく短くなる可能性があります。一方、ワイヤーAは比較的摩耗が少なく、浅い摩耗痕が残っています。また,ワイヤAの表面処理層は,ワイヤBの表面処理層のように同じ条件下で剥離することはなかった。
銅線表面の傷つきにくさ。
図4は、試験後のワイヤのスクラッチ痕を示したものである。ワイヤーAの保護層は非常に優れた耐傷性を示し、〜12.6Nの荷重で剥離した。これに対し、ワイヤBの保護層は荷重~1.0Nで剥離した。このようにワイヤの耐傷性に大きな差があることから、ワイヤAは耐摩耗性が大幅に向上していることがわかる。図5に示すように、スクラッチ試験中の法線力、COF、深さの変化から、試験中の皮膜破壊についてより深く理解することができる。
結論
この対照研究では、表面処理された銅線の耐摩耗性を定量的に評価するナノベア社のトライボメータと、銅線の耐傷性を確実に評価するナノベア社のメカニカルテスターを紹介しました。ワイヤの表面処理は、その寿命期間中のトライボメカニカル特性に重要な役割を果たします。ワイヤーAの適切な表面処理により、耐摩耗性と耐傷性が大幅に向上し、過酷な環境下での電線の性能と寿命に重要な役割を果たしました。
ナノベアのトライボメータは、ISOおよびASTMに準拠した回転モードとリニアモードによる精密で再現性の高い摩耗・摩擦試験と、オプションの高温摩耗、潤滑、トライボ腐食モジュールを1つの統合済みシステムで利用することができます。ナノベアの比類なき製品群は、薄型・厚型、軟質・硬質コーティング、フィルム、基材のあらゆるトライボロジー特性を測定するための理想的なソリューションです。
さて、次はアプリケーションについてです。
カテゴリー
- アプリケーションノート
- ブロック・オン・リングトライボロジー
- 腐食トライボロジー
- 摩擦試験|摩擦係数
- 高温機械試験
- 高温トライボロジー
- 湿度・ガス トライボロジー
- 湿度機械試験
- 圧痕|クリープとリラクゼーション
- 圧痕|破壊靭性
- 圧痕|硬度・弾性率
- 圧痕|紛失と保管
- 圧痕|応力と歪み
- 圧痕|降伏強度と疲労の関係
- ラボラトリーテスト
- リニアトライボロジー
- 液体機械試験
- 液状トライボロジー
- 低温トライボロジー
- メカニカルテスト
- プレスリリース
- プロフィロメトリー|平坦度・反り率
- プロフィロメトリー|幾何学と形状
- プロフィロメトリー|粗さと仕上がり
- プロフィロメトリー|段差の高さと厚み
- プロフィロメトリー|テクスチャーとグレーン
- プロフィロメトリー|体積・面積
- プロフィロメトリーテスト
- リング・オン・リング トライボロジー
- 回転トライボロジー
- スクラッチテスト|接着剤の不具合について
- スクラッチテスト|コヒーシブフェール
- スクラッチテスト|マルチパス摩耗
- スクラッチテスト|スクラッチハードネス
- スクラッチテスト トライボロジー
- トレードショー
- トライボロジー試験
- 未分類
月別アーカイブ
- 2022年7月
- 2022年7月
- 2022年7月
- 2022年7月
- 2022年7月
- 2022年7月
- 2022年7月
- 2022年7月
- 2022年7月
- 2022年7月
- 2022年7月
- 2022年7月
- 2022年7月
- 2022年7月
- 2022年7月
- 2022年7月
- 2022年7月
- 2022年7月
- 2022年7月
- 2022年7月
- 2022年7月
- 2022年7月
- 2022年7月
- 2022年7月
- 2022年7月
- 2022年7月
- 2022年7月
- 2022年7月
- 2022年7月
- 2022年7月
- 2022年7月
- 2022年7月
- 2022年7月
- 2022年7月
- 2022年7月
- 2022年7月
- 2022年7月
- 2022年7月
- 2022年7月
- 2022年7月
- 2022年7月
- 2022年7月
- 2022年7月
- 2022年7月
- 2022年7月
- 2022年7月
- 2022年7月
- 2022年7月
- 2022年7月
- 2022年7月
- 2022年7月
- 2022年7月
- 2022年7月
- 2022年7月
- 2022年7月
- 2022年7月
- 2022年7月
- 2022年7月
- 2022年7月
- 2022年7月
- 2022年7月
- 2022年7月
- 2022年7月
- 2022年7月
- 2022年7月
- 2022年7月
- 2022年7月
- 2022年7月
- 2022年7月
- 2022年7月
- 2022年7月
- 2022年7月
- 2022年7月
- 2022年7月
- 2022年7月
- 2022年7月
- 2022年7月
- 2022年7月
- 2022年7月
- 2022年7月
- 2022年7月
- 2022年7月
- 2022年7月
- 2022年7月
- 2022年7月
- 2022年7月
- 2022年7月
- 2022年7月
- 2022年7月
- 2022年7月
- 2022年7月
- 2022年7月
- 2022年7月
- 2022年7月
- 2022年7月
- 2022年7月
- 2022年7月
- 2022年7月
- 2022年7月
- 2022年7月
- 2022年7月
- 2022年7月
- 2022年7月
- 2022年7月
- 2022年7月
- 2022年7月
- 2022年7月
- 2022年7月
- 2022年7月
- 2022年7月
- 2022年7月
- 2022年7月
- 2022年7月
- 2022年7月
- 2022年7月
- 2022年7月
- 2022年7月
- 2022年7月
- 2022年7月
- 2022年7月
- 2022年7月
- 2022年7月
- 2022年7月
- 2022年7月
- 2022年7月
- 2022年7月
- 2022年7月
- 2022年7月
- 2022年7月
- 2022年7月
- 2022年7月
- 2022年7月
- 2022年7月
- 2022年7月
- 2022年7月