はじめに
ディーゼルエンジンの燃料に含まれる全エネルギーのうち、摩擦損失は約10%を占める[1].摩擦損失の40-55%はパワーシリンダーシステムから生じている。この摩擦によるエネルギー損失は、パワーシリンダーシステムで発生するトライボロジー的相互作用をより良く理解することで減少させることができる。
パワーシリンダシステムにおける摩擦損失の大部分は、ピストンスカートとシリンダライナの接触に起因している。実際のエンジンでは、力、温度、速度が常に変化しているため、ピストンスカート、潤滑油、シリンダー界面の相互作用は非常に複雑です。最適なエンジン性能を得るためには、各要因を最適化することが重要です。本研究では、ピストンスカート-潤滑油-シリンダーライナー(P-L-C)界面における摩擦力と摩耗を引き起こすメカニズムを再現することに焦点を当てます。
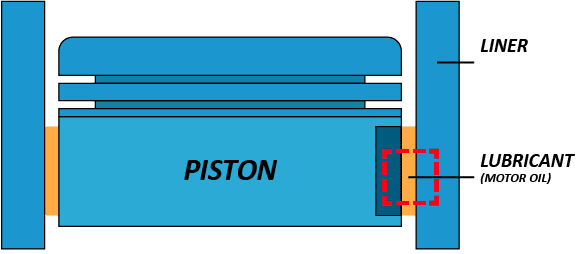
パワーシリンダーシステムとピストンスカート-潤滑剤-シリンダーライナーの界面の概略図。
[1] Bai, Dongfang.内燃機関のピストンスカート潤滑のモデリング。Diss.MIT, 2012