岩石摩擦学
岩石摩擦学
使用 NANOVEA 摩擦计
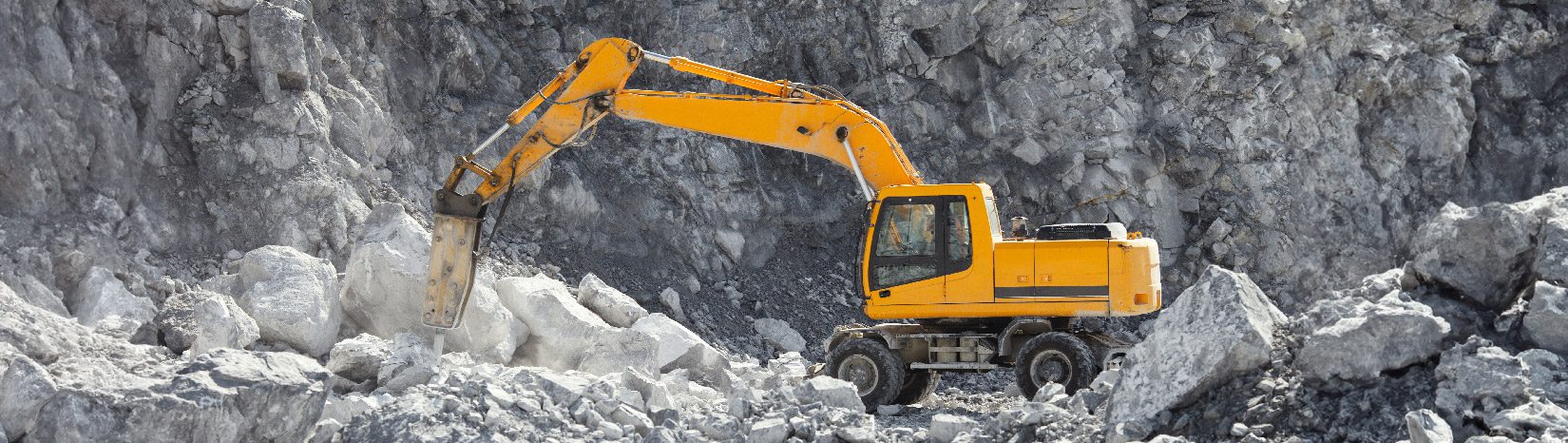
编写者
李端杰,博士
简介
岩石由矿物颗粒组成。这些矿物的类型和丰度,以及矿物颗粒之间的化学键合强度,决定了岩石的机械和摩擦学特性。根据地质岩石循环,岩石可以发生转变,通常分为三种主要类型:火成岩、沉积岩和变质岩。这些岩石表现出不同的矿物和化学成分、渗透性和颗粒尺寸,这些特性导致了它们不同的耐磨性。岩石摩擦学研究岩石在各种地质和环境条件下的磨损和摩擦行为。
岩石摩擦学的重要性
在钻井过程中,岩石会发生各种类型的磨损,包括擦伤和摩擦,导致钻头和切削工具的维修和更换造成重大的直接和间接损失。因此,岩石的可钻性、可钻性、可切削性和磨蚀性的研究在石油、天然气和采矿业中至关重要。岩石摩擦学研究在选择最有效和最具成本效益的钻井策略方面发挥着关键作用,从而提高整体效率并有助于保护材料、能源和环境。此外,最大限度地减少表面摩擦对于减少钻头和岩石之间的相互作用非常有利,从而减少工具磨损并提高钻孔/切割效率。
测量目标
在本研究中,我们模拟并比较了两种类型岩石的摩擦学特性,以展示 NANOVEA T50 的能力 摩擦仪 以受控和监测的方式测量岩石的摩擦系数和磨损率。
NANOVEA
T50
了解更多
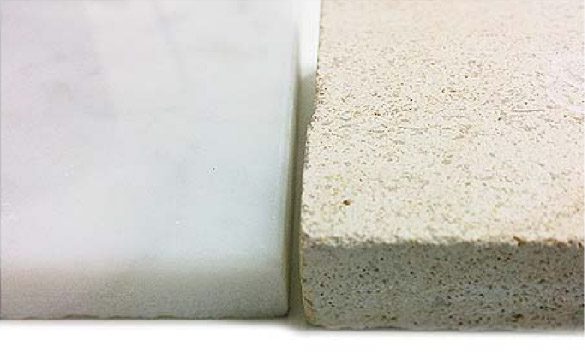
样品
测试程序
使用 Pin-on-Disc 磨损模块的 NANOVEA T50 摩擦磨损试验机评估了两个岩石样品的摩擦系数、COF 和耐磨性。 Al2O3 球(直径 6 mm)用作计数器材料。测试后使用 NANOVEA 非接触式轮廓仪检查磨损轨迹。测试参数总结如下。
磨损率K的计算公式为K=V/(F×s)=A/(F×n),其中V为磨损体积,F为法向载荷,s为滑动距离,A为磨损轨迹的横截面积,n 是转数。使用 NANOVEA 光学轮廓仪评估表面粗糙度和磨损轨迹轮廓,并使用光学显微镜检查磨损轨迹形态。
请注意,本研究中以 Al2O3 球作为计数器材料为例。任何不同形状的固体材料都可以使用定制夹具来模拟实际应用情况。
测试参数
钢表面
石灰石、大理石
耐磨环半径 |
5毫米 |
常态力 |
10 N |
测试时间 |
10分钟 |
速度 |
100转/分 |
结果与讨论
图 1 使用 NANOVEA 机械测试仪的微压痕模块对石灰石和大理石样品的硬度 (H) 和弹性模量 (E) 进行了比较。石灰岩样品表现出较低的 H 和 E 值,分别为 0.53 和 25.9 GPa,而大理石样品的 H 值为 1.07,E 值为 49.6 GPa。石灰石样品可归因于其较大的表面不均匀性,这源于其颗粒状和多孔特性。
图 2 描绘了两个岩石样品磨损测试期间 COF 的演变。在磨损测试开始时,石灰石的 COF 最初快速增加至约 0.8,并在整个测试期间保持该值。 COF 的这种突然变化可归因于 Al2O3 球渗透到岩石样品中,这是由于磨损轨迹内接触面发生的快速磨损和粗糙化过程造成的。相比之下,在滑动距离约 5 米后,大理石样品的 COF 显着增加至更高的值,这表明与石灰石相比,其耐磨性更优异。
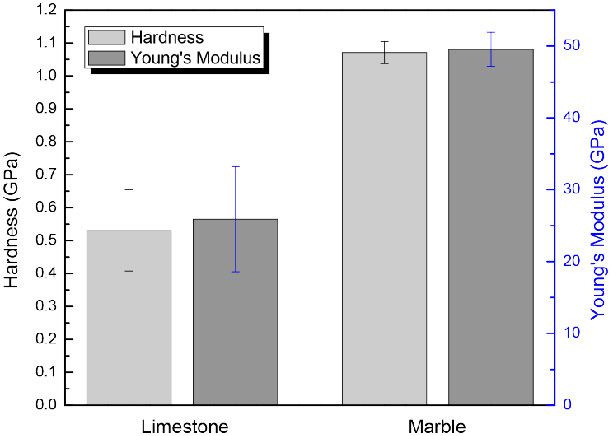
图1:
石灰石和大理石样品之间的硬度和杨氏模量比较。
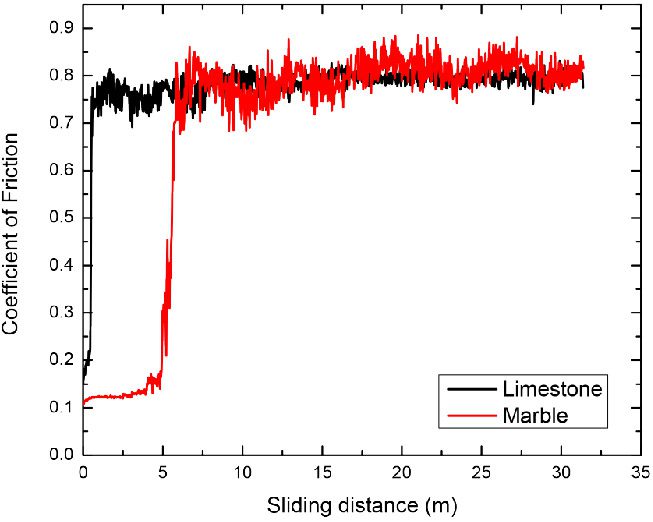
图2:
摩擦系数 (COF) 的演变
在磨损测试期间的石灰石和大理石样品中。
图 3 比较了磨损测试后石灰石和大理石样品的横截面轮廓,表 1 总结了磨损轨迹分析的结果。图 4 显示了光学显微镜下样品的磨损痕迹。磨损轨迹评估与 COF 演变观察一致:大理石样品在较长时间内保持较低的 COF,其磨损率较低,为 0.0046 mm3/N m,而石灰石的磨损率为 0.0353 mm3/N m。大理石优越的机械性能使其比石灰石具有更好的耐磨性。
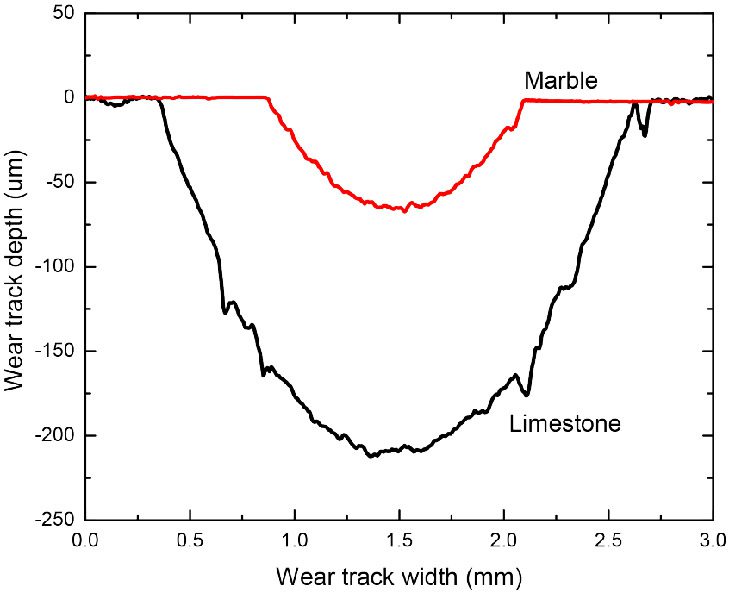
图3:
磨损轨迹的横截面轮廓。
|
山谷地区 |
山谷深度 |
磨损率 |
石灰石 |
35.3±5.9×104 微米2 |
229±24微米 |
0.0353毫米3/牛米 |
大理石 |
4.6±1.2×104 微米2 |
61±15微米 |
0.0046毫米3/牛米 |
表1:
磨损轨迹分析结果总结。
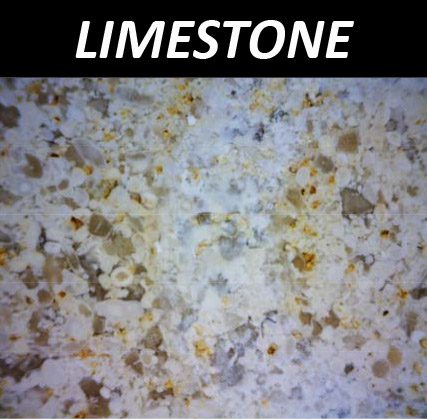
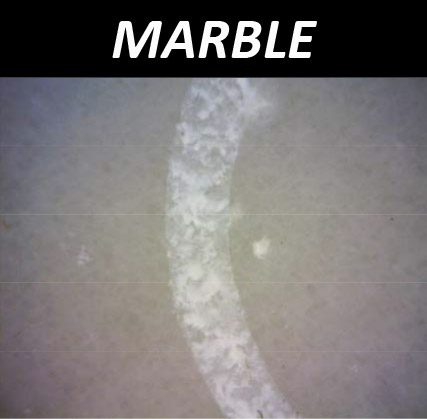
图4:
光学显微镜下的磨损痕迹。
结论
在这项研究中,我们展示了 NANOVEA 摩擦磨损试验机以受控和监测的方式评估两种岩石样品(即大理石和石灰石)的摩擦系数和耐磨性的能力。大理石卓越的机械性能有助于其卓越的耐磨性。这种特性使得石油和天然气行业的钻探或切割变得具有挑战性。相反,当用作高质量建筑材料(例如地砖)时,它的使用寿命会显着延长。
NANOVEA 摩擦磨损试验机提供精确且可重复的磨损和摩擦测试功能,在旋转和线性模式下均符合 ISO 和 ASTM 标准。此外,它还提供用于高温磨损、润滑和摩擦腐蚀的可选模块,所有这些模块都无缝集成到一个系统中。 NANOVEA 无与伦比的系列是确定薄或厚、软或硬涂层、薄膜、基材和岩石摩擦学的全方位摩擦学特性的理想解决方案。
PTFE涂层磨损测试
使用摩擦仪绘制地板的渐进式磨损图
摩擦试验机测高温下划痕硬度
工业涂料的划痕和磨损评估
摩擦仪试验机测量聚合物皮带的磨损和摩擦
使用摩擦仪测量砂纸的磨损性能
活塞磨损测试
用摩擦仪进行玻璃涂层湿度磨损测试
高温下的原位磨损测量