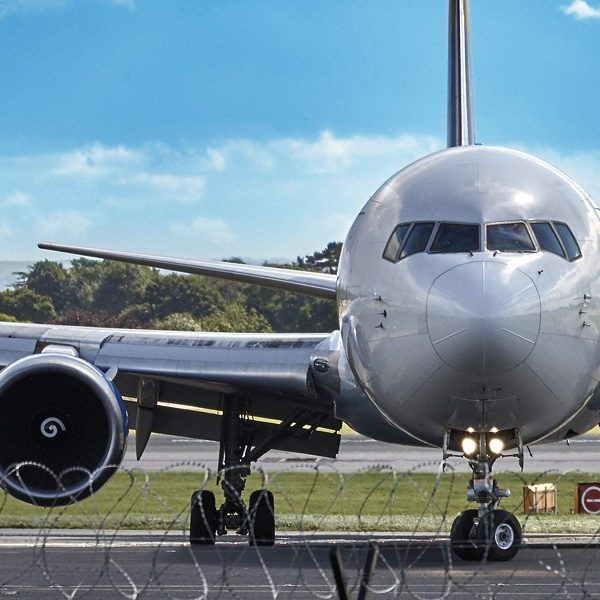
DLC膜のトライボロジーにおける湿度効果
DLCの湿度下での摩耗評価の重要性
ダイヤモンド ライク カーボン (DLC) コーティングは、強化された摩擦特性、つまり優れた耐摩耗性と非常に低い摩擦係数 (COF) を備えています。 DLC コーティングは、さまざまな材料上に蒸着されるとダイヤモンドの特性を与えます。有利な摩擦機械特性により、DLC コーティングは航空宇宙部品、かみそりの刃、金属切削工具、ベアリング、オートバイのエンジン、医療用インプラントなどのさまざまな産業用途に適しています。
DLC コーティングは、高真空および乾燥条件下で鋼球に対して非常に低い COF (0.1 未満) を示します。12.しかし、DLCコーティングは環境条件の変化、特に相対湿度(RH)に敏感である。3.湿度や酸素濃度が高い環境では、COFが大幅に増加する可能性があります。4。制御された湿度での信頼性の高い摩耗評価により、トライボロジー用途における DLC コーティングの現実的な環境条件がシミュレートされます。ユーザーは適切な比較を行い、対象用途に最適なDLCコーティングを選択します。
さまざまな湿度にさらされたDLCの摩耗挙動の変化。
測定目的
この研究では Nanovea を紹介します トライボメータ 湿度コントローラーを備えたこのツールは、さまざまな相対湿度における DLC コーティングの摩耗挙動を調査するのに最適なツールです。
試験方法
DLC コーティングの耐摩擦性と耐摩耗性は、Nanovea Tribometer によって評価されました。テストパラメータを表 1 にまとめます。トライボチャンバーに取り付けられた湿度コントローラは、±1% の精度で相対湿度 (RH) を正確に制御しました。試験後、DLC コーティングの摩耗痕跡と SiN ボールの摩耗痕を光学顕微鏡を使用して検査しました。
注: 潤滑剤や高温などの環境条件下で、さまざまな材料のカップリングの性能をシミュレートするために、任意の固体ボール材料を適用できます。
結果および考察
DLCコーティングは、低摩擦で耐摩耗性に優れているため、トライボロジー用途に最適です。DLCコーティングの摩擦は、図2に示すような湿度依存性の挙動を示しています。比較的乾燥した条件下(10% RH)では、DLCコーティングは摩耗試験中、約0.05という非常に低いCOFを示しました。RHが30%まで上昇すると、DLCコーティングは、試験中、〜0.1の一定のCOFを示しました。COFの初期段階は、RHが50%以上に上昇した最初の2000回転で観察されます。DLCコーティングは、RHが50、70、90%のときにそれぞれ〜0.20、〜0.26、〜0.33という最大COFを示す。慣らし運転後、DLCコーティングのCOFは、RH50、70、90%でそれぞれ〜0.11、0.13、0.20と一定に保たれる。
図3はSiNボールの摩耗痕、図4は摩耗試験後のDLCコーティングの摩耗痕を比較したものである。湿度の低い環境にさらされたDLCコーティングの方が、摩耗痕の直径が小さくなっていることがわかる。接触面において繰り返し摺動することで,SiN ボール表面に転写 DLC 層が蓄積される。この段階で,DLC 被膜は自身の転写膜と摺動し,効率的な潤滑剤として相対運動を促進し,せん断変形によるさらなる質量減少を抑制していることがわかる。低RH環境(10%や30%など)では,SiNボールの摩耗痕に転写膜が観察され,ボールの摩耗過程が減速される.この摩耗過程は、図4に示すようにDLCコーティングの摩耗痕の形態に反映される。これは,接触界面に安定したDLC膜が形成され,摩擦と摩耗速度が大幅に低減されたためである。
結論
湿度は、DLC コーティングの摩擦学的性能に重要な役割を果たします。 DLC コーティングは、摺動相手 (この研究では SiN ボール) に転写された安定した黒鉛層の形成により、乾燥状態で大幅に強化された耐摩耗性と優れた低摩擦を備えています。 DLC コーティングは、それ自身の転写層に対して滑ります。この転写層は効率的な潤滑剤として機能し、相対運動を促進し、せん断変形によって引き起こされるさらなる質量損失を抑制します。相対湿度が上昇すると、SiN ボール上に膜が観察されなくなり、SiN ボールと DLC コーティングの摩耗率が増加します。
Nanovea トライボメーターは、ISO および ASTM 準拠の回転モードおよび直線モードを使用した反復可能な摩耗および摩擦試験を提供し、1 つの事前統合システムで利用可能なオプションの湿度モジュールを備えています。これにより、ユーザーはさまざまな湿度での作業環境をシミュレートでき、さまざまな作業条件下での材料のトライボロジー挙動を定量的に評価するための理想的なツールをユーザーに提供できます。
ナノベーストライボメータとラボサービスについての詳細はこちら
1 C. Donnet, Surf.Coat.Technol.100-101 (1998) 180.
2 三好和彦, B. Pohlchuck, K.W. Street, J.S. Zabinski, J.H. Sanders, A.A. Voevodin, R.L.C. Wu, Wear 225-229 (1999) 65.
3 R. Gilmore, R. Hauert, Surf.Coat.Technol.133-134 (2000) 437.
4 R. Memming, H.J. Tolle, P.E. Wierenga, Thin Solid Coatings 143 (1986) 31
さて、次はアプリケーションについてです。
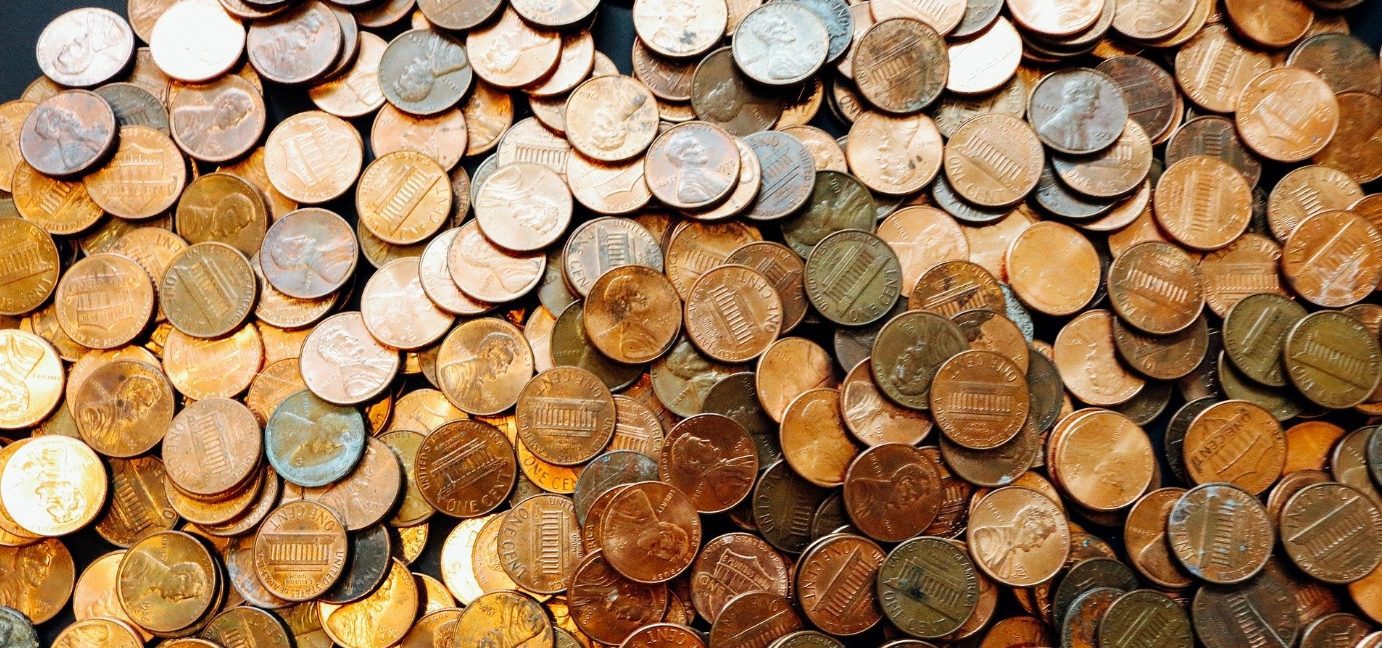
非接触式プロフィロメータによるペニーの3次元表面解析
コインの非接触形状測定の重要性
通貨は商品やサービスと交換されるため、現代社会では高く評価されています。硬貨や紙幣の通貨は多くの人の手に渡ります。物理的な通貨の継続的な転送により、表面の変形が生じます。ナノベアの3D プロフィロメーター 異なる年に鋳造されたコインの地形をスキャンして、表面の違いを調査します。
コインの特徴は、一般的なオブジェクトであるため、一般の人々にとって容易に認識できます。 Nanovea の高度な表面解析ソフトウェアである Mountains 3D の強みを紹介するには、1 ペニーが最適です。当社の 3D 表面形状計で収集された表面データにより、表面の減算と 2D 輪郭抽出による複雑な形状の高度な分析が可能になります。制御されたマスク、スタンプ、または金型を使用した表面減算により製造プロセスの品質を比較し、輪郭抽出により寸法解析により公差を特定します。 Nanovea の 3D プロフィロメーターと Mountains 3D ソフトウェアは、ペニー硬貨のような一見単純な物体のサブミクロンの地形を調査します。
測定目的
Nanovea社の高速ラインセンサーを使用して、5枚のペニーの上面全体をスキャンしました。各ペニーの内側と外側の半径は、Mountains Advanced Analysis Softwareを使用して測定されました。各ペニー表面から関心領域の抽出と表面の直接減算を行い、表面の変形を定量化しました。
結果および考察
3Dサーフェス
Nanovea HS2000 プロフィロメーターは、1円玉の表面を取得するために、10um x 10um のステップサイズで 20mm x 20mm の領域を 400 万点スキャンするのにわずか 24 秒しかかかりませんでした。以下は、スキャンのハイトマップと3Dビジュアライゼーションです。3D表示では、目では見えない細かな部分まで高速度センサーが拾っていることが分かります。1円玉の表面には、たくさんの小さな傷が見えます。3Dビューで見たコインの質感と粗さを調査。
ペニーの輪郭を抽出し,寸法解析を行った結果,エッジの内径と外径が判明した。外側の半径は平均9.500mm±0.024、内側の半径は平均8.960mm±0.032となりました。Mountains 3Dは、2Dおよび3Dデータソースに対して、距離測定、ステップ高、平面性、角度計算などの寸法解析を行うことができます。
図5は、サーフェスサブトラクション解析の対象領域を示したものである。2007年の1円玉を基準面として、4つの古い1円玉の表面を分析した。2007年版の表面から減算することで、穴や峰のあるペニー間の差がわかる。表面体積の差は、穴や峰の体積を足したものである。RMS誤差は、ペニー表面同士がどの程度一致しているかを示すものである。
結論
Nanovea社のHigh-Speed HS2000Lは、異なる年に鋳造された5枚の硬貨をスキャンしました。3DソフトウェアMountainsは、輪郭抽出、寸法分析、表面減算を用いて各コインの表面を比較しました。この分析では、表面の特徴の違いを直接比較しながら、硬貨の内側と外側の半径を明確に定義しています。ナノメートルレベルの分解能であらゆる表面を測定できるナノベアの3Dプロフィロメーターと、マウンテンズの3D解析機能を組み合わせれば、研究および品質管理への応用は無限に広がります。
さて、次はアプリケーションについてです。
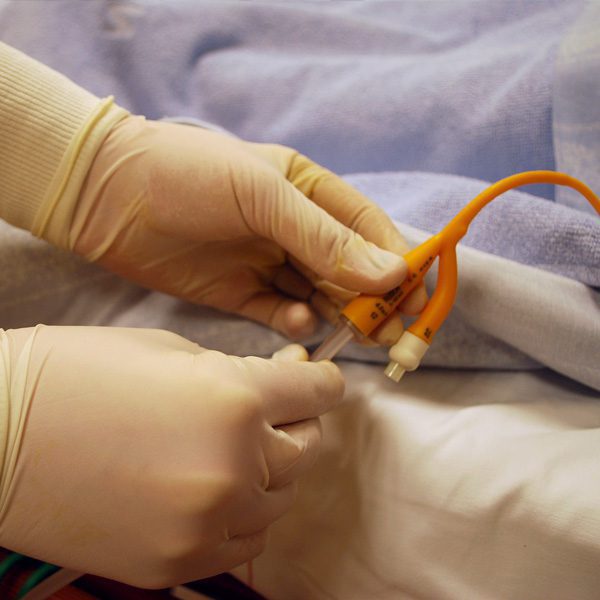
ポリマー・チューブの寸法と表面仕上げ
高分子チューブの寸法・表面解析の重要性
ポリマー材料で作られたチューブは、自動車、医療、電気、その他多くの分野に及ぶ多くの業界で一般的に使用されています。この研究では、Nanovea を使用して、さまざまなポリマー材料で作られた医療用カテーテルを研究しました。 3D非接触形状計 を使用して、表面粗さ、形態、および寸法を測定します。感染症、物理的外傷、炎症など、カテーテルに関する多くの問題は、カテーテル表面と関連する可能性があるため、表面粗さはカテーテルにとって極めて重要です。また、摩擦係数のような機械的特性も、表面特性を観察することで研究することができます。これらの定量的なデータを得ることで、カテーテルが医療用途に使用できることを確認することができる。
光学顕微鏡や電子顕微鏡と比較して、角度/曲率を測定できること、透明度や反射率に関わらず材料表面を測定できること、最小限の試料準備、非侵襲性のため、軸色相を用いた3D非接触プロフィロメトリはカテーテル表面の特性評価に非常に適しています。従来の光学顕微鏡とは異なり、表面の高さを求めることができ、寸法を求めたり、形状を除去して表面の粗さを求めるなど、計算機による解析に使用することができる。また、電子顕微鏡とは異なり、試料調製が少なく、非接触であるため、試料調製による汚染や誤差を恐れることなく、迅速にデータを収集することができる。
測定目的
このアプリケーションでは、Nanovea 3D 非接触型プロフィロメータを使用して、TPE(熱可塑性エラストマー)製とPVC(ポリ塩化ビニル)製の2つのカテーテルの表面をスキャンします。2つのカテーテルの形態、径方向寸法、高さ方向のパラメータを取得し、比較することができます。
結果および考察
3Dサーフェス
ポリマー製チューブは湾曲していますが、ナノベア3D非接触型プロフィロメーターはカテーテルの表面をスキャンすることができます。スキャンした画像から3D画像を取得し、表面を素早く、直接目視で検査することができます。
半径方向外側の寸法は、オリジナルのスキャンからプロファイルを抽出し、そのプロファイルに円弧をフィットさせることによって得られた。これは、品質管理アプリケーションのための迅速な寸法分析を行う3D非接触プロフィロメーターの能力を示しています。また、カテーテルの長さ方向に複数のプロファイルを簡単に取得することができます。
半径方向外側の寸法は、オリジナルのスキャンからプロファイルを抽出し、そのプロファイルに円弧をフィットさせることによって得られた。これは、品質管理アプリケーションのための迅速な寸法分析を行う3D非接触プロフィロメーターの能力を示しています。また、カテーテルの長さ方向に複数のプロファイルを簡単に取得することができます。
結論
このアプリケーションでは、Nanovea 3D 非接触型プロフィロメータを使用して、ポリマー製チューブの特性を評価する方法を示しました。具体的には、医療用カテーテルの表面計測、半径方向の寸法、表面粗さを取得しました。TPEカテーテルの外径半径は2.40mmであるのに対し、PVCカテーテルは1.27mmであることが判明しました。TPEカテーテルの表面は、PVCカテーテルよりも粗いことがわかった。TPEのSaは0.9740μmであるのに対し、PVCは0.1791μmであった。今回は医療用カテーテルを使用しましたが、3D非接触形状測定はさまざまな表面に適用することができます。取得できるデータや計算は、ここに示したものに限られるものではありません。
さて、次はアプリケーションについてです。
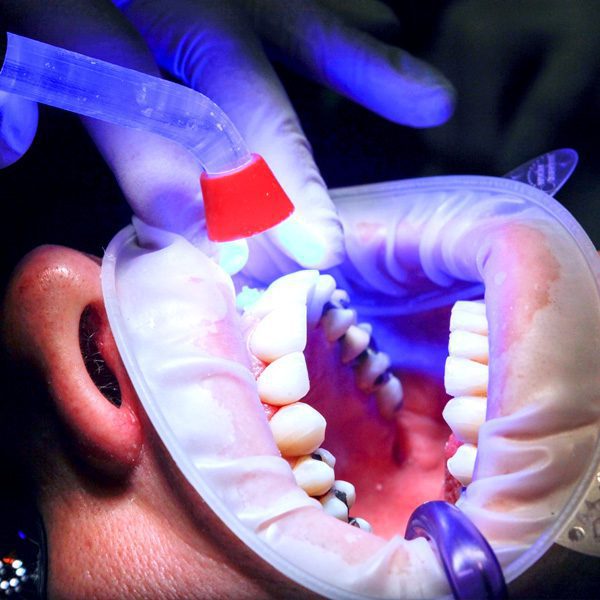
ナノインデンテーションを用いた歯の硬さ評価
バイオ材料におけるナノインデンテーションの重要性
ゲルから脆性材料に至るまで、高度な敏感な材料を使用する今日の品質管理環境では、従来の多くの機械的試験 (硬度、接着力、圧縮、突刺し、降伏強度など) が必要となり、より高い精度と信頼性の管理が求められています。従来の機械式計装では、必要な高感度の負荷制御と分解能を提供できません。バルク材料に使用するように設計されています。試験される材料のサイズに対する関心が高まるにつれて、 ナノインデンテーション 生体材料を使って行われている研究など、より小さな表面に関する重要な機械的情報を取得するための信頼できる方法を提供しました。生体材料に特に関連する課題には、非常に柔らかい材料から脆い材料に対する正確な荷重制御が可能な機械的試験の開発が必要でした。また、さまざまな機械的テストを実行するには複数の機器が必要でしたが、現在では単一のシステムで実行できるようになりました。ナノインデンテーションは、敏感な用途向けにナノ制御された荷重で正確な分解能で幅広い測定を提供します。
測定目的
このアプリケーションでは、ナノベア メカニカルテスターは、ナノインデンテーション モードで、歯の象牙質、虫歯、歯髄の硬度と弾性率を研究するために使用されます。ナノインデンテーション試験で最も重要な点は、サンプルを固定することです。ここでは、スライスした歯を採取し、エポキシを取り付けて、3 つの対象領域すべてを試験用に露出させておきました。
結果および考察
このセクションでは、異なる試料の主な数値結果を比較した要約表と、実施した各圧痕を含む完全な結果リストがあり、可能な場合は圧痕の顕微鏡写真も添えています。これらの全結果は、硬度とヤング率の測定値を押し込み深さとして、その平均値と標準偏差を表示しています。なお、表面粗さが圧痕と同じ大きさの範囲にある場合、結果に大きなばらつきが生じる可能性があることを考慮しておく必要がある。
主な数値結果のサマリー表。
結論
最後に、ナノインデンテーション・モードのナノベアメカニカルテスターで、歯の機械的特性を正確に測定する方法を紹介しました。このデータは、実際の歯の機械的特性によりよく適合する詰め物の開発に利用することができます。ナノベアメカニカルテスターの位置決め機能により、様々なゾーンに渡る歯の硬度の完全なマッピングが可能です。
同じシステムを使って、200Nまでの高荷重で歯の材料の破壊靭性をテストすることが可能です。多孔質材料では、マルチサイクル荷重試験で弾性残存率を評価することができます。平らな円柱状のダイヤモンドチップを使用することで、各ゾーンでの降伏強度の情報を得ることができます。また、DMA(Dynamic Mechanical Analysis)により、損失弾性率や貯蔵弾性率などの粘弾性特性を評価することができます。
ナノベアーのナノモジュールは、独自のフィードバック応答により、かかる荷重を正確に制御するため、こうした試験に最適です。このため、ナノモジュールを使用して正確なナノスクラッチ試験を行うことも可能です。歯材や充填材の耐スクラッチ性と耐摩耗性の研究は、メカニカルテスターの有用性をさらに高めています。2ミクロンの鋭い探針を使って充填材の傷を定量的に比較することで、実際のアプリケーションでの挙動をより正確に予測することが可能になります。マルチパス摩耗または直接回転摩耗試験も一般的な試験であり、長期的な生存率に関する重要な情報を提供します。
さて、次はアプリケーションについてです。
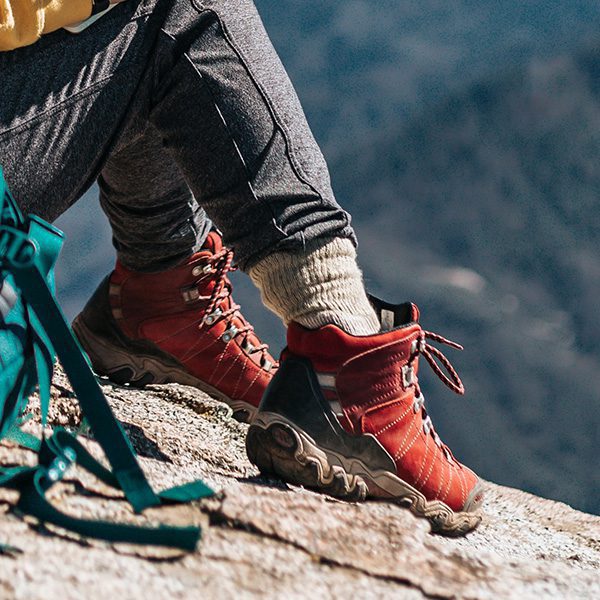
極低速域での摩擦評価
低速域での摩擦評価の重要性
摩擦とは、固体表面同士を滑らせて相対運動に抵抗させる力のことである。この2つの接触面の相対運動が起こると、界面での摩擦により運動エネルギーが熱に変換される。また、このようなプロセスは、材料の摩耗、ひいては使用中の部品の性能劣化につながる可能性がある。
ゴムは伸び率が大きく、弾力性に富み、防水性や耐摩耗性にも優れているため、自動車のタイヤやワイパーブレード、靴底など、摩擦が重要な役割を果たすさまざまな用途や製品に幅広く使用されている。これらの用途の性質や要求に応じて、異なる材料に対して高い摩擦と低い摩擦のどちらかが望まれる。そのため、さまざまな表面に対するゴムの摩擦を制御し、信頼性の高い方法で測定することが重要になります。
測定目的
さまざまな材料に対するゴムの摩擦係数 (COF) は、Nanovea を使用して制御および監視された方法で測定されます。 トライボメータ。この研究では、極低速でさまざまな材料の COF を測定する Nanovea トライボメーターの能力を紹介したいと思います。
結果および考察
3種類の材料(Stainless steel SS 316, Cu 110, optional Acrylic)に対するゴム球(φ6mm, RubberMill)の摩擦係数(COF)をNanovea Tribometerで評価した.試験した金属サンプルは、測定前に機械的に研磨し、鏡面仕上げとした。法線荷重を加えた際のゴム球のわずかな変形によって面積接触が生じ、COF測定に対する試料表面のアスペリティや不均一性の影響を軽減することもできます。試験パラメータを表 1 に示す。
4種類の速度で異なる素材に対してゴム球を衝突させたときのCOFを図2に示す。2 に、ソフトウェアによって自動的に計算された平均 COF をまとめ、図 3 で比較した。興味深いことに、金属試料(SS 316 と Cu 110)は、回転速度が 0.01 rpm という非常に低い値から 5 rpm まで上昇すると、COF が著しく増加することがわかります。この結果は、いくつかの研究室から報告されている結果と一致している。Groschが提案したように4 ゴムの摩擦は、主に(1)ゴムと他の材料の接着、(2)表面の凹凸によるゴムの変形によるエネルギー損失の2つのメカニズムで決定される。シャラマッハ5 軟質ゴム球と硬質表面との界面において,ゴムが相手材から剥離する波が観察された。ゴムが基材表面から剥離する力と剥離の波の速度から、試験中の異なる速度での摩擦の違いを説明することができる。
これに対し、ゴムとアクリルのカップルは、異なる回転数で高いCOFを示しました。回転速度が0.01 rpmから5 rpmまで上昇すると、COF値は1.02から1.09までわずかに上昇した。このような高いCOFは、おそらく試験中に形成された接触面の局所的な化学結合が強くなったことに起因しています。
結論
本研究では、ゴムが極低速で、硬い表面に対する摩擦が相対運動の速度が上がるにつれて大きくなるという特異な摩擦挙動を示すことを示した。ゴムは、異なる材料の上を滑るとき、異なる摩擦を示します。ナノベーストライボメータは、異なる速度で制御・監視された方法で材料の摩擦特性を評価することができ、ユーザーは材料の摩擦メカニズムの基本的な理解を深め、目標とするトライボロジー工学アプリケーションに最適な材料カップルを選択することが可能です。
ナノベーストライボメータは、ISOおよびASTMに準拠した回転モードとリニアモードによる精密で再現性の高い摩耗・摩擦試験と、オプションで高温摩耗、潤滑、トライボコロージョンを1つの統合されたシステムで利用することが可能です。0.01 rpmまでの極めて低い速度で回転ステージを制御し、摩擦の変化をその場でモニターすることが可能です。ナノベアの比類なき製品群は、薄いまたは厚い、柔らかいまたは硬いコーティング、フィルム、および基材のトライボロジー特性をフルレンジで測定するための理想的なソリューションとなります。
さて、次はアプリケーションについてです。
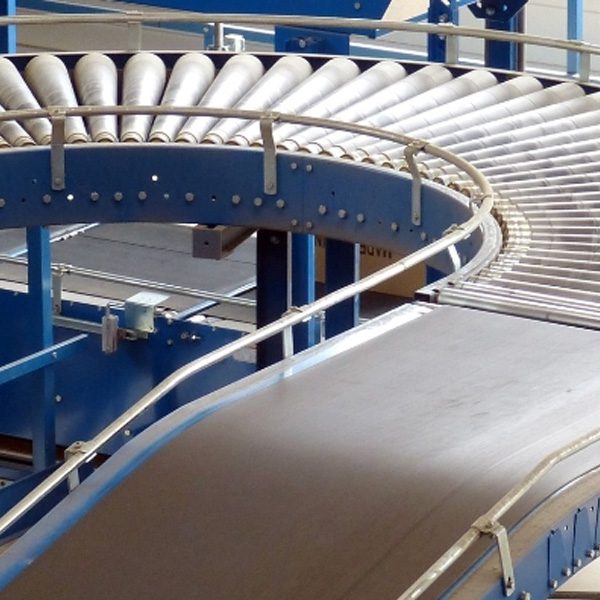
高分子のトライボロジー
はじめに
高分子はさまざまな用途に幅広く利用され、日常生活に欠かせないものとなっている。琥珀、絹、天然ゴムなどの天然高分子は、人類の歴史において不可欠な役割を担ってきた。合成高分子の製造プロセスを最適化することで、強靭性、粘弾性、自己潤滑性など、ユニークな物理的特性を実現することができる。
高分子の摩耗と摩擦の重要性
ポリマーは、タイヤ、ベアリング、コンベヤーベルトなどのトライボロジー用途によく使われている。
ポリマーの機械的特性、接触条件、摩耗過程で形成される破片や転写膜の特性によって、さまざまな摩耗メカニズムが発生します。ポリマーが使用条件下で十分な耐摩耗性を有することを確認するためには、信頼性が高く定量的なトライボロジー評価が必要である。トライボロジー評価により、異なるポリマーの摩耗挙動を制御・監視しながら定量的に比較し、目的とする用途に適した材料候補を選択することができます。
ナノベーストライボメータは、ISOとASTMに準拠した回転・直線モードによる再現性の高い摩耗・摩擦試験と、オプションで高温摩耗・潤滑モジュールを1つの統合済みシステムで利用できます。この比類のないラインナップにより、ユーザーは、集中応力、摩耗、高温など、ポリマーのさまざまな作業環境をシミュレートすることができます。
測定目的
この研究では、Nanovea が トライボメータ は、さまざまなポリマーの摩擦抵抗と耐摩耗性を、適切に制御された定量的な方法で比較するための理想的なツールです。
試験方法
さまざまな一般的なポリマーの摩擦係数 (COF) と耐摩耗性は、Nanovea Tribometer によって評価されました。 Al2O3 ボールをカウンター材 (ピン、静止サンプル) として使用しました。ポリマー(動的回転サンプル)の摩耗痕跡は、 非接触3D表面形状計 テスト終了後の光学顕微鏡。オプションとして、非接触内視鏡センサーを使用して、摩耗試験中に動的サンプルにピンが貫通する深さを測定できることに注意してください。試験パラメータを表 1 にまとめます。摩耗率 K は、式 K=Vl(Fxs) を使用して評価しました。ここで、V は摩耗量、F は垂直荷重、s は滑り距離です。
なお,本研究ではAl2O3ボールを対向材として使用した。実際の適用条件下での2つの試料の性能をより詳細にシミュレートするために、任意の固体材料に置き換えることができます。
結果および考察
摩擦はトライボロジー応用において重要な役割を果たす一方、摩耗速度は材料の寿命を決定する重要な要因です。図2はAl2O3ボールに対する各種ポリマーの摩耗試験におけるCOFの推移を比較したものである。COFは、いつ故障が発生し、摩耗が新しい段階に入るかを示す指標として機能します。試験したポリマーのうち、HDPEは摩耗試験中、COFが最も低く、0.15程度に保たれています。COFが滑らかであることは、安定したトライボコンタクトが形成されていることを示唆しています。
図3と図4は、試験後のポリマーサンプルの摩耗軌跡を光学顕微鏡で測定した結果を比較したものです。In-situ非接触三次元形状測定機は、ポリマー試料の摩耗量を正確に測定し、それぞれ0.0029、0.0020、0.0032m3/N mの摩耗量を正確に計算することが可能です。一方、CPVCの摩耗痕には深い平行摩耗痕が認められ、0.1121m3/N mという最も高い摩耗量を示した。
まとめ
高分子の耐摩耗性は、そのサービス性能に重要な役割を果たします。この研究では、ナノベーストライボメータが、様々なポリマーの摩擦係数と摩耗率を、1つの試験片で評価することを紹介しました。
をよく制御し、定量的な方法で行った。HDPEは試験したポリマーの中で最も低いCOFを示し、約0.15であった。HDPE、ナイロン66、ポリプロピレンはそれぞれ0.0029、0.0020、0.0032 m3/N mという低い摩耗率を有しています。低摩擦と優れた耐摩耗性の組み合わせにより、HDPEはポリマートライボロジー用途に適した材料といえます。
In-situ 非接触型3次元形状測定器は、精密な摩耗量測定を可能にし、摩耗痕の詳細な形態を解析するツールを提供することで、摩耗メカニズムの基本的な理解への洞察を深めます
さて、次はアプリケーションについてです。
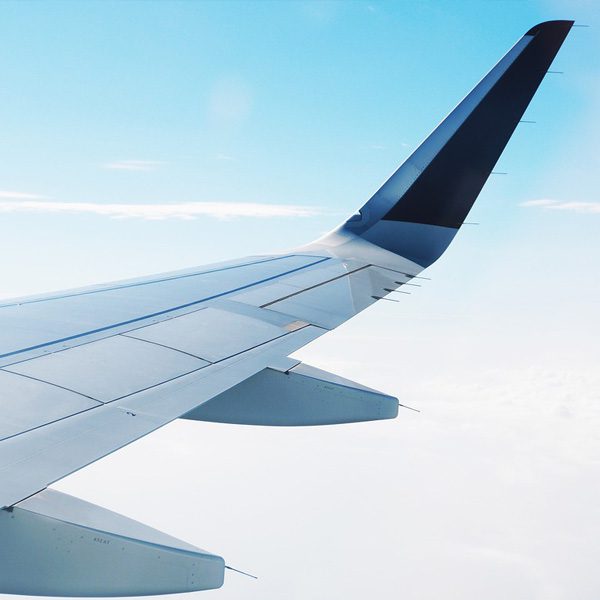
3次元形状測定によるハニカムパネルの表面仕上げ
はじめに
ハニカムパネル表面の粗さ、気孔率、テクスチャーは、最終的なパネル設計のために定量化することが重要です。これらの表面品質は、パネル表面の美観と機能特性に直接関連する可能性があります。表面の質感と気孔率をより良く理解することで、パネル表面の加工と製造性を最適化することができます。ハニカムパネルの定量的で正確かつ信頼性の高い表面測定は、アプリケーションや塗装の要件に応じた表面パラメータを制御するために必要です。ナノベア3D非接触センサーは、これらのパネル表面を正確に測定することができる独自のクロマティックコンフォーカル技術を利用しています。
測定目的
この研究では、高速ライン センサーを備えた Nanovea HS2000 プラットフォームを使用して、表面仕上げの異なる 2 つのハニカム パネルを測定し、比較しました。ナノベアをご紹介します 非接触表面形状計は、高速かつ正確な 3D プロファイリング測定と表面仕上げの包括的な詳細分析を提供する機能を備えています。
結果および考察
表面仕上げを変化させた2つのハニカムパネル試料、すなわち試料1および試料2の表面を測定した。試料1と試料2の表面のフォールスカラーと3Dビューをそれぞれ図3、図4に示す。粗さと平坦度の値は高度な解析ソフトウェアによって計算され、表1で比較されています。サンプル2はサンプル1に比べ、よりポーラスな表面を呈しています。その結果、試料1の粗さSaが4.27μmであるのに対し、試料2は14.7μmと高い粗さを有していることがわかる。
ハニカムパネル表面の2次元プロファイルを図5で比較し、サンプル表面の異なる位置での高さ変化を視覚的に比較することができます。サンプル1では、最も高い山部と最も低い谷部の位置で、高さの変化が約25μmであることが観察されます。一方、サンプル2は、2Dプロファイル全体でいくつかの深い孔があることがわかります。高度な解析ソフトは、図 4.b 試料 2 の表に示すように、比較的深い 6 つの孔の位置を自動的に特定し、その深さを測定する機能を備えています。この6つの孔のうち、最も深い孔は、最大深度が90μm近くあります(ステップ4)。
Sample 2 の細孔径と分布をさらに調べるために、空隙率評価を行い、次節で考察する。スライス図を図 5 に、結果を表 2 にまとめました。図5で青色で示された細孔は、試料表面に比較的均質に分布していることがわかります。細孔の投影面積は、試料表面全体の18.9%を構成しています。1mm²当たりの気孔の体積は約0.06mm³です。気孔の平均深さは42.2μmで、最大深さは108.1μmです。
まとめ
このアプリケーションでは、高速ラインセンサを搭載したナノベア HS2000 プラットフォームが、ハニカムパネルサンプルの表面仕上げを高速かつ正確に分析・比較するための理想的なツールであることを紹介しています。高解像度のプロファイルスキャンと高度な解析ソフトウェアの組み合わせにより、ハニカムパネルサンプルの表面仕上げを包括的かつ定量的に評価することができます。
ここに掲載されているデータは、解析ソフトウェアで利用可能な計算のごく一部を示しているに過ぎません。ナノベアプロフィロメータは、半導体、マイクロエレクトロニクス、太陽電池、光ファイバー、自動車、航空宇宙、冶金、機械加工、コーティング、製薬、バイオメディカル、環境、その他多くの産業における幅広い用途で、ほぼあらゆる表面を測定することが可能です。
さて、次はアプリケーションについてです。
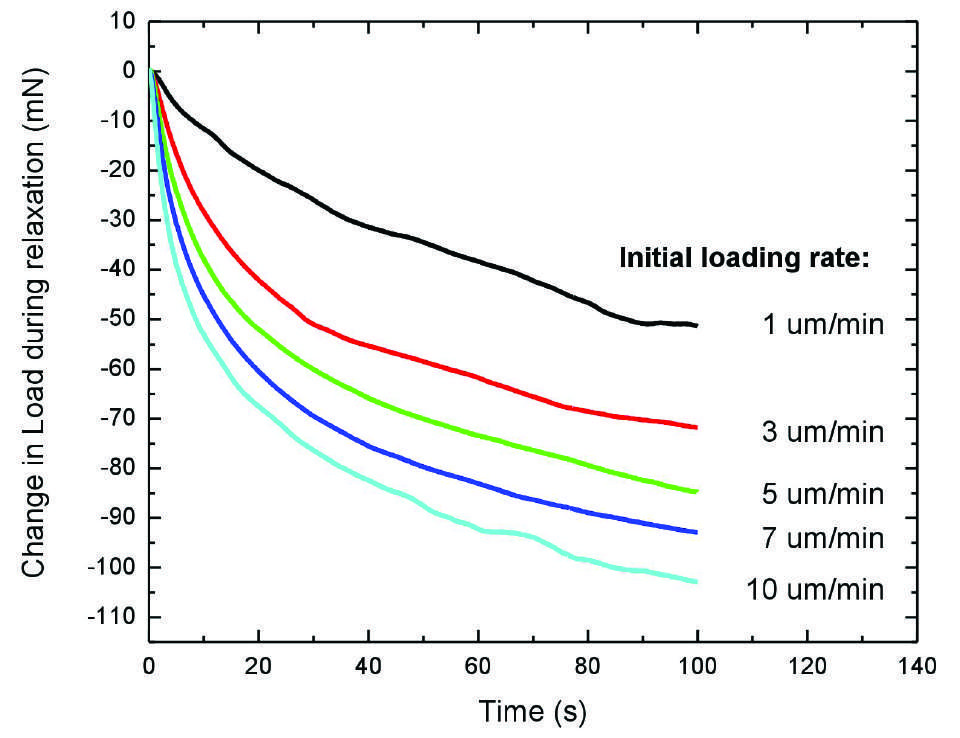
ナノインデンテーションによる応力緩和測定
はじめに
粘弾性材料は、粘性と弾性の両方の材料特性を持つことが特徴である。これらの材料は、一定のひずみで時間依存的に応力が減少(応力「緩和」)し、初期の接触力が大きく損なわれることになる。応力緩和は、材料の種類、組織、温度、初期応力、時間などに依存する。応力緩和を理解することは、特定の用途に必要な強度と柔軟性(緩和)を持つ最適な材料を選択する上で非常に重要である。
ストレス・リラクゼーション測定の重要性
ASTM E328i「材料および構造物の応力緩和の標準試験方法」に従い、材料や構造物に対して、最初に圧子を用いて所定の最大力に達するまで外力を加えておく。最大力に達した後、圧子の位置はその深さで一定に保たれます。そして、圧子の位置を維持するために必要な外力の変化を、時間の関数として測定する。応力緩和試験で難しいのは、深さを一定に保つことです。ナノベアメカニカルテスターの ナノインデンテーション モジュールは、圧電アクチュエーターによる深さの閉ループ(フィードバック)制御を適用することで、応力緩和を正確に測定します。アクチュエーターは深さを一定に保つためにリアルタイムで反応し、荷重の変化は高感度の荷重センサーによって測定・記録されます。この試験は、ほぼすべての種類の材料で実施することができ、厳しい試料寸法の要件は必要ありません。さらに、1つの平らな試料で複数の試験を行うことができ、試験の再現性を確保することができます。
測定目的
このアプリケーションでは、Nanovea Mechanical Tester のナノインデンテーション モジュールが、アクリルと銅のサンプルの応力緩和挙動を測定します。 Nanovea を紹介します。 メカニカルテスター は、ポリマーおよび金属材料の時間依存性の粘弾性挙動を評価するための理想的なツールです。
試験条件
Nanovea Mechanical Testerのナノインデンテーション・モジュールにより、アクリルと銅のサンプルの応力緩和を測定しました。1~10 μm/minの範囲でさまざまな圧痕の負荷速度が適用されました。目標の最大荷重に達すると、一定の深さで緩和が測定されました。一定の深さで100秒間の保持時間を設け、保持時間の経過に伴う荷重の変化を記録しました。試験はすべて周囲条件(室温23℃)で実施し、圧痕試験のパラメータは表1にまとめた。
結果および考察
図2 は、例としてアクリルサンプルと圧痕負荷速度3 µm/minの応力緩和測定中の変位と荷重の時間的変化を示しています。この試験の全体は、3つのステージに分けることができます。ローディング、リラクゼーション、アンローディングです。荷重ステージでは、荷重が徐々に増加するにつれて深さが直線的に増加しました。最大荷重に達すると、弛緩段階が開始されました。このステージでは、装置の閉ループ深度制御機能を使用して100秒間一定の深度を維持し、時間とともに荷重が減少することが観察されました。試験全体は、圧子をアクリル試料から取り外すための除荷ステージで終了しました。
さらに、同じ圧子負荷速度を用いて、緩和(クリープ)期間を除いた圧子試験を実施した。これらの試験から荷重-変位プロットを取得し、アクリルおよび銅の各試料について図3のグラフにまとめました。圧子負荷速度が10μm/minから1μm/minに減少するにつれて、荷重-変位曲線はアクリルと銅の両方でより高い浸透深度に向かって徐々にシフトしていきました。このような時間依存的なひずみの増加は、材料の粘弾性クリープ効果によるものである。低い負荷速度では、粘弾性材料が外部応力に反応し、それに応じて変形するまでの時間が長くなる。
図 4 に、試験した両材料について、異なる押込み荷重速度を用いた一定ひずみでの荷重の推移をプロットし た。荷重は、試験の緩和段階(100秒保持)の初期に高い割合で減少し、保持時間が〜50秒に達すると減速した。ポリマーや金属などの粘弾性材料は、より高い押込み荷重率を受けると、より大きな荷重損失率を示す。緩和時の荷重損失率は、圧子負荷速度が1~10μm/minに増加すると、アクリルでは51.5~103.2mN、銅では15.0~27.4mNに増加したことが、以下に要約されるようになります。 図5.
ASTM規格E328iiに記載されているように、応力緩和試験で遭遇する主な問題は、ひずみ/深さを一定に保つことができない装置であることです。ナノベアメカニカルテスターは、高速で作動する圧電アクチュエーターと独立したコンデンサーの深さセンサーの間で深さの閉ループ制御を行うことができるため、優れた精度の応力緩和測定が可能になっています。緩和の段階では、圧電アクチュエーターが圧子を調節して一定の深さの制約をリアルタイムで維持し、同時に独立した高精度荷重センサーによって荷重の変化が測定・記録されます。
まとめ
ナノベアメカニカルテスターのナノインデンテーション・モジュールを用いて、アクリルと銅のサンプルの応力緩和を、異なる荷重率で測定しました。低い荷重率で圧痕を形成すると、荷重時の材料のクリープ効果により、より大きな最大深さに到達します。アクリルおよび銅の両サンプルは、目標とする最大荷重における圧子位置を一定に保つと、応力緩和挙動を示します。緩和段階での荷重損失の大きな変化は、より高い圧子負荷率の試験で観察された。
ナノベアメカニカルテスターによる応力緩和試験は、ポリマーや金属材料の時間依存の粘弾性挙動を定量的かつ確実に測定できる装置であることを示します。このテスターは、単一プラットフォーム上にナノ・マイクロモジュールを搭載した、他に類を見ない多機能な装置です。湿度・温度制御モジュールを組み合わせることで、幅広い産業に適用可能な環境試験機能を実現します。ナノ・マイクロモジュールには、スクラッチ試験、硬さ試験、摩耗試験などのモードがあり、単一のシステムで最も幅広く、最も使いやすい機械的試験機能を提供します。
さて、次はアプリケーションについてです。
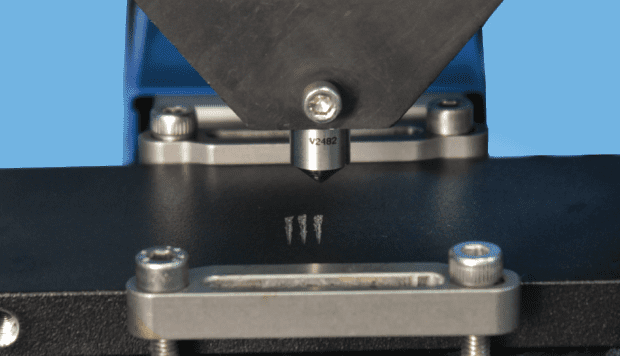
スクラッチテストによる塗膜故障の把握
はじめに
材料の表面処理は、装飾的な外観から、摩耗、腐食、その他の攻撃から基材を保護することまで、さまざまな機能的用途において重要な役割を担っています。コーティングの品質と寿命を決定する重要な要素は、その凝集力と接着力である。
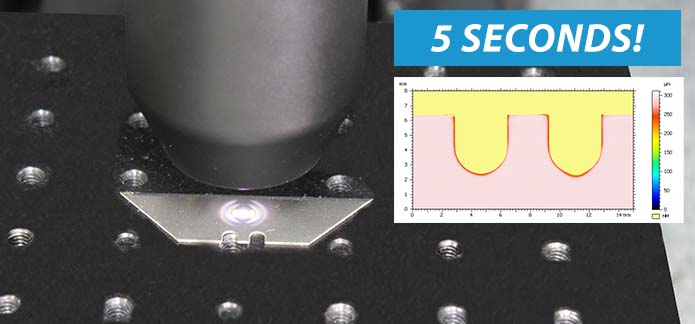
高速スキャンと非接触プロフィロメトリー
はじめに
素早く簡単にセットアップできる表面測定は時間と労力を節約し、品質管理、研究開発、生産施設には不可欠です。ナノベア 非接触表面形状計 は、3D と 2D の両方の表面スキャンを実行して、あらゆる表面のナノスケールからマクロスケールの形状を測定できるため、幅広い使いやすさを提供します。
カテゴリー
- アプリケーションノート
- ブロック・オン・リングトライボロジー
- 腐食トライボロジー
- 摩擦試験|摩擦係数
- 高温機械試験
- 高温トライボロジー
- 湿度・ガス トライボロジー
- 湿度機械試験
- 圧痕|クリープとリラクゼーション
- 圧痕|破壊靭性
- 圧痕|硬度・弾性率
- 圧痕|紛失と保管
- 圧痕|応力と歪み
- 圧痕|降伏強度と疲労の関係
- ラボラトリーテスト
- リニアトライボロジー
- 液体機械試験
- 液状トライボロジー
- 低温トライボロジー
- メカニカルテスト
- プレスリリース
- プロフィロメトリー|平坦度・反り率
- プロフィロメトリー|幾何学と形状
- プロフィロメトリー|粗さと仕上がり
- プロフィロメトリー|段差の高さと厚み
- プロフィロメトリー|テクスチャーとグレーン
- プロフィロメトリー|体積・面積
- プロフィロメトリーテスト
- リング・オン・リング トライボロジー
- 回転トライボロジー
- スクラッチテスト|接着剤の不具合について
- スクラッチテスト|コヒーシブフェール
- スクラッチテスト|マルチパス摩耗
- スクラッチテスト|スクラッチハードネス
- スクラッチテスト トライボロジー
- トレードショー
- トライボロジー試験
- 未分類
月別アーカイブ
- 2022年7月
- 2022年7月
- 2022年7月
- 2022年7月
- 2022年7月
- 2022年7月
- 2022年7月
- 2022年7月
- 2022年7月
- 2022年7月
- 2022年7月
- 2022年7月
- 2022年7月
- 2022年7月
- 2022年7月
- 2022年7月
- 2022年7月
- 2022年7月
- 2022年7月
- 2022年7月
- 2022年7月
- 2022年7月
- 2022年7月
- 2022年7月
- 2022年7月
- 2022年7月
- 2022年7月
- 2022年7月
- 2022年7月
- 2022年7月
- 2022年7月
- 2022年7月
- 2022年7月
- 2022年7月
- 2022年7月
- 2022年7月
- 2022年7月
- 2022年7月
- 2022年7月
- 2022年7月
- 2022年7月
- 2022年7月
- 2022年7月
- 2022年7月
- 2022年7月
- 2022年7月
- 2022年7月
- 2022年7月
- 2022年7月
- 2022年7月
- 2022年7月
- 2022年7月
- 2022年7月
- 2022年7月
- 2022年7月
- 2022年7月
- 2022年7月
- 2022年7月
- 2022年7月
- 2022年7月
- 2022年7月
- 2022年7月
- 2022年7月
- 2022年7月
- 2022年7月
- 2022年7月
- 2022年7月
- 2022年7月
- 2022年7月
- 2022年7月
- 2022年7月
- 2022年7月
- 2022年7月
- 2022年7月
- 2022年7月
- 2022年7月
- 2022年7月
- 2022年7月
- 2022年7月
- 2022年7月
- 2022年7月
- 2022年7月
- 2022年7月
- 2022年7月
- 2022年7月
- 2022年7月
- 2022年7月
- 2022年7月
- 2022年7月
- 2022年7月
- 2022年7月
- 2022年7月
- 2022年7月
- 2022年7月
- 2022年7月
- 2022年7月
- 2022年7月
- 2022年7月
- 2022年7月
- 2022年7月
- 2022年7月
- 2022年7月
- 2022年7月
- 2022年7月
- 2022年7月
- 2022年7月
- 2022年7月
- 2022年7月
- 2022年7月
- 2022年7月
- 2022年7月
- 2022年7月
- 2022年7月
- 2022年7月
- 2022年7月
- 2022年7月
- 2022年7月
- 2022年7月
- 2022年7月
- 2022年7月
- 2022年7月
- 2022年7月
- 2022年7月
- 2022年7月
- 2022年7月
- 2022年7月
- 2022年7月
- 2022年7月
- 2022年7月
- 2022年7月
- 2022年7月
- 2022年7月
- 2022年7月
- 2022年7月
- 2022年7月