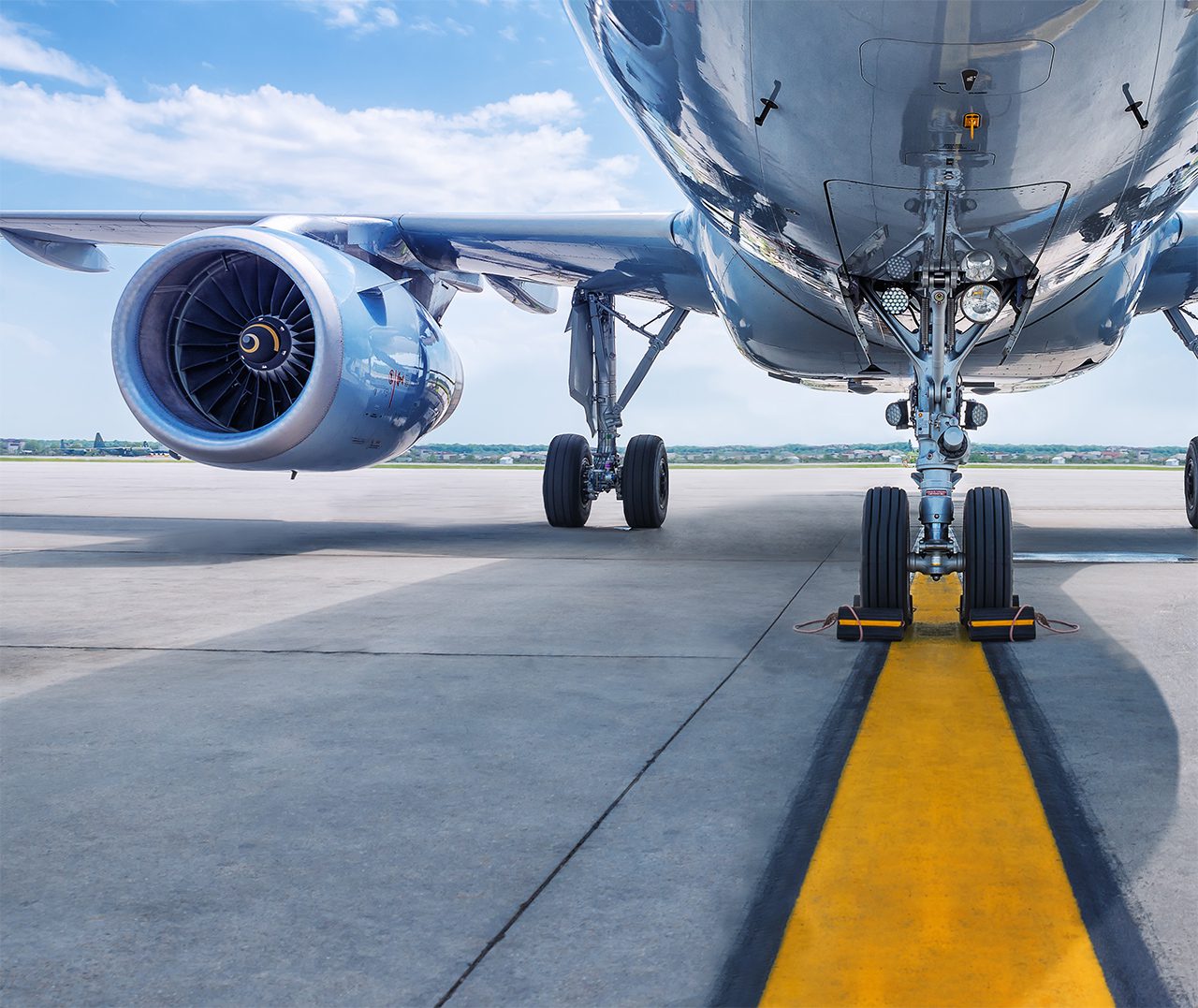
Fretting Wear Evaluation
FRETTING WEAR EVALUATION

Author:
Duanjie Li, PhD
Revised by
Jocelyn Esparza

INTRODUCTION
Fretting is “a special wear process that occurs at the contact area between two materials under load and subject to minute relative motion by vibration or some other force.” When machines are in operation, vibrations inevitably occur in joints that are bolted or pinned, between components that are not intended to move, and in oscillating couplings and bearings. The amplitude of such relative sliding motion is often in the order of micrometers to millimeters. Such repetitive low-amplitude motion causes serious localized mechanical wear and material transfer at the surface, which may lead to reduced production efficiency, machine performance or even damage to the machine.
Importance of Quantitative
Fretting Wear Evaluation
Fretting wear often involves several complex wear mechanisms taking place at the contact surface, including two-body abrasion, adhesion and/or fretting fatigue wear. In order to understand the fretting wear mechanism and select the best material for fretting wear protection, reliable and quantitative fretting wear evaluation is needed. The fretting wear behavior is significantly influenced by the work environment, such as displacement amplitude, normal loading, corrosion, temperature, humidity and lubrication. A versatile tribometer that can simulate the different realistic work conditions will be ideal for fretting wear evaluation.
Steven R. Lampman, ASM Handbook: Volume 19: Fatigue and Fracture
http://www.machinerylubrication.com/Read/693/fretting-wear
MEASUREMENT OBJECTIVE
In this study, we evaluated the fretting wear behaviors of a stainless steel SS304 sample at different oscillation speeds and temperatures to showcase the capacity of NANOVEA T50 Tribometer in simulating the fretting wear process of metal in a well-controlled and monitored manner.
NANOVEA
T50
TEST CONDITIONS
The fretting wear resistance of a stainless steel SS304 sample was evaluated by NANOVEA Tribometer using Linear Reciprocating Wear Module. A WC (6 mm diameter) ball was used as the counter material. The wear track was examined using a NANOVEA 3D non-contact profiler.
The fretting test was performed at room temperature (RT) and 200 °C to study the effect of high temperature on the fretting wear resistance of the SS304 sample. A heating plate on the sample stage heated up the sample during the fretting test at 200 °C. The wear rate, K, was evaluated using the formula K=V/(F×s), where V is the worn volume, F is the normal load, and s is the sliding distance.
Please note that a WC ball as a counter material was used as an example in this study. Any solid material with different shapes and surface finish can be applied using a custom fixture to simulate the actual application situation.
TEST PARAMETERS
of the wear measurements

RESULTS & DISCUSSION
The 3D wear track profile allows direct and accurate determination of the wear track volume loss calculated by the NANOVEA Mountains analysis software.
The reciprocating wear test at a low speed of 100 rpm and room temperature exhibits a small wear track of 0.014 mm³. In comparison, the fretting wear test carried out at a high speed of 1000 rpm creates a substantially larger wear track with a volume of 0.12 mm³. Such an accelerated wear process may be attributed to the high heat and intense vibration generated during the fretting wear test, which promotes oxidation of the metallic debris and results in severe three-body abrasion. The fretting wear test at an elevated temperature of 200 °C forms a larger wear track of 0.27 mm³.
The fretting wear test at 1000 rpm has a wear rate of 1.5×10-4 mm³/Nm, which is nearly nine times compared to that in a reciprocating wear test at 100 rpm. The fretting wear test at an elevated temperature further accelerates the wear rate to 3.4×10-4 mm³/Nm. Such a significant difference in wear resistance measured at different speeds and temperatures shows the importance of proper simulations of fretting wear for realistic applications.
Wear behavior can change drastically when small changes in testing conditions are introduced into the tribosystem. The versatility of the NANOVEA Tribometer allows measuring wear under various conditions, including high temperature, lubrication, corrosion and others. The accurate speed and position control by the advanced motor enables users to perform the wear test at speeds ranging from 0.001 to 5000 rpm, making it an ideal tool for research/testing labs to investigate the fretting wear in different tribological conditions.
Fretting wear tracks at various conditions
under the optical microscope

3D WEAR TRACKs PROFILES
provide more insight in fundamental understanding
of the fretting wear mechanism
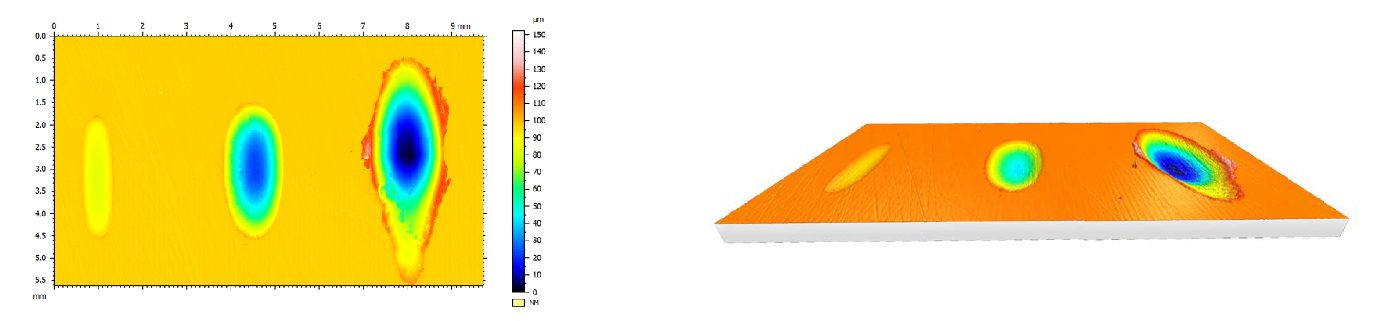
RESULT SUMMARY OF WEAR TRACKS
measured using different test parameters

CONCLUSION
In this study, we showcased the capacity of the NANOVEA Tribometer in evaluating the fretting wear behavior of a stainless steel SS304 sample in a well-controlled and quantitative manner.
The test speed and temperature play critical roles in the fretting wear resistance of the materials. The high heat and intense vibration during the fretting resulted in substantially accelerated wear of the SS304 sample by close to nine times. The elevated temperature of 200 °C further increased the wear rate to 3.4×10-4 mm3/Nm.
The versatility of the NANOVEA Tribometer makes it an ideal tool for measuring fretting wear under various conditions, including high temperature, lubrication, corrosion and others.
NANOVEA Tribometers offer precise and repeatable wear and friction testing using ISO and ASTM compliant rotative and linear modes, with optional high temperature wear, lubrication and tribo-corrosion modules available in one pre-integrated system. Our unmatched range is an ideal solution for determining the full scope of tribological properties of thin or thick, soft or hard coatings, films and substrates.
NOW, LET'S TALK ABOUT YOUR APPLICATION
分类
- Application Notes
- Block on Ring Tribology
- Corrosion Tribology
- Friction Testing | Coefficient of Friction
- High Temperature Mechanical Testing
- High Temperature Tribology
- Humidity and Gases Tribology
- Humidity Mechanical Testing
- Indentation | Creep and Relaxation
- Indentation | Fracture Toughness
- Indentation | Hardness and Elastic
- Indentation | Loss and Storage
- Indentation | Stress vs Strain
- Indentation | Yield Strength and Fatigue
- Laboratory Testing
- Linear Tribology
- Liquid Mechanical Testing
- Liquid Tribology
- Low Temperature Tribology
- Mechanical Testing
- Press Release
- Profilometry | Flatness and Warpage
- Profilometry | Geometry and Shape
- Profilometry | Roughness and Finish
- Profilometry | Step Height and Thickness
- Profilometry | Texture and Grain
- Profilometry | Volume and Area
- Profilometry Testing
- Ring on Ring Tribology
- Rotational Tribology
- Scratch Testing | Adhesive Failure
- Scratch Testing | Cohesive Failure
- Scratch Testing | Multi-Pass Wear
- Scratch Testing | Scratch Hardness
- Scratch Testing Tribology
- Tradeshow
- Tribology Testing
- Uncategorized
归档
- 2023年9 月
- 2023年8 月
- 2023年6 月
- 2023年5 月
- 2022年7 月
- 2022年5 月
- 2022年4 月
- 2022年1 月
- 2021年12 月
- 2021年11 月
- 2021年10 月
- 2021年9 月
- 2021年8 月
- 2021年7 月
- 2021年6 月
- 2021年5 月
- 2021年3 月
- 2021年2 月
- 2020年12 月
- 2020年11 月
- 2020年10 月
- 2020年9 月
- 2020年7 月
- 2020年5 月
- 2020年4 月
- 2020年3 月
- 2020年2 月
- 2020年1 月
- 2019年11 月
- 2019年10 月
- 2019年9 月
- 2019年8 月
- 2019年7 月
- 2019年6 月
- 2019年5 月
- 2019年4 月
- 2019年3 月
- 2019年1 月
- 2018年12 月
- 2018年11 月
- 2018年10 月
- 2018年9 月
- 2018年7 月
- 2018年6 月
- 2018年5 月
- 2018年4 月
- 2018年3 月
- 2018年2 月
- 2017年11 月
- 2017年10 月
- 2017年9 月
- 2017年8 月
- 2017年6 月
- 2017年5 月
- 2017年4 月
- 2017年3 月
- 2017年2 月
- 2017年1 月
- 2016年11 月
- 2016年10 月
- 2016年8 月
- 2016年7 月
- 2016年6 月
- 2016年5 月
- 2016年4 月
- 2016年3 月
- 2016年2 月
- 2016年1 月
- 2015年12 月
- 2015年11 月
- 2015年10 月
- 2015年9 月
- 2015年8 月
- 2015年7 月
- 2015年6 月
- 2015年5 月
- 2015年4 月
- 2015年3 月
- 2015年2 月
- 2015年1 月
- 2014年11 月
- 2014年10 月
- 2014年9 月
- 2014年8 月
- 2014年7 月
- 2014年6 月
- 2014年5 月
- 2014年4 月
- 2014年3 月
- 2014年2 月
- 2014年1 月
- 2013年12 月
- 2013年11 月
- 2013年10 月
- 2013年9 月
- 2013年8 月
- 2013年7 月
- 2013年6 月
- 2013年5 月
- 2013年4 月
- 2013年3 月
- 2013年2 月
- 2013年1 月
- 2012年12 月
- 2012年11 月
- 2012年10 月
- 2012年9 月
- 2012年8 月
- 2012年7 月
- 2012年6 月
- 2012年5 月
- 2012年4 月
- 2012年3 月
- 2012年2 月
- 2012年1 月
- 2011年12 月
- 2011年11 月
- 2011年10 月
- 2011年9 月
- 2011年8 月
- 2011年7 月
- 2011年6 月
- 2011年5 月
- 2010年11 月
- 2010年1 月
- 2009年4 月
- 2009年3 月
- 2009年1 月
- 2008年12 月
- 2008年10 月
- 2007年8 月
- 2006年7 月
- 2006年3 月
- 2005年1 月
- 2004年4 月