类别。轮廓测量测试

药用片剂表面粗糙度检测
药用片剂
使用三维轮廓仪测试粗糙度

作者。
Jocelyn Esparza
简介
片剂是当今最流行的药物剂量。每片都是由活性物质(产生药理作用的化学物质)和非活性物质(崩解剂、粘合剂、润滑剂、稀释剂——通常以粉末的形式)组合而成。活性和非活性物质然后被压缩或模压成固体。然后,根据制造商的规格,药片或涂层或非涂层。
为了有效,片剂涂层需要遵循片剂上压印的标识或字符的精细轮廓,它们需要足够稳定和坚固,以便在处理片剂的过程中存活下来,而且在涂层过程中不能导致片剂相互粘连。目前的片剂通常有一个多糖和聚合物为基础的涂层,其中包括颜料和增塑剂等物质。最常见的两种片剂包衣是薄膜包衣和糖衣。与糖衣相比,薄膜涂层不那么笨重,更耐用,而且在准备和应用时不那么费时。然而,薄膜涂料更难隐藏片剂的外观。
片剂包衣对于防潮、掩盖成分的味道以及使片剂更容易吞咽是必不可少的。更重要的是,片剂包衣能控制药物释放的位置和速度。
测量目标
在这个应用中,我们使用 NANOVEA光学分析器 和先进的Mountains软件来测量和量化各种名牌压制药丸(1个涂层和2个非涂层)的地形,以比较它们的表面粗糙度。
假设安非他命(涂层)由于具有保护性涂层,其表面粗糙度将最低。
NANOVEA
HS2000
测试条件
用Nanovea HS2000扫描了三个批次的名牌药用压片。
使用高速线传感器测量各种表面粗糙度参数,符合ISO 25178标准。
扫描区域
2 x 2 mm
侧面扫描分辨率
5 x 5 μm
扫描时间
4秒
样品

结果与讨论
在扫描片剂后,用先进的Mountains分析软件进行了表面粗糙度研究,计算出每个片剂的表面平均值、均方根值和最大高度。

计算出的数值支持这样的假设:由于有保护层包裹其成分,所以爱必妥的表面粗糙度较低。泰诺表明,在所有三种测量的药片中,泰诺的表面粗糙度最高。
制作了每块平板表面地形的2D和3D高度图,显示了测量到的高度分布。从五块平板中选出一块来代表每个品牌的身高地图。这些高度图是视觉检测外围表面特征(如凹坑或山峰)的好工具。

总结
在这项研究中,我们分析和比较了三种名牌压制药丸的表面粗糙度。Advil, Tylenol, 和Excedrin。事实证明,Advil的平均表面粗糙度最低。这可以归因于包裹药物的橙色涂层的存在。相比之下,Excedrin和Tylenol都没有涂层,但是,它们的表面粗糙度仍然彼此不同。事实证明,泰诺的平均表面粗糙度在所有研究的药片中是最高的。
使用 NANOVEA 使用带有高速线传感器的HS2000,我们能够在不到1分钟的时间内测量5片药。这可以证明对今天生产中数百个药片的质量控制测试很有用。
现在,让我们来谈谈你的申请
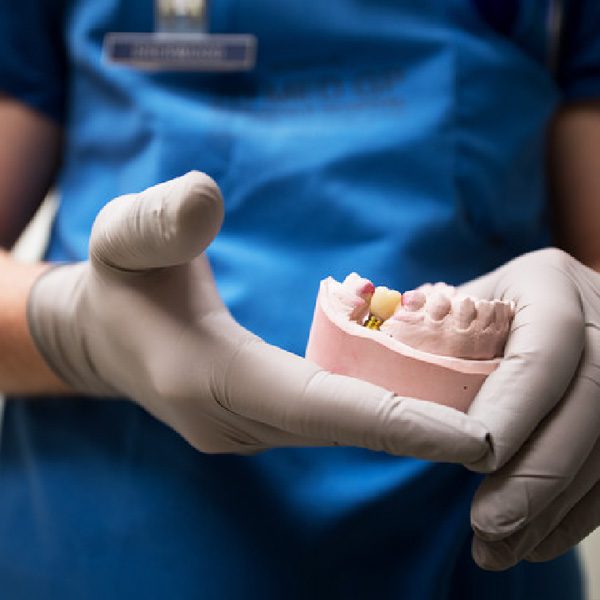
牙科工具。尺寸和表面粗糙度分析
简介
精确的尺寸和最佳的表面粗糙度对于牙科螺钉的功能至关重要。许多牙科螺钉尺寸需要高精度,例如半径、角度、距离和台阶高度。了解局部表面粗糙度对于插入人体内部的任何医疗工具或部件以最大限度地减少滑动摩擦也非常重要。
用于尺寸研究的非接触式轮廓测量
纳诺瓦 3D 非接触式轮廓仪 使用基于色光的技术来测量任何材料表面:透明、不透明、镜面、漫射、抛光或粗糙。与接触式探针技术不同,非接触式技术可以在狭小的区域内进行测量,并且不会由于尖端按压较软的塑料材料而导致变形而增加任何固有误差。与焦点变化技术相比,基于色光的技术还提供卓越的横向和高度精度。 Nanovea Profiler 可以直接扫描大型表面,无需缝合,并在几秒钟内对零件的长度进行轮廓分析。由于轮廓仪能够测量表面,无需任何复杂的算法来处理结果,因此可以测量纳米到宏观范围的表面特征和高表面角度。
测量目标
在此应用中,使用 Nanovea ST400 光学轮廓仪在单次测量中沿着平面和螺纹特征测量牙科螺钉。从平坦区域计算表面粗糙度,并确定螺纹特征的各种尺寸。
牙科螺丝样本分析 NANOVEA 光学轮廓仪。
分析牙科螺钉样品。
结果
三维表面
牙科螺钉的 3D 视图和假色视图显示了一个平坦区域,螺纹从两侧开始。它为用户提供了一个简单的工具,可以从不同角度直接观察螺钉的形态。从全扫描中提取平坦区域以测量其表面粗糙度。
2D 表面分析
还可以从表面提取线轮廓以显示螺钉的横截面图。轮廓分析和台阶高度研究用于测量螺钉上特定位置的精确尺寸。
结论
在此应用中,我们展示了 Nanovea 3D 非接触式轮廓仪在单次扫描中精确计算局部表面粗糙度和测量大尺寸特征的能力。
数据显示局部表面粗糙度为 0.9637 μm。螺纹之间的螺钉半径为 1.729 毫米,螺纹平均高度为 0.413 毫米。螺纹之间的平均角度被确定为61.3°。
这里显示的数据仅代表分析软件中可用的一部分计算结果。
编写者
李端杰博士、乔纳森·托马斯和皮埃尔·勒鲁
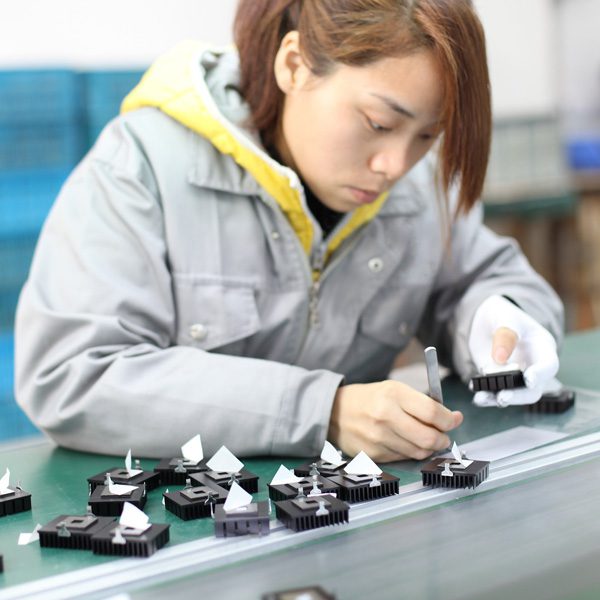
在线粗糙度检查
了解更多
非接触式轮廓仪对在线粗糙度检测的重要性
表面缺陷来源于材料加工和产品制造。在线表面质量检测可确保对最终产品进行最严格的质量控制。纳诺维亚酒店 3D 非接触式轮廓仪 利用具有独特功能的彩色共焦技术,无需接触即可确定样品的粗糙度。可安装多个轮廓仪传感器,同时监测产品不同区域的粗糙度和纹理。由分析软件实时计算的粗糙度阈值可作为快速可靠的通过/失败工具。
测量目标
在这项研究中,Nanovea粗糙度检测传送系统配备了一个点式传感器,用于检测丙烯酸和砂纸样品的表面粗糙度。我们展示了Nanovea非接触式轮廓仪在生产线上实时提供快速、可靠的在线粗糙度检测的能力。
结果和讨论
输送式轮廓仪系统可以在两种模式下工作,即触发模式和连续模式。如图2所示,在触发模式下,当样品在光学轮廓仪头下通过时,样品的表面粗糙度被测量。相比之下,连续模式可以不间断地测量连续样品的表面粗糙度,如金属板和织物。可以安装多个光学轮廓仪传感器来监测和记录不同样品区域的粗糙度。
在实时粗糙度检测测量过程中,软件窗口显示通过和失败告警,如图4和图5所示。当粗糙度值在给定的阈值内时,测量的粗糙度以绿色突出显示。然而,当测量的表面粗糙度超出设定的阈值范围时,高亮部分变成红色。这为用户提供了一个工具来确定产品表面光洁度的质量。
在下面的章节中,将使用两种类型的样品,如丙烯酸和砂纸来演示检测系统的触发和连续模式。
触发模式。亚克力样品的表面检查
如图1所示,一系列亚克力样品在传送带上排列并在光学轮廓仪头下移动。图6中的假彩色视图显示了表面高度的变化。如图6b所示,一些镜子般的成品亚克力样品已经被打磨,形成了粗糙的表面纹理。
当亚克力样品在光学轮廓仪头下以恒定的速度移动时,表面轮廓被测量,如图7和图8所示。同时计算出所测轮廓的粗糙度值,并与阈值进行比较。当粗糙度值超过设定的阈值时,就会启动红色故障警报,使用户能够立即发现并找到生产线上的缺陷产品。
连续模式。砂纸样品的表面检查
如图9所示,砂纸样品表面的表面高度图、粗糙度分布图和合格/不合格粗糙度阈值图。如表面高度图所示,砂纸样品在使用的部分有几个较高的峰值。图9C的调色板上的不同颜色代表了局部表面的粗糙度值。粗糙度图在砂纸样品的完整区域表现出均匀的粗糙度,而使用过的区域则以深蓝色突出显示,表明该区域的粗糙度值降低。可以设置一个合格/不合格的粗糙度阈值来定位这样的区域,如图9D所示。
当砂纸连续通过在线轮廓仪传感器下方时,实时的局部粗糙度值被计算和记录,如图10所示。根据设定的粗糙度阈值,在软件屏幕上显示合格/不合格警报,作为质量控制的一个快速和可靠的工具。对生产线上的产品表面质量进行现场检查,及时发现有缺陷的地方。
在这个应用中,我们已经证明了Nanovea传送带轮廓仪配备的光学非接触式轮廓仪传感器可以作为一个可靠的在线质量控制工具有效和高效地工作。
该检测系统可以安装在生产线上,就地监测产品的表面质量。粗糙度阈值作为判断产品表面质量的可靠标准,使用户能够及时发现有缺陷的产品。提供两种检测模式,即触发模式和连续模式,以满足对不同类型产品的检测要求。
这里显示的数据只代表了分析软件中的一部分计算结果。Nanovea轮廓仪几乎可以测量任何领域的表面,包括半导体、微电子、太阳能、纤维、光学、汽车、航空航天、冶金、加工、涂层、制药、生物医学、环境和其他许多领域。
现在,让我们来谈谈你的申请
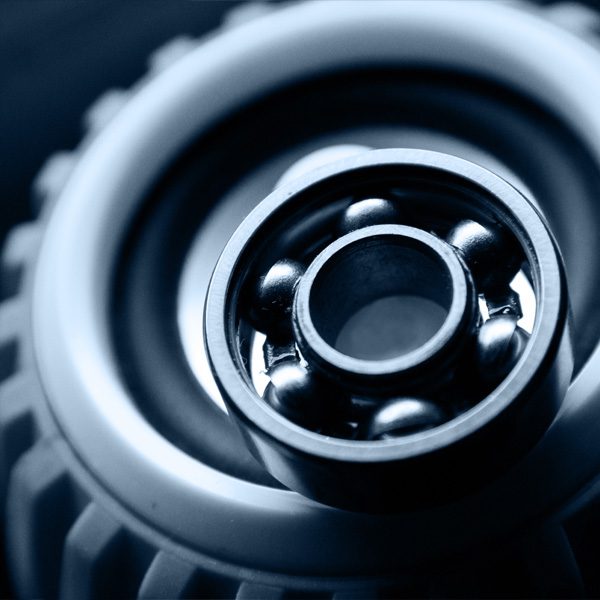
环-块磨损测试
块对环磨损评估的重要性
环块 (ASTM G77) 测试是一种广泛使用的技术,可评估材料在不同模拟条件下的滑动磨损行为,为特定摩擦学应用提供可靠的材料对排名。
测量目标
在这个应用中,Nanovea机械测试仪测量不锈钢SS304和铝Al6061金属合金样品的YS和UTS。样品的YS和UTS值是公认的,这表明Nanovea的压痕方法是可靠的。
Nanovea 的摩擦磨损试验机使用 Block-on-Ring 模块评估了 S-10 环上 H-30 块的滑动磨损行为。 H-30 块由硬度为 30HRC 的 01 工具钢制成,而 S-10 环由表面硬度为 58 至 63 HRC 的 4620 型钢制成,环直径约为 34.98 毫米。在干燥和润滑的环境中进行块环测试,以研究对磨损行为的影响。润滑测试是在 USP 重矿物油中进行的。使用 Nanovea 的磨损轨迹进行检查 3D非接触式轮廓仪。测试参数总结于表1中。磨损率(K)采用公式K=V/(F×s)评估,其中V为磨损体积,F为法向载荷,s为滑动距离。
结果和讨论
图 2 比较了干燥和润滑环境下环块测试的摩擦系数 (COF)。该块在干燥环境中的摩擦力明显大于润滑环境中的摩擦力。 COF
在前 50 转的磨合期间,COF 会波动,并在其余 200 转磨损测试中达到约 0.8 的恒定 COF。相比之下,在 USP 重矿物油润滑中进行的环块测试在整个 500,000 转磨损测试中始终表现出 0.09 的低 COF。该润滑剂可将表面之间的摩擦系数显着降低约 90 倍。
图3和图4显示了干磨损和润滑磨损试验后块上磨损疤痕的光学图像和截面2D轮廓。磨损轨迹量和磨损率如表2所示。在较低转速72 rpm、200转的干磨损试验下,钢块表现出9.45 mm˙的大磨损疤痕体积。相比之下,在矿物油润滑剂中以197转/分钟、50转的更高转速进行的磨损试验,产生的磨损轨迹体积很小,为0.03 mm˙。
ÿgure 3中的图像显示在干燥条件下的试验中发生了严重磨损,而润滑磨损试验中则发生了轻微磨损。干磨损试验过程中产生的高温和强烈振动促进了金属碎片的氧化,导致严重的三体磨损。在润滑测试中,矿物油减少摩擦,冷却接触表面,并将磨损过程中产生的磨料碎片运输掉。这导致磨损率降低了signiÿcant ~8×10。在不同的环境中耐磨性的这种巨大差异表明了在实际使用条件下进行适当滑动磨损模拟的重要性。
当试验条件发生微小变化时,磨损行为可能发生剧烈变化。Nanovea的摩擦计的多功能性允许在高温、润滑和摩擦腐蚀条件下进行磨损测量。精确的速度和位置控制的先进电机使磨损测试执行的速度从0.001到5000 rpm,使其成为研究/测试实验室的理想工具,以调查磨损在不同的摩擦学条件。
用Nanovea的非接触光学proÿlometer检测样品的表面状况。图5显示了磨损试验后环的表面形貌。为了更好地呈现滑动磨损过程中产生的表面形貌和粗糙度,去掉了圆柱形。Signiÿcant在200转的干磨损试验中,由于三体磨损过程发生了表面粗糙化。干磨损试验后的块体和环体的粗糙度Ra分别为14.1和18.1 μ m,而在较高速度下进行50万转长期润滑磨损试验后的粗糙度Ra分别为5.7和9.1 μ m。该试验证明了活塞环-气缸接触处适当润滑的重要性。严重的磨损会迅速损坏没有润滑的接触面,导致使用质量不可逆的恶化,甚至导致发动机损坏。
结论
在本研究中,我们展示了如何使用 Nanovea 的摩擦计来评估钢金属对的滑动磨损行为,并使用遵循 ASTM G77 标准的环上块模块。润滑剂在材料对的磨损性能中起着至关重要的作用。矿物油可将 H-30 块的磨损率降低约 8×10ˆ 倍,将 COF 降低约 90 倍。 Nanovea 摩擦计的多功能性使其成为测量各种润滑、高温和摩擦腐蚀条件下磨损行为的理想工具。
Nanovea 的摩擦试验机使用符合 ISO 和 ASTM 的旋转和线性模式提供精确且可重复的磨损和摩擦测试,并在一个预集成系统中提供可选的高温磨损、润滑和摩擦腐蚀模块。 Nanovea 无与伦比的系列是确定薄或厚、软或硬涂层、薄膜和基材的全方位摩擦学特性的理想解决方案。
现在,让我们来谈谈你的申请
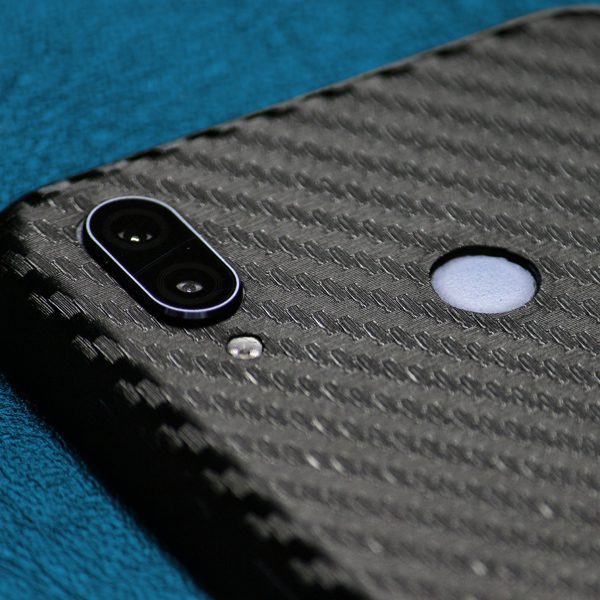
使用三维轮廓测量法的复合材料分析
非接触式轮廓测量法对复合材料的重要性
尽量减少缺陷是至关重要的,这样复合材料在加固应用中才会尽可能的强大。作为一种各向异性的材料,关键是编织方向的一致性,以保持高性能的可预测性。复合材料是强度与重量比最高的材料之一,在某些情况下,它比钢更强。重要的是要限制复合材料的表面暴露面积,以减少化学脆弱性和热膨胀效应。轮廓测量法的表面检测对于复合材料的质量控制生产至关重要,以确保在长期使用中的强大性能。
纳诺维亚的 3D 非接触式轮廓仪 与其他表面测量技术(例如接触式探针或干涉测量法)不同。我们的轮廓仪使用轴向色差来测量几乎任何表面,开放式样品台允许测量任何尺寸的样品,无需准备。在表面轮廓测量过程中获得纳米到宏观测量,样品反射率或吸收的影响为零。我们的轮廓仪可以轻松测量任何材料:透明、不透明、镜面、漫射、抛光和粗糙,具有无需软件操作即可测量高表面角度的先进能力。非接触式轮廓仪技术提供了理想且用户友好的功能,可最大限度地进行复合材料表面研究;以及 2D 和 3D 组合功能的优势。
测量目标
本应用中使用的Nanovea HS2000L轮廓仪测量了两个编织的碳纤维复合材料的表面。表面粗糙度、编织长度、各向同性、分形分析和其他表面参数被用来描述复合材料的特征。测量的区域是随机选择的,并假定足够大,可以使用Nanovea强大的表面分析软件比较属性值。
结果和讨论
表面分析
各向同性显示了编织的方向性,以确定预期的属性值。我们的研究表明,双向复合材料是~60%的各向同性,正如预期。同时,单向复合材料是~13%的各向同性,由于强大的单纤维路径方向纤维。
编织尺寸决定了复合材料中使用的纤维的包装和宽度的一致性。我们的研究表明,我们可以很容易地测量织造尺寸,精确到微米,以确保零件的质量。


主导波长的纹理分析表明两种复合材料的股线尺寸都是4.27微米厚。纤维表面的分形维度分析决定了光滑度,以寻找纤维在基体中的固定程度。单向纤维的分形尺寸高于双向纤维,这可能影响复合材料的加工。
总结
在这个应用中,我们已经表明Nanovea HS2000L非接触式轮廓仪可以精确地描述复合材料的纤维表面。我们用高度参数、各向同性、纹理分析和距离测量等方法区分了碳纤维的编织类型的差异。
我们的轮廓仪表面测量精确和快速地减轻了复合材料的损坏,这减少了零件的缺陷,最大限度地提高了复合材料的能力。Nanovea的3D轮廓仪速度范围从<1mm/s到500mm/s,适合于研究应用到高速检查的需要。Nanovea的轮廓仪是解决方案
以满足任何复合测量的需要。
现在,让我们来谈谈你的申请
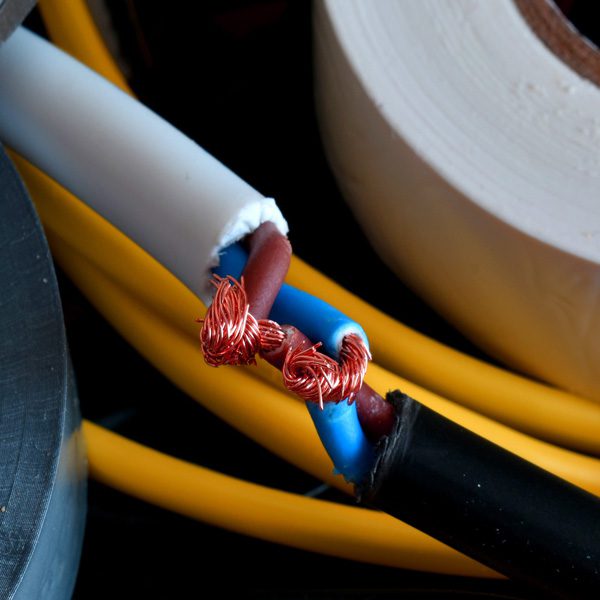
表面处理过的铜线的磨损和划痕评估
铜线的磨损和划痕评估的重要性
自电磁铁和电报发明以来,铜在电线方面的应用有着悠久的历史。由于铜的耐腐蚀性、可焊性以及在高达150℃的高温下的性能,铜线被广泛用于电子设备,如面板、仪表、计算机、商业机器和电器。所有开采出来的铜大约有一半是用来制造电线和电缆导体的。
铜线的表面质量对应用服务性能和使用寿命至关重要。铜线中的微观缺陷可能导致过度磨损、裂纹的产生和扩展、导电性下降和焊接性不足。适当的铜线表面处理可以消除拉丝过程中产生的表面缺陷,提高耐腐蚀、耐刮擦和耐磨性。许多使用铜线的航空应用需要控制行为以防止意外的设备故障。为了正确评估铜线表面的耐磨性和耐刮擦性,需要进行可量化和可靠的测量。
测量目标
在这个应用中,我们模拟了不同铜线表面处理的受控磨损过程。 划痕测试 测量导致处理过的表面层失效所需的负载。这项研究展示了 Nanovea 摩擦仪 和 机械测试仪 作为电线评估和质量控制的理想工具。
测试过程和程序
通过 Nanovea 摩擦磨损试验机使用线性往复磨损模块评估两种不同表面处理的铜线(线 A 和线 B)的摩擦系数 (COF) 和耐磨性。 Al2O3 球(直径 6 毫米)是本应用中使用的计数器材料。使用 Nanovea 的磨损轨迹进行检查 3D非接触式轮廓仪。测试参数总结于表 1 中。
本次研究以Al₂O₃球为例进行了说明。任何具有不同形状和表面光洁度的固体材料都可以使用定制夹具来模拟实际的应用情况。
结果和讨论
铜线的磨损。
图2显示了铜线在磨损测试中的COF变化。A线在整个磨损试验过程中显示出稳定的COF约为0.4,而B线在头100转时显示出约0.35的COF,并逐渐增加到约0.4。
图3比较了测试后铜线的磨损轨迹。Nanovea公司的3D非接触式轮廓仪对磨损痕迹的详细形貌进行了出色的分析。通过提供对磨损机理的基本理解,可以直接和准确地确定磨损轨迹体积。经过600转的磨损试验,B线表面有明显的磨损痕迹损伤。剖面仪3D视图显示,B线的表面处理层被完全去除,大大加快了磨损过程。这在铜基板暴露的B线上留下了平坦的磨损痕迹。这可能导致使用B线的电气设备的寿命显著缩短。相比之下,A线的磨损相对较轻,其表面的磨损痕迹较浅。在相同条件下,A线表面处理层不像B线表面处理层那样被去除。
铜线表面的耐刮擦性。
图4显示了测试后导线上的划痕。线材A的保护层表现出非常好的抗划痕能力。相比之下,B线的保护层在约1.0N的载荷下失效。这些线的耐刮擦性有如此大的差异,这有助于它们的磨损性能,其中A线拥有大大增强的耐磨性。图5所示的划痕测试中法向力、COF和深度的演变提供了关于测试中涂层失效的更多信息。
总结
在这项对照研究中,我们展示了Nanovea的摩擦仪对表面处理过的铜线的耐磨性进行定量评估,以及Nanovea的机械测试仪对铜线的耐刮擦性进行可靠评估。铜线的表面处理在其使用寿命中对三者的机械性能起着关键作用。电线A的适当表面处理大大增强了耐磨性和耐刮擦性,这对粗糙环境中的电线的性能和寿命至关重要。
Nanovea的摩擦仪使用符合ISO和ASTM标准的旋转和线性模式,提供精确和可重复的磨损和摩擦测试,在一个预集成的系统中可以选择高温磨损、润滑和三相腐蚀模块。Nanovea无与伦比的范围是确定薄或厚、软或硬的涂层、薄膜和基材的全部摩擦学特性的理想解决方案。
现在,让我们来谈谈你的申请
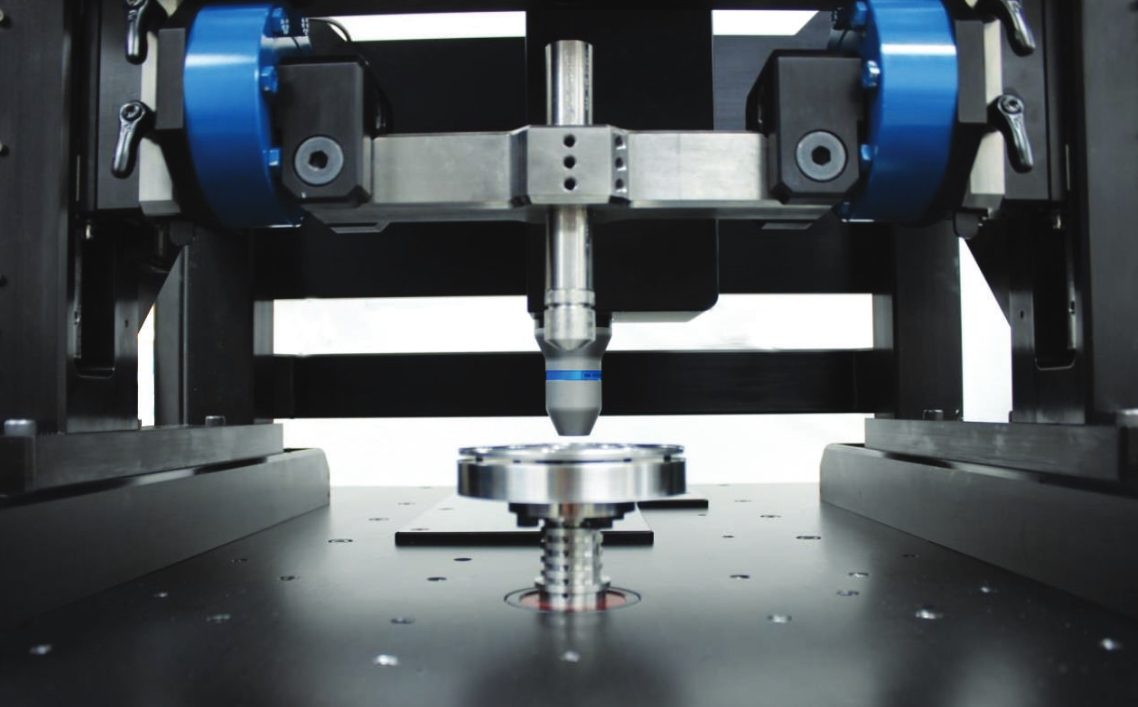
动态负载摩擦学
动态负载摩擦学
简介
磨损几乎发生在每一个工业部门,并造成了约0.75%的GDP成本1。摩擦学研究对于提高生产效率、应用性能以及保护材料、能源和环境至关重要。在广泛的摩擦学应用中,振动和振荡不可避免地发生。过度的外部振动加速了磨损过程,降低了服务性能,导致机械部件出现灾难性的故障。
传统的死荷载摩擦仪通过质量砝码施加正常载荷。这样的加载技术不仅将加载选项限制在一个恒定的负载上,而且在高负载和高速度下产生强烈的不可控振动,导致磨损行为评估的局限性和不一致性。可靠地评估受控振荡对材料磨损行为的影响,对于不同工业应用中的研发和质量控制是可取的。
Nanovea 突破性的高负载 摩擦仪 具有动态负载控制系统,最大负载能力为 2000 N。先进的气动压缩空气加载系统使用户能够评估材料在高正常载荷下的摩擦学行为,并具有抑制磨损过程中产生的不良振动的优点。因此,可以直接测量负载,无需旧设计中使用的缓冲弹簧。并联电磁体振荡加载模块可施加良好控制的振荡,所需振幅高达 20 N,频率高达 150 Hz。
摩擦力是直接根据施加到上支架的侧向力进行高精度测量的。现场监测位移,从而深入了解测试样品磨损行为的演变。受控振荡载荷下的磨损测试还可以在腐蚀、高温、潮湿和润滑环境中进行,以模拟摩擦学应用的真实工作条件。集成高速 非接触式轮廓仪 在几秒钟内自动测量磨损轨迹形态和磨损量。
测量目标
在这项研究中,我们展示了Nanovea T2000动态负载摩擦仪在研究不同涂层和金属样品在受控振荡负载条件下的摩擦学行为的能力。
测试程序
通过Nanovea T2000摩擦仪和传统的死负荷摩擦仪,按照ASTM G992的规定,使用销轴在盘上的设置,评估和比较了300微米厚的耐磨涂层的摩擦学行为,例如摩擦系数,COF和耐磨性。
通过 Nanovea T2000 摩擦试验机的动态负载摩擦学模式,对受控振荡下的 6 mm Al203 球的单独 Cu 和 TiN 涂层样品进行了评估。
测试参数汇总于表1。
集成的三维轮廓仪配备了线传感器,在测试后自动扫描磨损轨迹,在几秒钟内提供最准确的磨损量测量。
结果和讨论
气动负载系统与死负载系统
使用Nanovea T2000摩擦仪对耐磨涂层的摩擦学行为与传统的死负荷(DL)摩擦仪进行了比较。图2显示了涂层COF的变化。我们观察到涂层在磨损测试中表现出了相当的COF值~0.6。然而,图3中不同位置的20个横截面图表明,在死负荷系统下,涂层经历了更严重的磨损。
在高负荷和高速度下,死负载系统的磨损过程产生了强烈的振动。接触面的巨大集中压力与高滑动速度相结合,产生大量的重量和结构振动,导致加速磨损。传统的死负荷摩擦仪使用质量砝码来施加负荷。这种方法在较低的接触载荷和温和的磨损条件下是可靠的;然而,在较高的载荷和速度的侵蚀性磨损条件下,显著的振动导致砝码反复弹跳,造成不均匀的磨损轨迹,导致不可靠的摩擦学评估。计算出的磨损率为8.0±2.4 x 10-4 mm3/N m,显示出高磨损率和大的标准偏差。
Nanovea T2000摩擦仪设计有一个动态控制负载系统,以抑制振荡。它用压缩空气施加正常载荷,最大限度地减少了磨损过程中产生的不必要的振动。此外,主动闭环加载控制确保在整个磨损测试过程中施加恒定的载荷,测针跟随磨损轨迹的深度变化。如图3a所示,测得的磨损轨迹轮廓明显更加一致,从而使磨损率低至3.4±0.5 x 10-4 mm3/N m。
图4所示的磨损轨迹分析证实了Nanovea T2000摩擦仪的气动压缩空气加载系统进行的磨损测试,与传统的死负荷摩擦仪相比,产生了更平滑、更一致的磨损轨迹。此外,Nanovea T2000摩擦仪在磨损过程中测量测针位移,进一步了解现场磨损行为的进展。
铜样品磨损的可控振荡
Nanovea T2000摩擦仪的平行振荡加载电磁铁模块使用户能够研究控制振幅和频率振荡对材料磨损行为的影响。如图6所示,Cu样品的COF被就地记录。在第一次330转的测量中,铜样品表现出恒定的COF~0.3,标志着在界面上形成了稳定的接触和相对平滑的磨损轨迹。随着磨损试验的继续,COF的变化表明磨损机制的变化。相比之下,在50N的振幅控制下的磨损试验表现出不同的磨损行为:COF在磨损过程开始时迅速增加,并在整个磨损试验中表现出明显的变化。COF的这种行为表明,在正常载荷中施加的振荡在接触处的不稳定滑动状态中起了作用。
图7比较了由集成非接触式光学轮廓仪测量的磨损轨迹形态。可以看出,在控制振荡幅度为5N的情况下,Cu样品表现出更大的磨损轨迹,体积为1.35 x 109 µm3,而在没有施加振荡的情况下,体积为5.03 x 108 µm3。受控振荡使磨损率明显加快了约2.7倍,显示了振荡对磨损行为的关键影响。
受控振荡对TiN涂层磨损的影响
图8中显示了TiN涂层样品的COF和磨损轨迹。从测试期间COF的演变来看,TiN涂层在振荡下表现出明显不同的磨损行为。在磨损试验开始时的磨合期后,TiN涂层显示出约0.3的恒定COF,这是由于TiN涂层和亚铝₃球之间界面的稳定滑动接触。然而,当TiN涂层开始失效时,氧化铝球穿透涂层并与下面的新钢基体滑动。同时在磨损轨道上产生大量坚硬的TiN涂层碎片,将稳定的双体滑动磨损变为三体磨损。材料耦合特性的这种变化导致了COF演化过程中的变化增加。强加的5N和10N振荡加速了TiN涂层的失效,从~400转到100转以下。在控制振荡下的磨损试验后,TiN涂层样品上较大的磨损痕迹与COF的这种变化是一致的。
Nanovea T2000摩擦磨损仪的先进气动加载系统与传统的死负载系统相比,拥有作为自然快速减震器的内在优势。与使用伺服电机和弹簧组合来施加负载的负载控制系统相比,气动系统的这种技术优势是真实的。正如本研究中所展示的那样,该技术确保了在高负荷下可靠和更好的控制磨损评估。此外,主动闭环加载系统可以在磨损测试期间将正常载荷改变为所需值,以模拟在制动系统中看到的实际应用。
我们已经表明,Nanovea T2000动态负载摩擦仪使用户能够定量评估材料在不同控制振荡条件下的摩擦学行为,而不是在测试过程中受到不受控制的振动条件的影响。振动在金属和陶瓷涂层样品的磨损行为中起着重要作用。
平行电磁铁振荡加载模块以设定的振幅和频率提供精确控制的振荡,使用户能够模拟现实生活条件下的磨损过程,而环境振动往往是一个重要因素。在磨损过程中存在强加的振荡,铜和TiN涂层样品的磨损率都大大增加。原地测量的摩擦系数和测针位移的变化是摩擦学应用中材料性能的重要指标。集成的三维非接触式轮廓仪提供了一种工具,可以在几秒钟内精确测量磨损量并分析磨损痕迹的详细形态,为从根本上了解磨损机制提供更多的见解。
T2000配备了一个自调谐、高质量和高扭矩的电机,有一个20位的内部速度和一个16位的外部位置编码器。它使摩擦仪能够提供一个无与伦比的转速范围,从0.01到5000rpm,可以以阶梯式跳跃或连续的速度变化。与使用底部扭矩传感器的系统相反,Nanovea摩擦仪使用顶部的高精度称重传感器来准确和单独测量摩擦力。
Nanovea摩擦仪提供精确和可重复的磨损和摩擦测试,使用符合ISO和ASTM标准的旋转和线性模式(包括4球、止推垫圈和环上块状测试),在一个预集成的系统中可选择高温磨损、润滑和三相腐蚀模块。Nanovea T2000无与伦比的范围是确定薄或厚、软或硬的涂层、薄膜和基材的全部摩擦学特性的理想解决方案。
现在,让我们来谈谈你的申请
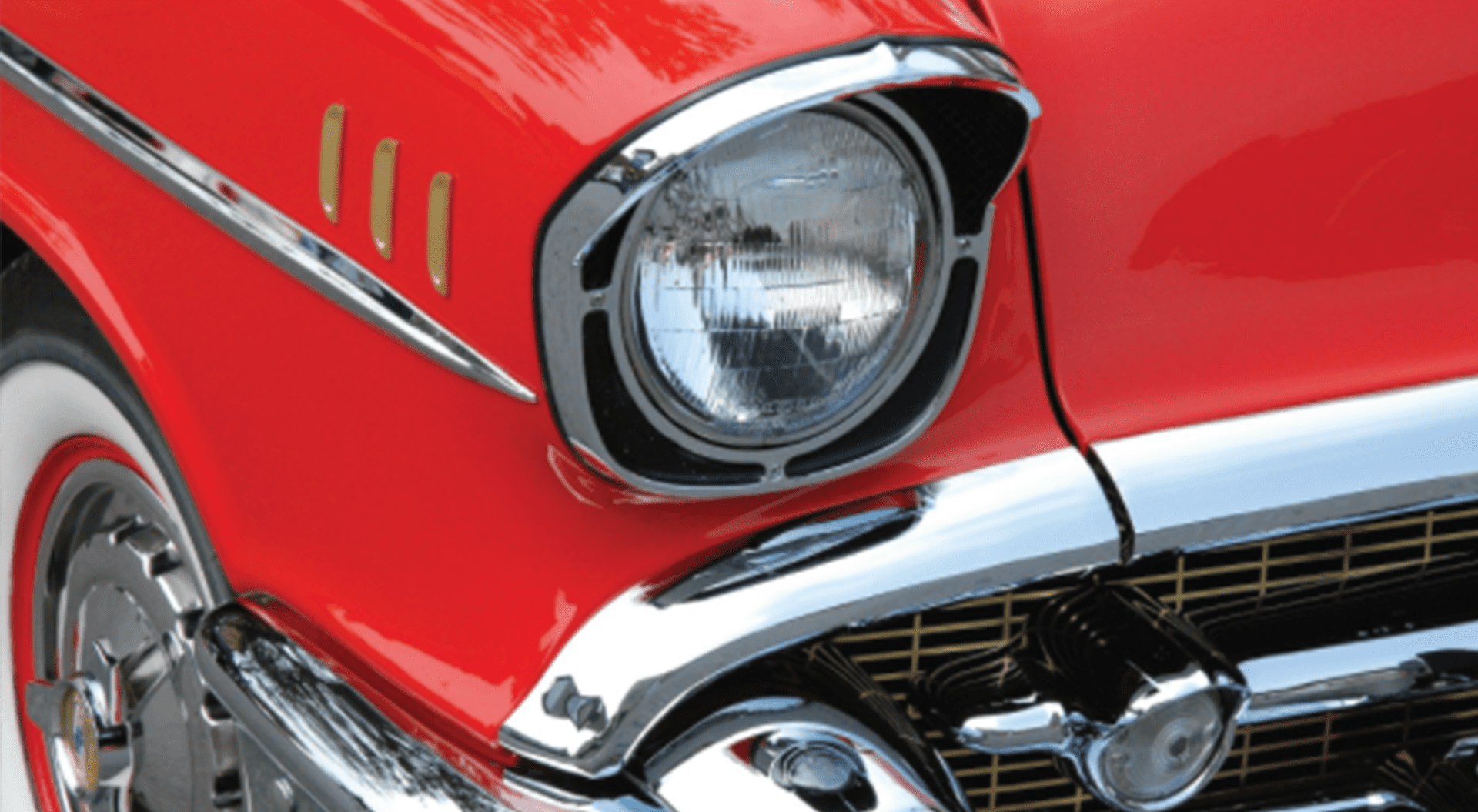
使用三维轮廓测量法的油漆橙皮纹理分析
使用三维轮廓测量法的油漆橙皮纹理分析
简介
基材上表面结构的大小和频率会影响到光泽涂料的质量。涂料桔皮纹理,以其外观命名,可以从基材影响和涂料应用技术中发展。纹理问题通常以波浪形、波长和对光泽涂层的视觉效果来量化。最小的纹理会导致光泽度下降,而较大的纹理则会在涂层表面产生可见的波纹。了解这些纹理的发展及其与基材和技术的关系是质量控制的关键。
轮廓测量法对于纹理测量的重要性
与用于测量光泽纹理的传统二维仪器不同,三维非接触式测量可快速提供用于了解表面特征的三维图像,并可快速调查感兴趣的区域。如果没有速度和三维审查,质量控制环境将完全依赖于二维信息,对整个表面的可预测性很低。了解三维纹理可以选择最佳的加工和控制措施。确保此类参数的质量控制在很大程度上依赖于可量化、可重现和可靠的检测。Nanovea三维非接触式 轮廓仪 Nanovea轮廓仪采用色度共焦技术,具有测量快速测量过程中发现的陡峭角度的独特能力。由于探头接触、表面变化、角度或反射率等原因,其他技术无法提供可靠数据,而Nanovea轮廓仪却能成功解决这些问题。
测量目标
在这个应用中,Nanovea HS2000L测量了亮光油漆的橙皮纹理。有无穷无尽的表面参数从三维表面扫描中自动计算出来。在这里,我们通过量化油漆橙皮纹理的特征来分析扫描的3D表面。
Nanovea HS2000L量化了橙皮漆的各向同性和高度参数。桔子皮纹理以94.4%的各向异性量化了随机图案方向。高度参数以24.84µm的高度差来量化纹理。
图4中的承载率曲线是深度分布的图形化表示。这是软件内的一个互动功能,允许用户查看不同深度的分布和百分比。图5中提取的剖面图给出了橙皮纹理的有用粗糙度值。144微米阈值以上的提取峰值显示了橘子皮的纹理。这些参数很容易调整为其他区域或感兴趣的参数。
总结
在这个应用中,Nanovea HS2000L 3D非接触轮廓仪精确地表征了光泽涂层上的橘皮纹理的地形和纳米细节。通过许多有用的测量(尺寸、粗糙度、表面纹理、形状形状、平面度、翘曲平面度、体积面积、阶跃高度等),可以快速识别和分析3D表面测量中感兴趣的区域。快速选择的二维截面提供了一套完整的表面测量资源的光泽纹理。特殊领域的兴趣可以进一步分析与集成AFM模块。Nanovea 3D轮廓仪的速度范围从<1毫米/秒到500毫米/秒,适用于研究应用,以满足高速检测的需要。Nanovea 3D轮廓仪有广泛的配置,以适合您的应用程序。
现在,让我们来谈谈你的申请

用非接触式轮廓仪对硬币的三维表面进行分析
非接触式轮廓测量法对钱币的重要性
货币在现代社会中具有很高的价值,因为它可以用来交换商品和服务。硬币和纸币在许多人的手中流通。实物货币的不断转移会造成表面变形。纳诺维亚的 3D 轮廓仪 扫描不同年份铸造的硬币的地形,以研究表面差异。
硬币特征很容易为公众所识别,因为它们是常见的物体。花一分钱就能了解 Nanovea 高级表面分析软件的优势:Mountains 3D。使用我们的 3D 轮廓仪收集的表面数据可以通过表面减法和 2D 轮廓提取对复杂的几何形状进行高级分析。使用受控掩模、印模或模具进行表面减法可比较制造工艺的质量,而轮廓提取可通过尺寸分析来识别公差。 Nanovea 的 3D 轮廓仪和 Mountains 3D 软件可研究看似简单物体(如便士)的亚微米形貌。
测量目标
使用Nanovea公司的高速线传感器扫描了五枚硬币的整个上表面。每枚硬币的内外半径都是用Mountains高级分析软件测量的。从感兴趣区域的每个硬币表面提取直接表面减法量化表面变形。
结果和讨论
三维表面
Nanovea HS2000轮廓仪仅用24秒就扫描了一个20mm x 20mm区域的400万个点,步长为10um x 10um,获得了一枚硬币的表面。下面是扫描的高度图和3D可视化图。3D视图显示了高速传感器捕捉肉眼无法察觉的小细节的能力。硬币表面有许多细小的划痕。研究了硬币在三维视图中看到的纹理和粗糙度。
提取了便士的轮廓,通过尺寸分析得到了边缘特征的内径和外径。外半径平均为9.500 mm ± 0.024,而内半径平均为8.960 mm ± 0.032。Mountains 3D可以对二维和三维数据源进行额外的尺寸分析,包括距离测量、台阶高度、平面度和角度计算。
图5显示了表面减法分析所关注的区域。2007年的便士被用作四个旧便士的参考表面。从2007年的分币表面减去,显示出有孔/峰的分币之间的差异。总的表面体积差是由孔/峰的体积相加得到的。均方根误差指的是分币表面相互之间的吻合程度。
总结
Nanovea的高速HS2000L扫描了5枚不同年份铸造的便士。Mountains 3D软件使用轮廓提取、尺寸分析和表面减法来比较每枚硬币的表面。该分析明确了硬币之间的内、外半径,同时直接比较了表面特征的差异。Nanovea的3D轮廓仪能够测量任何纳米级分辨率的表面,结合Mountains的3D分析能力,可能的研究和质量控制应用是无限的。
现在,让我们来谈谈你的申请
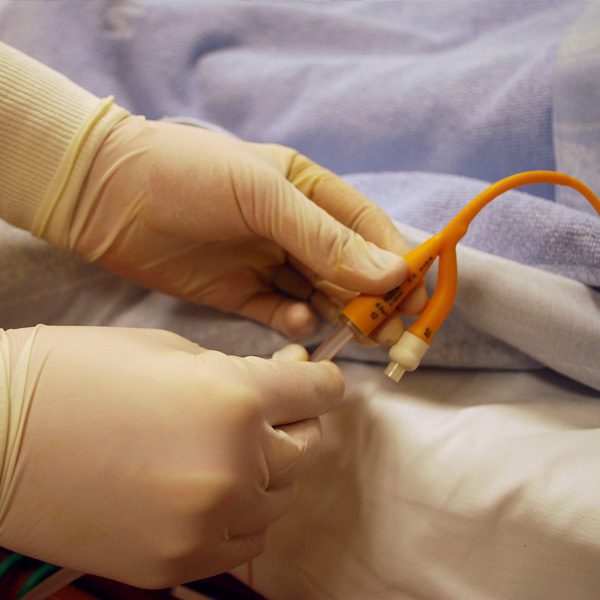
聚合物管材的尺寸和表面处理
聚合物管的尺寸和表面分析的重要性
由聚合物材料制成的管材通常用于许多行业,包括汽车、医疗、电气和许多其他类别。在这项研究中,使用 Nanovea 研究了由不同聚合材料制成的医用导管 3D 非接触式轮廓仪 来测量表面粗糙度、形态和尺寸。表面粗糙度对导管至关重要,因为导管的许多问题,包括感染、物理创伤和炎症都可能与导管表面有关。机械性能,如摩擦系数,也可以通过观察表面性能来研究。可以获得这些可量化的数据,以确保导管可以用于医疗应用。
与光学显微镜和电子显微镜相比,使用轴向色度的三维非接触式轮廓测量法在表征导管表面方面非常可取,因为它能够测量角度/曲率,尽管有透明度或反射率,但仍能测量材料表面,样品准备工作最少,而且是非侵入性的。与传统的光学显微镜不同,可以获得表面的高度,并用于计算分析;例如,找到尺寸和去除形式,以找到表面粗糙度。与电子显微镜相比,有很少的样品准备,非接触性也允许快速收集数据,而不用担心样品准备的污染和错误。
测量目标
在这项应用中,Nanovea 3D非接触式轮廓仪被用来扫描两根导管的表面:一根由TPE(热塑性弹性体)制成,另一根由PVC(聚氯乙烯)制成。将获得并比较这两根导管的形态、径向尺寸和高度参数。
结果和讨论
三维表面
尽管聚合物管有一定的弯曲度,但Nanovea 3D非接触式轮廓仪可以扫描导管的表面。从所做的扫描中,可以获得一个三维图像,以便快速、直接地对表面进行视觉检查。
通过从原始扫描图像中提取轮廓线并拟合圆弧得到外径向尺寸。这显示了三维非接触式轮廓仪在质量控制应用中进行快速尺寸分析的能力。沿着导管的长度可以很容易地获得多个剖面。
通过从原始扫描图像中提取轮廓线并拟合圆弧得到外径向尺寸。这显示了三维非接触式轮廓仪在质量控制应用中进行快速尺寸分析的能力。沿着导管的长度可以很容易地获得多个剖面。
总结
在这个应用中,我们已经展示了Nanovea 3D非接触式轮廓仪如何被用来表征聚合物管。具体来说,获得了医用导管的表面计量学、径向尺寸和表面粗糙度。发现TPE导管的外半径为2.40mm,而PVC导管为1.27mm。TPE导管的表面被发现比PVC导管更粗糙。TPE的Sa为0.9740µm,而PVC为0.1791µm。虽然在此应用中使用了医用导管,但三维非接触式轮廓测量法也可应用于各种表面。可获得的数据和计算结果并不局限于所显示的内容。
现在,让我们来谈谈你的申请
分类
- 应用说明
- 环形摩擦学座谈会
- 腐蚀摩擦学
- 摩擦测试|摩擦系数
- 高温机械测试
- 高温摩擦学
- 湿度和气体 摩擦学
- 湿度的机械测试
- 压痕|蠕变和松弛
- 压痕|断裂韧性
- 压痕 | 硬度和弹性
- 压痕|损失和储存
- 压痕 | 应力与应变
- 压痕|屈服强度和疲劳
- 实验室测试
- 线性摩擦学
- 液体机械测试
- 液体摩擦学
- 低温摩擦学
- 机械测试
- 新闻发布
- 轮廓测量 - 平面度和翘曲度
- 轮廓测量法 | 几何和形状
- 轮廓测量 - 粗糙度和光洁度
- 轮廓测量法|台阶高度和厚度
- 轮廓测量法 | 纹理和颗粒
- 轮廓测量法|体积和面积
- 轮廓仪测试
- 环对环摩擦学
- 旋转摩擦学
- 刮擦测试|胶粘剂失效
- 刮擦测试 | 粘着性失效
- 刮擦测试 | 多次磨损
- 划痕测试|划痕硬度
- 划痕测试 摩擦学
- 贸易展销会
- 摩擦学测试
- 未分类
归档
- 2023年9 月
- 2023年8 月
- 2023年6 月
- 2023年5 月
- 2022年7 月
- 2022年5 月
- 2022年4 月
- 2022年1 月
- 2021年12 月
- 2021年11 月
- 2021年10 月
- 2021年9 月
- 2021年8 月
- 2021年7 月
- 2021年6 月
- 2021年5 月
- 2021年3 月
- 2021年2 月
- 2020年12 月
- 2020年11 月
- 2020年10 月
- 2020年9 月
- 2020年7 月
- 2020年5 月
- 2020年4 月
- 2020年3 月
- 2020年2 月
- 2020年1 月
- 2019年11 月
- 2019年10 月
- 2019年9 月
- 2019年8 月
- 2019年7 月
- 2019年6 月
- 2019年5 月
- 2019年4 月
- 2019年3 月
- 2019年1 月
- 2018年12 月
- 2018年11 月
- 2018年10 月
- 2018年9 月
- 2018年7 月
- 2018年6 月
- 2018年5 月
- 2018年4 月
- 2018年3 月
- 2018年2 月
- 2017年11 月
- 2017年10 月
- 2017年9 月
- 2017年8 月
- 2017年6 月
- 2017年5 月
- 2017年4 月
- 2017年3 月
- 2017年2 月
- 2017年1 月
- 2016年11 月
- 2016年10 月
- 2016年8 月
- 2016年7 月
- 2016年6 月
- 2016年5 月
- 2016年4 月
- 2016年3 月
- 2016年2 月
- 2016年1 月
- 2015年12 月
- 2015年11 月
- 2015年10 月
- 2015年9 月
- 2015年8 月
- 2015年7 月
- 2015年6 月
- 2015年5 月
- 2015年4 月
- 2015年3 月
- 2015年2 月
- 2015年1 月
- 2014年11 月
- 2014年10 月
- 2014年9 月
- 2014年8 月
- 2014年7 月
- 2014年6 月
- 2014年5 月
- 2014年4 月
- 2014年3 月
- 2014年2 月
- 2014年1 月
- 2013年12 月
- 2013年11 月
- 2013年10 月
- 2013年9 月
- 2013年8 月
- 2013年7 月
- 2013年6 月
- 2013年5 月
- 2013年4 月
- 2013年3 月
- 2013年2 月
- 2013年1 月
- 2012年12 月
- 2012年11 月
- 2012年10 月
- 2012年9 月
- 2012年8 月
- 2012年7 月
- 2012年6 月
- 2012年5 月
- 2012年4 月
- 2012年3 月
- 2012年2 月
- 2012年1 月
- 2011年12 月
- 2011年11 月
- 2011年10 月
- 2011年9 月
- 2011年8 月
- 2011年7 月
- 2011年6 月
- 2011年5 月
- 2010年11 月
- 2010年1 月
- 2009年4 月
- 2009年3 月
- 2009年1 月
- 2008年12 月
- 2008年10 月
- 2007年8 月
- 2006年7 月
- 2006年3 月
- 2005年1 月
- 2004年4 月