월간 아카이브: 9월 2019
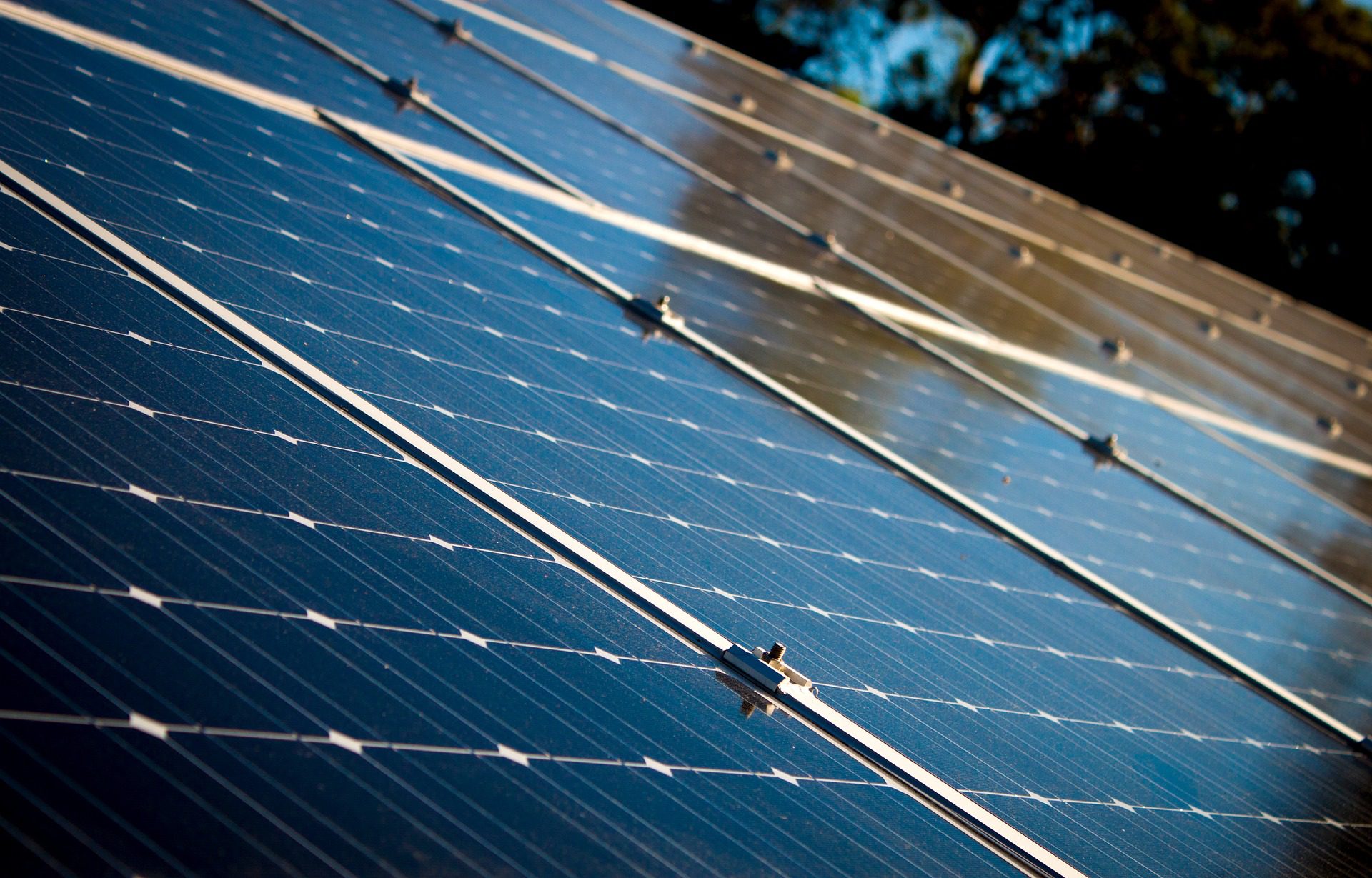
태양 전지의 표면 거칠기 및 특징
태양광 패널 테스트의 중요성
태양전지의 에너지 흡수를 극대화하는 것은 재생 가능한 자원으로서 태양전지가 살아남기 위한 핵심 요소입니다. 여러 층의 코팅과 유리 보호막은 태양전지가 작동하는 데 필요한 빛의 흡수, 투과, 반사를 가능하게 합니다. 대부분의 소비자용 태양전지가 15~18% 효율로 작동한다는 점을 고려할 때, 에너지 출력을 최적화하는 것은 현재 진행형입니다.
연구에 따르면 표면 거칠기는 빛의 반사율에 중요한 역할을 하는 것으로 나타났습니다. 빛의 반사율을 줄이기 위해 유리의 초기 레이어는 가능한 한 매끄러워야 하지만, 이후 레이어는 이 지침을 따르지 않습니다. 각각의 공핍 영역 내에서 빛이 산란될 가능성을 높이고 셀 내에서 빛의 흡수를 높이려면 각 코팅과 다른 코팅의 경계에 어느 정도의 거칠기가 필요합니다1. 이러한 영역의 표면 거칠기를 최적화하면 태양 전지가 최상의 성능으로 작동할 수 있으며, 나노비아 HS2000 고속 센서를 사용하면 표면 거칠기를 빠르고 정확하게 측정할 수 있습니다.
측정 목표
이 연구에서는 나노비아의 기능을 보여줄 것입니다. 프로파일 미터 고속 센서가 장착된 HS2000으로 태양전지의 표면 거칠기와 기하학적 특징을 측정합니다. 이 데모에서는 유리 보호막이 없는 단결정 태양 전지를 측정하지만, 이 방법론은 다른 다양한 애플리케이션에 사용할 수 있습니다.
테스트 절차 및 방법
태양 전지의 표면을 측정하기 위해 다음 테스트 매개 변수를 사용했습니다.
결과 및 토론
아래는 태양 전지의 2D 가색 보기와 각각의 높이 매개변수를 사용하여 표면의 면적을 추출한 것입니다. 두 표면 모두에 가우시안 필터를 적용하고 추출된 영역을 평탄화하기 위해 보다 적극적인 인덱스를 사용했습니다. 이렇게 하면 컷오프 지수보다 큰 형태(또는 파형)는 제외되어 태양 전지의 거칠기를 나타내는 특징만 남게 됩니다.
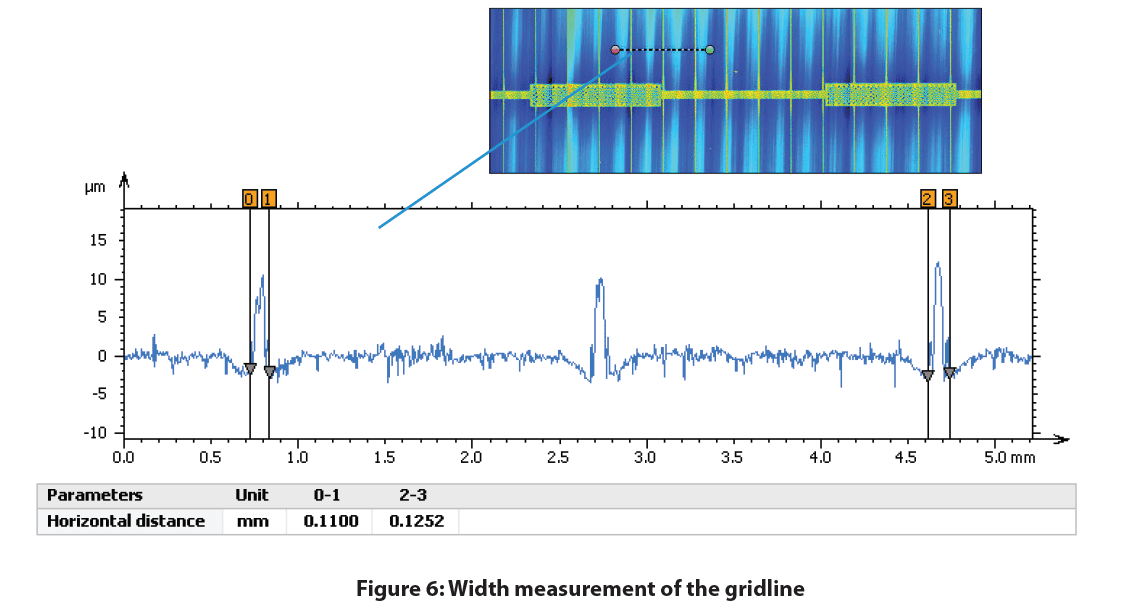

결론
이 연구에서는 나노베아 HS2000 라인 센서가 단결정 태양전지의 표면 거칠기와 특징을 측정할 수 있는 능력을 보여줄 수 있었습니다. 여러 샘플의 정확한 측정을 자동화하고 합격/불합격 한계를 설정할 수 있는 기능을 갖춘 나노베아 HS2000 라인 센서는 품질 관리 검사에 완벽한 선택입니다.
참조
1 숄츠, 루보미르. 라다니, 리보르. 뮬러 로바, 자밀라. "다층 태양 전지의 광학적 특성에 대한 표면 거칠기의 영향"전기 및 전자 공학 발전, 12 권, 6 호, 2014, 631-638 쪽.
이제 애플리케이션에 대해 이야기해 보겠습니다.
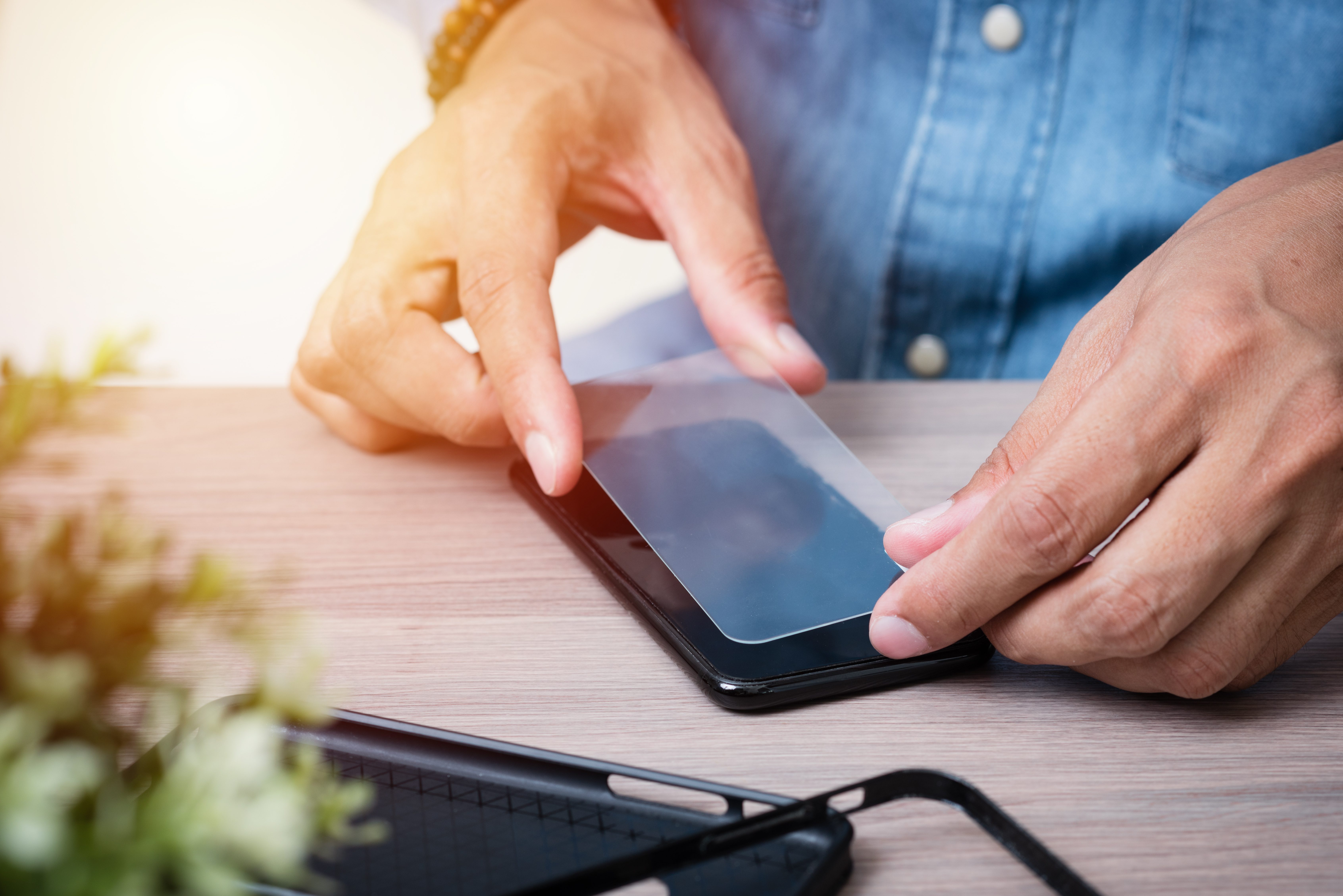
휴대폰 화면 보호기의 스크래치 방지
화면 보호기 테스트의 중요성
휴대폰 화면은 깨지거나 긁히지 않도록 설계되었지만 여전히 손상되기 쉽습니다. 매일 휴대폰을 사용하면 스크래치와 균열이 쌓이는 등 마모가 발생할 수 있습니다. 이러한 화면을 수리하는 데는 비용이 많이 들 수 있으므로 화면 보호기는 화면의 내구성을 높이기 위해 일반적으로 구입하여 사용하는 저렴한 손상 방지 아이템입니다.
나노비아 PB1000 기계식 테스터의 매크로 모듈을 음향 방출(AE) 센서와 함께 사용하면 스크래치1 테스트에서 화면 보호기가 고장을 일으키는 임계 부하를 명확하게 식별하여 두 가지 유형의 화면 보호기 간 비교 연구를 수행할 수 있습니다.
화면 보호기 소재의 일반적인 두 가지 유형은 TPU(열가소성 폴리우레탄)와 강화 유리입니다. 이 중 강화 유리는 충격 및 스크래치 보호 기능이 뛰어나므로 가장 좋은 것으로 간주됩니다. 그러나 가장 비싸기도 합니다. 반면에 TPU 화면 보호기는 가격이 저렴하고 플라스틱 화면 보호기를 선호하는 소비자에게 인기있는 선택입니다. 화면 보호기는 스크래치와 충격을 흡수하도록 설계되고 일반적으로 부서지기 쉬운 특성을 가진 재료로 만들어지기 때문에 현장 AE 감지와 결합 된 제어 스크래치 테스트는 응집 실패 (예 : 균열, 칩핑 및 파손) 및 / 또는 접착 실패 (예 : 박리 및 갈라짐)가 발생하는 하중을 결정하기위한 최적의 테스트 설정입니다.
측정 목표
이 연구에서는 나노비아의 PB1000 기계식 테스터의 매크로 모듈을 사용하여 두 가지 상용 화면 보호기에 대해 세 가지 스크래치 테스트를 수행했습니다. 음향 방출 센서와 광학 현미경을 사용하여 각 화면 보호기에 고장이 발생하는 임계 하중을 확인했습니다.
테스트 절차 및 방법
나노비아 PB1000 기계식 테스터를 사용하여 휴대폰 화면에 부착하고 마찰 센서 테이블에 고정된 두 개의 화면 보호기를 테스트했습니다. 모든 스크래치에 대한 테스트 매개변수는 아래 표 1에 표로 정리되어 있습니다.
결과 및 토론
화면 보호기는 서로 다른 재질로 만들어졌기 때문에 각각 다양한 유형의 고장이 발생했습니다. TPU 화면 보호기의 경우 심각한 고장이 한 번만 관찰된 반면 강화 유리 화면 보호기는 두 번이나 관찰되었습니다. 각 샘플에 대한 결과는 아래 표 2에 나와 있습니다. 임계 하중 #1은 화면 보호기가 현미경으로 응집 실패의 징후를 보이기 시작한 하중으로 정의됩니다. 임계 부하 #2는 음향 방출 그래프 데이터에서 보이는 첫 번째 피크 변화로 정의됩니다.
TPU 화면 보호기의 경우, 임계 하중 #2는 보호기가 휴대폰 화면에서 눈에 띄게 벗겨지기 시작한 스크래치와 함께 위치와 관련이 있습니다. 나머지 스크래치 테스트에서 임계 하중 #2를 초과하면 휴대폰 화면 표면에 스크래치가 나타났습니다. 강화 유리 화면 보호기의 경우 임계 하중 #1은 방사형 골절이 나타나기 시작한 위치와 상관 관계가 있습니다. 임계 하중 #2는 더 높은 하중에서 스크래치가 끝날 때 발생합니다. 음향 방출은 TPU 화면 보호기보다 더 큰 크기이지만 휴대폰 화면에는 손상이 발생하지 않았습니다. 두 경우 모두 임계 하중 #2는 깊이의 큰 변화에 해당하며 압자가 화면 보호기를 관통했음을 나타냅니다.
결론
이 연구에서는 제어되고 반복 가능한 스크래치 테스트를 수행하는 동시에 음향 방출 감지를 사용하여 TPU 및 강화 유리로 만든 화면 보호기에서 접착 및 응집 실패가 발생하는 하중을 정확하게 식별하는 Nanovea PB1000 기계식 테스터의 기능을 보여줍니다. 이 문서에 제시된 실험 데이터는 강화유리가 휴대폰 화면의 스크래치 방지에 가장 효과적이라는 초기 가정을 뒷받침합니다.
Nanovea Mechanical Tester는 ISO 및 ASTM 규격을 준수하는 Nano 및 Micro 모듈을 사용하여 정확하고 반복 가능한 압입, 스크래치 및 마모 측정 기능을 제공합니다. 그만큼 기계 테스터 는 얇거나 두꺼운 코팅, 부드럽거나 단단한 코팅, 필름 및 기판의 전체 기계적 특성을 결정하는 데 이상적인 솔루션을 제공하는 완벽한 시스템입니다.
이제 애플리케이션에 대해 이야기해 보겠습니다.
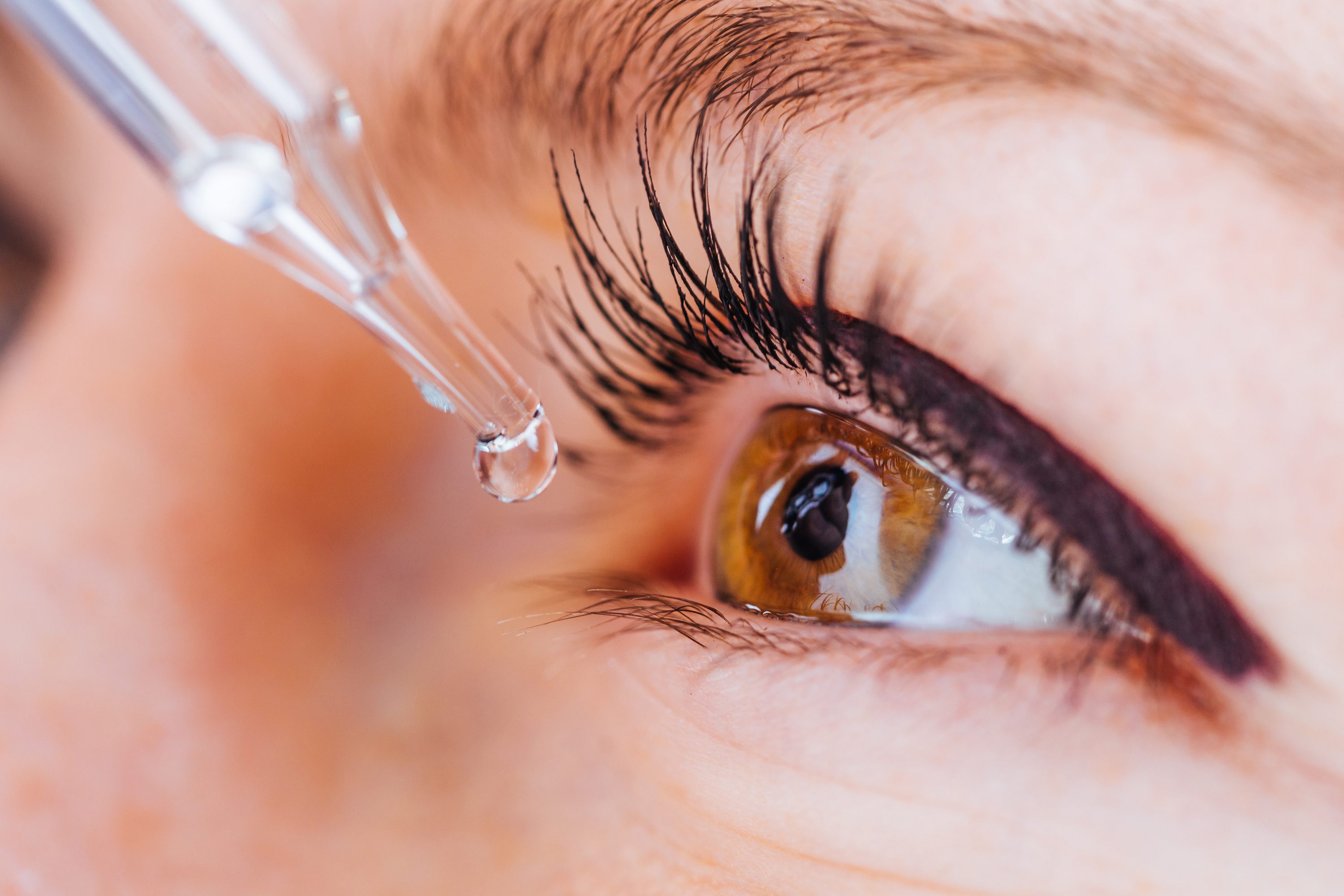
나노베아 T50 트라이보미터를 사용한 윤활 점안액 비교
점안액 솔루션 테스트의 중요성
측정 목표
이 연구에서는 나노베아 T50 트라이보미터의 핀 온 디스크 설정을 사용하여 세 가지 윤활 점안액 솔루션의 마찰 계수(COF)를 측정했습니다.
테스트 절차 및 방법
알루미나로 만든 직경 6mm 구형 핀을 유리 슬라이드에 적용하여 각 안약 용액이 두 표면 사이의 윤활제 역할을 하도록 했습니다. 모든 실험에 사용된 테스트 매개변수는 아래 표 1에 요약되어 있습니다.
결과 및 토론
테스트한 세 가지 점안액 용액의 최대, 최소 및 평균 마찰 계수 값은 아래 표 2에 표로 정리되어 있습니다. 각 점안액 용액에 대한 COF 대 회전수 그래프는 그림 2-4에 나와 있습니다. 각 테스트 중 COF는 전체 테스트 기간의 대부분 동안 비교적 일정하게 유지되었습니다. 샘플 A의 평균 COF가 가장 낮아 윤활 특성이 가장 우수함을 나타냅니다.
결론
이 연구에서는 세 가지 점안액 용액의 마찰 계수를 측정하는 데 있어 나노베아 T50 트라이보미터의 성능을 선보입니다. 이 값을 바탕으로 샘플 A가 다른 두 샘플에 비해 마찰 계수가 낮고 따라서 윤활성이 더 우수하다는 것을 보여줍니다.
나노베아 트라이보미터 ISO 및 ASTM 준수 회전 및 선형 모듈을 사용하여 정확하고 반복 가능한 마모 및 마찰 테스트를 제공합니다. 또한 사전 통합된 하나의 시스템에서 사용할 수 있는 고온 마모, 윤활 및 마찰 부식 모듈 옵션도 제공합니다. 이러한 다양성을 통해 사용자는 실제 적용 환경을 더 잘 시뮬레이션하고 다양한 재료의 마모 메커니즘 및 마찰 특성에 대한 기본적인 이해를 향상시킬 수 있습니다.
이제 애플리케이션에 대해 이야기해 보겠습니다.
카테고리
- 애플리케이션 노트
- 링 마찰력 차단
- 부식 마찰학
- 마찰 테스트 | 마찰 계수
- 고온 기계 테스트
- 고온 마찰학
- 습도 및 가스 마찰학
- 습도 기계적 테스트
- 들여쓰기 | 크립 및 릴랙스
- 압흔 | 파단 인성
- 들여쓰기 | 경도 및 탄성
- 들여쓰기 | 분실 및 보관
- 들여쓰기 | 스트레스 대 변형
- 압흔 | 수율 강도 및 피로도
- 실험실 테스트
- 선형 마찰학
- 액체 기계 테스트
- 액체 마찰학
- 저온 마찰학
- 기계적 테스트
- 보도 자료
- 프로파일 측정 | 평탄도 및 휨
- 프로파일 측정 | 기하학 및 도형
- 프로파일 측정 | 거칠기 및 마감
- 프로파일 측정 | 스텝 높이 및 두께
- 프로파일 측정 | 텍스처 및 그레인
- 프로파일 측정 | 부피 및 면적
- 프로파일 측정 테스트
- 링 온 링 마찰학
- 회전 마찰학
- 스크래치 테스트 | 접착 실패
- 스크래치 테스트 | 응집력 실패
- 스크래치 테스트 | 멀티 패스 마모
- 스크래치 테스트 | 스크래치 경도
- 스크래치 테스트 마찰학
- 트레이드쇼
- 마찰 테스트
- 분류
보관함
- 2023년 9월
- 2023년 8월
- 2023년 6월
- 2023년 5월
- 2022년 7월
- 2022년 5월
- 2022년 4월
- 2022년 1월
- 2021년 12월
- 2021년 11월
- 2021년 10월
- 2021년 9월
- 2021년 8월
- 2021년 7월
- 2021년 6월
- 2021년 5월
- 2021년 3월
- 2021년 2월
- 2020년 12월
- 2020년 11월
- 2020년 10월
- 2020년 9월
- 2020년 7월
- 2020년 5월
- 2020년 4월
- 2020년 3월
- 2020년 2월
- 2020년 1월
- 2019년 11월
- 2019년 10월
- 2019년 9월
- 2019년 8월
- 2019년 7월
- 2019년 6월
- 2019년 5월
- 2019년 4월
- 2019년 3월
- 2019년 1월
- 2018년 12월
- 2018년 11월
- 2018년 10월
- 2018년 9월
- 2018년 7월
- 2018년 6월
- 2018년 5월
- 2018년 4월
- 2018년 3월
- 2018년 2월
- 2017년 11월
- 2017년 10월
- 2017년 9월
- 2017년 8월
- 2017년 6월
- 2017년 5월
- 2017년 4월
- 2017년 3월
- 2017년 2월
- 2017년 1월
- 2016년 11월
- 2016년 10월
- 2016년 8월
- 2016년 7월
- 2016년 6월
- 2016년 5월
- 2016년 4월
- 2016년 3월
- 2016년 2월
- 2016년 1월
- 2015년 12월
- 2015년 11월
- 2015년 10월
- 2015년 9월
- 2015년 8월
- 2015년 7월
- 2015년 6월
- 2015년 5월
- 2015년 4월
- 2015년 3월
- 2015년 2월
- 2015년 1월
- 2014년 11월
- 2014년 10월
- 2014년 9월
- 2014년 8월
- 2014년 7월
- 2014년 6월
- 2014년 5월
- 2014년 4월
- 2014년 3월
- 2014년 2월
- 2014년 1월
- 2013년 12월
- 2013년 11월
- 2013년 10월
- 2013년 9월
- 2013년 8월
- 2013년 7월
- 2013년 6월
- 2013년 5월
- 2013년 4월
- 2013년 3월
- 2013년 2월
- 2013년 1월
- 2012년 12월
- 2012년 11월
- 2012년 10월
- 2012년 9월
- 2012년 8월
- 2012년 7월
- 2012년 6월
- 2012년 5월
- 2012년 4월
- 2012년 3월
- 2012년 2월
- 2012년 1월
- 2011년 12월
- 2011년 11월
- 2011년 10월
- 2011년 9월
- 2011년 8월
- 2011년 7월
- 2011년 6월
- 2011년 5월
- 2010년 11월
- 2010년 1월
- 2009년 4월
- 2009년 3월
- 2009년 1월
- 2008년 12월
- 2008년 10월
- 2007년 8월
- 2006년 7월
- 2006년 3월
- 2005년 1월
- 2004년 4월